René Hubris Treat-a-Trek
#126
framebuilder
Since my classes were mentioned, I thought I better comment. My wife is going to retire this year so that means I will need to cut back on my teaching schedule. I'm way past the time when I could have retired. I usually do 5 three-week classes a year with one or two students in each class. I squeeze a painting class or two in there as well. I feel some obligation to continue teaching so the craft can maintain a high standard. I was very fortunate to go to Ellis Briggs in Yorkshire in 1975 to learn. Jack Briggs had plenty of time to show me and I worked along side Andrew the journeyman builder that allowed me to get my own experiences. I was a high school teacher at the time and my purpose for going was to bring the secrets back to the States to share them here. I taught my 1st class in a college setting in 1976 and have done it steadily since then. Over the years I've been able to refine the process. I expect every student to leave class with a professional quality frame. Sometimes I have to make up the difference for the less talented. I get a lot of students that have already taken another class somewhere else. I make zero effort to advertise and that weeds out the casuals. The most motivated seekers find me.
As a college and university trained teacher, I know what it takes for someone to catch on. Trying to cram everything into 2 weeks is usually too much. There is a huge amount of material to absorb. For example when students have come from 2-week classes, sometimes their former instructor(s) had to do some of the work to get them done on time. This can sometimes show in their lack of preparation to do it again. The most serious of my students go to the college campus in Ukraine where they stay 2 or 3 months making frames that we turn into bicycles for pastors. They are needed on the eastern front now. The 10 or so that have done that in the last 20 years have come back with some serious skills. My reason for mentioning all of this is that those that really want to get solid training should make plans before it is too late. I've got many that have expressed interest than I'll ever be able to teach. I don't know when I am going to stop but sundown is on the horizon. Probably before I want it to but it won't be immediately.
As a college and university trained teacher, I know what it takes for someone to catch on. Trying to cram everything into 2 weeks is usually too much. There is a huge amount of material to absorb. For example when students have come from 2-week classes, sometimes their former instructor(s) had to do some of the work to get them done on time. This can sometimes show in their lack of preparation to do it again. The most serious of my students go to the college campus in Ukraine where they stay 2 or 3 months making frames that we turn into bicycles for pastors. They are needed on the eastern front now. The 10 or so that have done that in the last 20 years have come back with some serious skills. My reason for mentioning all of this is that those that really want to get solid training should make plans before it is too late. I've got many that have expressed interest than I'll ever be able to teach. I don't know when I am going to stop but sundown is on the horizon. Probably before I want it to but it won't be immediately.
#127
Senior Member
Thread Starter
Join Date: Jun 2010
Location: Medford MA
Posts: 2,089
Bikes: Ron Cooper touring, 1959 Jack Taylor 650b ladyback touring tandem, Vitus 979, Joe Bell painted Claud Butler Dalesman, Colin Laing curved tube tandem, heavily-Dilberted 1982 Trek 6xx, René Herse tandem
Mentioned: 80 Post(s)
Tagged: 0 Thread(s)
Quoted: 964 Post(s)
Liked 1,451 Times
in
723 Posts
@Doug Fattic , I am sad to hear that. I probably won't make it, given what my next few years of career as a new PhD look like. But, equally likely to only build for myself and close friends, anyway. You were very helpful in your advice to get away from the Harris white flux.
Do you have any pointers for me based on the photos? Is no unsolicited advice from you a good sign or a bad sign? I will re-iterate that I appreciate all your advice. Here's a close-up of what I did. Unfortunately it's a little blurry, but you can at least see the flux and the coloring of the steel. The flux is Gasflux type H "Black Flux." You can see how much I applied, looking at the previous photo of the headtube with only the top lug brazed. Not enough?
Too much heat, again? By accident, I got some metal to dull red. Never bright cherry.
I did feel around inside the vent-holes with a soldering pick and could feel an internal shoreline. I used about 3/4 troy ounce of silver on the two lugs together.
Do you have any pointers for me based on the photos? Is no unsolicited advice from you a good sign or a bad sign? I will re-iterate that I appreciate all your advice. Here's a close-up of what I did. Unfortunately it's a little blurry, but you can at least see the flux and the coloring of the steel. The flux is Gasflux type H "Black Flux." You can see how much I applied, looking at the previous photo of the headtube with only the top lug brazed. Not enough?
Too much heat, again? By accident, I got some metal to dull red. Never bright cherry.
I did feel around inside the vent-holes with a soldering pick and could feel an internal shoreline. I used about 3/4 troy ounce of silver on the two lugs together.
