4130 tubing
#1
Banned.
Thread Starter
Join Date: Nov 2015
Posts: 2,077
Mentioned: 9 Post(s)
Tagged: 0 Thread(s)
Quoted: 760 Post(s)
Likes: 0
Liked 1 Time
in
1 Post
4130 tubing
I know the difference between straight gauge, double, and triple butted, and kinda about heat treated. But I really have no clue about 4130 tubing. Sure it's better than gas pipe. But many low end bicycles use 4130. And some mid range bicycles use 4130 also at twice the price. And there's Renolds 853 and such. SL of a thinner gauge, more difficult to weld properly but builds a lighter thus better frame.
So please educate me. Master!!
So please educate me. Master!!
#2
Senior Member
Join Date: Nov 2014
Location: Eugene, Oregon, USA
Posts: 27,547
Mentioned: 217 Post(s)
Tagged: 0 Thread(s)
Quoted: 18382 Post(s)
Liked 4,515 Times
in
3,355 Posts
4130 would be the generic name for aircraft chromoly steel.
[TABLE]
[TR]
[TD]Carbon[/TD]
[TD][/TD]
[TD="align: right"]0.28 - 0.33[/TD]
[/TR]
[TR]
[TD]Chromium[/TD]
[TD][/TD]
[TD="align: right"]0.8 - 1.1[/TD]
[/TR]
[TR]
[TD="width: 200"]Manganese[/TD]
[TD][/TD]
[TD="width: 100, align: right"]0.4 - 0.9
[/TD]
[/TR]
[TR]
[TD="width: 200"]Molybdenum[/TD]
[TD][/TD]
[TD="width: 100, align: right"]0.15 - 0.25[/TD]
[/TR]
[TR]
[TD="width: 200"]Phosphorus[/TD]
[TD][/TD]
[TD="width: 100, align: right"]0.035 max
[/TD]
[/TR]
[TR]
[TD="width: 200"]Silicon[/TD]
[TD][/TD]
[TD="width: 100, align: right"]0.15 - 0.35[/TD]
[/TR]
[TR]
[TD="width: 200"]Sulphur[/TD]
[TD][/TD]
[TD="width: 100, align: right"]0.04 max[/TD]
[/TR]
[/TABLE]
So, apparently there is some variation in composition.
Does Reynolds and Columbus publish their alloy composition?
One difference (other than butting, usually internally) is that the quality bike components will be seamless. Also, fork blades and chainstays will be tapered. And, of course, the model will also determine the stock thickness.
Hopefully other people will have more details.
Note:
It appears as if the Manganese proportion varies somewhat depending on which source one is reading. Most list 0.4 to 0.6. Others read 0.7 to 0.9, with one reference using the range 0.4 to 0.9.
https://www.suppliersonline.com/propertypages/4130.asp
[TABLE]
[TR]
[TD]Carbon[/TD]
[TD][/TD]
[TD="align: right"]0.28 - 0.33[/TD]
[/TR]
[TR]
[TD]Chromium[/TD]
[TD][/TD]
[TD="align: right"]0.8 - 1.1[/TD]
[/TR]
[TR]
[TD="width: 200"]Manganese[/TD]
[TD][/TD]
[TD="width: 100, align: right"]0.4 - 0.9
[/TD]
[/TR]
[TR]
[TD="width: 200"]Molybdenum[/TD]
[TD][/TD]
[TD="width: 100, align: right"]0.15 - 0.25[/TD]
[/TR]
[TR]
[TD="width: 200"]Phosphorus[/TD]
[TD][/TD]
[TD="width: 100, align: right"]0.035 max
[/TD]
[/TR]
[TR]
[TD="width: 200"]Silicon[/TD]
[TD][/TD]
[TD="width: 100, align: right"]0.15 - 0.35[/TD]
[/TR]
[TR]
[TD="width: 200"]Sulphur[/TD]
[TD][/TD]
[TD="width: 100, align: right"]0.04 max[/TD]
[/TR]
[/TABLE]
So, apparently there is some variation in composition.
Does Reynolds and Columbus publish their alloy composition?
One difference (other than butting, usually internally) is that the quality bike components will be seamless. Also, fork blades and chainstays will be tapered. And, of course, the model will also determine the stock thickness.
Hopefully other people will have more details.
Note:
It appears as if the Manganese proportion varies somewhat depending on which source one is reading. Most list 0.4 to 0.6. Others read 0.7 to 0.9, with one reference using the range 0.4 to 0.9.
https://www.suppliersonline.com/propertypages/4130.asp
Last edited by CliffordK; 01-20-16 at 07:54 PM.
#3
Senior Member
I think everybody uses different formulations so if you buy tubes by Reynolds, Columbus, True Temper, Tange, KVA, etc., it's all a little different. I think the term 4130 has devolved somewhat into a description of higher end pipes. I pay attention to diameter and wall thickness rather than what's in the steel.
Seamed tubes used to be low end but True Temper OX platinum is seamed and it's very good stuff. Don't run away from a modern tubeset just because it's seamed.
Seamed tubes used to be low end but True Temper OX platinum is seamed and it's very good stuff. Don't run away from a modern tubeset just because it's seamed.
