Discussion of a bad idea - yes, drilling carbon
#1
Senior Member
Thread Starter
Join Date: May 2021
Location: San Francisco
Posts: 2,039
Bikes: addict, aethos, creo, vanmoof, sirrus, public ...
Mentioned: 2 Post(s)
Tagged: 0 Thread(s)
Quoted: 1279 Post(s)
Liked 1,393 Times
in
711 Posts
Discussion of a bad idea - yes, drilling carbon
i will preface this by saying that there's almost no chance i would do this, but i'm interested in the discussion and curious what someone who knows more about the design and construction of carbon bicycle components would say, other than the knee jerk "DO NOT EVER DO THIS YOU IDIOT."
i have a one piece carbon bar stem (scott/syncros creston sl ic) on an electric road bike. it has a very sturdy two bolt accessory mount - unlike the very, very light roval alpinist bars on my other bike, which use one hold and worry me a bit with heavier computer/phone mounted.
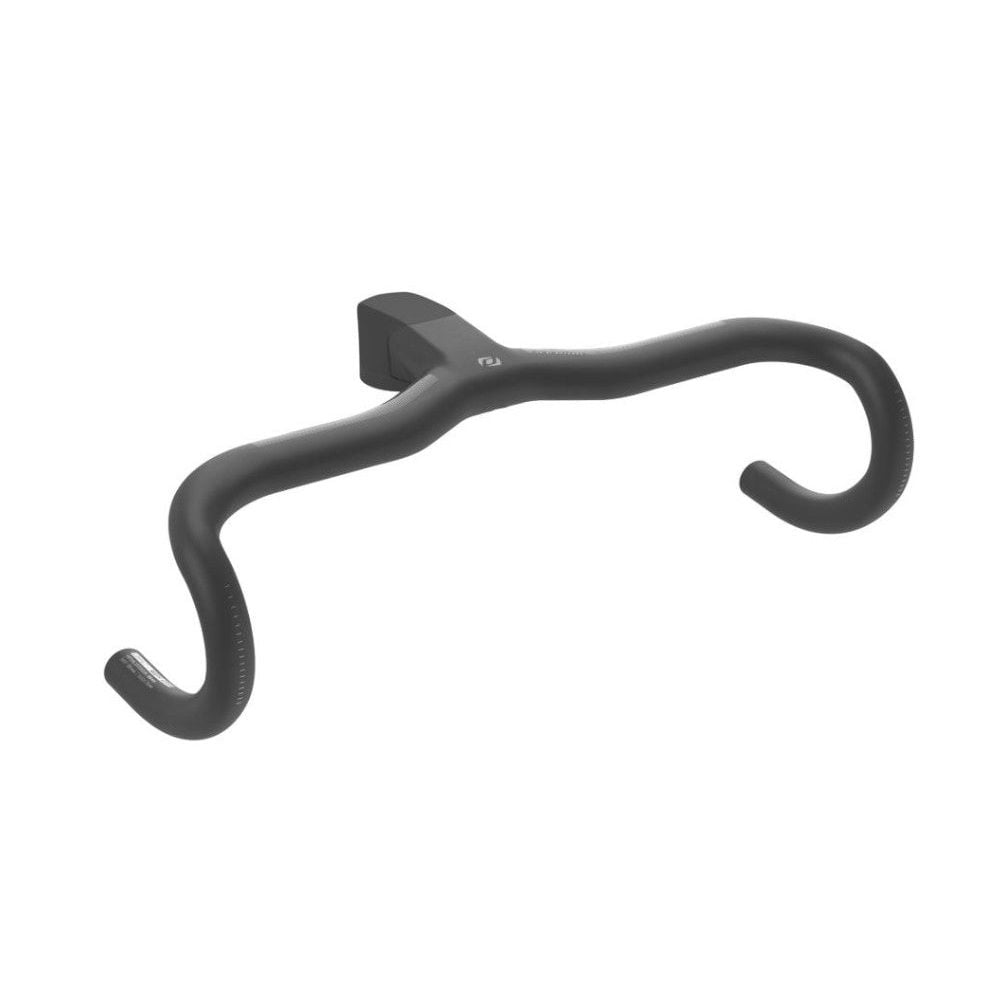
i use this bike as a commuter, and it's winter, so i've made a custom mount that has a battery powered light hanging from the bottom, centered under the holes. the light is removable for charging, it works well. but it's silly to ride around with a 230wh battery inside the bike and a separate battery powered light adding weight and bulk and needing charging. so, i'd love to wire a light to the internal battery. there's a wire for that. there's an easy route from the internal battery to the interior of the bars. there is no additional hole in that area.
so, three options : 1, leave it as is, don't die. 2, revise my mount to only use ONE of the screws, and probably some VHB tape over a reasonably large surface area including the entire area between and around the holes, and pass a wire through one of the holes. 3, drill a hole using the right drill bit between the holes, gob some epoxy around the edges etc.
i don't design bikes or bike parts but the things i do design often would have reinforcing along the blue lines i doodled there (not my picture, same cockpit.) what are the odds that it's not like this, that all the reinforcing and important fibers go completely around the two-hole area, and i could drill a small hole between the holes with zero risk of assplosion?
badIdea.jpg :
i have a one piece carbon bar stem (scott/syncros creston sl ic) on an electric road bike. it has a very sturdy two bolt accessory mount - unlike the very, very light roval alpinist bars on my other bike, which use one hold and worry me a bit with heavier computer/phone mounted.
