Wheel building question.
#51
Senior Member
that is going lower tension after turning the NDS nipples to the point where a very precise lateral true is no longer possible - backing off after that.
i dunno if he stressed the balancing of radial runout with the spoke tension variance. either by guestimation (having experience is sometimes enough) or by computing.
i am very laborious about this aspect and it is quite the most important thing to achieve from the get go in order to have both lower spoke tension and lower radial runout in the end after that extreme tension is done so that by stress relieving everything the spokes bend right where they need to bend - without pliers or fingers pressing - and the rim being straightened if not being a perfect circle to begin with.
there's also cold working of the rim that is done. increasing the rim's yield strength by doing so with the cost of reduced ductility. it's worth up to a certain point and about 200MPa is compression for the rim is quite the level i try to achieve but i also am careful about wax lubing the brass nipples and won't go at that compression mainly by turning the nipples unless with not so thin spokes.
YMMV.
as to your question... i am compensating for those unfortunate accidents when the rim (heavy rear end) hits the pavement with no tire to spread the load etc.
i do not want to have the lightest wheels but durability is the main goal for me as i do not have other's people money and i won't be selling crap to be rich. i care not if other people appreciate what i achieve, i don't need to have the public admire my bike which i am not sure if i'd have it painted like the frame is rusted to ward off thieves etc. i might be needing to sell it later. i pay rent etc. in short... i don't like what is described as the sod's law. if i would have had some wealth maybe i would just have a motorcycle for going about the city. i am poor therefore i need to fix my things and replace things (like rims) less often. and i don't like fixing things often but do like to have a wheel built/repaired so that i do not go over the whole thing ever again and only need to replace bearings.
the rim was bent out of shape when i bought the bike, the tension was low and all over the place. the previous owner was relatively rich but the mechanics he went to could not straighten the rim and could not figure out how to do it properly. many mechanics fix your stuff just so the chance of coming back to fix it again is not the least. and clients are just told it is their fault (bad riding) for the wheel needed to be retrued or that it is too heavy bike to sustain some hits. and clients do not know that the spoke tension needs to be high enough and that a 36h rim is able to take 150kgf drive side tension if spoke tension variance and radial true is very good.
so there you have it: i am compensating for being a poor sod. you can laugh at me for being poor. if i am poor i certainly am not right in the head, right? if i had some brains i would have been rich.
Last edited by adipe; 09-03-19 at 11:12 AM.
#52
Generally bewildered
Join Date: Aug 2015
Location: Eastern PA, USA
Posts: 3,037
Bikes: 2014 Trek Domane 6.9, 1999 LeMond Zurich, 1978 Schwinn Superior
Mentioned: 20 Post(s)
Tagged: 0 Thread(s)
Quoted: 1152 Post(s)
Liked 341 Times
in
251 Posts
adipe,
Thanks for clarifying your position regarding spoke tension. It sounds like you've worked on building wheels out of economic necessity. You might be interested in a guy named David Gingery. A few decades ago he wanted a machine shop but couldn't afford new machines. So he built (designed, made patterns and castings, machined, trued and finished) a set of reasonably good tools (lathe, milling machine,etc). You can read about it. Get "Build Your Own Metal Working Shop From Scrap" books from your library. Given your technical bent, may be of interest.
My understanding of Jobst's suggestion is that he viewed maximum spoke tension as the best way to avoid broken spokes or bent rims. Get the wheel true, then tighten up the spokes (while keeping things true and the spoke tensions even) until you have imminent taco. Then back off a bit to give yourself some safety margin from taco (SMFT).
If you get a good SMFT with 150kgf (!), good on you. But that seems really high to me.
As an engineer, I wonder too about the effect of rim distortions due to impact. For a perfectly round rim we may back off tension enough to have a good SMFT. But the moment we hit a bad pothole, the rim may be distorted (as the rim you mention was). Does this lessen our SMFT? Would a hard pothole hit put a really tight rim into taco mode, whereas a bit less tight setup would tolerate the hit better?
You mention cold working of the rim - an aspect I'd not thought about. Don't recall reading that in Brandt - did you come up with that? It makes some sense. But I'm not sure of the magnitude of effect.
I'm still going to disagree with you about not putting a slight (2-3)° bend in the spoke so that the nipple is not too canted in the spoke hole. I think its a good idea if the nipple is constrained enough so that you see a bend in the spoke. For the reason I mentioned: if the nipple is sufficiently canted, it creates a high stress point at the hole. Your point about not marring the spoke surface is one to keep in mind, so bending without scratching is key.. Brandt suggests that you can bend the spokes with your hands. If that was every possible for me, it was long in the past. I don't see how you can (even with 180kgf non-drive-side) get the spokes to bend so that the nipple's not canted. In fact, if high spoke tension DID bend the spoke with spoke tension alone we're into the plastic deformation range of the stress-strain curve, but we have no control of WHERE the bend occurs.
I had to look up Sod's law. Basically another belief that the universe conspires against you, and what you need is never there when you need it. (My understanding). Like when you need money, you don't have it. (Reminds me of trying to take out a loan: if you need it, they don't want to lend it!). It is also known as Finagle’s Law of Negative Dynamics or Finagle’s corollary to Murphy’s Law. (according to the American Thinker). I can't complain about being poor, but I think that everyone, rich and poor, has problems. Easier to deal with some of them if you've means. The trivial problems apply to everyone: Where is that d****d 3.5mm ball-end hex driver when I need it?
Thanks for clarifying your position regarding spoke tension. It sounds like you've worked on building wheels out of economic necessity. You might be interested in a guy named David Gingery. A few decades ago he wanted a machine shop but couldn't afford new machines. So he built (designed, made patterns and castings, machined, trued and finished) a set of reasonably good tools (lathe, milling machine,etc). You can read about it. Get "Build Your Own Metal Working Shop From Scrap" books from your library. Given your technical bent, may be of interest.
My understanding of Jobst's suggestion is that he viewed maximum spoke tension as the best way to avoid broken spokes or bent rims. Get the wheel true, then tighten up the spokes (while keeping things true and the spoke tensions even) until you have imminent taco. Then back off a bit to give yourself some safety margin from taco (SMFT).
If you get a good SMFT with 150kgf (!), good on you. But that seems really high to me.
As an engineer, I wonder too about the effect of rim distortions due to impact. For a perfectly round rim we may back off tension enough to have a good SMFT. But the moment we hit a bad pothole, the rim may be distorted (as the rim you mention was). Does this lessen our SMFT? Would a hard pothole hit put a really tight rim into taco mode, whereas a bit less tight setup would tolerate the hit better?
You mention cold working of the rim - an aspect I'd not thought about. Don't recall reading that in Brandt - did you come up with that? It makes some sense. But I'm not sure of the magnitude of effect.
I'm still going to disagree with you about not putting a slight (2-3)° bend in the spoke so that the nipple is not too canted in the spoke hole. I think its a good idea if the nipple is constrained enough so that you see a bend in the spoke. For the reason I mentioned: if the nipple is sufficiently canted, it creates a high stress point at the hole. Your point about not marring the spoke surface is one to keep in mind, so bending without scratching is key.. Brandt suggests that you can bend the spokes with your hands. If that was every possible for me, it was long in the past. I don't see how you can (even with 180kgf non-drive-side) get the spokes to bend so that the nipple's not canted. In fact, if high spoke tension DID bend the spoke with spoke tension alone we're into the plastic deformation range of the stress-strain curve, but we have no control of WHERE the bend occurs.
I had to look up Sod's law. Basically another belief that the universe conspires against you, and what you need is never there when you need it. (My understanding). Like when you need money, you don't have it. (Reminds me of trying to take out a loan: if you need it, they don't want to lend it!). It is also known as Finagle’s Law of Negative Dynamics or Finagle’s corollary to Murphy’s Law. (according to the American Thinker). I can't complain about being poor, but I think that everyone, rich and poor, has problems. Easier to deal with some of them if you've means. The trivial problems apply to everyone: Where is that d****d 3.5mm ball-end hex driver when I need it?
Last edited by WizardOfBoz; 09-03-19 at 01:33 PM.
#53
working on my sandal tan
Join Date: Aug 2011
Location: CID
Posts: 22,629
Bikes: 1991 Bianchi Eros, 1964 Armstrong, 1988 Diamondback Ascent, 1988 Bianchi Premio, 1987 Bianchi Sport SX, 1980s Raleigh mixte (hers), All-City Space Horse (hers)
Mentioned: 98 Post(s)
Tagged: 0 Thread(s)
Quoted: 3871 Post(s)
Liked 2,568 Times
in
1,579 Posts
extreme tension is the jobst brandt way (described and supported by him, not that he invented it). not that he has everything right about everything.
that is going lower tension after turning the NDS nipples to the point where a very precise lateral true is no longer possible - backing off after that.
that is going lower tension after turning the NDS nipples to the point where a very precise lateral true is no longer possible - backing off after that.
Some of the heavy-duty rims and spokes can take more tension, of course, but if you're going to recommend that everyone go this extreme, expect some pushback. High spoke tensions make the wheelbuilder look like a hero at first, but the user won't be happy if their rim ends up cracking all over the place later on.

Likes For ThermionicScott:
#54
Senior Member
#55
Senior Member
Jobst would probably object to being associated with "extreme" tensions like 180kgf+. His book is clear that he only recommended this procedure for lightweight (420g or so) box-section rims, and that aero rims could risk pulling the nipples through before deforming in waves. Drew Eckhardt reported that when building up classic Mavic rims in the Jobst way, he only reached 110 kgf or so, which is a level that most people would consider reasonable. Unfortunately, it's popular to think that if a little of something is good, more is always better, so Jobst has become the figurehead for extreme spoke tensions.
Some of the heavy-duty rims and spokes can take more tension, of course, but if you're going to recommend that everyone go this extreme, expect some pushback. High spoke tensions make the wheelbuilder look like a hero at first, but the user won't be happy if their rim ends up cracking all over the place later on.
Some of the heavy-duty rims and spokes can take more tension, of course, but if you're going to recommend that everyone go this extreme, expect some pushback. High spoke tensions make the wheelbuilder look like a hero at first, but the user won't be happy if their rim ends up cracking all over the place later on.

i never wanted to remain there, but wanted to straighten the bent out of shape rim as precisely as i could so that in the end spoke tension variance would be low with a straightened rim that has radial runout balanced to the tension variance. i got to
what i am doing here is saying how it works. i can't take any advantage off of it and i feel like i am wasting my time (shooting myself in the foot) only to have people attack me for not agreeing to the sheeple's dogma which has maximum tension 120kgf but that is with +/- 20% spoke tension variance. usually professional wheelbuilders do not explain the principles they work by but just present you the finished work without hurting your dogma.
there are people riding 140kgf DS tensioned wheels and even more than that after some wheelbuilders considered it's worth the effort. every wheelbuilder knows that if very low tension variance is achieved a high tension wheel can work very well and every wheelbuilder knows that the rim can give in and change shape by manipulating the spokes. not every wheelbuilder is happy to go high tension if lateral true can be kept very low at every stage of raising the NDS tension because the customer will not pay more for a wheel that has 0.1mm total radial and lateral runout and about 10% total spoke tension variance (mine is just a tad over +/-5%). some overweight customers will pay more just to receive wheels that won't go easily out of true. in such cases some but not all wheelbuilders will be able to deliver.
the rim is a 21mm inner width, 18mm height. about 500g weight is estimated. it's an "Oval" rim and i could not find out more exactly what model it is. eyeleted...
the maximum DS tension for the rear wheel is about 144kgf right now and that is with the tire being inflated. i did some measurements and established that the lowest NDS tension would approach zero at about 400kgf dynamic pure vertical load on the rim which is not an impossible accident to take place in case of a sudden puncture at the most inopportune time (high speed, potholes etc.). the unsprung weight of my bike on the rear wheel (measured) is 15kg (~33lb.) so i don't have to be an overweight person to consider this tension level something to be desired. i measured 18% spoke tension loss on the non drive side for two different loads on the rear wheel (measured by putting the wheel stand on the weighing scale with the load on the saddle). i did so by having myself on the bike and also a friend of mine which happens to have about 310 pounds (~140kg). i just thought it's relatively easy to measure so i did. most people have about 30-35% NDS tension loss as a function of load.
if having butted spokes on the NDS then a lower tension would be desired but i won't change the spokes for two reasons: 1. added cost and 2. lower strength to abuse by vandalism or direct accidental impacts to the spokes. i studied extensively and i am quite sure that the current spoke tension i have on the spokes is not excessive.
i do not recommend going that high (almost 180kgf) for most people that are not meticulous as to the radial runout / tension variance thing. if using a new rim that had no need for straightening i would have picked thinner spokes for NDS and i would have settled for standing on the wheel with the axle pressing on the floor at the goal spoke tension and that would have been all the work i would have done. there is a limit when using thinner spokes imposed by the torsional stress - that's why i wax lubricate.
i am only saying it works - because it did - and a wheelbuilder should be having all his homework done before trying this procedure.
and i do recommend people study as to find out for themselves what the flexural stresses (compression and tensional stresses) on the rim would be for some parameters or others.
some people go by feel, others study with numbers and learn about the strain-stress curves in tension and compression for spokes and for rims.
that's why i will say again: YMMV.
i had to do all this because i needed to fix the rim which was bent out of shape and had an extended flat spot over almost 3 spokes.
i could have just changed the rim but i was and still am on a low budget. had to borrow money to buy the bike and am struggling to make ends meet.
i had several bikes which have lost (stolen), one of them had a TK 540 rim (front wheel, rim brake) with DT Rev spokes that were almost 120kgf and i bought it in order to fix it (visible flat spot, about 1mm, fixed). it was the first wheel i worked on. don't ask me how i managed to go to 120kgf on the 1.5mm spokes without twisting the spokes into plastic deformation... someone who had no clue to wheelbuilding chose at the factory to have DT Prolock nipples (loctite like paste inside aluminum spokes) for those wheels and the tension when i bought it was all over the place and no more than 70-75kgf average. i changed to brass after i tried to work with the damn thing and had the surprise of getting to the loctite-like portion inside the nipples at less than 100kgf. i did not know yet about galvanic corrosion back then.