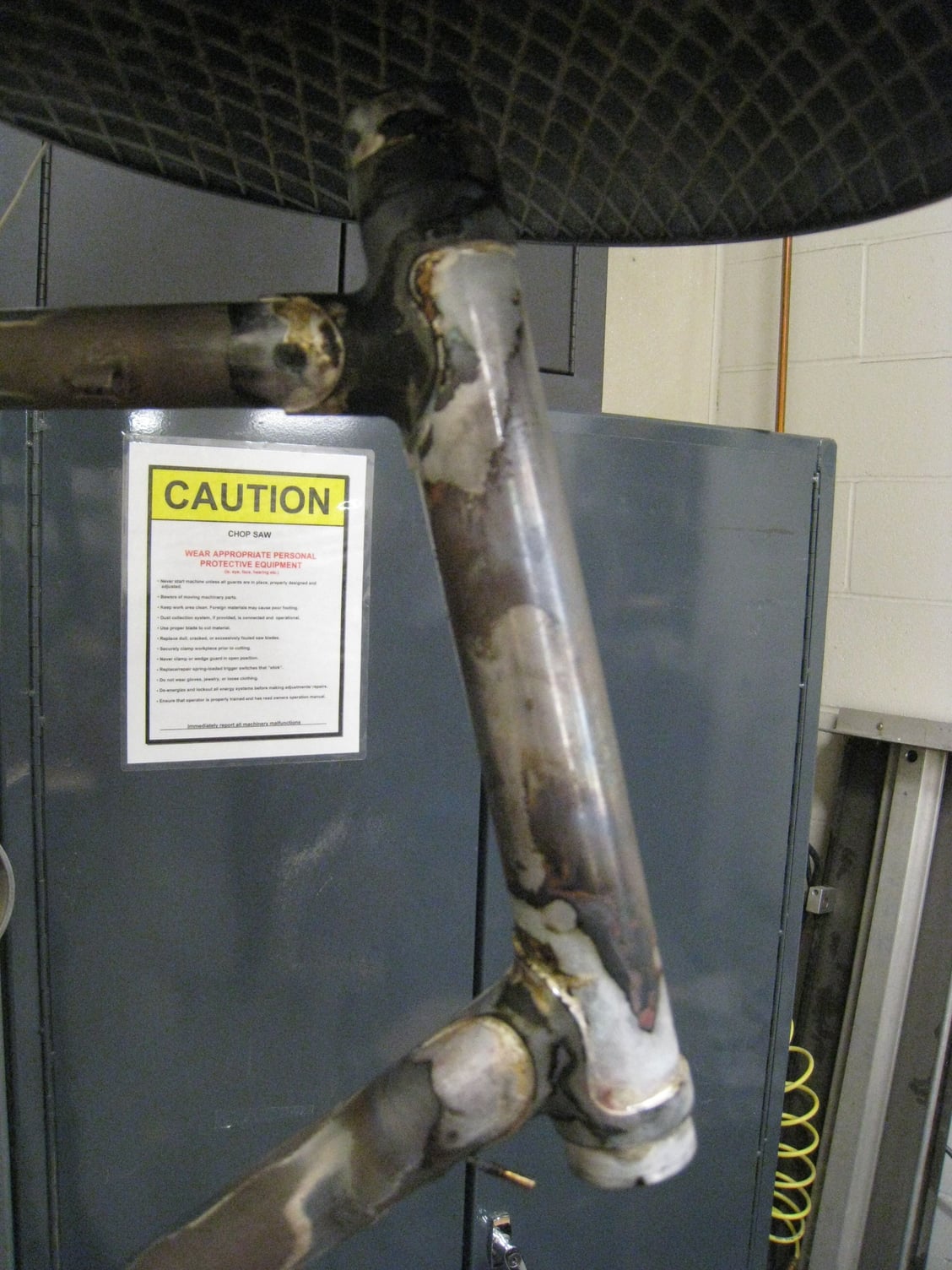
__________________
Owner & co-founder, Cycles René Hubris. Unfortunately attaching questionable braze-ons to perfectly good frames since about 2015. With style.
Owner & co-founder, Cycles René Hubris. Unfortunately attaching questionable braze-ons to perfectly good frames since about 2015. With style.
Last edited by scarlson; 01-12-22 at 12:59 AM.
#128
framebuilder
@Doug Fattic , I am sad to hear that. I probably won't make it, given what my next few years of career as a new PhD look like. But, equally likely to only build for myself and close friends, anyway. You were very helpful in your advice to get away from the Harris white flux.