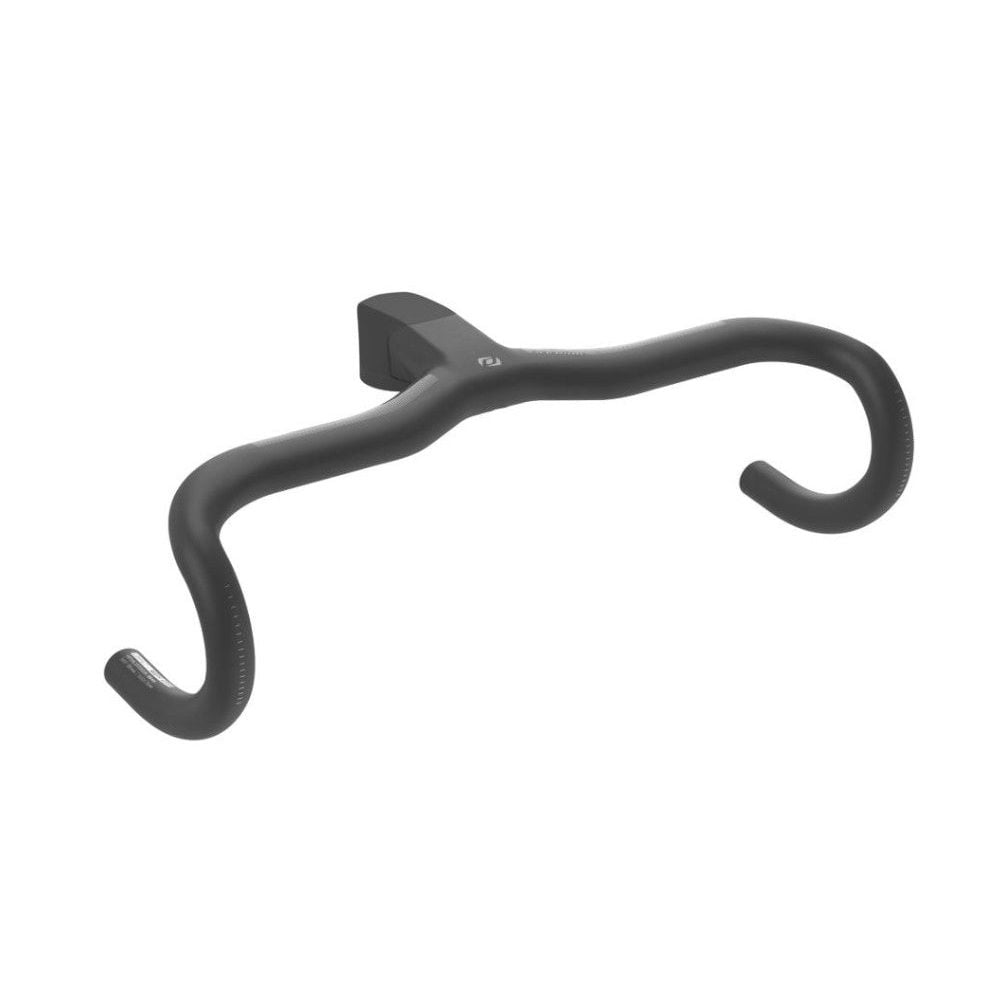
i use this bike as a commuter, and it's winter, so i've made a custom mount that has a battery powered light hanging from the bottom, centered under the holes. the light is removable for charging, it works well. but it's silly to ride around with a 230wh battery inside the bike and a separate battery powered light adding weight and bulk and needing charging. so, i'd love to wire a light to the internal battery. there's a wire for that. there's an easy route from the internal battery to the interior of the bars. there is no additional hole in that area.
so, three options : 1, leave it as is, don't die. 2, revise my mount to only use ONE of the screws, and probably some VHB tape over a reasonably large surface area including the entire area between and around the holes, and pass a wire through one of the holes. 3, drill a hole using the right drill bit between the holes, gob some epoxy around the edges etc.
i don't design bikes or bike parts but the things i do design often would have reinforcing along the blue lines i doodled there (not my picture, same cockpit.) what are the odds that it's not like this, that all the reinforcing and important fibers go completely around the two-hole area, and i could drill a small hole between the holes with zero risk of assplosion?