Last edited by adipe; 09-03-19 at 04:32 PM.
#56
Expired Member
Join Date: Jun 2007
Location: TN
Posts: 11,543
Mentioned: 37 Post(s)
Tagged: 0 Thread(s)
Quoted: 3674 Post(s)
Liked 5,433 Times
in
2,759 Posts
^^^ Good point

#57
working on my sandal tan
Join Date: Aug 2011
Location: CID
Posts: 22,629
Bikes: 1991 Bianchi Eros, 1964 Armstrong, 1988 Diamondback Ascent, 1988 Bianchi Premio, 1987 Bianchi Sport SX, 1980s Raleigh mixte (hers), All-City Space Horse (hers)
Mentioned: 98 Post(s)
Tagged: 0 Thread(s)
Quoted: 3871 Post(s)
Liked 2,568 Times
in
1,579 Posts
So if I'm reading you right, you're actually cranking up some of the spokes in order to straighten the rim? Apologies if that's what you've been trying to explain all along, it's just a foreign concept, and strikes me as risky. But it's hard to argue with success...
#58
Senior Member
adipe,
Thanks for clarifying your position regarding spoke tension. It sounds like you've worked on building wheels out of economic necessity. You might be interested in a guy named David Gingery. A few decades ago he wanted a machine shop but couldn't afford new machines. So he built (designed, made patterns and castings, machined, trued and finished) a set of reasonably good tools (lathe, milling machine,etc). You can read about it. Get "Build Your Own Metal Working Shop From Scrap" books from your library. Given your technical bent, may be of interest.
My understanding of Jobst's suggestion is that he viewed maximum spoke tension as the best way to avoid broken spokes or bent rims. Get the wheel true, then tighten up the spokes (while keeping things true and the spoke tensions even) until you have imminent taco. Then back off a bit to give yourself some safety margin from taco (SMFT).
If you get a good SMFT with 150kgf (!), good on you. But that seems really high to me.
As an engineer, I wonder too about the effect of rim distortions due to impact. For a perfectly round rim we may back off tension enough to have a good SMFT. But the moment we hit a bad pothole, the rim may be distorted (as the rim you mention was). Does this lessen our SMFT? Would a hard pothole hit put a really tight rim into taco mode, whereas a bit less tight setup would tolerate the hit better?
You mention cold working of the rim - an aspect I'd not thought about. Don't recall reading that in Brandt - did you come up with that? It makes some sense. But I'm not sure of the magnitude of effect.
I'm still going to disagree with you about not putting a slight (2-3)° bend in the spoke so that the nipple is not too canted in the spoke hole. I think its a good idea if the nipple is constrained enough so that you see a bend in the spoke. For the reason I mentioned: if the nipple is sufficiently canted, it creates a high stress point at the hole. Your point about not marring the spoke surface is one to keep in mind, so bending without scratching is key.. Brandt suggests that you can bend the spokes with your hands. If that was every possible for me, it was long in the past. I don't see how you can (even with 180kgf non-drive-side) get the spokes to bend so that the nipple's not canted. In fact, if high spoke tension DID bend the spoke with spoke tension alone we're into the plastic deformation range of the stress-strain curve, but we have no control of WHERE the bend occurs.
I had to look up Sod's law. Basically another belief that the universe conspires against you, and what you need is never there when you need it. (My understanding). Like when you need money, you don't have it. (Reminds me of trying to take out a loan: if you need it, they don't want to lend it!). It is also known as Finagle’s Law of Negative Dynamics or Finagle’s corollary to Murphy’s Law. (according to the American Thinker). I can't complain about being poor, but I think that everyone, rich and poor, has problems. Easier to deal with some of them if you've means. The trivial problems apply to everyone: Where is that d****d 3.5mm ball-end hex driver when I need it?
Thanks for clarifying your position regarding spoke tension. It sounds like you've worked on building wheels out of economic necessity. You might be interested in a guy named David Gingery. A few decades ago he wanted a machine shop but couldn't afford new machines. So he built (designed, made patterns and castings, machined, trued and finished) a set of reasonably good tools (lathe, milling machine,etc). You can read about it. Get "Build Your Own Metal Working Shop From Scrap" books from your library. Given your technical bent, may be of interest.
My understanding of Jobst's suggestion is that he viewed maximum spoke tension as the best way to avoid broken spokes or bent rims. Get the wheel true, then tighten up the spokes (while keeping things true and the spoke tensions even) until you have imminent taco. Then back off a bit to give yourself some safety margin from taco (SMFT).
If you get a good SMFT with 150kgf (!), good on you. But that seems really high to me.
As an engineer, I wonder too about the effect of rim distortions due to impact. For a perfectly round rim we may back off tension enough to have a good SMFT. But the moment we hit a bad pothole, the rim may be distorted (as the rim you mention was). Does this lessen our SMFT? Would a hard pothole hit put a really tight rim into taco mode, whereas a bit less tight setup would tolerate the hit better?
You mention cold working of the rim - an aspect I'd not thought about. Don't recall reading that in Brandt - did you come up with that? It makes some sense. But I'm not sure of the magnitude of effect.
I'm still going to disagree with you about not putting a slight (2-3)° bend in the spoke so that the nipple is not too canted in the spoke hole. I think its a good idea if the nipple is constrained enough so that you see a bend in the spoke. For the reason I mentioned: if the nipple is sufficiently canted, it creates a high stress point at the hole. Your point about not marring the spoke surface is one to keep in mind, so bending without scratching is key.. Brandt suggests that you can bend the spokes with your hands. If that was every possible for me, it was long in the past. I don't see how you can (even with 180kgf non-drive-side) get the spokes to bend so that the nipple's not canted. In fact, if high spoke tension DID bend the spoke with spoke tension alone we're into the plastic deformation range of the stress-strain curve, but we have no control of WHERE the bend occurs.
I had to look up Sod's law. Basically another belief that the universe conspires against you, and what you need is never there when you need it. (My understanding). Like when you need money, you don't have it. (Reminds me of trying to take out a loan: if you need it, they don't want to lend it!). It is also known as Finagle’s Law of Negative Dynamics or Finagle’s corollary to Murphy’s Law. (according to the American Thinker). I can't complain about being poor, but I think that everyone, rich and poor, has problems. Easier to deal with some of them if you've means. The trivial problems apply to everyone: Where is that d****d 3.5mm ball-end hex driver when I need it?
i consider the rim as working like a bridge that has points of equilibrium and an external load added on top of the internal load of the spokes in that gap between the equilibrium points when the large external load occurs. the total load (external + spokes in A, B, B, A tension, you get the picture) can be as high as about 600kgf for about 400kgf external load. the thicker the spokes the less the internal load is for a given deflection of the rim so you can only get the strongest possible wheel for a given rim by staying with such DT Alpine spokes. if i were to design a wheel i would take a wider (30+ outer width as opposed to 27mm current) and therefore also heavier rim, about 2mm spokes for DS, 1.8mm spokes for NDS. but i'm stuck with what people at the factory chose to equip these bikes wheels and the only thing i am not happy about after the fix - but also don't mind too much - is the rim width that is still not as wide for my tire preference which is 2.35-2.5" (now it is 2"). a wider, heavier rim would mean a more stable tire and more comfortable ride at somehow lower pressures. the weight of the wheel would have been quite the same with thinner spokes on the NDS. for 1.8mm on the NDS i would go at least 135kgf DS with a 36h wheel.
the safety margin as you call it implies that the rim is still strong enough to sustain the hit of an external load for a given average tension. the goal is to have the NDS approach zero for that large external load that is taken in consideration for this safety margin thing. i never met this "SMFT" term before and i am curious what FT means.
so i do not recommend having as large tension when using butted spokes because if the rim is deflected a certain amount (like when vertically hitting a pothole with no tire to spread the load) and then it is at it's yield for that deflection it's not the best thing to have the spoke tension still high. the extreme external load should have the spokes approaching zero tension, not remain under considerably high tension. there's also the aspect that the spokes at the 4:30 and 7:30 positions are in higher tension so that if there are butted spokes on the NDS then the DS will do more of the work keeping the rim and therefore having higher momentary tension. so YMMV. i went to this 144kgf tension - that is after the tire is inflated - especially as the spokes are shorter than usual (250mm with 2x on a 128mm flange diameter) spokes and having on both flanges the same DT Alpine spokes selected at the factory on a 36h rim that's about 500g.
it's because of the wheel not having butted spokes on the NDS (unproper selection/design) and also the poor job of wheelbuilding at the factory that the wheel was vulnerable to reach the state it was in before i bought it. that and... the heavy braking on the rear wheel with bumps of all kinds. but the previous owner was not over 90kg.
i don't reject putting a bend to the spoke at the nipple at low tensions, i am just saying that i'd rather not rely on it but more on the hard parallel grabbing technique or standing on the wheel with it lying on the axle or on the hub flange etc. having very high tension momentarily will bend the spokes where they are near the yield point. if it does not happen then fatigue will work them until they break. i went on to increase NDS so as to be almost equal to the indirectly raised DS (180kgf) because i needed to straighten the rim without hitting it etc. it's better to slowly put force on the rim and not hit it.
you may research here the strain-stress curve for 6061-T6 in compression:
https://hemi.jhu.edu/public-data/met...eries/adesola/
later edit: this link is more direct (checked the one above and it was not working at the time): https://hemi.jhu.edu/wp-content/uplo...8/07/ss1-2.png
i got from here the information that 2% strain in compression is alright for cold working 6061-T6 so that the yield strength gets increased with not too much ductility loss (by changing grain size):
https://digitalcommons.lmu.edu/cgi/viewcontent.cgi?referer=https://www.google.com/&httpsredir=1&article=1000&context=mech_fac
a bent out of shape rim can be harder to straighten than an imperfect new rim... because of the cold work done to it.
i figured the cold working of the rim on my own, i have not found yet anywhere anything written on this subject in a bike specific context. so you can quote me on that, together with the linked sources above. some people follow ritualistically procedures without trying to understand how they work in order to not copy the wrong things together with the good practices and be able to differentiate and figure out what average spoke tension would be best for a given tension variance and for the spoke thickness you may or may not be able to choose for different reasons.
the quite old practice of reaching high tensions is established but it can be dangerous if you don't know what you do because you can deform the wheel radially if you don't precisely balance radial runout with spoke tension variance.
apply the elastic modulus concept (about 179GPa for spokes that are not slack, its higher for slack spokes and therefore irrelevant because you do the tuning on the DS when the NDS are rather slack) to figure out how much more the spokes are stretched from the average level for given +/- tension in kgf or newtons.
if you (not necessarily the singular "you", other people maybe) still are not sure you get what i mean... imagine you later somehow achieve zero radial runout without touching the DS nipples anymore. will the spokes have zero tension variance? if not then you haven't balanced runout with tension variance. that's the principle.
when you understand these things you will be able to build a wheel with much less effort than i put into researching all this and also using zip ties and a tone generator to get the tension for each spoke. i am poor, you are rich. the 2mm constant section between the cross and the nipple afforded me the certainty of having the average tension i know to have. if the spokes would have been butted i would not have had a precise assessment of the average tension but still would have had precise spoke tension variance figures for tuning purposes - calculating how much to turn each nipple on the DS before continuing to work exclusively with NDS. two columns of input data in a spreadsheet, one for the tensions for each spoke, one for radial runout for each spoke. i struggled to measure radial runout with a laser tool that put a line on the wall so that the ratio of the distance to the rim (about 4cm) to the further distance to the wall was to make a considerable amplifying factor.
you can just guestimate when balancing radial true with tension variance but that would mean you are doing a sloppier work more often and sometimes have luck.
wheelbuilders with more expensive tools should be able to do the work much faster because they will measure in a much shorter time these things but it's a sad thing that they charge the money they charge for sloppy work. my intention is to give the general public this information so that either they can be able to know which work is sloppy and which work is not... or even better... buy a spoke key, maybe a laser thing... and get a tone generator that's available online for tension measurement. all it takes is to have the same spoke model on the drive side flange. i could work without a cheap laser tool on a new unbent rim by achieving almost zero radial runout and just measure the spoke tension so that i would have adjustments computed using only one collumn, it could be more tedious to achieve zero radial runout at medium tension with zip ties.
for people who don't know the formula to calculate tension by having known distance, thickness, frequency (Hz): T = πf²L²d²δ
explanations to be found following this link.
regarding Sod's Law:
i just am constrained to avoid risks and the funny aspect of the Sod's law is that people can get the conclusion that if something can go wrong it may very well (and think that will be so because of the biased perception thing added to the murphy's law) go wrong right at the worst possible moment with the worst outcome.
