Good tubing for DIY rack
#1
Senior Member
Thread Starter
Join Date: Oct 2015
Location: San Diego, California
Posts: 4,077
Bikes: Velo Orange Piolet
Mentioned: 28 Post(s)
Tagged: 0 Thread(s)
Quoted: 2228 Post(s)
Liked 2,011 Times
in
972 Posts
Good tubing for DIY rack
[rack that attaches to bike to support Carradice bag]
I want to make a simple rack - simple bends (fill tube with sand method), then smash the ends and drill them for attachment points.
No welding.
What'a a good tubing for this?
I want to make something like this:
I want to make a simple rack - simple bends (fill tube with sand method), then smash the ends and drill them for attachment points.
No welding.
What'a a good tubing for this?
I want to make something like this:
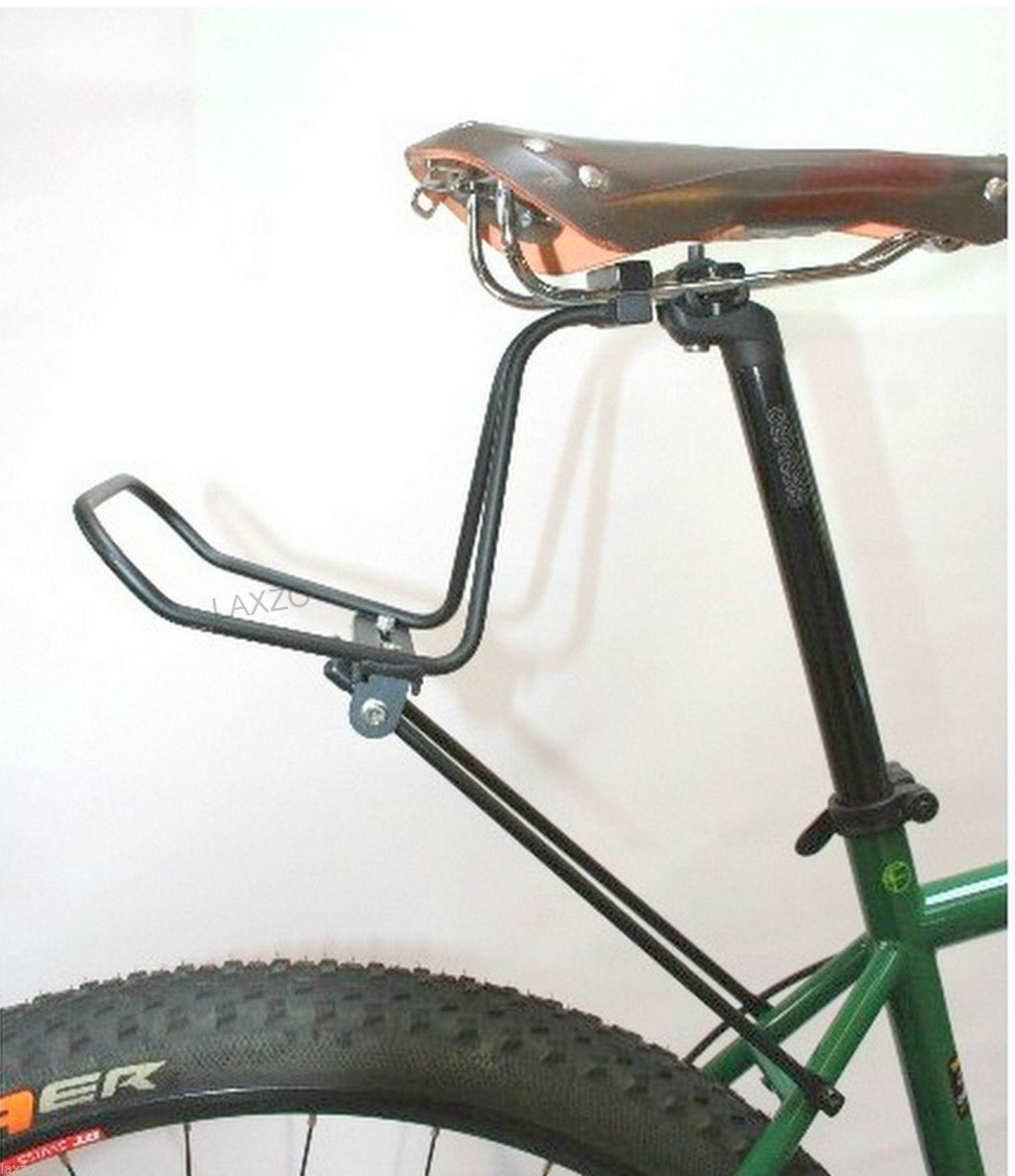
#2
Senior Member
Join Date: Sep 2010
Location: Roswell, GA
Posts: 8,319
Bikes: '93 Trek 750, '92 Schwinn Crisscross, '93 Mongoose Alta
Mentioned: 30 Post(s)
Tagged: 0 Thread(s)
Quoted: 1438 Post(s)
Liked 1,092 Times
in
723 Posts
I think steel tube will be too hard to bend by hand, and copper tubing is too soft to hold its shape well. Perhaps 1/8" copper pipe and fittings could be cobbled together (and look kind of pretty polished up) or aluminum bar and angle drilled and bolted would work. No experience bending aluminum tube so cannot comment.