#4
Decrepit Member
4130 is an AISI standard. Reynolds 525 and the Taiwan manufactured Reynolds 520 are 4130. Reynolds has always been forthcoming in publishing the chemistry of the various alloys they use for their steel tubing.
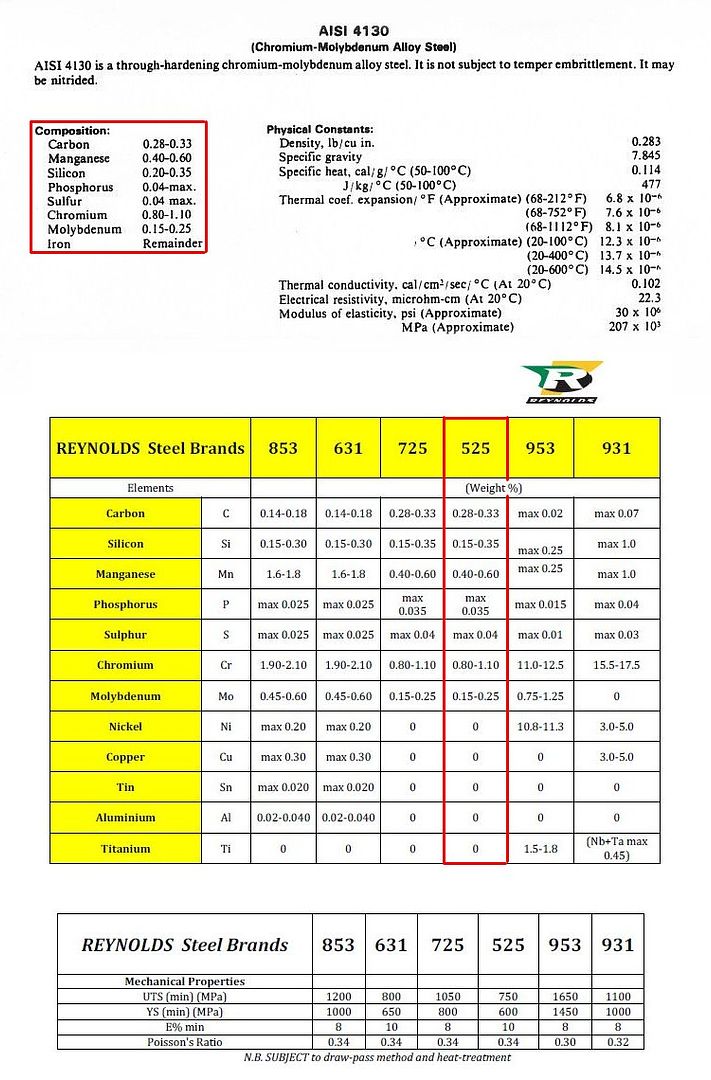
Here's the 531 (and 753) chemistry. 753 is heat treated 531 to achieve higher strength.
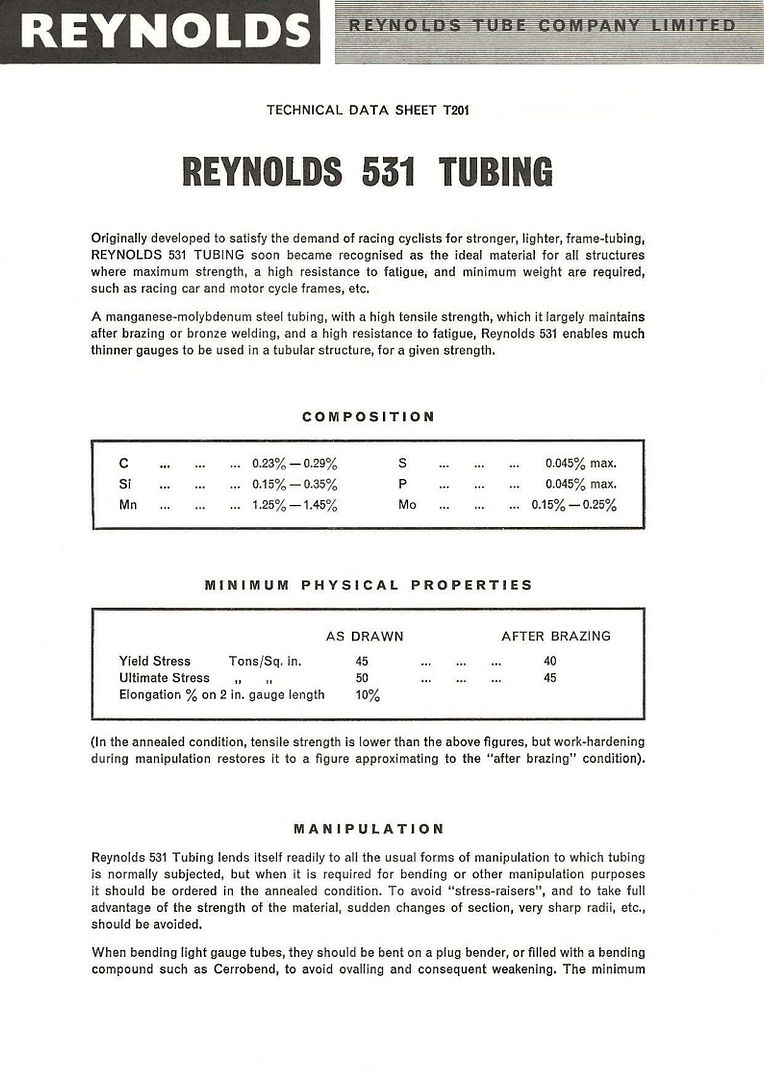
Here's a graph explaining the SAE-AISI steel alloy numbering system as well as a rundown of the effects of different elements in steel alloys. The source for both the graph below and the effects of different elements in steel alloys are from https://www.materialsengineer.com/E-Alloying-Steels.htm, which apparently is not currently available.
