Originally Posted by
WheresWaldo
Just finished up a Colnago C64 'D' shaped seat post mount for the Garmin Varia,
http://shpws.me/RYqZ
That looks fantastic @
WheresWaldo.
I'm curious whether you've considered designing with just a flat area where something like the K-Edge replacement Garmin inserts like this can be mounted?
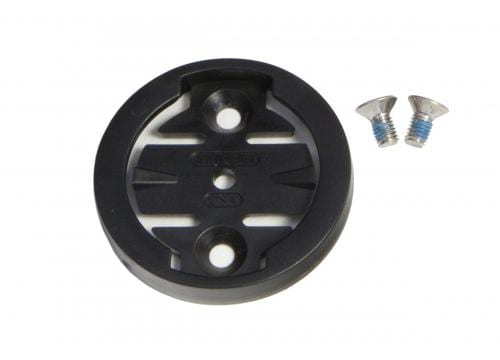
The out-front mount that I'm using on my bike right now has the Garmin on top, and a GoPro-style three-bladed mount thingy built into the bottom. The Garmin attaches to one of these plastic inserts that is screwed onto the mount. I'm about to start designing a replacement for my out-front mount that will have it being an organic part of the 4-bolt front stem plate. In other words, it will be a one-piece stem plate with the mount for these two devices built into it. Once I have a good design I'm going to upload it to one of these sites that does laser-sintered 3d printing in titanium and get an estimate. It will be expensive, but if it's not outrageously expensive I'd like to get one printed up to use on my own bike, eliminating the kludge that's on there right now. Anyhow I was thinking about how to design the Garmin twist interface that I'd trust could be 3D printed well enough to hold the Garmin securely, while not being too brutal on the garmin itself if it's made from titanium. I decided to just have my design feature a little rim that extends up around the base of one of these K-Edge style garmin mount inserts by a mm or two instead. I think it'll be as secure as it needs to be and I won't have to worry as much at the precision required of the 3D printer or my design to do up the mounting flanges and whatnot.
The one thing that concerns me is that I'm no mechanical engineer, so I have no true concept of how thick the titanium stem plate would have to be safe, and that's a part that must survive much greater forces than any simple device mount would have to. An easy and probably reasonable enough solution would be to just copy the dimensions of one of the aluminum stem plates I have and just assume that if they're strong enough in aluminum, they'll certainly be strong enough in titanium. I'd like to take advantage of the reduction in mounting hardware and whatnot, though, and see if I could achieve a final mount that not only is much cleaner and simpler than what I have now, but also a little lighter too. Not to mention that the cost estimates of these 3D printing sites seem to be based on calculated volume of metal powder used and printing time, so the lighter the final part, the cheaper it would be to actually have one made. There's no way I'd use my design in a plastic 3D-printed implementation for a stem mounting plate.
Anyhow, I'm in awe of your designs. My Solidworks skills are rudimentary at best, so designing my stem/device mount will push my Solidworks comfort envelope, but I think it's a good project. I can 3D print prototypes of it just for dimensional fit evaluations and whatnot, but I'd only mount up and use one done in metal.