#3
Engineer
Join Date: May 2010
Location: Bucharest, Romania, Europe
Posts: 591
Bikes: 1989 Krapf (with Dura-ace) road bike, 1973 Sputnik (made by XB3) road bike , 1961 Peugeot fixed gear, 2010 Trek 4400
Mentioned: 1 Post(s)
Tagged: 0 Thread(s)
Quoted: 38 Post(s)
Likes: 0
Liked 0 Times
in
0 Posts
I'd go with no tubing but solid smooth steel rebar (6mm should be enough.. even 4mm for light duty). Pretty cheap and if you got a vice and some vicegrips or even better an iron bending wrench (like this DESE MACHINE Pipe, Profile, Rebar Bending Machine -pretty cheap in most hardware stores) it will be easy enough to work with.
For fixing, cold hammering the end of a rebar works decent, but a heat to red hot on a stove then smashing with a hammer against an anvil will work best.
But steel is heavy, so most of this stuff is made out of solid aluminium bars welded/brazed together in different shapes to reinforce each other (like in a truss bridge). Bending aluminium is risky as it work hardens very quickly and will break.. so will need some heat treatment to normalize the structure before bending and after bending. Also most aluminium rods are cold drawn to reinforce the rod as it's already work hardened by the drawing process. So bending it again is not safe at all, it must be normalized before bending. - in other words aluminium bending is another level that is not for the home gamer.
Steel is heavy but at 6mm diameter will not add that much to a bike. even if you use 2m length of that rebar to make that rack will only be about half a kilo for that.
Another level for a nice sturdy rack is using steel electrical conduit. the 16mm type is about 400grams per meter.. but at that diameter you don't need much. Adding bends to electrical conduit is a bit harder. Sand fill may work (poorley) but definitely a job for a pipe bending tool with rollers and guides.
For fixing, cold hammering the end of a rebar works decent, but a heat to red hot on a stove then smashing with a hammer against an anvil will work best.
But steel is heavy, so most of this stuff is made out of solid aluminium bars welded/brazed together in different shapes to reinforce each other (like in a truss bridge). Bending aluminium is risky as it work hardens very quickly and will break.. so will need some heat treatment to normalize the structure before bending and after bending. Also most aluminium rods are cold drawn to reinforce the rod as it's already work hardened by the drawing process. So bending it again is not safe at all, it must be normalized before bending. - in other words aluminium bending is another level that is not for the home gamer.
Steel is heavy but at 6mm diameter will not add that much to a bike. even if you use 2m length of that rebar to make that rack will only be about half a kilo for that.
Another level for a nice sturdy rack is using steel electrical conduit. the 16mm type is about 400grams per meter.. but at that diameter you don't need much. Adding bends to electrical conduit is a bit harder. Sand fill may work (poorley) but definitely a job for a pipe bending tool with rollers and guides.
#5
Senior Member
Join Date: Sep 2010
Location: Roswell, GA
Posts: 8,319
Bikes: '93 Trek 750, '92 Schwinn Crisscross, '93 Mongoose Alta
Mentioned: 30 Post(s)
Tagged: 0 Thread(s)
Quoted: 1438 Post(s)
Liked 1,092 Times
in
723 Posts
Maybe cutting down a cheap/castoff rear rack for pre-bent materials, clamps, etc. would be a useful approach.