Do you have any pointers for me based on the photos? Is no unsolicited advice from you a good sign or a bad sign? I will re-iterate that I appreciate all your advice. Here's a close-up of what I did. Unfortunately it's a little blurry, but you can at least see the flux and the coloring of the steel. The flux is Gasflux type H "Black Flux." You can see how much I applied, looking at the previous photo of the headtube with only the top lug brazed. Not enough?
Too much heat, again? By accident, I got some metal to dull red. Never bright cherry.
I did feel around inside the vent-holes with a soldering pick and could feel an internal shoreline. I used about 3/4 troy ounce of silver on the two lugs together.
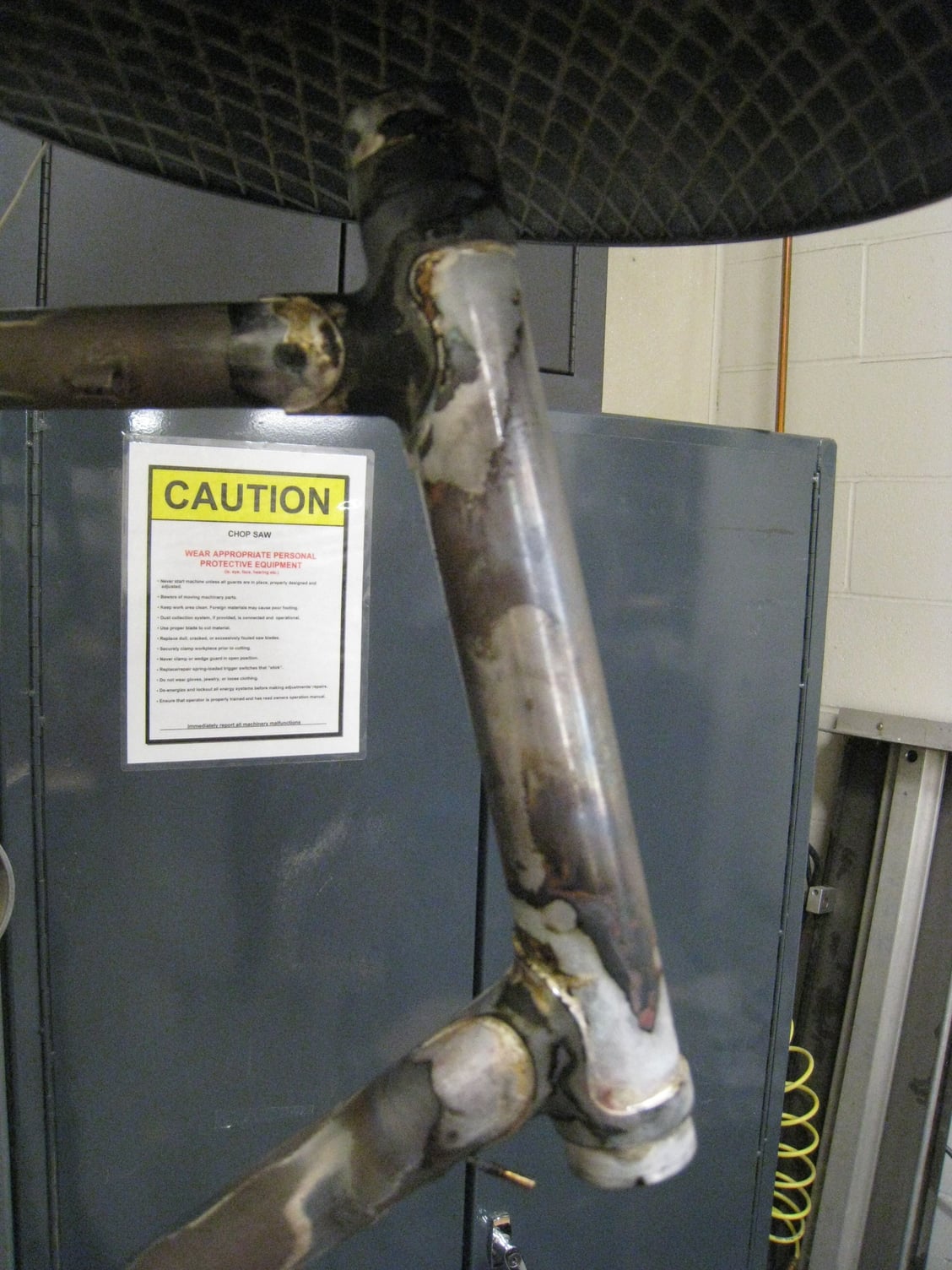
Do you have any pointers for me based on the photos? Is no unsolicited advice from you a good sign or a bad sign? I will re-iterate that I appreciate all your advice. Here's a close-up of what I did. Unfortunately it's a little blurry, but you can at least see the flux and the coloring of the steel. The flux is Gasflux type H "Black Flux." You can see how much I applied, looking at the previous photo of the headtube with only the top lug brazed. Not enough?
