Looks like you made a good choice. A liitle more info: Not only is that slotted aluminum very pricey, it also does not assemble in a very rigid manner, lots of the connectors are single screw and can rotate. Great for prototyping when you need flexibility, not the way I would go for final product - price or rigidity
Originally Posted by
tegnamo
My trailer search has come to an end it seems.
I considered:
- Buying a welder and welding my own. Not in the cards for a few reasons right now.
- Buying tubing and lots of screws and bolts. I just felt like it would be a little fiddly and I'd be chasing loose joints. At least for the size I wanted to build it didn't seem practical.
- Buying a Bikes at Work trailer. But their lead times are 6 months unless you tack on $240 for rush and then it's still not for another month or so.
- Following the lead of this cyclist from Boston. He bought an aluminum cargo basket that goes into a car hitch and then bought some BaW parts and made a trailer. The basket is only $150 or so! That's pretty crazy. I didn't want a "basket" style so much, however. I want a sturdy flat deck. Maybe coulda made it work, but didn't go this way regardless.
- Making one from t-slot (80/20) extrusion. I spent quite a few hours playing with the 80/20 catalog in Solidworks and seeing what I could come up with. I think my design is sturdy enough, and if you have the cash it's actually a pretty easy assembly process with no fab required I think. I also like that you can make adjustments to the components. So if you wanted to slide the axle forward or back, you just loosen the t-nuts and do it. You could even set it up where the whole trailer body could be widened or narrowed on the fly. Bikes at Work sells the axle, wheels, and hitch, and then you just need to create the main frame. Unfortunately after all was said and done, I had a trailer that cost between $1300 and $1400 at a minimum. A bit rich for me. But it was a fun exercise! Here's what I came up with before I realized it was a bit too expensive.
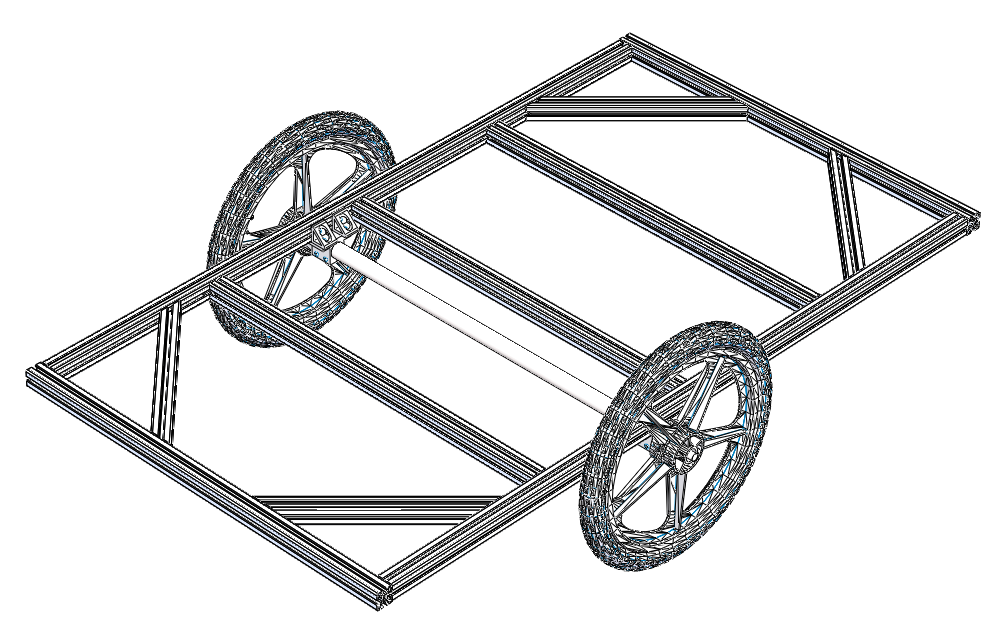
I used the lightest 1.5" extrusion and tried to not go overboard. If I had my own little machine shop I could have made some of the more costly aluminum parts I'd buy from 8020's catalog. They charge a fortune for little bits of aluminum. The extrusions aren't actually that expensive for what they are. $270 for all of the extrusion cut to length at the factory. But BaW's parts contribute a significant cost as well.
Okay, so what did I actually do? I
eventually decided to buy the very last Surly Bill trailer from QBP! I definitely appreciate the steel construction and it seems quite nice although I haven't received it yet. I may have gone with a BaW trailer if their lead times were not so long. Alas, I couldn't convince myself to wait. It's more narrow than I'd like but I can build around it I think. I just have to be careful that I don't create something too tall and tippy because the trailer is only 2 feet wide! I bet...given some more time investment, I could widen the axle and get an extra 6 inches on each side. The axles are a cool quill-stem design which means you can just pop them out. Would actually be a nice axle to DIY a trailer with.
One thing that will be interesting is how I hitch it to my Tern. I wound up buying the Big Dummy hitch because the other one wasn't in stock. I think I can ditch the long bar and just connect the joint to my Burley hitch which is bolted to the side of the Tern. We'll see...