#6
I'm good to go!
Join Date: Jul 2017
Location: Mississippi
Posts: 14,992
Bikes: Tarmac Disc Comp Di2 - 2020
Mentioned: 51 Post(s)
Tagged: 0 Thread(s)
Quoted: 6196 Post(s)
Liked 4,810 Times
in
3,318 Posts
I wouldn't use tube, I'd get some 1/4 to maybe 5/16 inch stainless steel rod, or perhaps a larger diameter plain steel rod. It'll bend nicely with some force and while being properly held with a bender or homemade fixture/jig.
I'd think copper or much or the soft steel and aluminum tube you can bend yourself will be too easy to deform under the loads you'll put on it while riding the average bumpy road. The thin tube that has the strength to resist the expected forces during rides that they use for some of these things is more difficult to bend and deal with without specific tools and skills.
You can sometimes get steel and aluminum of any shape at the same places your local machine shops get it. I've used Oneal Steel here locally. They sometimes have leftover odd lengths from large orders that were custom cut to length. They call them "drops" and many times sell them very cheap as they are less than the standard 16 to 20 foot lengths that most fabricating machine shops like to buy.
If you cannot buy from one of the local suppliers directly, then maybe you know some one with a business that can get it for you or use their name (with permission of course). What I've gotten is much less expensive than Home Depot or the other big box stores will sell the same stuff for.
I'd think copper or much or the soft steel and aluminum tube you can bend yourself will be too easy to deform under the loads you'll put on it while riding the average bumpy road. The thin tube that has the strength to resist the expected forces during rides that they use for some of these things is more difficult to bend and deal with without specific tools and skills.
You can sometimes get steel and aluminum of any shape at the same places your local machine shops get it. I've used Oneal Steel here locally. They sometimes have leftover odd lengths from large orders that were custom cut to length. They call them "drops" and many times sell them very cheap as they are less than the standard 16 to 20 foot lengths that most fabricating machine shops like to buy.
If you cannot buy from one of the local suppliers directly, then maybe you know some one with a business that can get it for you or use their name (with permission of course). What I've gotten is much less expensive than Home Depot or the other big box stores will sell the same stuff for.
#7
Nigel
Join Date: Mar 2011
Location: San Jose, CA
Posts: 2,991
Bikes: 1980s and 1990s steel: CyclePro, Nishiki, Schwinn, SR, Trek........
Mentioned: 12 Post(s)
Tagged: 0 Thread(s)
Quoted: 384 Post(s)
Likes: 0
Liked 6 Times
in
6 Posts
So many choices.....
Aluminum: pick an alloy that is easy to bend: a 5000 series like 5052. Do NOT pick a 6000 series like 6061; they will crack.
5052 drawn tubing, used for aircraft hydraulics, is the tubing that I would choose for your project.
Instead of sand, you might want to consider a low melting temp bismuth alloy for the filler, then melt it out. Like this: https://www.amazon.com/Low-Melting-P.../dp/B001QUVQE2
Aluminum: pick an alloy that is easy to bend: a 5000 series like 5052. Do NOT pick a 6000 series like 6061; they will crack.
5052 drawn tubing, used for aircraft hydraulics, is the tubing that I would choose for your project.
Instead of sand, you might want to consider a low melting temp bismuth alloy for the filler, then melt it out. Like this: https://www.amazon.com/Low-Melting-P.../dp/B001QUVQE2
#8
Senior Member
Join Date: Apr 2011
Posts: 7,067
Mentioned: 41 Post(s)
Tagged: 0 Thread(s)
Quoted: 4409 Post(s)
Liked 1,565 Times
in
1,027 Posts
So many choices.....
Aluminum: pick an alloy that is easy to bend: a 5000 series like 5052. Do NOT pick a 6000 series like 6061; they will crack.
5052 drawn tubing, used for aircraft hydraulics, is the tubing that I would choose for your project.
Instead of sand, you might want to consider a low melting temp bismuth alloy for the filler, then melt it out. Like this: https://www.amazon.com/Low-Melting-P.../dp/B001QUVQE2
Aluminum: pick an alloy that is easy to bend: a 5000 series like 5052. Do NOT pick a 6000 series like 6061; they will crack.