badIdea.jpg :
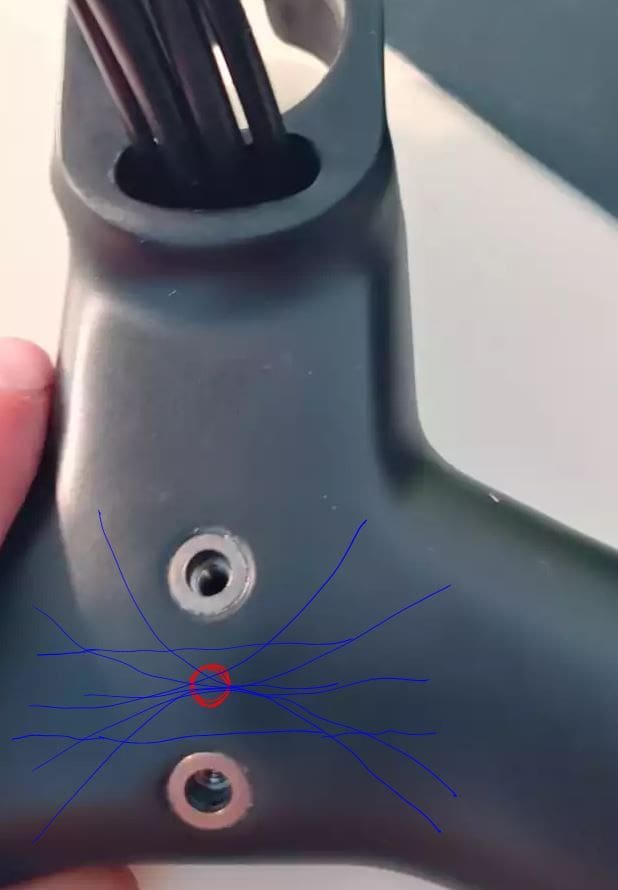
#2
Randomhead
Join Date: Aug 2008
Location: Happy Valley, Pennsylvania
Posts: 24,399
Mentioned: 0 Post(s)
Tagged: 0 Thread(s)
Quoted: 4 Post(s)
Liked 3,699 Times
in
2,519 Posts
It's extremely difficult to drill carbon without damage. I was looking at some forks recently, and there were pads glued to the outside. That's what I would do if I couldn't figure out how to piggyback on the mounts that are already there. Which I feel fairly confident I could do.
It is possible to tell how thick the carbon is there with ultrasonics. The way I look at it, that's not enough to tell you much about post-modification safety.
It is possible to tell how thick the carbon is there with ultrasonics. The way I look at it, that's not enough to tell you much about post-modification safety.
Likes For unterhausen:
#3
Senior Member
Thread Starter
Join Date: May 2021
Location: San Francisco
Posts: 2,039
Bikes: addict, aethos, creo, vanmoof, sirrus, public ...
Mentioned: 2 Post(s)
Tagged: 0 Thread(s)
Quoted: 1279 Post(s)
Liked 1,393 Times
in
711 Posts
It's extremely difficult to drill carbon without damage. I was looking at some forks recently, and there were pads glued to the outside. That's what I would do if I couldn't figure out how to piggyback on the mounts that are already there. Which I feel fairly confident I could do.
It is possible to tell how thick the carbon is there with ultrasonics. The way I look at it, that's not enough to tell you much about post-modification safety.
It is possible to tell how thick the carbon is there with ultrasonics. The way I look at it, that's not enough to tell you much about post-modification safety.
__________________

#4
semi-retired framebuilder
Idea 4 - fabricate a small aluminum plate that bolts to the two existing holes, and mount the light to that by drilling two new holes in the aluminum plate in the right places. I wouldn't drill carbon, no.
Likes For Mark Beaver:
#5
Senior Member
Thread Starter
Join Date: May 2021
Location: San Francisco
Posts: 2,039
Bikes: addict, aethos, creo, vanmoof, sirrus, public ...
Mentioned: 2 Post(s)
Tagged: 0 Thread(s)
Quoted: 1279 Post(s)
Liked 1,393 Times
in
711 Posts
the mounting of the light isn’t the issue… the two holes are fine for all that. it’s creating a fully concealed route for the electrical wire. i’ll share an image of the part which i’ve made that attaches the light and phone to the two holes, which works well!
__________________

#6
Senior Member
Join Date: Dec 2019
Posts: 956
Mentioned: 3 Post(s)
Tagged: 0 Thread(s)
Quoted: 321 Post(s)
Liked 263 Times
in
212 Posts
What if you glue an aluminium plate to the carbon first and then drill through the whole lot in one go? The idea being that the glue will stop the hole chowdering up into splinters of death as you drill (although the back-side will still do that a bit probably). Obviously sand it down a bit first and make sure you get a good bond.
#7
Senior Member
Thread Starter
Join Date: May 2021
Location: San Francisco
Posts: 2,039
Bikes: addict, aethos, creo, vanmoof, sirrus, public ...