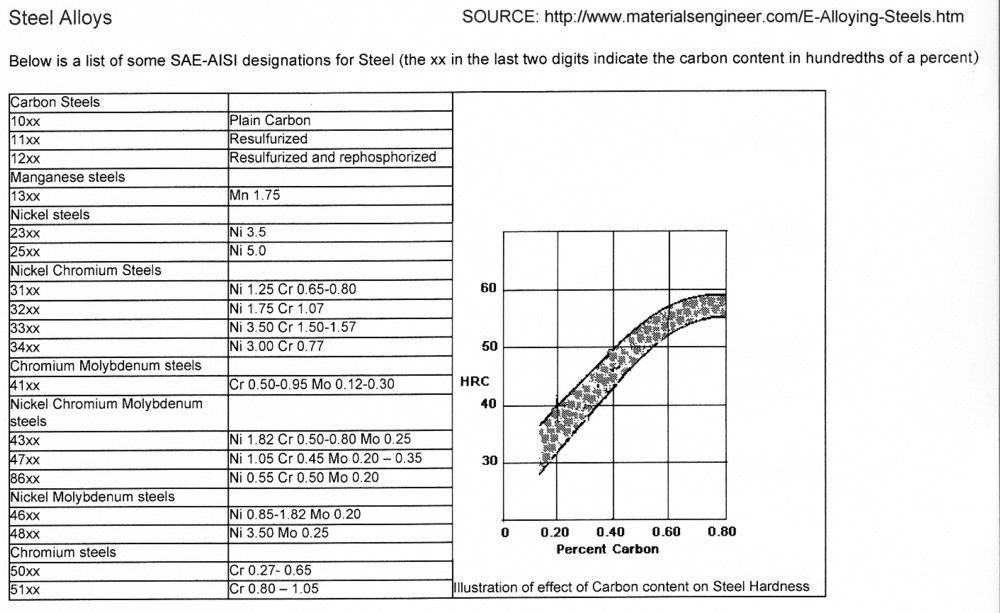
Effects of Elements on Steel
Steels are among the most commonly used alloys. The complexity of steel alloys is fairly significant. Not all effects of the varying elements are included. The following text gives an overview of some of the effects of various alloying elements. Additional research should be performed prior to making any design or engineering conclusions.
Carbon has a major effect on steel properties. Carbon is the primary hardening element in steel. Hardness and tensile strength increases as carbon content increases up to about 0.85% C as shown in the figure above. Ductility and weldability decrease with increasing carbon.
Manganese is generally beneficial to surface quality especially in resulfurized steels. Manganese contributes to strength and hardness, but less than carbon. The increase in strength is dependent upon the carbon content. Increasing the manganese content decreases ductility and weldability, but less than carbon. Manganese has a significant effect on the hardenability of steel.
Phosphorus increases strength and hardness and decreases ductility and notch impact toughness of steel. The adverse effects on ductility and toughness are greater in quenched and tempered higher-carbon steels. Phosphorous levels are normally controlled to low levels. Higher phosphorus is specified in low-carbon free-machining steels to improve machinability.
Sulfur decreases ductility and notch impact toughness especially in the transverse direction. Weldability decreases with increasing sulfur content. Sulfur is found primarily in the form of sulfide inclusions. Sulfur levels are normally controlled to low levels. The only exception is free-machining steels, where sulfur is added to improve machinability.
Silicon is one of the principal deoxidizers used in steelmaking. Silicon is less effective than manganese in increasing as-rolled strength and hardness. In low-carbon steels, silicon is generally detrimental to surface quality.
Copper in significant amounts is detrimental to hot-working steels. Copper negatively affects forge welding, but does not seriously affect arc or oxyacetylene welding. Copper can be detrimental to surface quality. Copper is beneficial to atmospheric corrosion resistance when present in amounts exceeding 0.20%. Weathering steels are sold having greater than 0.20% Copper.
Lead is virtually insoluble in liquid or solid steel. However, lead is sometimes added to carbon and alloy steels by means of mechanical dispersion during pouring to improve the machinability.
Boron is added to fully killed steel to improve hardenability. Boron-treated steels are produced to a range of 0.0005 to 0.003%. Whenever boron is substituted in part for other alloys, it should be done only with hardenability in mind because the lowered alloy content may be harmful for some applications. Boron is a potent alloying element in steel. A very small amount of boron (about 0.001%) has a strong effect on hardenability. Boron steels are generally produced within a range of 0.0005 to 0.003%. Boron is most effective in lower carbon steels.