5052 drawn tubing, used for aircraft hydraulics, is the tubing that I would choose for your project.
Instead of sand, you might want to consider a low melting temp bismuth alloy for the filler, then melt it out. Like this: https://www.amazon.com/Low-Melting-P.../dp/B001QUVQE2
I do agree that aluminum tubing makes the most sense - much stiffer than copper and lighter and easier to bend than steel. Hardware stores may have tube stock.
#9
Nigel
Join Date: Mar 2011
Location: San Jose, CA
Posts: 2,991
Bikes: 1980s and 1990s steel: CyclePro, Nishiki, Schwinn, SR, Trek........
Mentioned: 12 Post(s)
Tagged: 0 Thread(s)
Quoted: 384 Post(s)
Likes: 0
Liked 6 Times
in
6 Posts
Sand is sharp, and is composed of a large percentage of air even when packed down. The sharp corners result in stress risers in the bent aluminum, which may lead to cracking. The large amount of air means the sand can shift around - like foam peanuts in shipping boxes - thus not controlling the tube profile well.
Neither of these may be of a concern in this case.
Neither of these may be of a concern in this case.
#10
Senior Member
Join Date: Apr 2011
Posts: 7,067
Mentioned: 41 Post(s)
Tagged: 0 Thread(s)
Quoted: 4409 Post(s)
Liked 1,565 Times
in
1,027 Posts
Sand is sharp, and is composed of a large percentage of air even when packed down. The sharp corners result in stress risers in the bent aluminum, which may lead to cracking. The large amount of air means the sand can shift around - like foam peanuts in shipping boxes - thus not controlling the tube profile well.
Neither of these may be of a concern in this case.
Neither of these may be of a concern in this case.
Sand is a common tube bending material because it doesn't compact while being flexible enough to bend, is heat resistant and pours right out. I hadn't heard of filling the tube with solder in preference to it.
#11
Senior Member
Join Date: Jan 2013
Location: South Jersey
Posts: 2,266
Mentioned: 18 Post(s)
Tagged: 0 Thread(s)
Quoted: 714 Post(s)
Liked 800 Times
in
475 Posts
You guys are making too much of bending the tubing. I just bent this .375 x .035 wall 316 stainless tubing with a cheap Harbor Freight tubing bender. I used this same tubing and bender to make a rack 6 years ago and its still holding up just fine.
#13
Banned
adding to 4th , forge the ends of the steel rod , a shape to curve the tips like the saddle rail
and then hose clamps can secure it..
and then hose clamps can secure it..
#14
Senior Member
Thread Starter
Join Date: Oct 2015
Location: San Diego, California
Posts: 4,077
Bikes: Velo Orange Piolet
Mentioned: 28 Post(s)
Tagged: 0 Thread(s)
Quoted: 2228 Post(s)
Liked 2,011 Times
in
972 Posts
This might be the way to go. Do you think it's possible to flatten the ends of that specific tubing with a vise to make the connection points?
#16
Senior Member
Brazing really isn't hard, for what you're looking to do. You probably have a friend with an oxy-acetylene torch; buy a pack of low-fuming bronze sticks, and offer the rest with a pack of beer for a lesson/use of their torch. 3/8" chrome moly tubing is something like $5 a foot. Just about the only thing easier than that is using tin solder on copper...but if you can do that, you can work with steel, too.