Last edited by adipe; 09-04-19 at 06:37 AM.
#59
Senior Member
Thread Starter
Wish I could, but all shops within reasonable range to me have built wheels like this. This latest rebuild is going to cost $180, which I don't really have. I'm going to have to start cutting into essentials soon just so I can get to work. Though this time I flat out will not accept or pay for a build that is that bad.
I don't recall which one it was, but it was very thick and heavy. It was also a bit wider than my current rim. The bill I have just says velo blunt.
#60
Senior Member
Wish I could, but all shops within reasonable range to me have built wheels like this. This latest rebuild is going to cost $180, which I don't really have. I'm going to have to start cutting into essentials soon just so I can get to work. Though this time I flat out will not accept or pay for a build that is that bad.
I don't recall which one it was, but it was very thick and heavy. It was also a bit wider than my current rim. The bill I have just says velo blunt.
I don't recall which one it was, but it was very thick and heavy. It was also a bit wider than my current rim. The bill I have just says velo blunt.
if new to wheelbuilding an eyeleted rim will be safer to work on. be sure to lubricate both the threads and eyelets/nipples interface.
best lube is bolt lube which is wax based. wax is a solid lubricant that is not best to transfer heat but the heat generated by the friction of nipples turning is quite low.
nipples will not uncrew because of the friction being lowered but they will unscrew more easily at zero tension if not lubricated properly. don't use moly nor graphite as they promote galvanic corrosion of the nipples or rim.
the brainy thing to do is use a spreadsheet to translate into mm the amount of higher or lower tension spoke from the average on each DS and corelate that data with the radial runout. put labels on DS spokes as to be sure they are not under elastic twist after your turn the nipples. the elastic twist will impose added unnecessary stresses on the rim at high tension.
179GPa is a rough estimation for the elastic modulus of the stainless steel when under not a very low tension. about 206GPa is the value for low tension but you can ignore that.
9.8/3.14159/179000*290mm gets you that 0.005mm elongation for +9.8newtons in tension from the average.
(newtons/section area/modulus*spoke length)
after you balance radial runout with tension variance everything will go very smooth. i can't remember at which tension i did this thing, it's somewhere under 70kgf with the NDS slack.
when you later on check dish - you can turn the wheel in reverse to compare - you can settle with about 0.5mm towards the brake disc because when you inflate the tire the rim will go towards the cassette, the dish will change for the better. the wheelbuilder's dilemma is: should i try to have zero dish or should i move the wheel away from the cassette as a compromise to increase durability? how much will the tire be inflated? will the user obsess over perfect dish?
in order to adjust dish if needed after you raise the NDS and the DS is too high or too low i would advise you to put labels on the rim to mark the position of the DS nipples so that you are able to turn them exactly n*90 degrees each and have as low error as possible. you may also do a final radial and spoke tension variance adjustment/check if you want to.
typical spokes that are 2mm near the nipples have 0.45mm thread pitch so you can calculate the angle to turn using the spoke key after calculating how much is needed to adjust in order to achieve radial with tension variance balance.
https://www.szynalski.com/tone-generator/
i have a not so good at music friend i asked to tell me if he can differentiate between 600Hz and 604Hz and he told me he had no trouble discerning the difference. that difference would mean just a bit more than 1kgf. pluck spokes holding the other crossed one to be silent and alternate to better assess the frequency. they will make each other vibrate... because they cross.
1kgf error in assessing spoke tension can mean 0.005mm (5 microns) elongation for a 2mm thick spoke.
it's much harder to have the same precision when you measure radial true at each spoke so the precision is alright. the most important thing is to do the data gathering and computing.
if you correlate this input data and the resulting values you will be able to do a better job than wheelbuilders that have not figured these things out or that prefer to do sloppy work by guestimation and not spend more time.
don't expect to educate them as most people will take it as recognizing as having a weakness if you dare try educating them.
the least resistance would be from people with no qualifications, the qualified "experts" will tend to get vocal and dismiss anything new that's come from a perceived amateur and maybe some of them will secretly study the thing later. or they might as well say that their intuition is very accurate and therefore just lie about it because they never test their intuition. not many pluck the spokes to listen to them and a semitone difference means a 12% tension variance.
i don't have many posts on this forum about wheelbuilding. you can search the other posts on similar threads you can fill in stuff if needed, get the picture, understand the procedure and how to do the computing.
and you need not reach high tension in order to back off with a new rim. but make sure you stress relieve the wheel and learn how to do it properly.
i suggest having someone show you how hard parallel spokes should be grabbed. you should be able to pluck spokes if you choose to stand on the rim with the axle pressing on the floor but only do so when it's precisely laterally trued at each stage of raising NDS tension, supposing you adjusted correctly for radial runout / tension variance. when plucking spokes you can compare to the tone generator so that you make sure the spokes don't go considerably higher than 200kgf
i say "stand on the rim" because that's what i did when working on my first wheel that had 1.5mm thin spokes. i do not know your weight so... YMMV.
the more tensioned the spokes the more weight you can put on the rim in this manner. be careful and take notice that the spokes that go lower tension momentarily in this manner should not go zero tension.
for example... i was pressing on the rim (TK 540) with all my weight at the final ~120kg tension for the dishless front wheel;
plucking the spokes when i was standing on the rim they were at almost 190kgf which was quite high for that 1.5mm section diameter so you get the picture.
i would choose a safe 2x with the large flange as your hub motor has.
i am not sure about mixing 2x DS with 3x NDS, it will help only with heavy braking and you should be able to brake relying on the front brake and not brake in pulses with the rear wheel going over bumps. i discarded the rear brake as being not too much use for me and thought to make room and take off weight. i rode for more than a year without a rear brake on the last bike which was a CX with riser bars. your NDS spokes (leading vs trailing) were breaking probably when braking over bumps.
Last edited by adipe; 09-03-19 at 09:15 PM.
#61
Senior Member
Join Date: Dec 2007
Location: San Jose, California
Posts: 3,504
Bikes: 2001 Tommasini Sintesi w/ Campagnolo Daytona 10 Speed
Mentioned: 5 Post(s)
Tagged: 0 Thread(s)
Quoted: 145 Post(s)
Likes: 0
Liked 35 Times
in
30 Posts
Wow...just wow...
1. Most alloy rims are rated for 90kgf to 110kgf tension AFTER a proper stress relieving cycle has been done.
2. Select makes and models can survive 110kgf to 130kgf.
3. What Jobst meant by max tension that a rim can handle was simply:
- Tension - cyclically upwards.
- Stress relieve via super hard squeezes of parallel spokes.
- If rim stays true, dished, good to go OR good for another tension cycle. (judgement call)
- If not, you may - JUST may be slightly overtensioned - back off a 1/4 to 1/2 turn.
4. When Jobst referred to 130-150 kgf or a 50% tension add-on, he was talking about the rough temporary point reached during a stress relieve cycle.
5. When Jobst AND other folks in his "circle" talked about 180kgf, 190kgf, etc., they're referring to the fact that our spokes we use have a tension capacity waaaay beyond what they will ever be required to support bicycle wheels. In other words, we do not need stronger spokes...they have tons of overhead already.
As a matter of fact, if tension capacity were all we cared for, we'd still be riding plain Jane zinc steel spokes. We'd just be breaking spokes more often. There's a reason we've switched to softer stainless steel.
6. Building wheels to 150kgf?
- You're violating the warranty of 99% of the rims out there BOTH alloy AND carbon.
- 80% wouldn't last beyond 6 months of everyday riding - spoke/nipple pull through AND/OR eyelet/hole separation via immediate and nearby material.
- Wheels probably wobble moment tire is inflated - goes away upon deflation - a clear signal of extreme overtensioning.
7. Pressing down on the sides of the rim of a wheel IS NOT STRESS RELIEVING.
- Super hard squeezes of parallel spokes. (Jobst)
- Bracing rim circumferentially AND bracing hub while walking the spokes. (Jobst)
- Paired spoke inward press by hydraulic machine by a tested measured amount (Mass production motorcycle wheel line.)
- Crank arm twist. (Sheldonbrown.com)
That snake oil #7 is really old - same for tying and soldering for strength, no-dish/zero dish wheel, etc.
Seems every ten years, someone digs 'em back up from the dead so they can make a name for themselves as an "expert" or to make a quick "buck" on the gullible.
=8-|
1. Most alloy rims are rated for 90kgf to 110kgf tension AFTER a proper stress relieving cycle has been done.
2. Select makes and models can survive 110kgf to 130kgf.
3. What Jobst meant by max tension that a rim can handle was simply:
- Tension - cyclically upwards.
- Stress relieve via super hard squeezes of parallel spokes.
- If rim stays true, dished, good to go OR good for another tension cycle. (judgement call)
- If not, you may - JUST may be slightly overtensioned - back off a 1/4 to 1/2 turn.
4. When Jobst referred to 130-150 kgf or a 50% tension add-on, he was talking about the rough temporary point reached during a stress relieve cycle.
5. When Jobst AND other folks in his "circle" talked about 180kgf, 190kgf, etc., they're referring to the fact that our spokes we use have a tension capacity waaaay beyond what they will ever be required to support bicycle wheels. In other words, we do not need stronger spokes...they have tons of overhead already.
As a matter of fact, if tension capacity were all we cared for, we'd still be riding plain Jane zinc steel spokes. We'd just be breaking spokes more often. There's a reason we've switched to softer stainless steel.
6. Building wheels to 150kgf?
- You're violating the warranty of 99% of the rims out there BOTH alloy AND carbon.
- 80% wouldn't last beyond 6 months of everyday riding - spoke/nipple pull through AND/OR eyelet/hole separation via immediate and nearby material.
- Wheels probably wobble moment tire is inflated - goes away upon deflation - a clear signal of extreme overtensioning.
7. Pressing down on the sides of the rim of a wheel IS NOT STRESS RELIEVING.
- Super hard squeezes of parallel spokes. (Jobst)
- Bracing rim circumferentially AND bracing hub while walking the spokes. (Jobst)
- Paired spoke inward press by hydraulic machine by a tested measured amount (Mass production motorcycle wheel line.)
- Crank arm twist. (Sheldonbrown.com)
That snake oil #7 is really old - same for tying and soldering for strength, no-dish/zero dish wheel, etc.
Seems every ten years, someone digs 'em back up from the dead so they can make a name for themselves as an "expert" or to make a quick "buck" on the gullible.
=8-|
__________________
5000+ wheels built since 1984...
Disclaimer:
1. I do not claim to be an expert in bicycle mechanics despite my experience.
2. I like anyone will comment in other areas.
3. I do not own the preexisting concepts of DISH and ERD.
4. I will provide information as I always have to others that I believe will help them protect themselves from unscrupulous mechanics.
5. My all time favorite book is:
Kahane, Howard. Logic and Contemporary Rhetoric: The Use of Reason in Everyday Life
5000+ wheels built since 1984...
Disclaimer:
1. I do not claim to be an expert in bicycle mechanics despite my experience.
2. I like anyone will comment in other areas.
3. I do not own the preexisting concepts of DISH and ERD.
4. I will provide information as I always have to others that I believe will help them protect themselves from unscrupulous mechanics.
5. My all time favorite book is:
Kahane, Howard. Logic and Contemporary Rhetoric: The Use of Reason in Everyday Life
Last edited by mrrabbit; 09-03-19 at 09:16 PM.
#62
Generally bewildered
Join Date: Aug 2015
Location: Eastern PA, USA
Posts: 3,037
Bikes: 2014 Trek Domane 6.9, 1999 LeMond Zurich, 1978 Schwinn Superior
Mentioned: 20 Post(s)
Tagged: 0 Thread(s)
Quoted: 1152 Post(s)
Liked 341 Times
in
251 Posts
So SMFT is an ironic term I just invented to be humorous. But it does apply.
Forgive me if you're native land is Mexico (and you know tacos well), but in case your not familiar this is a taco shell:
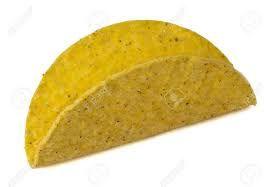
This is a wheel that is "tacoed" (it also has its pin joints compromised, but that's another subject):
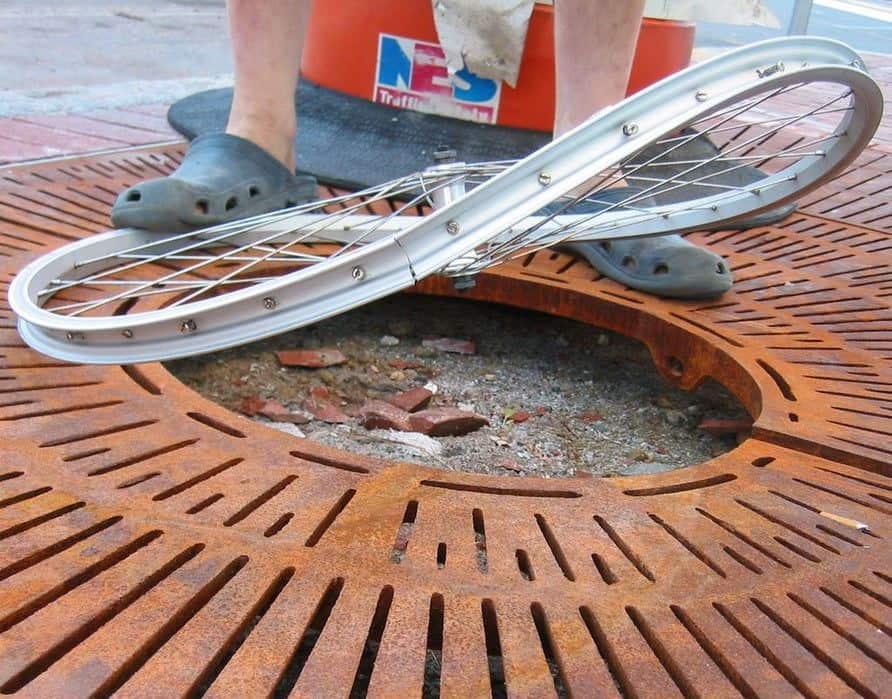
So one method of wheel construction is to tighten your spokes until the wheel just barely begins to "taco", and then back off and lower the tension. I used the (hopefully humorous) term "Safety Margin From Taco" to denote how much you back off the spoke tension. So SMFT is a made-up, humorous term for a real thing.
