Buying or making a unicrown fork for a new frame?
#1
Full Member
Thread Starter
Buying or making a unicrown fork for a new frame?
I just recently finished my first fillet brazed frame. I basically used my 2013 Ti Fargo as a model to make a bike packing bike for my son. Since this frame has thru-axles, I need to buy or make a fork. Finding one with the same fork offset and steerer tube angle has been a challenge. I have watched a Youtube on a fillet brazed unicrown fork for a gravel bike and it was beautiful, except for the half pound of brass the builder used to make it. I don't TIG weld, and carbon fiber is not an option. I found a fork that is close and wanted to ask the framebuilder community if they think it will work. The Kona Unit X has a fork that is 2mm longer.
Fork length Fork offset Head Tube Angle
Fargo 468mm 45mm 71 degrees
Unit X 470mm 50mm 69 degrees
My gut tell me it would be close enough, but I would hate putting something on this bike that makes it handle weird.
Thanks for your input!
Fork length Fork offset Head Tube Angle
Fargo 468mm 45mm 71 degrees
Unit X 470mm 50mm 69 degrees
My gut tell me it would be close enough, but I would hate putting something on this bike that makes it handle weird.
Thanks for your input!
Last edited by Gyro_T; 03-04-24 at 11:59 PM. Reason: align columns
#2
Senior Member
Join Date: Dec 2019
Posts: 956
Mentioned: 3 Post(s)
Tagged: 0 Thread(s)
Quoted: 321 Post(s)
Liked 263 Times
in
212 Posts
You could also consider making a segmented fork. These are quite fun to do and can be done with either TIG or fillet brazing. I use TIG and make the arms out of 1" cromoly steerer tube. The caps are just 1/16" mild steel sheet.
I weld the arms straight onto the steerer and TIG braze on a crown race seat which I make on my Chinese minilathe out of some black iron pipe. You can also buy crown race seat parts that braze onto the bottom of the steerer I believe.
I weld the arms straight onto the steerer and TIG braze on a crown race seat which I make on my Chinese minilathe out of some black iron pipe. You can also buy crown race seat parts that braze onto the bottom of the steerer I believe.
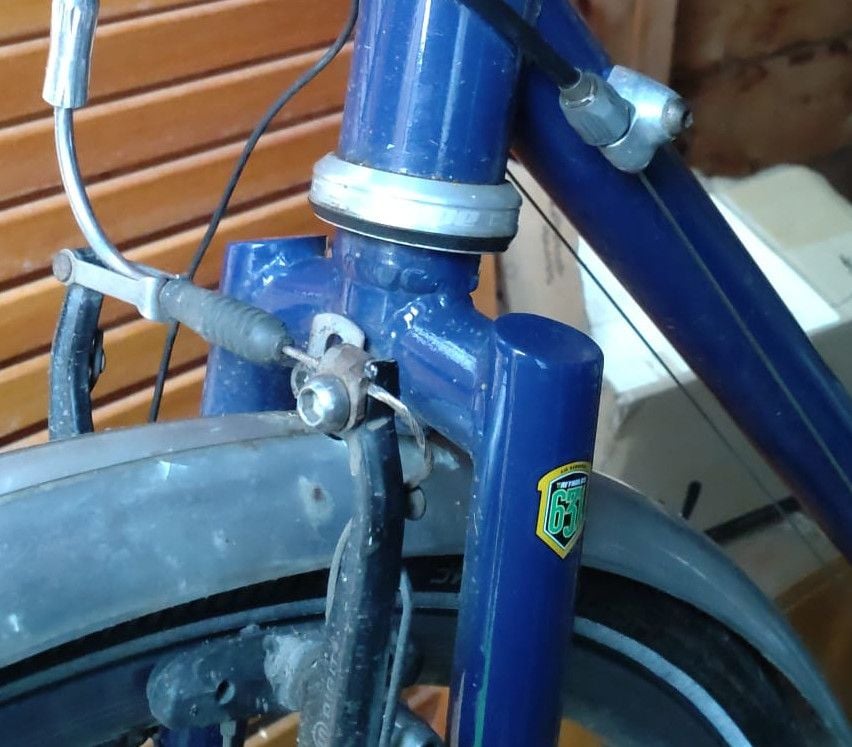
Likes For guy153:
#3
Senior Member
Join Date: Feb 2012
Location: Rochester, NY
Posts: 18,094
Bikes: Stewart S&S coupled sport tourer, Stewart Sunday light, Stewart Commuting, Stewart Touring, Co Motion Tandem, Stewart 3-Spd, Stewart Track, Fuji Finest, Mongoose Tomac ATB, GT Bravado ATB, JCP Folder, Stewart 650B ATB
Mentioned: 0 Post(s)
Tagged: 0 Thread(s)
Quoted: 4209 Post(s)
Liked 3,875 Times
in
2,315 Posts
First I ask what is meant by "steerer angle"? Do you mean head tube steering angle? If so the fork has nothing to do with that but that frame angle does locate the fork at that angle, to establish the steering geometry that the fork's specs do contribute to also.