#17
Senior Member
Join Date: Jan 2013
Location: South Jersey
Posts: 2,266
Mentioned: 18 Post(s)
Tagged: 0 Thread(s)
Quoted: 714 Post(s)
Liked 800 Times
in
475 Posts
#18
Senior Member
Thread Starter
Join Date: Oct 2015
Location: San Diego, California
Posts: 4,077
Bikes: Velo Orange Piolet
Mentioned: 28 Post(s)
Tagged: 0 Thread(s)
Quoted: 2228 Post(s)
Liked 2,011 Times
in
972 Posts
Rough sketch:
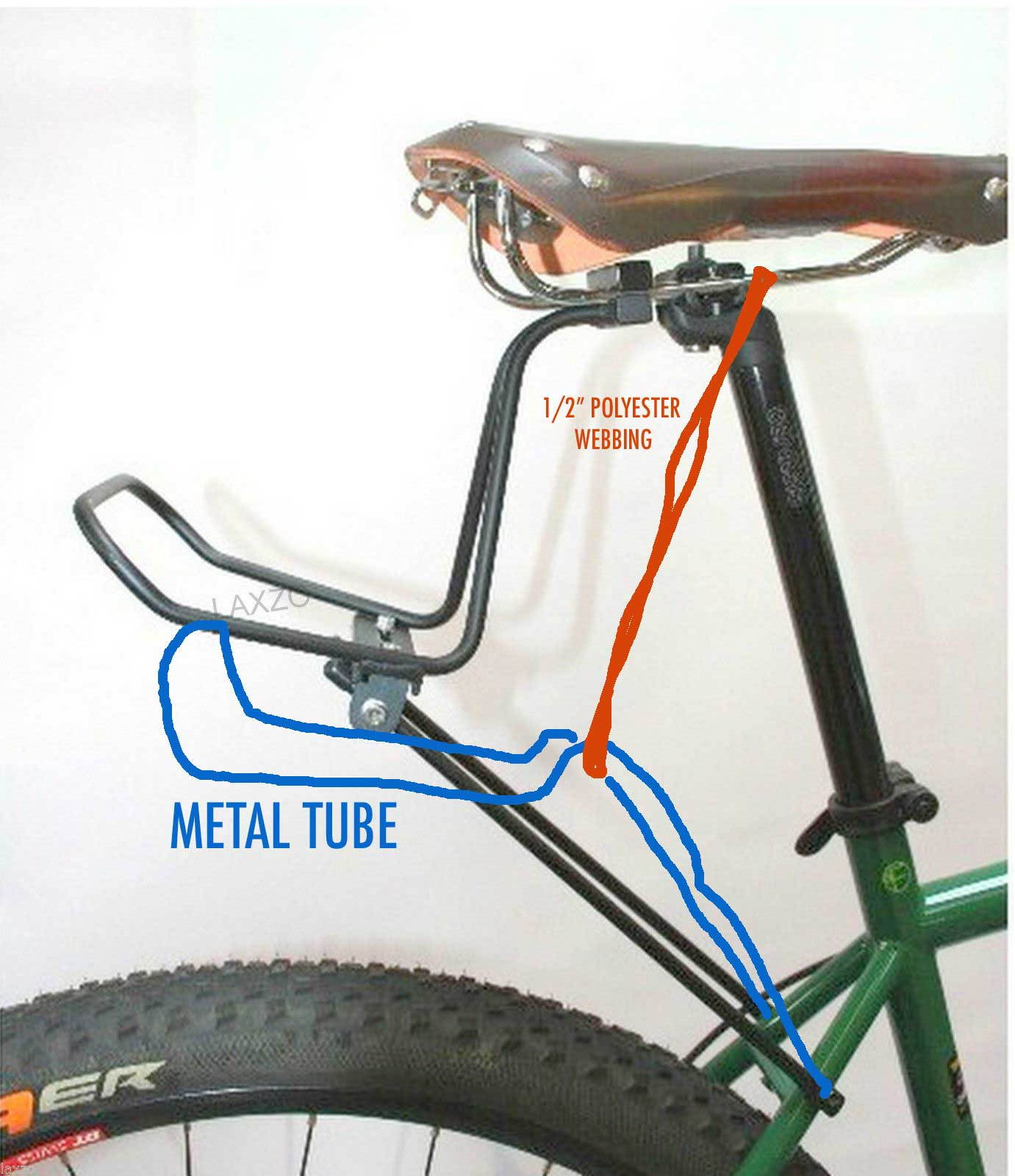
Last edited by tyrion; 06-26-18 at 10:48 AM.
#19
Senior Member
Since outer-skin of structures take majority of load, 3/8" tubing will be way, way stronger than 1/4" solid rod for less weight (to 4th-power ^4 of diameter). It's same principle as making large-diameter hollow bikes rather than solid bar. No one makes a bike-frame from solid bars of any material.
Similar with hub-axles or BB-axles. Larger-diameter hollow is better than solid small-diameter.
Same with handlebars. No one uses 1/2" solid handlebars.
Similar with hub-axles or BB-axles. Larger-diameter hollow is better than solid small-diameter.
Same with handlebars. No one uses 1/2" solid handlebars.