Too much heat, again? By accident, I got some metal to dull red. Never bright cherry.
I did feel around inside the vent-holes with a soldering pick and could feel an internal shoreline. I used about 3/4 troy ounce of silver on the two lugs together.
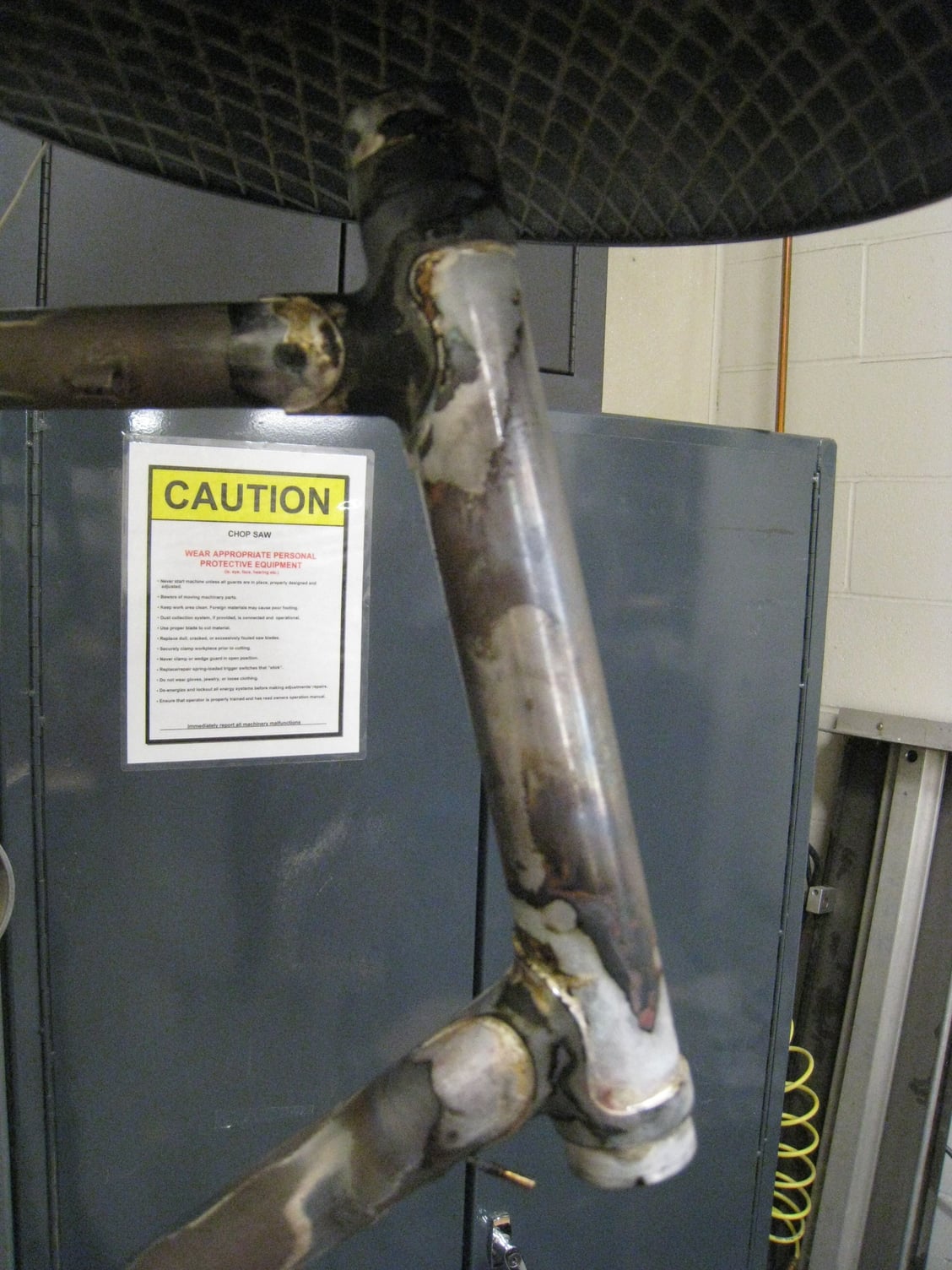
3/4 of an once sounds like more than enough silver for 2 luged joints.