Chromium is commonly added to steel to increase corrosion resistance and oxidation resistance, to increase hardenability, or to improve high-temperature strength. As a hardening element, Chromium is frequently used with a toughening element such as nickel to produce superior mechanical properties. At higher temperatures, chromium contributes increased strength. Chromium is a strong carbide former. Complex chromium-iron carbides go into solution in austenite slowly; therefore, sufficient heating time must be allowed for prior to quenching.
Nickel is a ferrite strengthener. Nickel does not form carbides in steel. It remains in solution in ferrite, strengthening and toughening the ferrite phase. Nickel increases the hardenability and impact strength of steels.
Molybdenum increases the hardenability of steel. Molybdenum may produce secondary hardening during the tempering of quenched steels. It enhances the creep strength of low-alloy steels at elevated temperatures.
Aluminum is widely used as a deoxidizer. Aluminum can control austenite grain growth in reheated steels and is therefore added to control grain size. Aluminum is the most effective alloy in controlling grain growth prior to quenching. Titanium, zirconium, and vanadium are also valuable grain growth inhibitors, but there carbides are difficult to dissolve into solution in austenite.
Zirconium can be added to killed high-strength low-alloy steels to achieve improvements in inclusion characteristics. Zirconium causes sulfide inclusions to be globular rather than elongated thus improving toughness and ductility in transverse bending.
Niobium (Columbium) increases the yield strength and, to a lesser degree, the tensile strength of carbon steel. The addition of small amounts of Niobium can significantly increase the yield strength of steels. Niobium can also have a moderate precipitation strengthening effect. Its main contributions are to form precipitates above the transformation temperature, and to ret@rd the recrystallization of austenite, thus promoting a fine-grain microstructure having improved strength and toughness.
Titanium is used to ret@rd grain growth and thus improve toughness. Titanium is also used to achieve improvements in inclusion characteristics. Titanium causes sulfide inclusions to be globular rather than elongated thus improving toughness and ductility in transverse bending.
Vanadium increases the yield strength and the tensile strength of carbon steel. The addition of small amounts of Vanadium can significantly increase the strength of steels. Vanadium is one of the primary contributors to precipitation strengthening in microalloyed steels. When thermomechanical processing is properly controlled the ferrite grain size is refined and there is a corresponding increase in toughness. The impact transition temperature also increases when vanadium is added.
All microalloy steels contain small concentrations of one or more strong carbide and nitride forming elements. Vanadium, niobium, and titanium combine preferentially with carbon and/or nitrogen to form a fine dispersion of precipitated particles in the steel matrix.
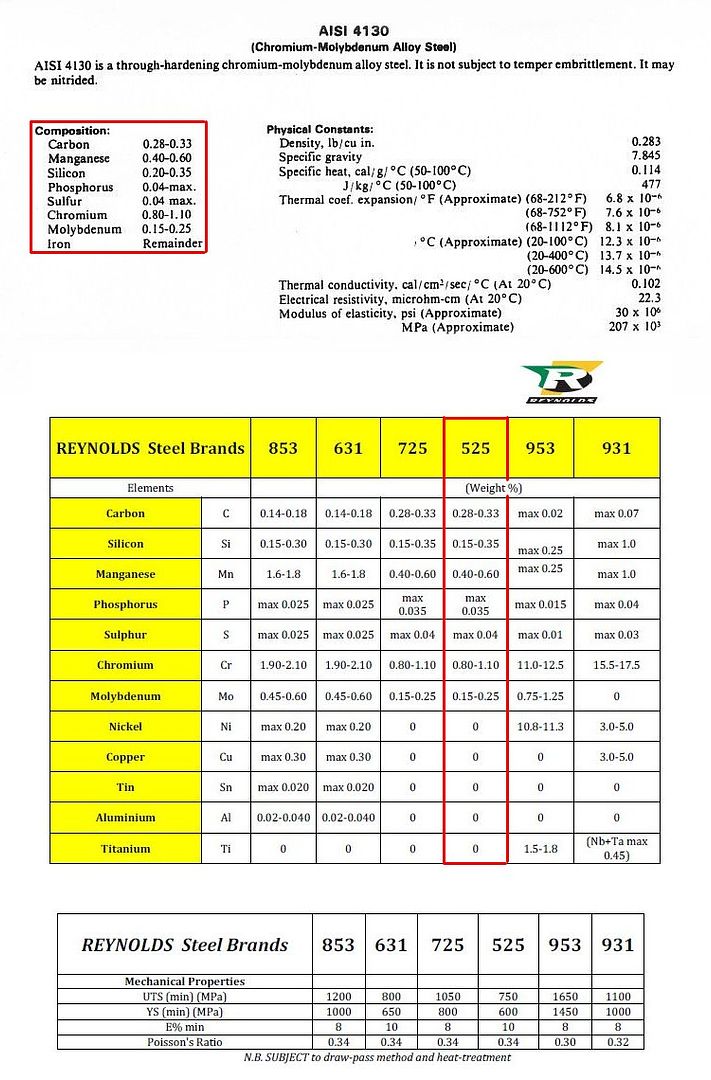
Here's the 531 (and 753) chemistry. 753 is heat treated 531 to achieve higher strength.
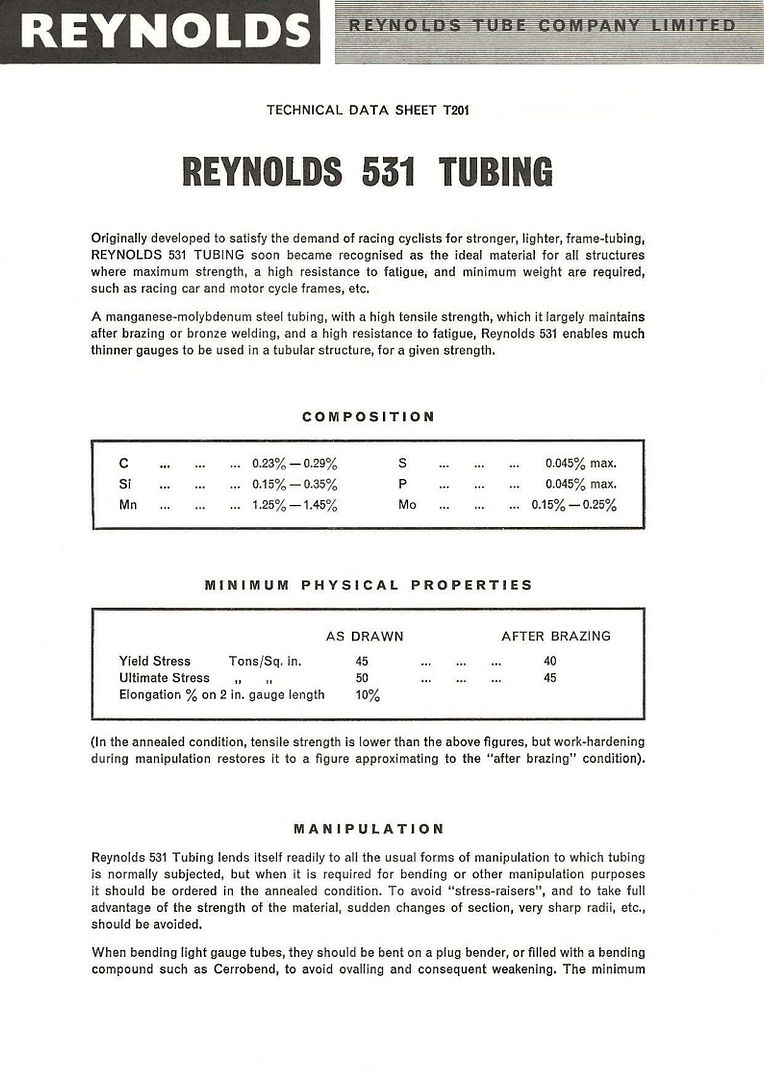
Here's a graph explaining the SAE-AISI steel alloy numbering system as well as a rundown of the effects of different elements in steel alloys. The source for both the graph below and the effects of different elements in steel alloys are from https://www.materialsengineer.com/E-Alloying-Steels.htm, which apparently is not currently available.
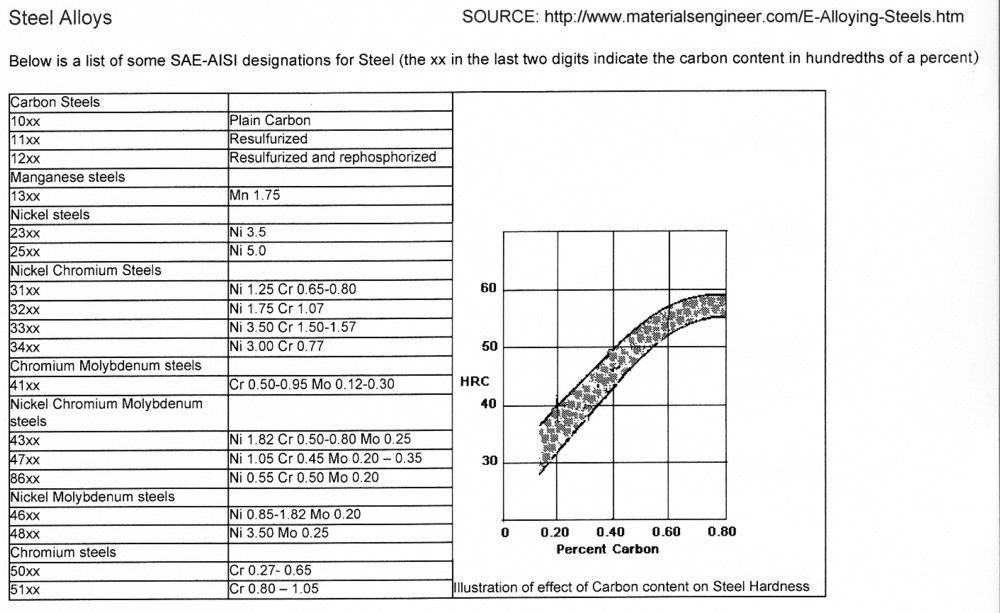
Effects of Elements on Steel
Steels are among the most commonly used alloys. The complexity of steel alloys is fairly significant. Not all effects of the varying elements are included. The following text gives an overview of some of the effects of various alloying elements. Additional research should be performed prior to making any design or engineering conclusions.
