Originally Posted by
tulsarob
I hope the 7075 will make the difference.
7075 is notable for its high strength-to-weight ratio and improved strength over 6061. Because of this, 7075 is largely used in aerospace, marine and transportation industries. Any industry where high strength and light weight properties are critical, this alloy is preferred. High-end bicycle components, molds for the plastics and tool industries, airframes, and even military-grade rifle receivers all heavily utilize 7075.
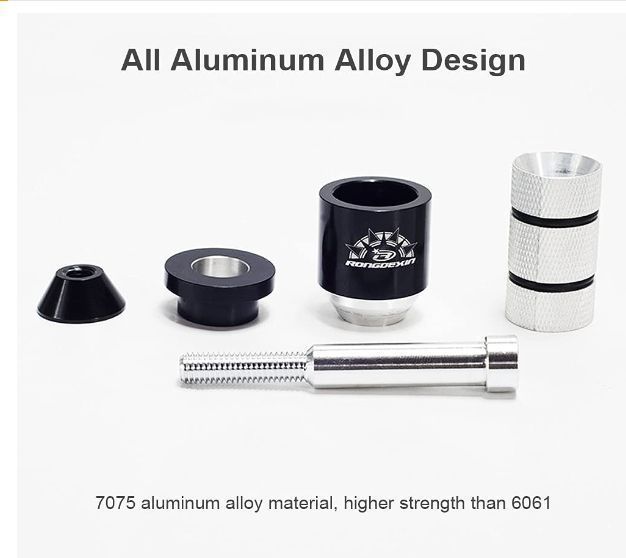
Ok, I'm not liking this design any more. You want a setup that will be strong and rigid. Strength and rigidity are based upon mechanical design and material of construction. This design essentially has what amounts to a spherical bearing (yes, its a cone and cup, but the cone length is very small compared to diameter). This means that the bolt itself is what resists most of of the bending force. The weakness is that the bolt has a significantly smaller diameter than the tube. Furthermore, this is likely a part made in a country with a wide range of quality control and ethical commitment to safe design. If this was 1950s USA and you be certain you were getting a super high quality (e.g. AN) bolt, and you carefully torqued the bolt properly, perhaps you could have some semblance of trust that this setup would not fail catastrophically. As in the bolt not snapping or stretching so much you lose purchase on the steer tube. But bolts come from heavens knows where these days. Some are great. Some have the stiffness of manchego cheese, the ductility of porcelain, and the stiffness of a pool noodle. The point is, it's the bolt's strengh and stiffness that dominates the failure mode. Six vs seven thousand series has pretty much nil effect on the overall joint strength and performance.
My original conception of your design was that your stem was going to go onto the actual steerer, and that the extender would only provide a little bit of length, just enough to provide some bending stiffness while preventing the stem clamp from "closing on air". But you've added a stem extender (AND high rise bars!), which will increase manyfold the bending moment on that poor bolt! The design creates essentiallly a stress riser, and the extender and high bars amplify the forces that riding will apply to that bolt.
The failure modes are not attractive. Snapping of the bolt means that the bars are connected to the bike by brake cables. Another failure mode is that if the bold stretches the joint loosens and the top part has no torsional communication with the bottom. You'd have handlebars, but they wouldn't steer anything!
The video created by the Chinese(?) fella had the best idea. I liked that video. If it were me (engineer who grew up working in a machine shop and then worked on and off for seven years in a bike shop) I'd get a tube extender that has a solid design (no joints) and that has a swaged smaller diameter section that inserts into your steerer tube, like in the video. That smooth transition from smaller to larger diameter is probably better than a machined design with a sharp shoulder. I'd buy a couple different ones and choose the one with minimal clearance/ightest fit. I'd actually use epoxy to glue the extender into the steerer, and would also tighten the wedge that came with the design (with the clever idea of using an oversize nut for the stop - see the video and dry fit before using epoxy). This is a permanent mod. Once set, sand off any glue that is proud of the setup and woiuld install the stem directly on the extension, not on an extension of the extension.
As a further precaution (I'm a big guy) I'd actually add an external brace. They sell tube clamps for automotive roll bars (pic below). There's pretty ugly and I don't see 1-1/8 inch offerings. Then I was looking for a bike specific product of a 1-1/8 inch clamp made of alloy and couldn't find it. So what I would do is buy a cheap stem of promising design off ebay and would saw it and file it to just leave a 1-1/8 clamp of, say 1.5 inches length. I'd clamp that over the joint between your steerer and extender. In fact, I see an advantage of this functionally: You could adjust the reinforcing clamp for preload, tighten the lower clamp, and then your handlebar stem adjustment and centering could be done without worrying about messing up the preload.
But the critical thing is that I would not ride a design that did not have the tube extender inserted into the steerer, with the stem clamped to the extender. The design shown above has a flaw in that it has all bending moment on the bolt. And 7075 won't help that problem.