The real question I had was, if you start out near tight enough to taco, and you hit a bad bump and the wheel is deformed, would the wheel taco? That is, is there such a thing as being too close to a tacoed wheel. Is there a minimum SMFT?
Forgive me if you're native land is Mexico (and you know tacos well), but in case your not familiar this is a taco shell:
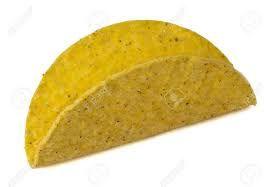
This is a wheel that is "tacoed" (it also has its pin joints compromised, but that's another subject):
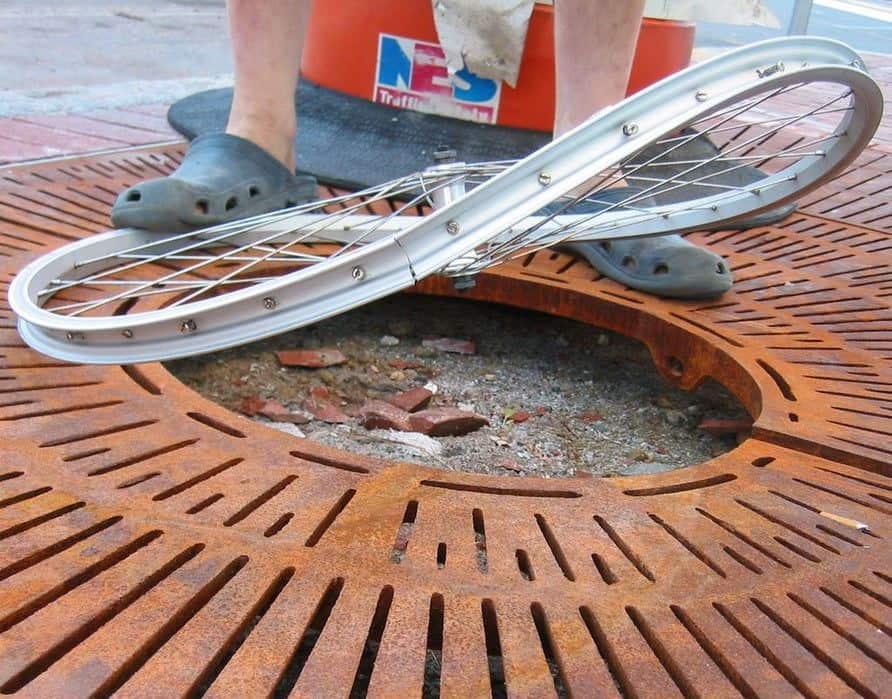
So one method of wheel construction is to tighten your spokes until the wheel just barely begins to "taco", and then back off and lower the tension. I used the (hopefully humorous) term "Safety Margin From Taco" to denote how much you back off the spoke tension. So SMFT is a made-up, humorous term for a real thing.
The real question I had was, if you start out near tight enough to taco, and you hit a bad bump and the wheel is deformed, would the wheel taco? That is, is there such a thing as being too close to a tacoed wheel. Is there a minimum SMFT?
Last edited by WizardOfBoz; 09-03-19 at 10:18 PM.
#63
Generally bewildered
Join Date: Aug 2015
Location: Eastern PA, USA
Posts: 3,037
Bikes: 2014 Trek Domane 6.9, 1999 LeMond Zurich, 1978 Schwinn Superior
Mentioned: 20 Post(s)
Tagged: 0 Thread(s)
Quoted: 1152 Post(s)
Liked 341 Times
in
251 Posts
PS, mrrabbit builds wheels as a business and a lot of folks here seem to have a good opinion of him. His note (above mine) is useful reading. But we may be mis-reading your comments, adipe.
#64
Passista
Join Date: Jul 2005
Posts: 7,598
Bikes: 1998 Pinarello Asolo, 1992 KHS Montaña pro, 1980 Raleigh DL-1, IGH Hybrid, IGH Utility
Mentioned: 5 Post(s)
Tagged: 0 Thread(s)
Quoted: 867 Post(s)
Liked 721 Times
in
396 Posts
So SMFT is an ironic term I just invented to be humorous. But it does apply.
Forgive me if you're native land is Mexico (and you know tacos well), but in case your not familiar this is a taco shell:
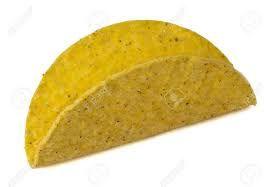
This is a wheel that is "tacoed" (it also has its pin joints compromised, but that's another subject):
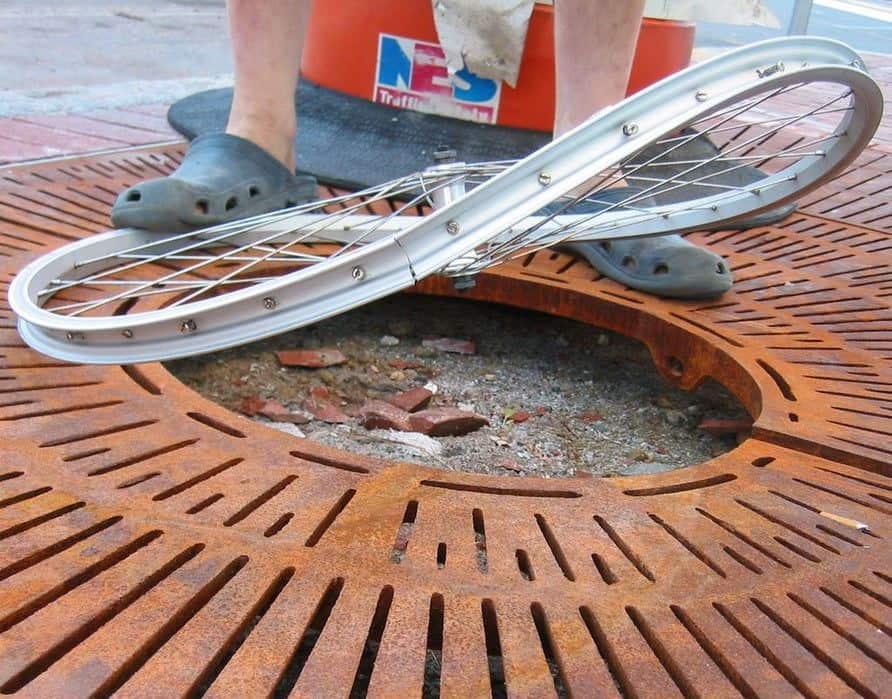
So one method of wheel construction is to tighten your spokes until the wheel just barely begins to "taco", and then back off and lower the tension. I used the (hopefully humorous) term "Safety Margin From Taco" to denote how much you back off the spoke tension. So SMFT is a made-up, humorous term for a real thing.
The real question I had was, if you start out near tight enough to taco, and you hit a bad bump and the wheel is deformed, would the wheel taco? That is, is there such a thing as being too close to a tacoed wheel. Is there a minimum SMFT?
Forgive me if you're native land is Mexico (and you know tacos well), but in case your not familiar this is a taco shell:
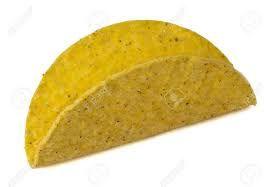
This is a wheel that is "tacoed" (it also has its pin joints compromised, but that's another subject):
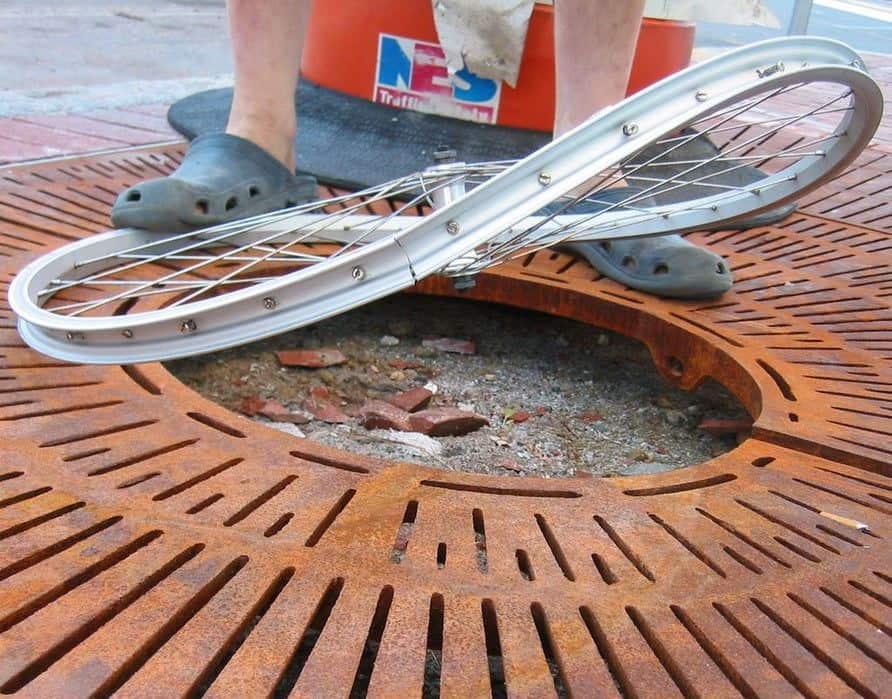
So one method of wheel construction is to tighten your spokes until the wheel just barely begins to "taco", and then back off and lower the tension. I used the (hopefully humorous) term "Safety Margin From Taco" to denote how much you back off the spoke tension. So SMFT is a made-up, humorous term for a real thing.
The real question I had was, if you start out near tight enough to taco, and you hit a bad bump and the wheel is deformed, would the wheel taco? That is, is there such a thing as being too close to a tacoed wheel. Is there a minimum SMFT?

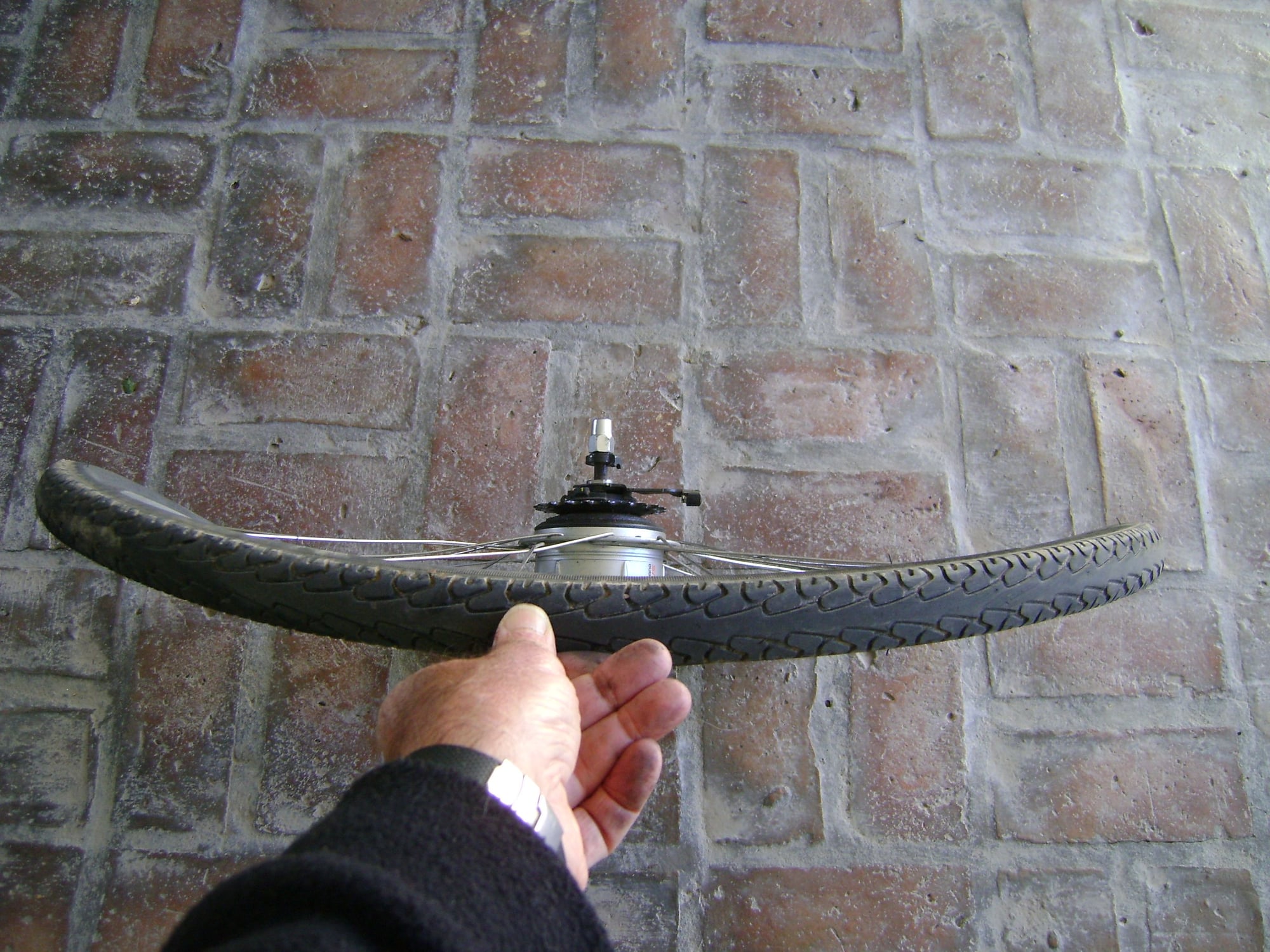
#65
Senior Member
i get attacked after i explain how things work. credit is not given. it seems that people feel insecure and therefore attack to defend their ignorance.