#20
Banned
Yea but that example the Carradice Bagman is not a bike frame, or handlebars.
so Red Herring card on that..
I have a Carradice SQR, bag support, that is made using Rod Stock
And another bag support they included with their Carradura Rear bag ,
Steel ..<chromed>. also rod stock ..
there have been bag supports entirely bent from steel , and plastic coated where it wrapped around the seat stats, above the brake bridge
(I sold the one I had years ago )
but only frames where the seat stay tips are attached to the sides of the frame, Seat /top tube lug,
not behind .."fastback" style as shown..
(where your red line attaches to the blue line ,
that is where that may fail, unless reinforced,
...
so Red Herring card on that..
I have a Carradice SQR, bag support, that is made using Rod Stock
And another bag support they included with their Carradura Rear bag ,
Steel ..<chromed>. also rod stock ..
there have been bag supports entirely bent from steel , and plastic coated where it wrapped around the seat stats, above the brake bridge
(I sold the one I had years ago )
but only frames where the seat stay tips are attached to the sides of the frame, Seat /top tube lug,
not behind .."fastback" style as shown..
(where your red line attaches to the blue line ,
that is where that may fail, unless reinforced,
...
Last edited by fietsbob; 06-26-18 at 01:03 PM.
#22
Senior Member
Thread Starter
Join Date: Oct 2015
Location: San Diego, California
Posts: 4,077
Bikes: Velo Orange Piolet
Mentioned: 28 Post(s)
Tagged: 0 Thread(s)
Quoted: 2228 Post(s)
Liked 2,011 Times
in
972 Posts
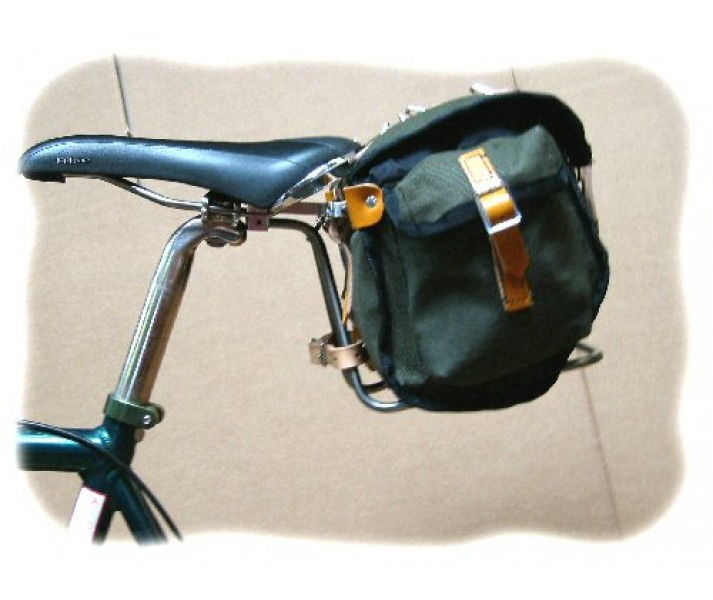
#23
Senior Member
Yeah, actual width of tubing becomes triangulation. Most stress will be at attachment point, so make that beefy.
#24
Senior Member
Join Date: Apr 2011
Posts: 7,067
Mentioned: 41 Post(s)
Tagged: 0 Thread(s)
Quoted: 4409 Post(s)
Liked 1,565 Times
in
1,027 Posts
Seems like the goals of Tyrion's basic design could be accomplished without bending anything. Does the bag support have to be horizontal to work right, or could it be at the same angle it comes off the stays?
#25
Senior Member
Thread Starter
Join Date: Oct 2015
Location: San Diego, California
Posts: 4,077
Bikes: Velo Orange Piolet
Mentioned: 28 Post(s)
Tagged: 0 Thread(s)
Quoted: 2228 Post(s)
Liked 2,011 Times
in
972 Posts
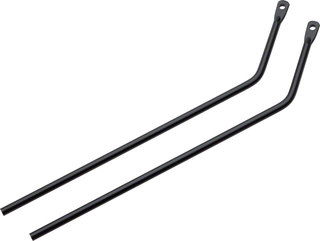
I still might go with those Salsa struts and fashion a little platform. But the homemade bent steel tubing project looks doable for $25 ($15 for tubing and $10 for tube bender).