I'm not familiar with Gasflux's type H. I use Gasflux type G. It operates at 100º higher temperature than their more common type U. Burning off the flux is a very common rookie error. I have students apply it way further up the tube then I need so they won't run out because it takes them much longer to braze a joint than me. Oops I have to go and get ready for another day of class. When I get a chance I can explain more about flux.
#129
Senior Member
Thread Starter
Join Date: Jun 2010
Location: Medford MA
Posts: 2,089
Bikes: Ron Cooper touring, 1959 Jack Taylor 650b ladyback touring tandem, Vitus 979, Joe Bell painted Claud Butler Dalesman, Colin Laing curved tube tandem, heavily-Dilberted 1982 Trek 6xx, René Herse tandem
Mentioned: 80 Post(s)
Tagged: 0 Thread(s)
Quoted: 964 Post(s)
Liked 1,451 Times
in
723 Posts
By coincidence, the student in my class that started this week has already earned his PhD + more. It is always difficult to analyze the quality of a braze from just a picture. I can see you got it a bit too hot and didn't use enough flux. Why you got it so hot can't be known without seeing you braze in person. Were you using the same Mapp Turbo torch like you did a couple of years ago to put on cantilever bosses? That provides a kind of broad soaking heat pattern. You have to control heat with it like an on off switch. Flick on flick off. A very common student error is that their torch hand freezes when applying silver because they have not yet leaned to operate both hands independently. The problem is that it is easy enough to bring a joint up to brazing temperature but then when they start to add silver, it is very hard to keep that temperature window without going over some. Another way to control heat without flicking the flame on/off is to pull back with the flame so it is cooler farther away. The reason this is difficult for students is because in it normal that both of their hands want to go in as the silver holding hand moves closer as the silver melts. It isn't natural they can operate them independently enough at first so one hand is moving in while the other is moving back. That hakes practice.
3/4 of an once sounds like more than enough silver for 2 luged joints.
I'm not familiar with Gasflux's type H. I use Gasflux type G. It operates at 100º higher temperature than their more common type U. Burning off the flux is a very common rookie error. I have students apply it way further up the tube then I need so they won't run out because it takes them much longer to braze a joint than me. Oops I have to go and get ready for another day of class. When I get a chance I can explain more about flux.
I'll re-iterate, I really appreciate your advice. I'm doing this whole thing as a learning exercise. This is how I have fun: learning new things when the stakes are relatively low.
__________________
Owner & co-founder, Cycles René Hubris. Unfortunately attaching questionable braze-ons to perfectly good frames since about 2015. With style.
Owner & co-founder, Cycles René Hubris. Unfortunately attaching questionable braze-ons to perfectly good frames since about 2015. With style.
#130
framebuilder
You can reuse Type G too. If you have let the joint cool you can always add more. What you want to look out for and avoid is surface oxidation caused by heating when there is not enough flux left. Or getting the joint too hot. That ugly black surface. Type G flux seems to clean better than type U. When the surface goes black silver won't stick to it. Getting more flux over that area can sometimes cleanse the surface some.
Does your lab prohibit any kind of oxygen assist or just pressured tanks? I ask because using an oxygen concentrator is an excellent option. Over on Velocipede Salon my subject thread on oxygen concentrators has over 30.000 views. The one on using propane instead of acetylene has over 180,000. Obviously more people are interested in an alternative to oxyacetylene units than amateur frame builders. It is the way home hobbyists in jewelry and lamp making (working with melting glass) can use oxypropane in a home setting. It isn't jut about heat volume or BTUs but the fine flame point that allows me to pinpoint my heat to get clean shorelines.
Does your lab prohibit any kind of oxygen assist or just pressured tanks? I ask because using an oxygen concentrator is an excellent option. Over on Velocipede Salon my subject thread on oxygen concentrators has over 30.000 views. The one on using propane instead of acetylene has over 180,000. Obviously more people are interested in an alternative to oxyacetylene units than amateur frame builders. It is the way home hobbyists in jewelry and lamp making (working with melting glass) can use oxypropane in a home setting. It isn't jut about heat volume or BTUs but the fine flame point that allows me to pinpoint my heat to get clean shorelines.