2mm of A-C difference is pretty small a change for that spec. Here are two threads I created involving non traditional crown/fork making to offer some ideas. Andy
Unicycle Build - Bike Forums
A Long Time Coming - Bike Forums
2mm of A-C difference is pretty small a change for that spec. Here are two threads I created involving non traditional crown/fork making to offer some ideas. Andy
Unicycle Build - Bike Forums
A Long Time Coming - Bike Forums
__________________
AndrewRStewart
AndrewRStewart
Likes For Andrew R Stewart:
#4
Senior Member
Join Date: Feb 2012
Location: Rochester, NY
Posts: 18,094
Bikes: Stewart S&S coupled sport tourer, Stewart Sunday light, Stewart Commuting, Stewart Touring, Co Motion Tandem, Stewart 3-Spd, Stewart Track, Fuji Finest, Mongoose Tomac ATB, GT Bravado ATB, JCP Folder, Stewart 650B ATB
Mentioned: 0 Post(s)
Tagged: 0 Thread(s)
Quoted: 4209 Post(s)
Liked 3,875 Times
in
2,315 Posts
You could also consider making a segmented fork. These are quite fun to do and can be done with either TIG or fillet brazing. I use TIG and make the arms out of 1" cromoly steerer tube. The caps are just 1/16" mild steel sheet.
I weld the arms straight onto the steerer and TIG braze on a crown race seat which I make on my Chinese minilathe out of some black iron pipe. You can also buy crown race seat parts that braze onto the bottom of the steerer I believe.
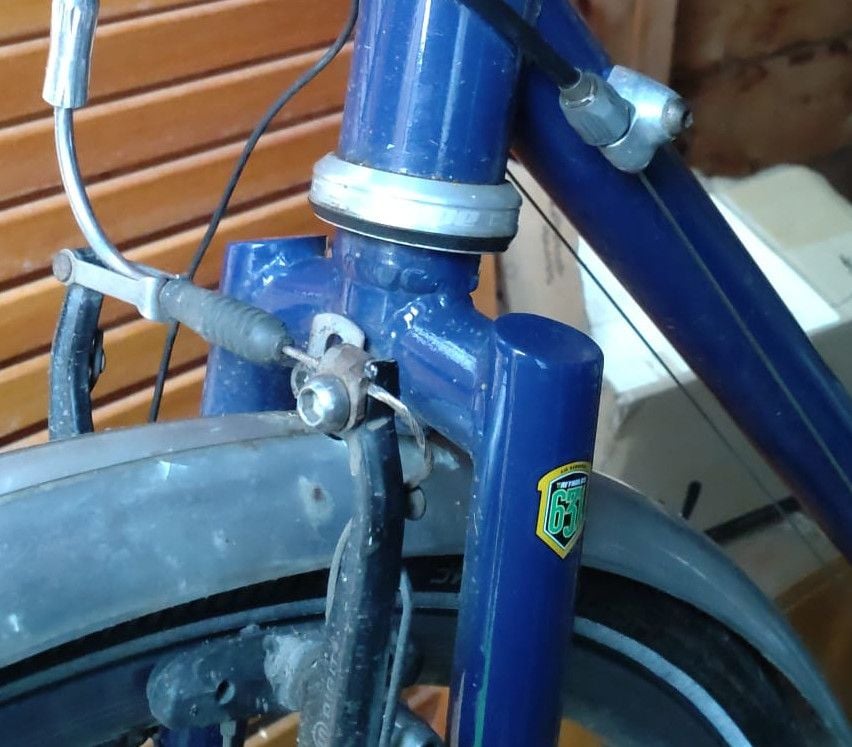
I weld the arms straight onto the steerer and TIG braze on a crown race seat which I make on my Chinese minilathe out of some black iron pipe. You can also buy crown race seat parts that braze onto the bottom of the steerer I believe.