Mentioned: 2 Post(s)
Tagged: 0 Thread(s)
Quoted: 1279 Post(s)
Liked 1,393 Times
in
711 Posts
for a little more context,
here's a version of the attachment i made for a battery powered light - the white stuff is freshly 3d printed, it will be painted matte black. the bolt through the captured nut has a thumbscrew on the other side allowing the light to be easily removed for charging. but it's a pretty heavy light. would be way better to connect it to the bike's battery. obviously the part which the light slides into (which is an extremely tight fit, not going anywhere) would be made differently for a smaller wired light.
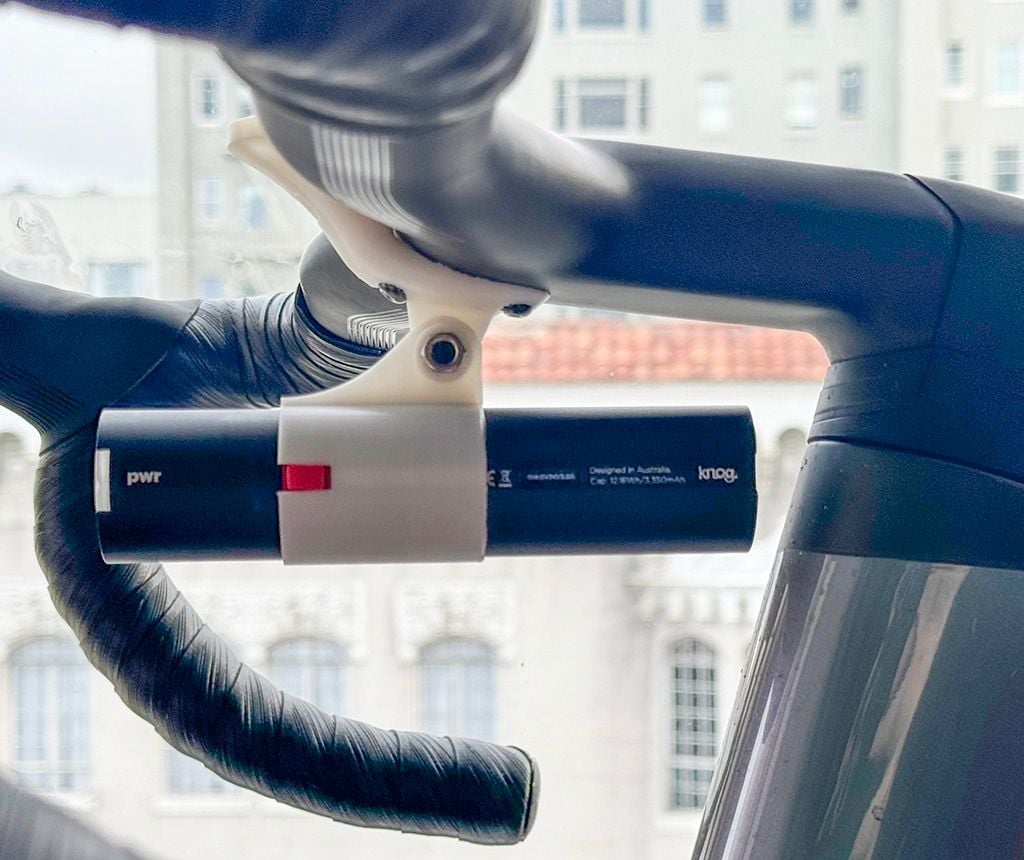
from below - the two black bolts are into the pair of embeds in the bar. there are no other holes. i could probably make a hole in one of the plastic headset spacers, but the wire will be exposed and coming out below the rotation of the bars.