Carbon has a major effect on steel properties. Carbon is the primary hardening element in steel. Hardness and tensile strength increases as carbon content increases up to about 0.85% C as shown in the figure above. Ductility and weldability decrease with increasing carbon.
Manganese is generally beneficial to surface quality especially in resulfurized steels. Manganese contributes to strength and hardness, but less than carbon. The increase in strength is dependent upon the carbon content. Increasing the manganese content decreases ductility and weldability, but less than carbon. Manganese has a significant effect on the hardenability of steel.
Phosphorus increases strength and hardness and decreases ductility and notch impact toughness of steel. The adverse effects on ductility and toughness are greater in quenched and tempered higher-carbon steels. Phosphorous levels are normally controlled to low levels. Higher phosphorus is specified in low-carbon free-machining steels to improve machinability.
Sulfur decreases ductility and notch impact toughness especially in the transverse direction. Weldability decreases with increasing sulfur content. Sulfur is found primarily in the form of sulfide inclusions. Sulfur levels are normally controlled to low levels. The only exception is free-machining steels, where sulfur is added to improve machinability.
Silicon is one of the principal deoxidizers used in steelmaking. Silicon is less effective than manganese in increasing as-rolled strength and hardness. In low-carbon steels, silicon is generally detrimental to surface quality.
Copper in significant amounts is detrimental to hot-working steels. Copper negatively affects forge welding, but does not seriously affect arc or oxyacetylene welding. Copper can be detrimental to surface quality. Copper is beneficial to atmospheric corrosion resistance when present in amounts exceeding 0.20%. Weathering steels are sold having greater than 0.20% Copper.
Lead is virtually insoluble in liquid or solid steel. However, lead is sometimes added to carbon and alloy steels by means of mechanical dispersion during pouring to improve the machinability.
Boron is added to fully killed steel to improve hardenability. Boron-treated steels are produced to a range of 0.0005 to 0.003%. Whenever boron is substituted in part for other alloys, it should be done only with hardenability in mind because the lowered alloy content may be harmful for some applications. Boron is a potent alloying element in steel. A very small amount of boron (about 0.001%) has a strong effect on hardenability. Boron steels are generally produced within a range of 0.0005 to 0.003%. Boron is most effective in lower carbon steels.
Chromium is commonly added to steel to increase corrosion resistance and oxidation resistance, to increase hardenability, or to improve high-temperature strength. As a hardening element, Chromium is frequently used with a toughening element such as nickel to produce superior mechanical properties. At higher temperatures, chromium contributes increased strength. Chromium is a strong carbide former. Complex chromium-iron carbides go into solution in austenite slowly; therefore, sufficient heating time must be allowed for prior to quenching.
Nickel is a ferrite strengthener. Nickel does not form carbides in steel. It remains in solution in ferrite, strengthening and toughening the ferrite phase. Nickel increases the hardenability and impact strength of steels.
Molybdenum increases the hardenability of steel. Molybdenum may produce secondary hardening during the tempering of quenched steels. It enhances the creep strength of low-alloy steels at elevated temperatures.
Aluminum is widely used as a deoxidizer. Aluminum can control austenite grain growth in reheated steels and is therefore added to control grain size. Aluminum is the most effective alloy in controlling grain growth prior to quenching. Titanium, zirconium, and vanadium are also valuable grain growth inhibitors, but there carbides are difficult to dissolve into solution in austenite.
Zirconium can be added to killed high-strength low-alloy steels to achieve improvements in inclusion characteristics. Zirconium causes sulfide inclusions to be globular rather than elongated thus improving toughness and ductility in transverse bending.
Niobium (Columbium) increases the yield strength and, to a lesser degree, the tensile strength of carbon steel. The addition of small amounts of Niobium can significantly increase the yield strength of steels. Niobium can also have a moderate precipitation strengthening effect. Its main contributions are to form precipitates above the transformation temperature, and to ret@rd the recrystallization of austenite, thus promoting a fine-grain microstructure having improved strength and toughness.
Titanium is used to ret@rd grain growth and thus improve toughness. Titanium is also used to achieve improvements in inclusion characteristics. Titanium causes sulfide inclusions to be globular rather than elongated thus improving toughness and ductility in transverse bending.
Vanadium increases the yield strength and the tensile strength of carbon steel. The addition of small amounts of Vanadium can significantly increase the strength of steels. Vanadium is one of the primary contributors to precipitation strengthening in microalloyed steels. When thermomechanical processing is properly controlled the ferrite grain size is refined and there is a corresponding increase in toughness. The impact transition temperature also increases when vanadium is added.
All microalloy steels contain small concentrations of one or more strong carbide and nitride forming elements. Vanadium, niobium, and titanium combine preferentially with carbon and/or nitrogen to form a fine dispersion of precipitated particles in the steel matrix.
#5
Senior Member
Join Date: Nov 2014
Location: Eugene, Oregon, USA
Posts: 27,547
Mentioned: 217 Post(s)
Tagged: 0 Thread(s)
Quoted: 18382 Post(s)
Liked 4,515 Times
in
3,355 Posts
Thanks for the notes Scooper,
I was looking at the Manganese proportion in 4130, and noted several different values depending on the source.
I have a Jamis with 520. I don't know if it was chromed, but it has a bright silver finish (clearcoat in bad shape), but very little rust.
I was looking at the Manganese proportion in 4130, and noted several different values depending on the source.
I have a Jamis with 520. I don't know if it was chromed, but it has a bright silver finish (clearcoat in bad shape), but very little rust.
#6
Disco Infiltrator
Join Date: May 2013
Location: Folsom CA
Posts: 13,446
Bikes: Stormchaser, Paramount, Tilt, Samba tandem
Mentioned: 72 Post(s)
Tagged: 0 Thread(s)
Quoted: 3126 Post(s)
Liked 2,105 Times
in
1,369 Posts
I think it's entertaining how the bike industry uses these things as sort of informal brands or code words.
__________________
Genesis 49:16-17
Genesis 49:16-17
#7
Senior Member
Join Date: Sep 2006
Location: Boise, ID
Posts: 378
Bikes: 2005 Performer Toscana, RANS V3 steel, RANS Citi, Kona Hoo-Ha
Mentioned: 1 Post(s)
Tagged: 0 Thread(s)
Quoted: 3 Post(s)
Liked 0 Times
in
0 Posts
Actually, many low end bikes use high tensile steel, which is just one small step above gas pipe. Every Walmart/Magna/Huffy probably ever made is hi-tensile because the materials cost is much lower. If a bike uses 4130, it will often be labeled as such.
#9
Senior Member
Join Date: Oct 2014
Location: Portland, OR
Posts: 12,910
Bikes: (2) ti TiCycles, 2007 w/ triple and 2011 fixed, 1979 Peter Mooney, ~1983 Trek 420 now fixed and ~1973 Raleigh Carlton Competition gravel grinder
Mentioned: 129 Post(s)
Tagged: 0 Thread(s)
Quoted: 4806 Post(s)
Liked 3,933 Times
in
2,558 Posts
We are losing sight of what really matters. Tube diameter and wall thickness. These are all steels. If we make two bikes, one from gas pipe and the other from 953 with the identical diameters and tube thicknesses, the will weight the same and ride identically. (Not quite true. Stainless steels are a little different, both in weight and stiffness, but by maybe 2%. Still those judging the frames will have a tough time telling them apart.) Until they jump them off a high jump, then the gas pipe will bend. But 50 miles of racing on halfway decent roads. No difference at all.
The huge advantage of high strength steels is that they allow framebuilders to use much thinner wall tubings. This allows the diameters to get enlarged for stiffness. If you are willing to have a frame that dents easily, you can have the light weight and stiffness made possible by the high end tubes. If you stick with the old smaller diameters to get the wall thickness up and hold the weight to something reasonable so you can have a durable, bump resistant frame, the strength of the tubing and therefor the "whiz-factor" matter far less.
Ben
#10
Decrepit Member
This table compares the ultimate tensile strength and yield strength of several steel alloys. As Ben points out, in the Reynolds chart only 525 and 725 have chemistry that meets the AISI Standard 4130; everything else on the chart, including 853, is some other alloy. 725 is heat treated 525 to achieve higher strength.
Generally speaking, "high tensile" or "Hi-ten" alloy is plain carbon steel like AISI 1010, 1020, or 1030, and have lower UTS and YS than 4130 chromium-molybdenum and higher strength alloys like 853 and 953. Some time ago, I put together this table using the referenced standards and manufacturers' literature.

All steel alloys from AISI 1010 to Reynolds 953 (Carpenter Technology Custom 455) have virtually the same density (~0.28 pounds per cubic inch) and virtually the same Modulus of Elasticity (E), or "stiffness", of ~200 GPa. So the biggest properties that differentiate them are strength, and elasticity which is a property describing the ductility/brittleness of the alloy. As Ben explained, stronger alloy tubing can be drawn with thinner walls which means less material and therefore less weight. The big downside of thinner walls is a loss of stiffness, so to restore stiffness lost by drawing the walls thinner, the tubing diameters were increased by developing oversize and extra oversize tubing diameters.
Generally speaking, "high tensile" or "Hi-ten" alloy is plain carbon steel like AISI 1010, 1020, or 1030, and have lower UTS and YS than 4130 chromium-molybdenum and higher strength alloys like 853 and 953. Some time ago, I put together this table using the referenced standards and manufacturers' literature.

All steel alloys from AISI 1010 to Reynolds 953 (Carpenter Technology Custom 455) have virtually the same density (~0.28 pounds per cubic inch) and virtually the same Modulus of Elasticity (E), or "stiffness", of ~200 GPa. So the biggest properties that differentiate them are strength, and elasticity which is a property describing the ductility/brittleness of the alloy. As Ben explained, stronger alloy tubing can be drawn with thinner walls which means less material and therefore less weight. The big downside of thinner walls is a loss of stiffness, so to restore stiffness lost by drawing the walls thinner, the tubing diameters were increased by developing oversize and extra oversize tubing diameters.
#11
Decrepit Member
Just for kicks, this table compares the properties and chemistry of the five currently available stainless steel tubesets (KVA MS3 has replaced MS2, but I haven't updated the table yet).
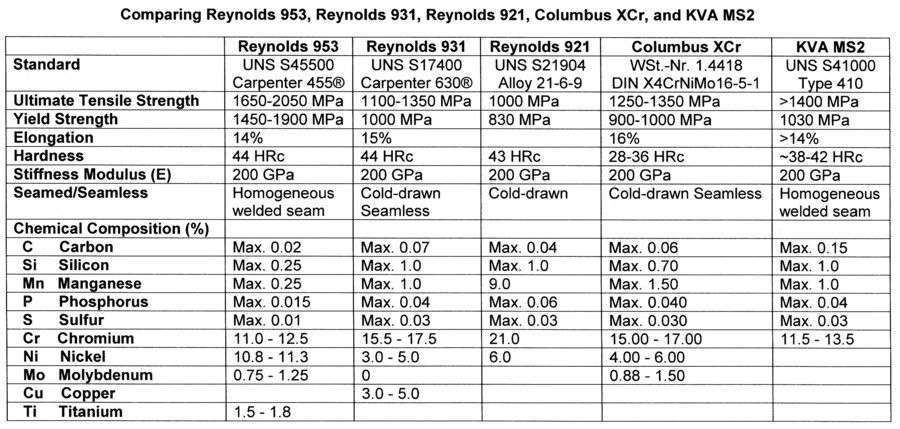
#12
Senior Member
Join Date: Nov 2014
Location: Eugene, Oregon, USA
Posts: 27,547
Mentioned: 217 Post(s)
Tagged: 0 Thread(s)
Quoted: 18382 Post(s)
Liked 4,515 Times
in
3,355 Posts
Keep in mind that one of the reasons that chromoly (4130) is popular is that it is relatively tolerant to high weld temperatures, with minimal loss of strength at the welds.
Reynolds 531 is much less tolerant of TIG welding temperatures.
Reynolds 531 is much less tolerant of TIG welding temperatures.
#13
Decrepit Member
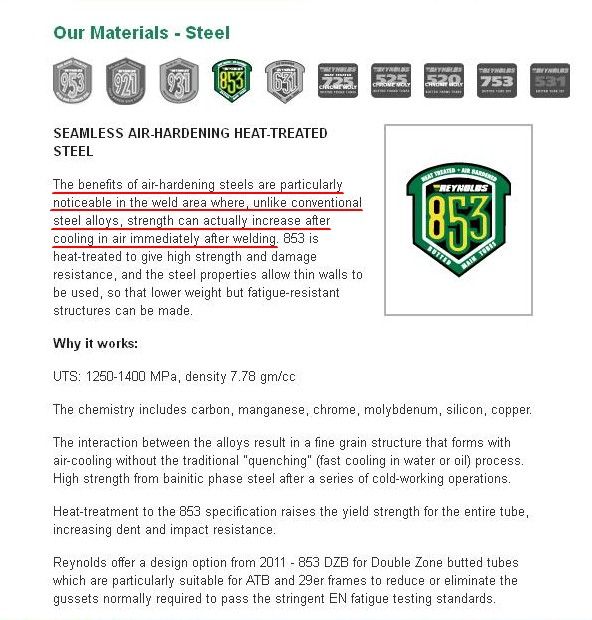
#14
Old fart
Join Date: Nov 2004
Location: Appleton WI
Posts: 24,792
Bikes: Several, mostly not name brands.
Mentioned: 153 Post(s)
Tagged: 0 Thread(s)
Quoted: 3591 Post(s)
Liked 3,401 Times
in
1,935 Posts
"4130" steel just describes the alloy in a general way. For bicycle frames, the particular alloy is only one of several characteristics to take into account. Other would include wall thickness, tube diameter, tapering/shaping, heat treatment, temperature tolerance (welding versus brazing), seamless versus seamed, etc.
#15
Randomhead
Join Date: Aug 2008
Location: Happy Valley, Pennsylvania
Posts: 24,402
Mentioned: 0 Post(s)
Tagged: 0 Thread(s)
Quoted: 4 Post(s)
Liked 3,701 Times
in
2,521 Posts
4130 varies widely in quality. Assuming it all has the same material properties, there are lots of other things that can affect suitability. A lot of times, the cheaper bikes use a lot more of it because they are afraid of the quality of the welding. And a lot of it comes with pits on the surface nowadays, so you have to accommodate that too. Bicycle tubing is drawn to a much higher standard.
Thread
Thread Starter
Forum
Replies
Last Post
Regulatori
Singlespeed & Fixed Gear
16
01-29-16 08:34 PM
BluesDawg
Fifty Plus (50+)
27
04-10-15 02:33 PM
joejeweler
Hybrid Bicycles
2
06-14-12 07:54 PM
joejeweler
Mountain Biking
2
06-14-12 07:51 PM