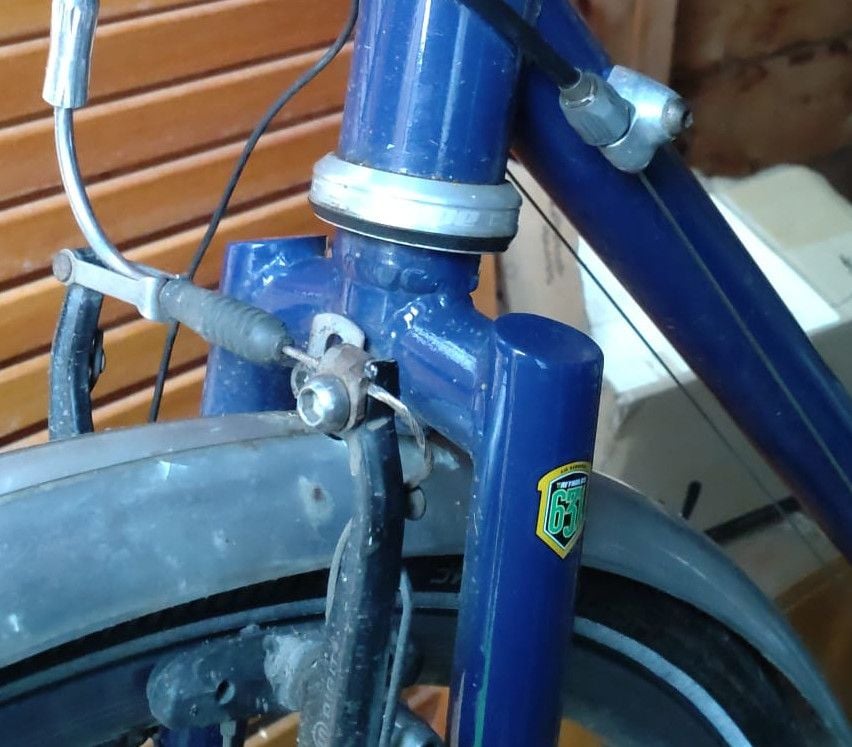
__________________
AndrewRStewart
AndrewRStewart
Likes For Andrew R Stewart:
#5
Full Member
Thread Starter
My "table" got scrambled when I posted. I just wanted to compare the two forks. The Unit X fork is 2mm longer with 5mm more offset. The HT angle is 3 degrees more slack angle than the Fargo fork. Thanks for those links!
Last edited by Gyro_T; 03-05-24 at 09:40 AM.
#6
Full Member
Thread Starter
That looks like something I might be able to do. From where do you get Reynolds 631 tubes?
#7
Senior Member
Join Date: Dec 2019
Posts: 956
Mentioned: 3 Post(s)
Tagged: 0 Thread(s)
Quoted: 321 Post(s)
Liked 263 Times
in
212 Posts
The legs are 1.0mm/0.6mm Reynolds EX5707, curved to a 45mm offset and they taper down to 13mm. Really nice. Actually a benefit of making segmented forks is you have much more choice of blades than if you make a unicrown.
The actual steerer is a 28.6mm Reynolds one, which is 1.6mm wall at the bottom end.
Likes For guy153:
#8
Senior Member
Join Date: Dec 2019
Posts: 956
Mentioned: 3 Post(s)
Tagged: 0 Thread(s)
Quoted: 321 Post(s)
Liked 263 Times
in
212 Posts
I get them directly from Reynolds being in the UK. These are the EX5707 blades (the most curved and the thinnest). Make sure that if you're using a disk brake you get the slightly thicker ones (EX5719, EX5720 or EX5730 depending on how much bend you want in them).