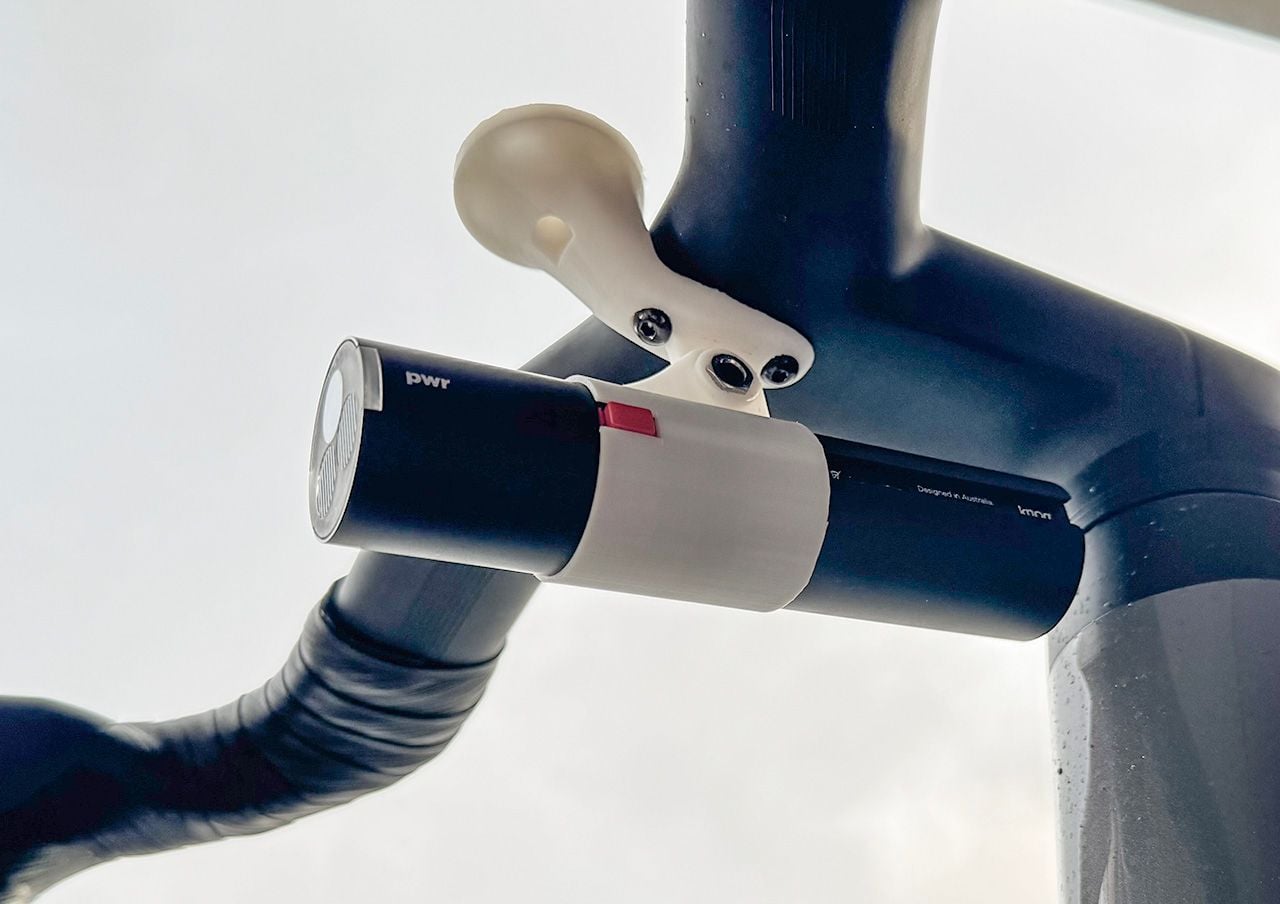
here is what a previously finished version of the sp-connect mount looks like on top, it's very clean.
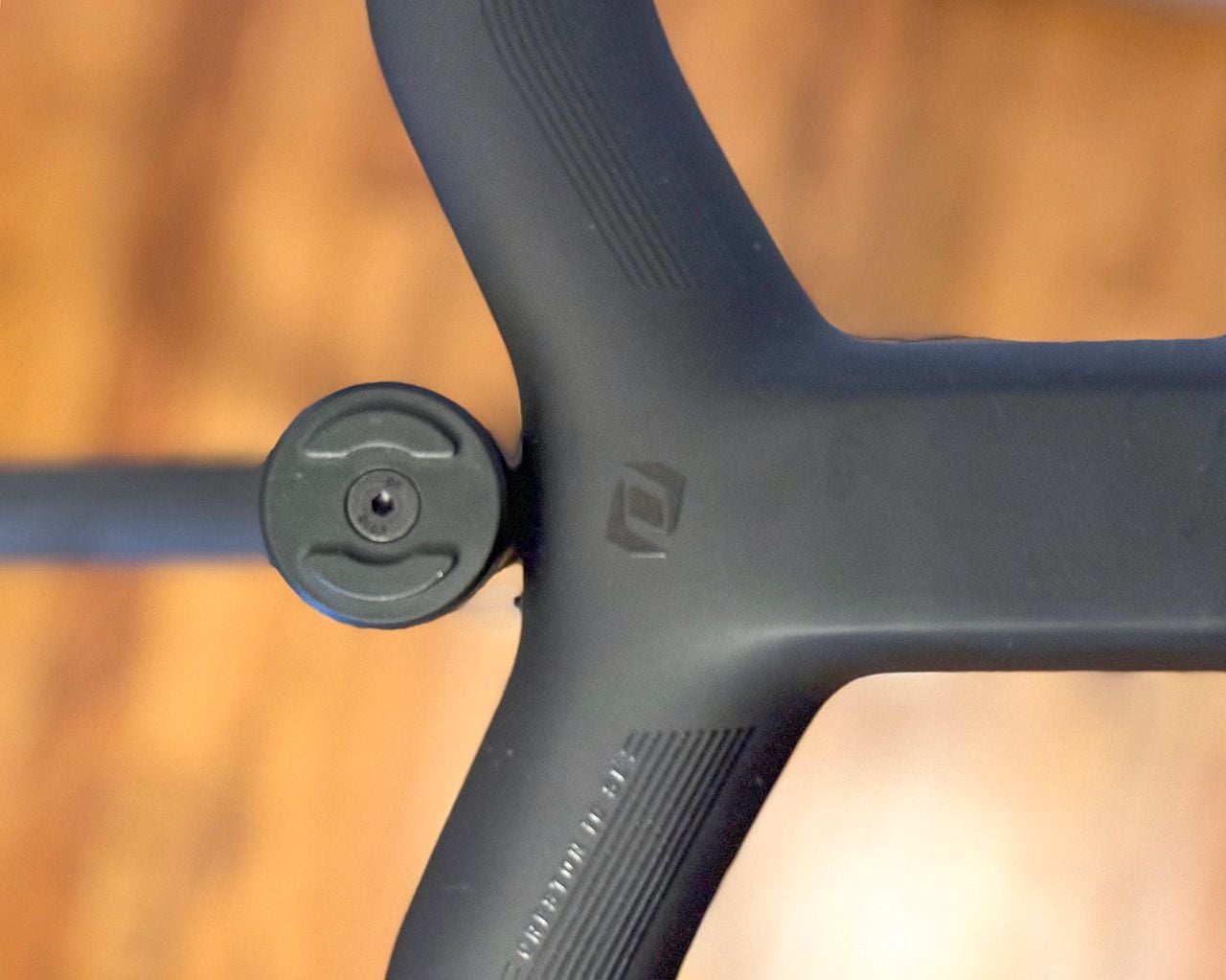
i'm leaning towards only using one of the bolts for the mechanical attachment, along with a complete layer of VHB tape on the mating surface. i'd hope the tape would remove any bending while the single bolt would be adequate for the "vertical" component of the load. and, of course, a light without a battery is a fraction of the weight.
a crazy alternative might be to electrify the bolts from the inside and embed some wiring channels inside the 3d print. not sure what the implications of power being present at the embeds and exposed bolt heads would be though. i can imagine with enough rain it might short across them.