insulted. yet again. as if i were selling "snake oil". i don't sell anything. others people sell their sloppy work. i never bragged of having built thousands of wheels.
there is not much strength in such numbers except for people who are not able to study structural engineering but rely solely on anecdotal evidence and established dogma.
i don't build wheels in order to take people's money. others do and some of them will attack me to present themselves as victorious over the other person.
bogus arguments thrown in the attack.
ask any engineer friend you might have to study the data using numbers, flexural stress of the arch etc. and you might have these truths certified.
i might have patented a software to assist the wheel builder in gathering data and getting computations done for the amount of spoke key turn for each nipple etc.
how about that? would you rather have secret or patented science or aren't you glad that i instead have given for free very useful information to back up my claims for the way i built my wheels? and i build disregarding the "warranty" aspect of it because i have no use for it. i have not worked with new rims, my work was much harder in fixing bent out of shape rims. low budget.
but hey, some people who aren't struggling to make ends meet attack me and present their reputation as an argument. i presented better arguments but got obscured by the avalanche of pointed bogus arguments against the scientific arguments about grain size structure that gets finer by cold working so that you would benefit from a higher yield strength of the rim IF you need not a downhill work but more like what touring people seek which is durability and not too much rim deflection that makes a small contribution to radial give but also makes the wheel more vulnerable to accidents. the safety margin thing.
any wheel builder can know that you may exceed the maximum tension given by the manufacturer to the general public... if spoke tension is kept at a much lower variance than usually tolerance which is +/-20% (park tool literature).
i have also given the strain hardening details regarding the 6061-T6 on a respectable independent source to establish the 2% strain cold work (here, again) which corresponds to about 200MPa (strain stress curve link provided right next to the other link about the cold working aspect - later edit: take this link) if you take the time to read my post which i wrote yesterday.
if you can't figure out the tensional stress for the rim around the spoke hole for a certain tension of the spokes and the equilibrium points thing... spare me the direct personal attacks or i might bite back somehow.
i have not exceeded the 96.5MPa fatigue recommendation (for tension stress) for the 6061-T6 in static load of the rim due to flexural stress.
the wheel experiences less variance in dynamic strain the more the spokes compress the rim.
the general recommendation also does not mention stress corrosion cracking due to the chemical factor which can be prevented. but who am i do disagree with general practice?...
and here's one more thing... you might search to find fatigue cycles until break for salty conditions vs normal air, you might have a surprise.
here's an example.
these are verifiable scientific arguments, i'm not relying on anecdotal evidence or general practice and methods.
insulted. yet again. as if i were selling "snake oil". i don't sell anything. others people sell their sloppy work. i never bragged of having built thousands of wheels.
there is not much strength in such numbers except for people who are not able to study structural engineering but rely solely on anecdotal evidence and established dogma.
i don't build wheels in order to take people's money. others do and some of them will attack me to present themselves as victorious over the other person.
bogus arguments thrown in the attack.
ask any engineer friend you might have to study the data using numbers, flexural stress of the arch etc. and you might have these truths certified.
i might have patented a software to assist the wheel builder in gathering data and getting computations done for the amount of spoke key turn for each nipple etc.
how about that? would you rather have secret or patented science or aren't you glad that i instead have given for free very useful information to back up my claims for the way i built my wheels? and i build disregarding the "warranty" aspect of it because i have no use for it. i have not worked with new rims, my work was much harder in fixing bent out of shape rims. low budget.
but hey, some people who aren't struggling to make ends meet attack me and present their reputation as an argument. i presented better arguments but got obscured by the avalanche of pointed bogus arguments against the scientific arguments about grain size structure that gets finer by cold working so that you would benefit from a higher yield strength of the rim IF you need not a downhill work but more like what touring people seek which is durability and not too much rim deflection that makes a small contribution to radial give but also makes the wheel more vulnerable to accidents. the safety margin thing.
any wheel builder can know that you may exceed the maximum tension given by the manufacturer to the general public... if spoke tension is kept at a much lower variance than usually tolerance which is +/-20% (park tool literature).
i have also given the strain hardening details regarding the 6061-T6 on a respectable independent source to establish the 2% strain cold work (here, again) which corresponds to about 200MPa (strain stress curve link provided right next to the other link about the cold working aspect - later edit: take this link) if you take the time to read my post which i wrote yesterday.
if you can't figure out the tensional stress for the rim around the spoke hole for a certain tension of the spokes and the equilibrium points thing... spare me the direct personal attacks or i might bite back somehow.
i have not exceeded the 96.5MPa fatigue recommendation (for tension stress) for the 6061-T6 in static load of the rim due to flexural stress.
the wheel experiences less variance in dynamic strain the more the spokes compress the rim.
the general recommendation also does not mention stress corrosion cracking due to the chemical factor which can be prevented. but who am i do disagree with general practice?...
and here's one more thing... you might search to find fatigue cycles until break for salty conditions vs normal air, you might have a surprise.
here's an example.
these are verifiable scientific arguments, i'm not relying on anecdotal evidence or general practice and methods.
Last edited by adipe; 09-04-19 at 06:30 AM.
#66
Expired Member
Join Date: Jun 2007
Location: TN
Posts: 11,543
Mentioned: 37 Post(s)
Tagged: 0 Thread(s)
Quoted: 3674 Post(s)
Liked 5,433 Times
in
2,759 Posts
^^^ Be not discouraged, prophets often travel a hard road!
#67
Generally bewildered
Join Date: Aug 2015
Location: Eastern PA, USA
Posts: 3,037
Bikes: 2014 Trek Domane 6.9, 1999 LeMond Zurich, 1978 Schwinn Superior
Mentioned: 20 Post(s)
Tagged: 0 Thread(s)
Quoted: 1152 Post(s)
Liked 341 Times
in
251 Posts
Your pic looks like the brim part of a hat form for a sombrero. I don't know if I could even get a wheel to be that symmetrically distorted. Is that what others have experienced?
I think the key thing is that when you have a wheel that's true, and you ratchet up the tension, then
1) If the wheel starts to distort in a taco/8-bend shape, STOP. And then BACK OFF on the tension.
2) If the rim starts cracking at the nipple holes, STOP. Buy a new rim and replace the one you've knackered.
I'll reask my question: Once you get to incipient taco transition, how much should you back off? Is there a range that is too little? That is, will a wheel that is very close to taco be less stable than one that is backed off more?
I think the key thing is that when you have a wheel that's true, and you ratchet up the tension, then
1) If the wheel starts to distort in a taco/8-bend shape, STOP. And then BACK OFF on the tension.
2) If the rim starts cracking at the nipple holes, STOP. Buy a new rim and replace the one you've knackered.
I'll reask my question: Once you get to incipient taco transition, how much should you back off? Is there a range that is too little? That is, will a wheel that is very close to taco be less stable than one that is backed off more?
#68
Passista
Join Date: Jul 2005
Posts: 7,598
Bikes: 1998 Pinarello Asolo, 1992 KHS Montaña pro, 1980 Raleigh DL-1, IGH Hybrid, IGH Utility
Mentioned: 5 Post(s)
Tagged: 0 Thread(s)
Quoted: 867 Post(s)
Liked 721 Times
in
396 Posts
Your pic looks like the brim part of a hat form for a sombrero. I don't know if I could even get a wheel to be that symmetrically distorted. Is that what others have experienced?
I think the key thing is that when you have a wheel that's true, and you ratchet up the tension, then
1) If the wheel starts to distort in a taco/8-bend shape, STOP. And then BACK OFF on the tension.
2) If the rim starts cracking at the nipple holes, STOP. Buy a new rim and replace the one you've knackered.
I'll reask my question: Once you get to incipient taco transition, how much should you back off? Is there a range that is too little? That is, will a wheel that is very close to taco be less stable than one that is backed off more?
I think the key thing is that when you have a wheel that's true, and you ratchet up the tension, then
1) If the wheel starts to distort in a taco/8-bend shape, STOP. And then BACK OFF on the tension.
2) If the rim starts cracking at the nipple holes, STOP. Buy a new rim and replace the one you've knackered.
I'll reask my question: Once you get to incipient taco transition, how much should you back off? Is there a range that is too little? That is, will a wheel that is very close to taco be less stable than one that is backed off more?
#69
Senior Member
Join Date: Jun 2003
Posts: 668
Mentioned: 0 Post(s)
Tagged: 0 Thread(s)
Quoted: 140 Post(s)
Liked 72 Times
in
48 Posts
I think le mans is onto something here. Those spoke nipples look like they have no ability to swivel. Which made me think: "Could those spokes be US/British 13 gauge - 2.3mm, rather than 14 gauge - 2.0mm)?". Can you measure the spoke gauge? If the spokes are too thick, and the nipples are proportional, then they won't swivel at all. Which appears to be the case.
The Jobst Brandt method of tensioning the wheel almot to failure before backing off tension won't work on modern wheels. He favored old school 36 spoke wheels with light rims. Modern wheels have fewer spokes and stronger rims.
Changing the number of crosses won't change the angle from the rim much, unless you go to 1 cross. You could do that but you are still in for new spokes. It doesn't really matter how many crosses you use, but it's better to use lighter spokes with 36h wheels.
Tensioning the NDS to 180 kgf seems like madness. That would take the drive side to somewhere north of 300 kgf. That's close to the yield strength of some lighter spokes, even without considering twisting. Maybe it's more than some rims can hold also. (I have an old Mavic manual that recommends 90-110 kgf for the drive side.)
em
#70
Generally bewildered
Join Date: Aug 2015
Location: Eastern PA, USA
Posts: 3,037
Bikes: 2014 Trek Domane 6.9, 1999 LeMond Zurich, 1978 Schwinn Superior
Mentioned: 20 Post(s)
Tagged: 0 Thread(s)
Quoted: 1152 Post(s)
Liked 341 Times
in
251 Posts
That's the answer. Somewhere above the OP wrote that they were 2.3 mm spokes. With a 36 spoke wheel you don't need heavy spokes. Most rims aren't strong enough to adequately tension 36 2 mm spokes. Back in the day, I had 36 spoke wheels with 1.8 mm straight gauge spokes that were perfectly reliable.
The Jobst Brandt method of tensioning the wheel almot to failure before backing off tension won't work on modern wheels. He favored old school 36 spoke wheels with light rims. Modern wheels have fewer spokes and stronger rims.
The Jobst Brandt method of tensioning the wheel almot to failure before backing off tension won't work on modern wheels. He favored old school 36 spoke wheels with light rims. Modern wheels have fewer spokes and stronger rims.
Agree with everything else Eddy wrote. Interesting question regarding wheel weight, ride, strength and ability to withstand potholes and such: what is the balance between rim strength (and weight, and moment of inertia) and spoke number and gauge and weight and moment of inertia? Certainly 36 spoke wheels have a pretty good history and the support provided by 36 spokes allows you to whittle down the weight of an alloy rim. But with CF, you can get a VERY strong and rigid rim with low weight. So how much can you back off on number of spokes and spoke gauge?
#71
Generally bewildered
Join Date: Aug 2015
Location: Eastern PA, USA
Posts: 3,037
Bikes: 2014 Trek Domane 6.9, 1999 LeMond Zurich, 1978 Schwinn Superior
Mentioned: 20 Post(s)
Tagged: 0 Thread(s)
Quoted: 1152 Post(s)
Liked 341 Times
in
251 Posts
Kind of hard to blame that on spoke tension! Hope you were ok, and that the wheel was the only thing that got damaged (my custom Paramount had the rear triangle crumpled by a drunk hitting me, but I was ok so I guess I can't complain).