Likes For guy153:
#9
Full Member
Thread Starter
Fillet brazed unicrown
First I ask what is meant by "steerer angle"? Do you mean head tube steering angle? If so the fork has nothing to do with that but that frame angle does locate the fork at that angle, to establish the steering geometry that the fork's specs do contribute to also.
2mm of A-C difference is pretty small a change for that spec. Here are two threads I created involving non traditional crown/fork making to offer some ideas. Andy
Unicycle Build - Bike Forums
A Long Time Coming - Bike Forums
2mm of A-C difference is pretty small a change for that spec. Here are two threads I created involving non traditional crown/fork making to offer some ideas. Andy
Unicycle Build - Bike Forums
A Long Time Coming - Bike Forums
Mike
#10
Senior Member
Join Date: Feb 2012
Location: Rochester, NY
Posts: 18,094
Bikes: Stewart S&S coupled sport tourer, Stewart Sunday light, Stewart Commuting, Stewart Touring, Co Motion Tandem, Stewart 3-Spd, Stewart Track, Fuji Finest, Mongoose Tomac ATB, GT Bravado ATB, JCP Folder, Stewart 650B ATB
Mentioned: 0 Post(s)
Tagged: 0 Thread(s)
Quoted: 4209 Post(s)
Liked 3,875 Times
in
2,315 Posts
The 1" steerer used for the "arms" is a Columbus one that's 2.3mm at one end and 1.55mm at the other. I think I used pieces from the "thin" end (which is still quite thick). That one steerer has made 3 or 4 forks now.
The legs are 1.0mm/0.6mm Reynolds EX5707, curved to a 45mm offset and they taper down to 13mm. Really nice. Actually a benefit of making segmented forks is you have much more choice of blades than if you make a unicrown.
The actual steerer is a 28.6mm Reynolds one, which is 1.6mm wall at the bottom end.
The legs are 1.0mm/0.6mm Reynolds EX5707, curved to a 45mm offset and they taper down to 13mm. Really nice. Actually a benefit of making segmented forks is you have much more choice of blades than if you make a unicrown.
The actual steerer is a 28.6mm Reynolds one, which is 1.6mm wall at the bottom end.
__________________
AndrewRStewart
AndrewRStewart
Likes For Andrew R Stewart:
#11
Senior Member
Join Date: Feb 2012
Location: Rochester, NY
Posts: 18,094
Bikes: Stewart S&S coupled sport tourer, Stewart Sunday light, Stewart Commuting, Stewart Touring, Co Motion Tandem, Stewart 3-Spd, Stewart Track, Fuji Finest, Mongoose Tomac ATB, GT Bravado ATB, JCP Folder, Stewart 650B ATB
Mentioned: 0 Post(s)
Tagged: 0 Thread(s)
Quoted: 4209 Post(s)
Liked 3,875 Times
in
2,315 Posts
I read through and enjoyed the pictures and story of your "long time coming" build. I find beauty in steel and brass rod coming together like that! The amount of filler you used on the fork is much more conservative than what I saw on the Youtube channel. I guess I thought you needed that much for strength. My son weights about 190 and now that he is in his forties, rides a little more conservatively that he use to. I am rethinking building the fork myself and trying to reach a happy medium on the amount of rod I use. Thanks for sharing that.
Mike
Mike
__________________
AndrewRStewart
AndrewRStewart
#12
Senior Member
Join Date: Dec 2019
Posts: 956
Mentioned: 3 Post(s)
Tagged: 0 Thread(s)
Quoted: 321 Post(s)
Liked 263 Times
in
212 Posts
Thanks for following up. A bunch of years ago there were a few segmented fork failures that were posted and talked about on various forums. They have been referenced every so often since and it seems that inadequate wall thickness, vent holes, and heat management were part of the problems. Your "crown segments" are of significantly thicker wall that what I remember those failed forks had. Andy
#13
Randomhead
Join Date: Aug 2008
Location: Happy Valley, Pennsylvania
Posts: 24,399
Mentioned: 0 Post(s)
Tagged: 0 Thread(s)
Quoted: 4 Post(s)
Liked 3,699 Times
in
2,519 Posts
I think the failure of that fork Andy is talking about can be traced back to drilling vent holes on the outside diameter of the crown segment. Those crown segments see a lot of fatigue cycles. They really need to go inside, in the fork blade and steerer. Brave of the builder to post pics, I have to say. People speculate about builder skill when something fails, based on zero information.