here's a version of the attachment i made for a battery powered light - the white stuff is freshly 3d printed, it will be painted matte black. the bolt through the captured nut has a thumbscrew on the other side allowing the light to be easily removed for charging. but it's a pretty heavy light. would be way better to connect it to the bike's battery. obviously the part which the light slides into (which is an extremely tight fit, not going anywhere) would be made differently for a smaller wired light.
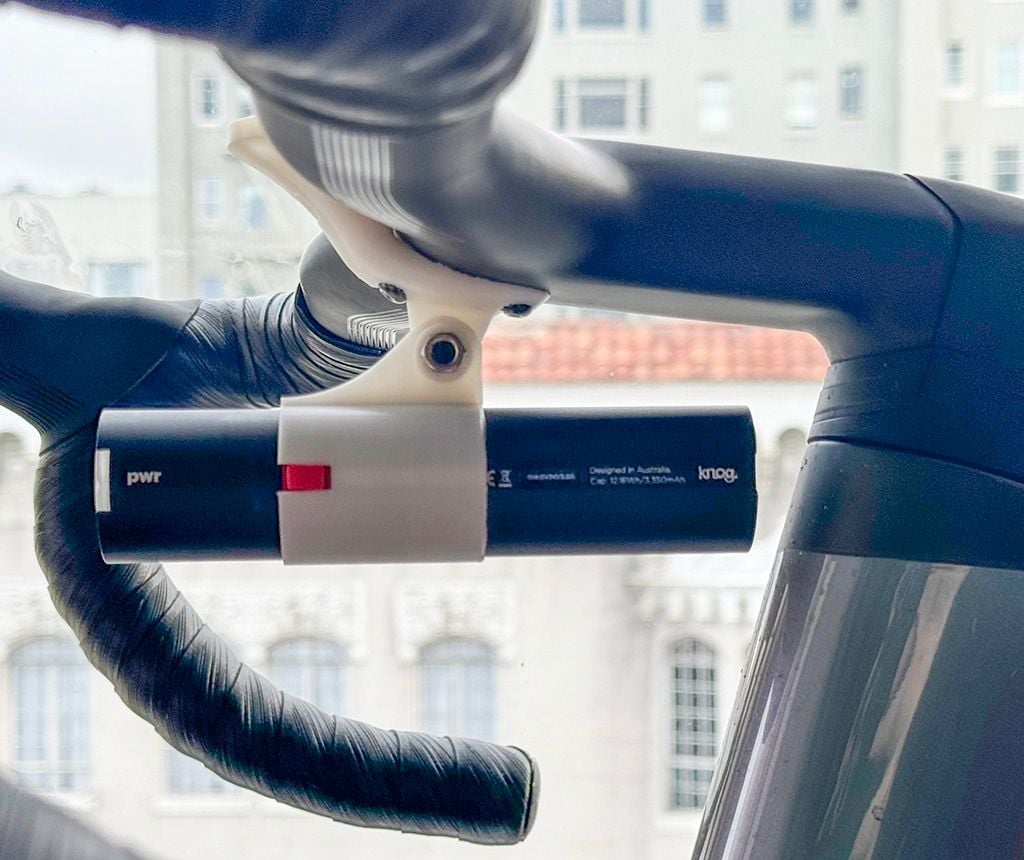
from below - the two black bolts are into the pair of embeds in the bar. there are no other holes. i could probably make a hole in one of the plastic headset spacers, but the wire will be exposed and coming out below the rotation of the bars.