#72
working on my sandal tan
Join Date: Aug 2011
Location: CID
Posts: 22,629
Bikes: 1991 Bianchi Eros, 1964 Armstrong, 1988 Diamondback Ascent, 1988 Bianchi Premio, 1987 Bianchi Sport SX, 1980s Raleigh mixte (hers), All-City Space Horse (hers)
Mentioned: 98 Post(s)
Tagged: 0 Thread(s)
Quoted: 3871 Post(s)
Liked 2,568 Times
in
1,579 Posts
They look to have the same issue to me, the pictures are just taken from different angles.

#73
Passista
Join Date: Jul 2005
Posts: 7,598
Bikes: 1998 Pinarello Asolo, 1992 KHS Montaña pro, 1980 Raleigh DL-1, IGH Hybrid, IGH Utility
Mentioned: 5 Post(s)
Tagged: 0 Thread(s)
Quoted: 867 Post(s)
Liked 721 Times
in
396 Posts
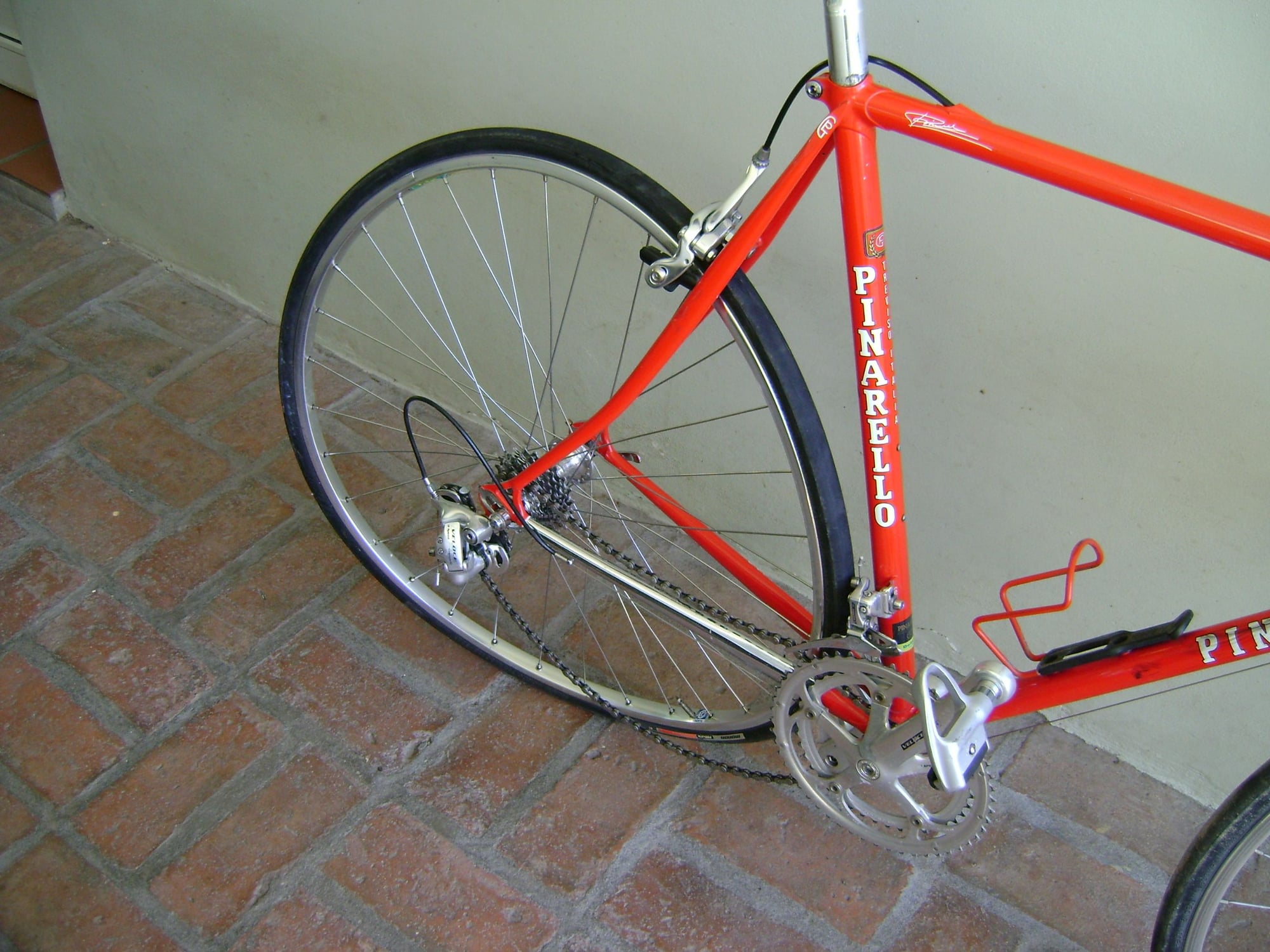
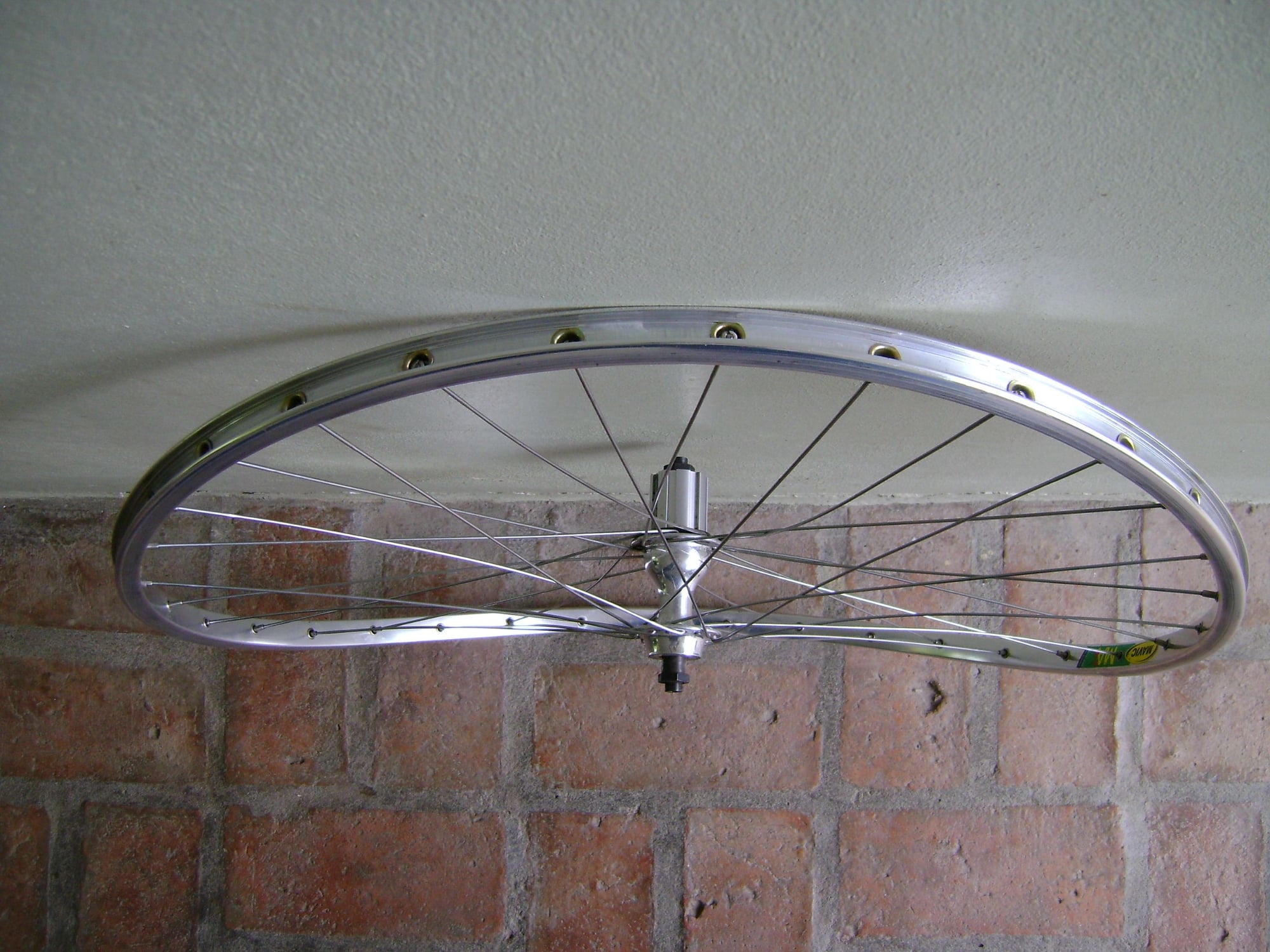
#74
Mostly harmless ™
Join Date: Nov 2010
Location: Novi Sad
Posts: 4,430
Bikes: Heavy, with friction shifters
Mentioned: 22 Post(s)
Tagged: 0 Thread(s)
Quoted: 1107 Post(s)
Liked 216 Times
in
130 Posts
i get attacked after i explain how things work. credit is not given. it seems that people feel insecure and therefore attack to defend their ignorance.
insulted. yet again. as if i were selling "snake oil". i don't sell anything. others people sell their sloppy work. i never bragged of having built thousands of wheels.
there is not much strength in such numbers except for people who are not able to study structural engineering but rely solely on anecdotal evidence and established dogma.
i don't build wheels in order to take people's money. others do and some of them will attack me to present themselves as victorious over the other person.
bogus arguments thrown in the attack.
ask any engineer friend you might have to study the data using numbers, flexural stress of the arch etc. and you might have these truths certified.
i might have patented a software to assist the wheel builder in gathering data and getting computations done for the amount of spoke key turn for each nipple etc.
how about that? would you rather have secret or patented science or aren't you glad that i instead have given for free very useful information to back up my claims for the way i built my wheels? and i build disregarding the "warranty" aspect of it because i have no use for it. i have not worked with new rims, my work was much harder in fixing bent out of shape rims. low budget.
but hey, some people who aren't struggling to make ends meet attack me and present their reputation as an argument. i presented better arguments but got obscured by the avalanche of pointed bogus arguments against the scientific arguments about grain size structure that gets finer by cold working so that you would benefit from a higher yield strength of the rim IF you need not a downhill work but more like what touring people seek which is durability and not too much rim deflection that makes a small contribution to radial give but also makes the wheel more vulnerable to accidents. the safety margin thing.
any wheel builder can know that you may exceed the maximum tension given by the manufacturer to the general public... if spoke tension is kept at a much lower variance than usually tolerance which is +/-20% (park tool literature).
i have also given the strain hardening details regarding the 6061-T6 on a respectable independent source to establish the 2% strain cold work (here, again) which corresponds to about 200MPa (strain stress curve link provided right next to the other link about the cold working aspect - later edit: take this link) if you take the time to read my post which i wrote yesterday.
if you can't figure out the tensional stress for the rim around the spoke hole for a certain tension of the spokes and the equilibrium points thing... spare me the direct personal attacks or i might bite back somehow.
i have not exceeded the 96.5MPa fatigue recommendation (for tension stress) for the 6061-T6 in static load of the rim due to flexural stress.
the wheel experiences less variance in dynamic strain the more the spokes compress the rim.
the general recommendation also does not mention stress corrosion cracking due to the chemical factor which can be prevented. but who am i do disagree with general practice?...
and here's one more thing... you might search to find fatigue cycles until break for salty conditions vs normal air, you might have a surprise.
here's an example.
these are verifiable scientific arguments, i'm not relying on anecdotal evidence or general practice and methods.
insulted. yet again. as if i were selling "snake oil". i don't sell anything. others people sell their sloppy work. i never bragged of having built thousands of wheels.
there is not much strength in such numbers except for people who are not able to study structural engineering but rely solely on anecdotal evidence and established dogma.
i don't build wheels in order to take people's money. others do and some of them will attack me to present themselves as victorious over the other person.
bogus arguments thrown in the attack.
ask any engineer friend you might have to study the data using numbers, flexural stress of the arch etc. and you might have these truths certified.
i might have patented a software to assist the wheel builder in gathering data and getting computations done for the amount of spoke key turn for each nipple etc.
how about that? would you rather have secret or patented science or aren't you glad that i instead have given for free very useful information to back up my claims for the way i built my wheels? and i build disregarding the "warranty" aspect of it because i have no use for it. i have not worked with new rims, my work was much harder in fixing bent out of shape rims. low budget.
but hey, some people who aren't struggling to make ends meet attack me and present their reputation as an argument. i presented better arguments but got obscured by the avalanche of pointed bogus arguments against the scientific arguments about grain size structure that gets finer by cold working so that you would benefit from a higher yield strength of the rim IF you need not a downhill work but more like what touring people seek which is durability and not too much rim deflection that makes a small contribution to radial give but also makes the wheel more vulnerable to accidents. the safety margin thing.
any wheel builder can know that you may exceed the maximum tension given by the manufacturer to the general public... if spoke tension is kept at a much lower variance than usually tolerance which is +/-20% (park tool literature).
i have also given the strain hardening details regarding the 6061-T6 on a respectable independent source to establish the 2% strain cold work (here, again) which corresponds to about 200MPa (strain stress curve link provided right next to the other link about the cold working aspect - later edit: take this link) if you take the time to read my post which i wrote yesterday.
if you can't figure out the tensional stress for the rim around the spoke hole for a certain tension of the spokes and the equilibrium points thing... spare me the direct personal attacks or i might bite back somehow.
i have not exceeded the 96.5MPa fatigue recommendation (for tension stress) for the 6061-T6 in static load of the rim due to flexural stress.
the wheel experiences less variance in dynamic strain the more the spokes compress the rim.
the general recommendation also does not mention stress corrosion cracking due to the chemical factor which can be prevented. but who am i do disagree with general practice?...
and here's one more thing... you might search to find fatigue cycles until break for salty conditions vs normal air, you might have a surprise.
here's an example.
these are verifiable scientific arguments, i'm not relying on anecdotal evidence or general practice and methods.