I was going to disagree about the thickness of stem extensions, then I converted the thickness I use into metric and realized it was 1.6mm. Using barleycorns as a basis for a measuring system is a harsh mistress.
I was going to disagree about the thickness of stem extensions, then I converted the thickness I use into metric and realized it was 1.6mm. Using barleycorns as a basis for a measuring system is a harsh mistress.
#14
Senior Member
Join Date: Dec 2019
Posts: 956
Mentioned: 3 Post(s)
Tagged: 0 Thread(s)
Quoted: 321 Post(s)
Liked 263 Times
in
212 Posts
I think the failure of that fork Andy is talking about can be traced back to drilling vent holes on the outside diameter of the crown segment. Those crown segments see a lot of fatigue cycles. They really need to go inside, in the fork blade and steerer. Brave of the builder to post pics, I have to say. People speculate about builder skill when something fails, based on zero information.
I was going to disagree about the thickness of stem extensions, then I converted the thickness I use into metric and realized it was 1.6mm. Using barleycorns as a basis for a measuring system is a harsh mistress.
I was going to disagree about the thickness of stem extensions, then I converted the thickness I use into metric and realized it was 1.6mm. Using barleycorns as a basis for a measuring system is a harsh mistress.
I also weld a cap on the bottom of the steerer (usually using metal only 0.11 barleycorns thick) just to keep mud and grime out and I sometimes drill a hole in that to let any water drain out that might have found its way into the steerer tube somehow.
#15
Full Member
Thread Starter
I ordered the Reynolds EX5720 fork blades from Torch and File in Portland, OR. I happen to have an old 531 steerer that I will use for the arms to make a segmented fork. I have been using Gasflux C-04 nickel bronze for my frame, not sure if that is the best possible choice for the fork. I did notice that the tensile strength of that rod is not as high as the rod Torch and File sells (65,000 psi vs 95,000). The brand they sell is Welco No. 17. The only filler rod I have experience with is generic LFB and the Gasflux. In my experience the Gasflux C-04 is a lot more forgiving than the generic LFB as far as getting nice looking fillets. I think that old Reynolds steerer is about one full barleycorn think!
Likes For Gyro_T:
#16
Senior Member
Join Date: Feb 2012
Location: Rochester, NY
Posts: 18,094
Bikes: Stewart S&S coupled sport tourer, Stewart Sunday light, Stewart Commuting, Stewart Touring, Co Motion Tandem, Stewart 3-Spd, Stewart Track, Fuji Finest, Mongoose Tomac ATB, GT Bravado ATB, JCP Folder, Stewart 650B ATB
Mentioned: 0 Post(s)
Tagged: 0 Thread(s)
Quoted: 4209 Post(s)
Liked 3,875 Times
in
2,315 Posts
I strongly suggest you use a filler that your are comfortable with. A well brazed joint that's not done cold, or not overheated and not taking too long to do (time at temp) is more than strong enough with CO4. Andy
__________________
AndrewRStewart
AndrewRStewart
Likes For Andrew R Stewart:
#17
Randomhead
Join Date: Aug 2008
Location: Happy Valley, Pennsylvania
Posts: 24,399
Mentioned: 0 Post(s)
Tagged: 0 Thread(s)
Quoted: 4 Post(s)
Liked 3,699 Times
in
2,519 Posts
I'm a bit surprised there is that much variation in strength between fillers. Spec sheet I see says, "up to 95000," maybe gasflux uses a nominal strength.
#18
Full Member
Thread Starter
filler
I learned that the Welco no. 17 was used for sweating lugs, not fillets! I guess that explains the difference.
Mike
Mike