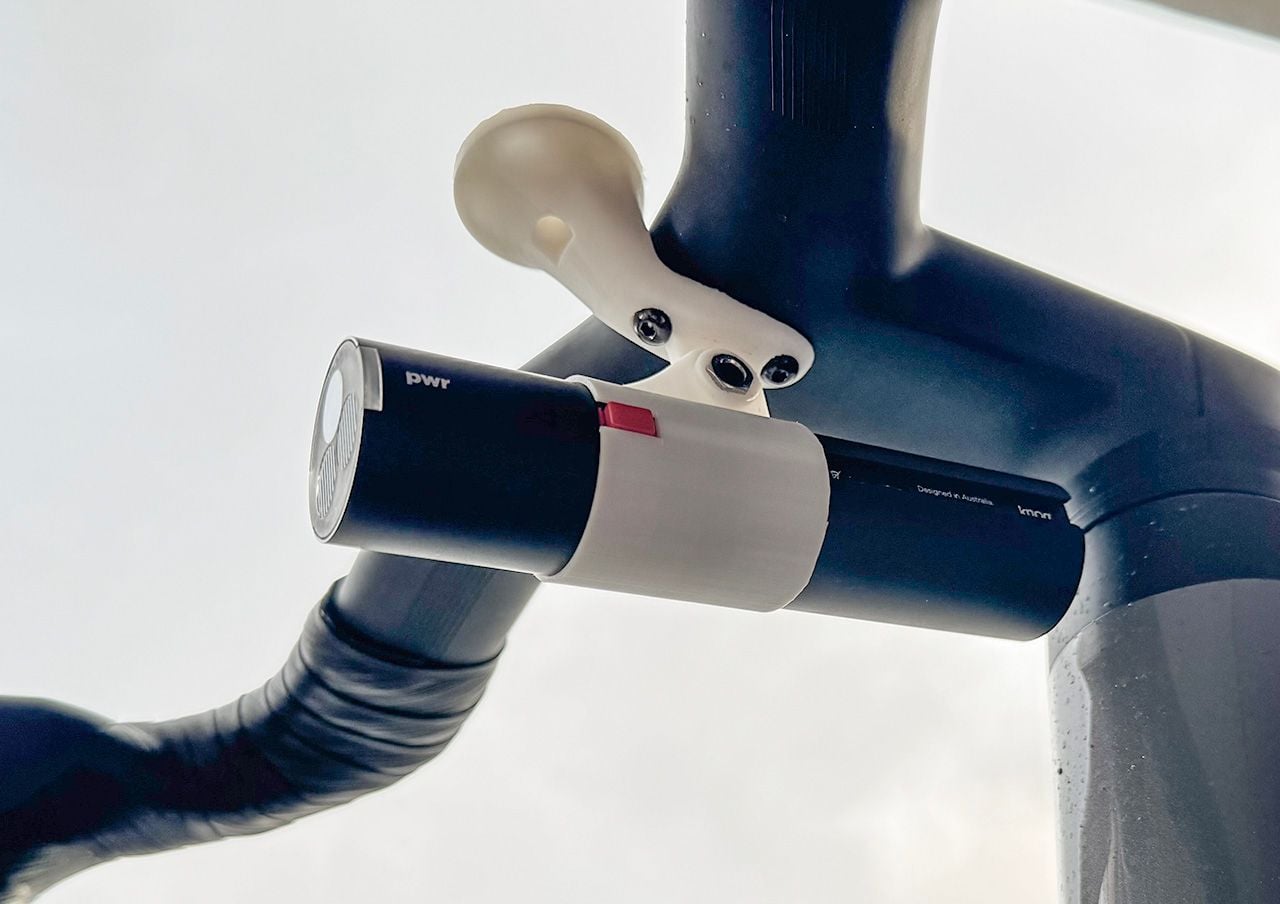
here is what a previously finished version of the sp-connect mount looks like on top, it's very clean.