Some very interesting points you've made. English is not my native so please take all I say, and my understanding of your claims with a grain of salt and ask for clarifications.
Based on my experience, I can share this - any return info is more than welcome:
1. Strong double walled rims help make a wheel more durable, spokes less likely to break. I suspect this is partly due to them allowing for higher spoke tensions, so no NDS spokes coming completely slack under loads.
2. For rear wheels, I find the minimal acceptable NDS tension to be the problematic part. With some, extremely dished wheels (narrow OLD and wide multi-speed cassette), this calls for very high DS spoke tension, if the rim is to be properly dished. Like 140 Kgf DS tension in order to keep the NDS tension over 80 Kgf (without the tyre mounted and inflated).
3. I also like to start with the rim dished further to the right, since it's a lot easier to bring the DS spokes to the needed tensions for proper dish, only then "pull it" to the left by adjusting NDS spoke tension, until it is brought to the desired minimum and the desired dish is achieved.
4. Like you pointed, having the rim run up to 0.5 mm to the left is good for the reasons you noted:
- when the tyre is inflated, it can go a bit back towards the middle, won't run further to the left definitely
- it allows more NDS tension, which is the weak point
- likewise, there's less difference in tension between the DS and the NDS spokes.
5. There is a point in spoke tightening process where same side spokes going back and spokes going forward have altering different tensions. Past a certain point, as they are tensioned by an equal amount of nipple turns, they become more and more uniform in tension (about 60-80 Kgf usually).
6. Wheels with higher spoke tension, as long as it doesn't exceed 70 - 80% of total amount of tension a rim can take, are stronger, all else being equal. Spokes can take a lot more tension than the rim (more on that later), while they suffer when coming slack (that's when fatigue cracks at the elbow happen). Also, a spoke coming completely slack usually ends up with the wheel collapsing, so that's another reason for having the spokes more highly tensioned.
7. In addition to rim's max tension, there is another limit in max tension of either spoke: nipple to rim interface. Even when lubricated. Rims with double eyelets are a lot better at this, allowing for more tension - all else being equal. Of course, nipple threads are another weak point: 1.8 mm wide spokes have the same thread pitch as 2 mm wide ones. So, they have less material at the end, being more prone to breaking at the nipple end. This is why I consider 2 mm wide (swaged) spokes to be more durable.
8. Swaged spokes twist more at very high tensions, but also elongate more, so don't become untensioned that easily. They are a bit easier to break with a strong outside force (hitting a rock/branch), but the force that breaks those is also very likely to damage a non-swaged spoke so it breaks down the road (a cut/dent that induces fatigue cracking). So I consider swaged spokes as more expensive, but more durable, with all the pros and cons calculated.
9. Standing on the rim should not be done with cartridge bearings, unless the axle is put in a hole, so the weight is not supported by the axle, but the hub shell itself - otherwise bearings could get damaged. With cup and cone bearings it's not that risky. Still, I consider it to be a risk move, rather do the stress relieving by pulling spokes in pairs (with leather gloves to not hurt my hands, you need a very strong squeeze).
10. I use a spoke tension meter, since plucking spokes is useless due to my zero talent for music/sounds. Though, for most normal people, it should be a faster method. Good quality hubs, spokes and rims allow one to easily reach +-10% equal tension of spokes on the same side. Poorly machined rims, spokes and nipples make that a bit harder (tightening all the spokes with an equal amount of nipple turns, gradually, ends up with tension variations and out of trueness, with the out of trueness not always "aligned" with the tension variations - almost like with bent rims).
EDIT:
11. Tensions above 150 Kgf exponentially increase the risk of a spoke breaking at the threads, in my opinion and experience. In addition to putting a lot of stress on the nipple to rim interface (contact area), requiring strong, double walled rims with double eyelets (or at least I'd say such rims are preferred). Likewise, as long as the NDS spoke tension gets to around 100 Kgf, there's little use in increasing spoke tension - it can only make the wheel less durable (for the afore mentioned reasons). If using swaged spokes, even for really heavy riders, I'd say that the minimum safe tension is even lower, around 80 Kgf.
Sorry for the long post.
Also, due to the length of your post, as well as the structure and the directions of the discussion, I'm not 100% sure I understand all you pointed out. But some good for thought from what I could gather - could be a good discussion, allowing all of us to learn something new.
As for my post, like I said: any questions, additions and, especially, corrections are more than welcome.
Last edited by Bike Gremlin; 09-06-19 at 12:38 AM.
#75
Senior Member
0. some hubs don't allow more than a certain amount of average tension. there are some anecdotal evidence for Chris King hubs that have their bearings becoming loose. other hubs could break if you go crazy with spoke tension. that's why i always say: YMMV. not every component is the same. there are reasons to not follow the Brandt (even if it's not accurate to have it named "his" method, just that he described it without too much stress on the radial tuning and/or how it is to be done in agreement/balance to tension variance) to the letter with hubs that may not work that well on extreme average tensions (from which you back off whatever amount you choose to do so).
1. i won't bother discussing single wall rims as they're quite history now. i could but it would be of too little use... and they allow for high tension, only they are less stable if you don't balance radial runout with tension variance as precisely as needed. i can't stress this enough. i already explained how to do it for those who will care to read other posts of mine.
2. i am quite dissapointed by the fact that they don't build hubs spaced for 5-6 speed like for example Hope Pro SS so that the spoke tension would be equal. of course this is the reason for most people's troubles with their wheels, e-bikes, loaded touring, clydes/athenas. my e-bike is now transformed into a singlespeed bike, the 9/10 speed spaced freehub is no use to me except to ensure an exact chainline with the cranks (not so easily repaceable bottom bracket). so, again, i don't like going into this discussion as most people are obsessed with having many cogs on the rear but few will consider having clipless pedals which can make singlespeed a breeze for any bike.
3. any wheel builder knows that for a wheel that will have dish (front disc and rear wheels) it's the best practice to radial true and then lateral true if needed by having a the least bit of tension NDS as needed and finally have a balanced radial runout to spoke tension variance. but few bother to do exact measurements for tension and radial runout (for each spoke) as to have computed values to be followed regarding each nipple angle to be turned +/- as to achieve that balance. after that is done NDS are to be raised in stages with stress relieving done in stages. that DS tension at which this tune is to be made is a rather "average" one. somewhere at most 70kgf should be enough so that if needed the final dish operation will sometimes needed to be done in just one or just a few 90 degrees turn of the nipples for the DS or none at all, depending on several factors. not much details are needed to be talked about here regarding the optimum medium tension for DS tension at which radial and tension variance should be tuned so that from that stage on the DS nipples are not to be touched except to do the final dish IF NEEDED.
4. the wheel builder's dilemma can be therefore also reformulated for those reasons like this: "should i bother for a less than 0.25mm difference from perfect dish? why bother doing so if it matters so little and there are reasons to prefer this" (see point 2. discussed) even myself being a perfectionist regarding the way my bike rides don't care for such accuracy which matters so little. therefore you can adjust dish by having just n*90 degrees of nipples turn if needed. putting oriented labels on the spokes is of much use as to ensure there is no elastic twist for the spokes. an unexperienced builder could put labels with marked lines (nipple positions or spoke key position for that matter) on the rim so that error does not add up when turning those n*90 degrees.
5. as the NDS get more and more tension the variance will also increase in absolute figures but the relative tension variance will not diminish in percent values too much except the rim is getting straightened in the process of raising tension in stages by stress relieving and by getting very high tension in order to back off after straightening the rim and strain hardening it and bedding in everything that has to be bedded in. achieving +/-5% tension variance and +/-0.05mm RADIAL (which i care for more than for the latter) and lateral true is not something that is really hard to do. it only takes time doing so but that balance for radial runout and tension variance has to be taken care of from the beginning. you might check again later if somehow for some reasons (usually with not so new rims and hubs) the bedding is not uniform and therefore messes with the initial balance so that before reaching the extreme tensions (whatever you take to mean that you won't go further from that point) you should check for that balance by doing another set of measurements if you are able to do that.
later edit: the strain-stres curve for the rim's material is in such way that it gets more and more stubborn right up to a bit over 200MPa after which the elastic modulus goes at much lower level than that where it begun with (at zero stress). the stress-strain graph has an inflection point. that's why i wrote that the variance in percent values does not change too much unless you do the plastic deformations of the rim either by stress relief (useful also in order to test the ground, to check before going further) or just raise NDS to extreme levels which is too difficult to do with spokes that are not thick enough for the job. take note that a narrow pressurized tire can be of much help. that and the mounting of it on a such thick tape as you care to have mounted on the rim. the tire will press harder on the rim with its bead on top of the pressure of the air pressing on the rim seat (that is after extracting the thickness of the tire and tube).
6. the rim can take more tension than people would imagine but it would be too vulnerable in riding if left that way. there's also what is called creep deformation to kick in if the wheel is left at tensions like 200+ (supposing you were able to very precisely tune radial runout and tension variance) and just sits in that state.
the right amount of average tension for a durable wheel depends on several factors:
a.) spoke thickness. straight gauge both sides dictates higher tension for two reasons, namely 1. preventing the NDS going slack such as to optimize durability and 2. the DS at 4:30 and 7:30 will be under less tension to be added to those spokes if straight gauge are on the NDS. DS spokes will be under more added tension if the NDS has butted spokes. of course the DS will under less static tension when butted spokes are on the NDS but i just thought to point out that higher static DS tension is alright with same straight gauge spokes on both DS and NDS, especially when using 36h (more spokes keeping the rim together at 4:30 and 7:30 positions etc.).
observe the 7:30 and 4:30 spoke tension going higher at the wheel's maximum load for the ~1100 average spoke tension of that wheel in the video - about 30% more.
if anyone cares to observe for a certain rim the wall into which the nipple sits and therefore figure out the shear stress...
https://www.kstoerz.com/freespoke/img/spoke_1.jpg
b.) spoke length - spokes would go easier slack if shorter to begin with at the same certain tension for the comparison sake.
c.) lower rim height makes the rim able to have larger radial deflection at loads and also less susceptible to flat spots - therefore you either pick thinner spokes (makes more sense) or work with higher tensions (there are few reasons to keep thick spokes). if height is on the upside like the rim is 20+mm then the spokes need not be at the same high tension that low profile rims dictate. and usually you have low spoke count with rims having more height as those rims tolerate more gap between the spokes and less compression of the rim as a result. such rims are used for being more aero.
7. i was able to go to 180kgf DS tension and 170kgf NDS tension with a single eyeleted rim (about 500g, 27mm external width, 18mm height and therefore not very thick wall in which the eyelets sit) i appreciate now even more after taking the pain to straighten it after it has been abused and somehow neglected by previous owners. in general when repairing such things quality work is hard to find and that is why i take the pain to work with zip ties, acoustics and some laser tool (less than 10 bucks was what i paid for it) as a quite recent addition to the minimum tools i work with. i had no hope to have a good job done by others so i started doing stuff myself. i can't afford better tools and i don't have much hope in taking money around where i live because in general people don't know better as to appreciate these things and i am very easily pissed when crap is thrown at me (sabotage etc.) and therefore i tend to have a loud mouth when accused of selling "snake oil" etc. i am not good at selling crap with a smiling face but tend to go crazy when what i give for free is criticized with bogus arguments and bad science when i know it to be tried and true, scientifically proven.
as a side note: i suspect (and i don't care to find out) there's a different thread pitch on some spokes (on some wheels i had in use several years ago) that were 1.8mm continuous section and therefore only butted at the flanges. so people better take care to ensure that the classic 0.45 thread pitch for 2mm section near the thread is what is used before doing the angle computing stuff i mentioned earlier. such spokes do not necessarily break easier at the nipple unless proper stress relieving is done. if the spokes are always in elastic bend near the yield limit then creep and fatigue will work them for those portions until they break.
8. if i were to have a bike that i need not worry for the spokes when securing the wheel with the bike lock or other ways in which they are vulnerable i would build with about 1.8mm DS and 1.5mm NDS but that also is for rims that are not to be straightened out. rims that are bent out of shape can be a nightmare to be fixed when using thin spokes. and... i would gladly use 36h both front and rear if the rim model is available in 36h. and i'd go 135kgf DS - which would mean about 88kgf NDS - so that when the tire is fitted (which should lower the tension even with 0 psi) and inflated the max DS tension is just a bit higher than 120kgf so that those wheels don't need to be touched again with the spoke key.
9. i guess this aspect is something anyone can figure out. i wrote in my recent posts that the wheel could be pressed not on the axle per se but on the flange that sits on some support. to use less words i would just say "pressing on the axle" and also the classic YMMV in regards to whatever the cartridge bearings you have or the weight you use (some are clydes, some are not) etc. for example i had 64kg at the time i worked with a DT Swiss TK540 and Rev (1.5mm spokes) when i stood on that wheel at just a tad under 120kgf average spoke tension. the hub was a cup and cone. the latter work i performed on a motor hub i trusted to have strong bearings. grabbing spokes in parallel sets is safer and quite alright when working on new rims but sometimes you need to fix light tacoed rims.
10. not many people are so unsensitive to the difference between 600 and 604 Hz. that's 11 cents in musical language. usually everyone can be precise to 4 cents which means about 0.5% error. using a precise spoke tension meter is better when you have one. if you don't have one and you have my stubbornness you use zip ties and acoustics AND a tone generator AND a computer to gather all data and figure out the angle for each nipple to turn.
11.a.) the spokes should be able to remain at 150 static tension after you cold worked them to more than 200kgf. i would not advise achieving 150kgf and leaving the spokes at that tension without going to at least more than 30% more tension. the means to do so is another matter. see the youtube video above to get a picture regarding delta tension at the point of 6:00 spoke(s) getting slack. the bend near the nipple will be made in a quite precise way.
11.b.) using almost 150 DS tension with the tire inflated is something i would advise only for final spoke tension variance of +/-5% and i would say it's quite appropriate to do so when using straight gauge spokes and/or high diameter flanges that have shorter spokes to the rim by imposing 2x patterns. that and the rim height being under 20mm as i wrote above (mine is 18mm). if i were to take the tire off the rim i wouldn't be surprised to measure more than 160kgf maximum spoke tension. i dunno exactly at which level they would be now with the tire taken off, i never bothered to measure. the maximum spoke tension now with the inflated tire is about 144kgf and that is with a radial/lateral runout at +/-0.05mm and tension variance surely less than +/-6%. but i'll say it again: 250mm spoke length (2x) on a 18mm height rim, 36 DT Alpine spokes. this affords me peace of mind for dynamic loads even higher than 400kgf as the tension drop was about 18% with respect to the load measured on the scales (rear wheel contact when weighing). the least tensioned NDS is about 85kgf.
11.c.) spoke tension is excessive at any level if the person who uses the wheels pressure washes them without adding something to prevent corrosion after the pressure wash. this is just one example of bad practice. stress corrosion cracking is not preventable just by using "normal" tension. it's just that the process starts depending on tension variance but there's the stuff that could get to the rim's surface wherever the anodized surface is scratched and bad stuff gets to it.
99. lubricate the threads with wax based lubes. the best mix should have lithium stearate as an additive. avoind graphite and moly as they are not corrosion free. the lower friction coefficient the less you need to apply techniques as to momentarily lower spoke tension when turning the nipples in order to raise spoke tension. microcrystalline wax is of much use and these substances are also generically called isoparaffins. add a bit of linseed (flaxseed) oil to the mix in order to seal the stuff against bacteria that degrade waxes (one of the causes of tire rot). as far as i know they say that microcrystalline is not so easily biodegradeable. you could check this stuff out for your own.
1. i won't bother discussing single wall rims as they're quite history now. i could but it would be of too little use... and they allow for high tension, only they are less stable if you don't balance radial runout with tension variance as precisely as needed. i can't stress this enough. i already explained how to do it for those who will care to read other posts of mine.
2. i am quite dissapointed by the fact that they don't build hubs spaced for 5-6 speed like for example Hope Pro SS so that the spoke tension would be equal. of course this is the reason for most people's troubles with their wheels, e-bikes, loaded touring, clydes/athenas. my e-bike is now transformed into a singlespeed bike, the 9/10 speed spaced freehub is no use to me except to ensure an exact chainline with the cranks (not so easily repaceable bottom bracket). so, again, i don't like going into this discussion as most people are obsessed with having many cogs on the rear but few will consider having clipless pedals which can make singlespeed a breeze for any bike.
3. any wheel builder knows that for a wheel that will have dish (front disc and rear wheels) it's the best practice to radial true and then lateral true if needed by having a the least bit of tension NDS as needed and finally have a balanced radial runout to spoke tension variance. but few bother to do exact measurements for tension and radial runout (for each spoke) as to have computed values to be followed regarding each nipple angle to be turned +/- as to achieve that balance. after that is done NDS are to be raised in stages with stress relieving done in stages. that DS tension at which this tune is to be made is a rather "average" one. somewhere at most 70kgf should be enough so that if needed the final dish operation will sometimes needed to be done in just one or just a few 90 degrees turn of the nipples for the DS or none at all, depending on several factors. not much details are needed to be talked about here regarding the optimum medium tension for DS tension at which radial and tension variance should be tuned so that from that stage on the DS nipples are not to be touched except to do the final dish IF NEEDED.
4. the wheel builder's dilemma can be therefore also reformulated for those reasons like this: "should i bother for a less than 0.25mm difference from perfect dish? why bother doing so if it matters so little and there are reasons to prefer this" (see point 2. discussed) even myself being a perfectionist regarding the way my bike rides don't care for such accuracy which matters so little. therefore you can adjust dish by having just n*90 degrees of nipples turn if needed. putting oriented labels on the spokes is of much use as to ensure there is no elastic twist for the spokes. an unexperienced builder could put labels with marked lines (nipple positions or spoke key position for that matter) on the rim so that error does not add up when turning those n*90 degrees.
5. as the NDS get more and more tension the variance will also increase in absolute figures but the relative tension variance will not diminish in percent values too much except the rim is getting straightened in the process of raising tension in stages by stress relieving and by getting very high tension in order to back off after straightening the rim and strain hardening it and bedding in everything that has to be bedded in. achieving +/-5% tension variance and +/-0.05mm RADIAL (which i care for more than for the latter) and lateral true is not something that is really hard to do. it only takes time doing so but that balance for radial runout and tension variance has to be taken care of from the beginning. you might check again later if somehow for some reasons (usually with not so new rims and hubs) the bedding is not uniform and therefore messes with the initial balance so that before reaching the extreme tensions (whatever you take to mean that you won't go further from that point) you should check for that balance by doing another set of measurements if you are able to do that.
later edit: the strain-stres curve for the rim's material is in such way that it gets more and more stubborn right up to a bit over 200MPa after which the elastic modulus goes at much lower level than that where it begun with (at zero stress). the stress-strain graph has an inflection point. that's why i wrote that the variance in percent values does not change too much unless you do the plastic deformations of the rim either by stress relief (useful also in order to test the ground, to check before going further) or just raise NDS to extreme levels which is too difficult to do with spokes that are not thick enough for the job. take note that a narrow pressurized tire can be of much help. that and the mounting of it on a such thick tape as you care to have mounted on the rim. the tire will press harder on the rim with its bead on top of the pressure of the air pressing on the rim seat (that is after extracting the thickness of the tire and tube).
6. the rim can take more tension than people would imagine but it would be too vulnerable in riding if left that way. there's also what is called creep deformation to kick in if the wheel is left at tensions like 200+ (supposing you were able to very precisely tune radial runout and tension variance) and just sits in that state.
the right amount of average tension for a durable wheel depends on several factors:
a.) spoke thickness. straight gauge both sides dictates higher tension for two reasons, namely 1. preventing the NDS going slack such as to optimize durability and 2. the DS at 4:30 and 7:30 will be under less tension to be added to those spokes if straight gauge are on the NDS. DS spokes will be under more added tension if the NDS has butted spokes. of course the DS will under less static tension when butted spokes are on the NDS but i just thought to point out that higher static DS tension is alright with same straight gauge spokes on both DS and NDS, especially when using 36h (more spokes keeping the rim together at 4:30 and 7:30 positions etc.).
if anyone cares to observe for a certain rim the wall into which the nipple sits and therefore figure out the shear stress...
https://www.kstoerz.com/freespoke/img/spoke_1.jpg
b.) spoke length - spokes would go easier slack if shorter to begin with at the same certain tension for the comparison sake.
c.) lower rim height makes the rim able to have larger radial deflection at loads and also less susceptible to flat spots - therefore you either pick thinner spokes (makes more sense) or work with higher tensions (there are few reasons to keep thick spokes). if height is on the upside like the rim is 20+mm then the spokes need not be at the same high tension that low profile rims dictate. and usually you have low spoke count with rims having more height as those rims tolerate more gap between the spokes and less compression of the rim as a result. such rims are used for being more aero.
7. i was able to go to 180kgf DS tension and 170kgf NDS tension with a single eyeleted rim (about 500g, 27mm external width, 18mm height and therefore not very thick wall in which the eyelets sit) i appreciate now even more after taking the pain to straighten it after it has been abused and somehow neglected by previous owners. in general when repairing such things quality work is hard to find and that is why i take the pain to work with zip ties, acoustics and some laser tool (less than 10 bucks was what i paid for it) as a quite recent addition to the minimum tools i work with. i had no hope to have a good job done by others so i started doing stuff myself. i can't afford better tools and i don't have much hope in taking money around where i live because in general people don't know better as to appreciate these things and i am very easily pissed when crap is thrown at me (sabotage etc.) and therefore i tend to have a loud mouth when accused of selling "snake oil" etc. i am not good at selling crap with a smiling face but tend to go crazy when what i give for free is criticized with bogus arguments and bad science when i know it to be tried and true, scientifically proven.
as a side note: i suspect (and i don't care to find out) there's a different thread pitch on some spokes (on some wheels i had in use several years ago) that were 1.8mm continuous section and therefore only butted at the flanges. so people better take care to ensure that the classic 0.45 thread pitch for 2mm section near the thread is what is used before doing the angle computing stuff i mentioned earlier. such spokes do not necessarily break easier at the nipple unless proper stress relieving is done. if the spokes are always in elastic bend near the yield limit then creep and fatigue will work them for those portions until they break.
8. if i were to have a bike that i need not worry for the spokes when securing the wheel with the bike lock or other ways in which they are vulnerable i would build with about 1.8mm DS and 1.5mm NDS but that also is for rims that are not to be straightened out. rims that are bent out of shape can be a nightmare to be fixed when using thin spokes. and... i would gladly use 36h both front and rear if the rim model is available in 36h. and i'd go 135kgf DS - which would mean about 88kgf NDS - so that when the tire is fitted (which should lower the tension even with 0 psi) and inflated the max DS tension is just a bit higher than 120kgf so that those wheels don't need to be touched again with the spoke key.
9. i guess this aspect is something anyone can figure out. i wrote in my recent posts that the wheel could be pressed not on the axle per se but on the flange that sits on some support. to use less words i would just say "pressing on the axle" and also the classic YMMV in regards to whatever the cartridge bearings you have or the weight you use (some are clydes, some are not) etc. for example i had 64kg at the time i worked with a DT Swiss TK540 and Rev (1.5mm spokes) when i stood on that wheel at just a tad under 120kgf average spoke tension. the hub was a cup and cone. the latter work i performed on a motor hub i trusted to have strong bearings. grabbing spokes in parallel sets is safer and quite alright when working on new rims but sometimes you need to fix light tacoed rims.
10. not many people are so unsensitive to the difference between 600 and 604 Hz. that's 11 cents in musical language. usually everyone can be precise to 4 cents which means about 0.5% error. using a precise spoke tension meter is better when you have one. if you don't have one and you have my stubbornness you use zip ties and acoustics AND a tone generator AND a computer to gather all data and figure out the angle for each nipple to turn.
11.a.) the spokes should be able to remain at 150 static tension after you cold worked them to more than 200kgf. i would not advise achieving 150kgf and leaving the spokes at that tension without going to at least more than 30% more tension. the means to do so is another matter. see the youtube video above to get a picture regarding delta tension at the point of 6:00 spoke(s) getting slack. the bend near the nipple will be made in a quite precise way.
11.b.) using almost 150 DS tension with the tire inflated is something i would advise only for final spoke tension variance of +/-5% and i would say it's quite appropriate to do so when using straight gauge spokes and/or high diameter flanges that have shorter spokes to the rim by imposing 2x patterns. that and the rim height being under 20mm as i wrote above (mine is 18mm). if i were to take the tire off the rim i wouldn't be surprised to measure more than 160kgf maximum spoke tension. i dunno exactly at which level they would be now with the tire taken off, i never bothered to measure. the maximum spoke tension now with the inflated tire is about 144kgf and that is with a radial/lateral runout at +/-0.05mm and tension variance surely less than +/-6%. but i'll say it again: 250mm spoke length (2x) on a 18mm height rim, 36 DT Alpine spokes. this affords me peace of mind for dynamic loads even higher than 400kgf as the tension drop was about 18% with respect to the load measured on the scales (rear wheel contact when weighing). the least tensioned NDS is about 85kgf.
11.c.) spoke tension is excessive at any level if the person who uses the wheels pressure washes them without adding something to prevent corrosion after the pressure wash. this is just one example of bad practice. stress corrosion cracking is not preventable just by using "normal" tension. it's just that the process starts depending on tension variance but there's the stuff that could get to the rim's surface wherever the anodized surface is scratched and bad stuff gets to it.
99. lubricate the threads with wax based lubes. the best mix should have lithium stearate as an additive. avoind graphite and moly as they are not corrosion free. the lower friction coefficient the less you need to apply techniques as to momentarily lower spoke tension when turning the nipples in order to raise spoke tension. microcrystalline wax is of much use and these substances are also generically called isoparaffins. add a bit of linseed (flaxseed) oil to the mix in order to seal the stuff against bacteria that degrade waxes (one of the causes of tire rot). as far as i know they say that microcrystalline is not so easily biodegradeable. you could check this stuff out for your own.
Last edited by adipe; 09-06-19 at 02:35 PM.