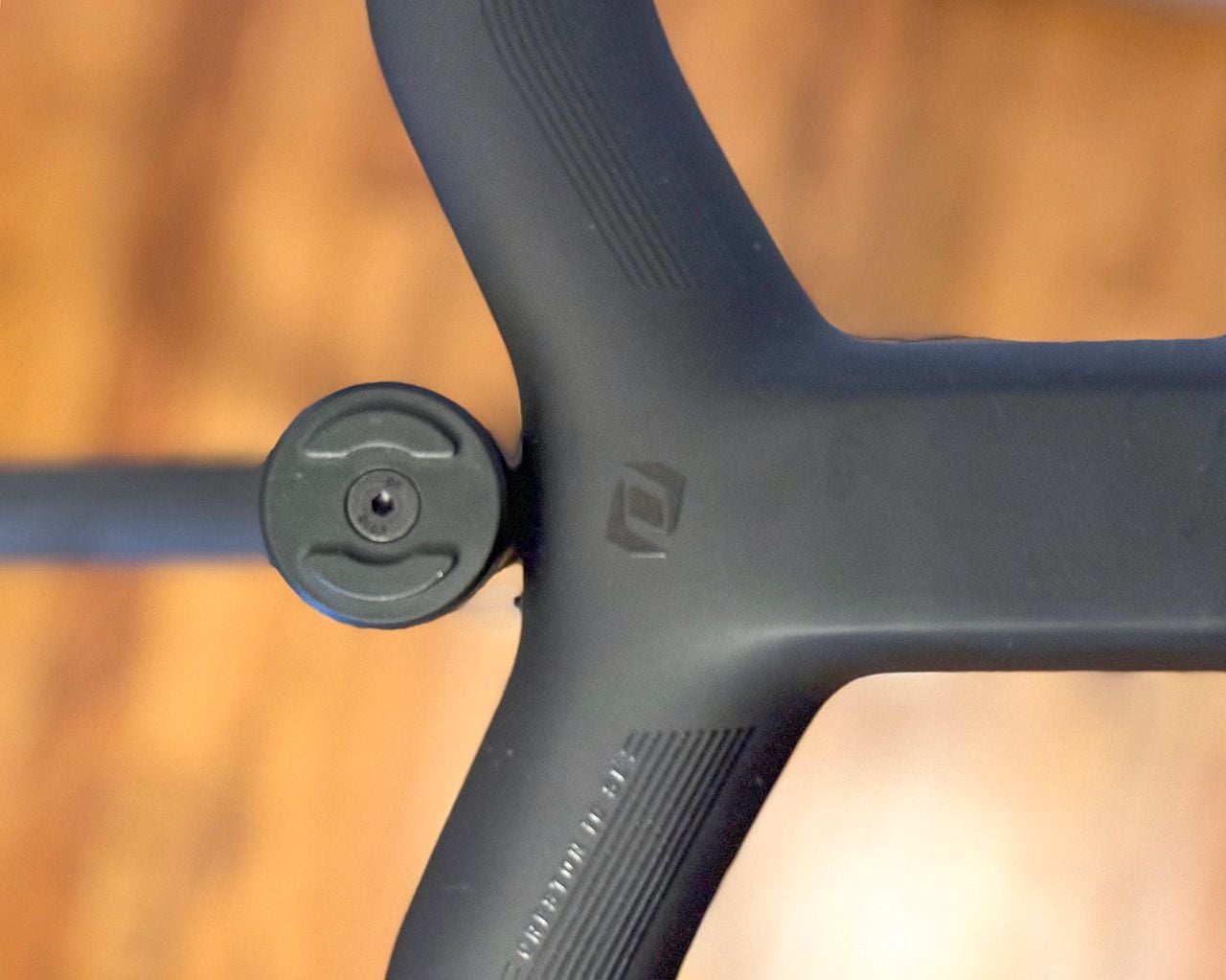
i'm leaning towards only using one of the bolts for the mechanical attachment, along with a complete layer of VHB tape on the mating surface. i'd hope the tape would remove any bending while the single bolt would be adequate for the "vertical" component of the load. and, of course, a light without a battery is a fraction of the weight.
a crazy alternative might be to electrify the bolts from the inside and embed some wiring channels inside the 3d print. not sure what the implications of power being present at the embeds and exposed bolt heads would be though. i can imagine with enough rain it might short across them.
#8
Senior Member
Thread Starter
Join Date: May 2021
Location: San Francisco
Posts: 2,039
Bikes: addict, aethos, creo, vanmoof, sirrus, public ...
Mentioned: 2 Post(s)
Tagged: 0 Thread(s)
Quoted: 1279 Post(s)
Liked 1,393 Times
in
711 Posts
What if you glue an aluminium plate to the carbon first and then drill through the whole lot in one go? The idea being that the glue will stop the hole chowdering up into splinters of death as you drill (although the back-side will still do that a bit probably). Obviously sand it down a bit first and make sure you get a good bond.
given the very low load involved i imagine i could use a very, very tiny wire through a very, very tiny hole.
Likes For mschwett: