Adding electric
#1
Junior Member
Thread Starter
Join Date: Aug 2014
Posts: 9
Mentioned: 0 Post(s)
Tagged: 0 Thread(s)
Quoted: 2 Post(s)
Likes: 0
Liked 0 Times
in
0 Posts
Adding electric
We have an older Trek T100 tandem and are considering adding electric assist to it. I am wondering if anyone has any experience with and if so, what company you went with. Thanks for the input.
#2
Senior Member
Join Date: Feb 2007
Posts: 1,440
Mentioned: 5 Post(s)
Tagged: 0 Thread(s)
Quoted: 625 Post(s)
Likes: 0
Liked 397 Times
in
275 Posts
I am currently waiting on funds for making my bicycle an ebike. I am picky and don't want it to be noisy. Another criteria is not having to make major mods to the bicycle frame. There are mid drives in various power configurations. They are almost always noisy. There are direct drive hub motors that aren't noisy and Geared hub motors that are and not noisy. Dependability is a big factor for me so I have chosen a direct drive hub motor. Direct drive hub motors allow regen. It is not very much regen but enough to act as a drag brake on a grade. If you go this route you need to make sure the setup you purchase has this feature. Good fitment to the bicycle is important to me. I can only use a front hub motor. Your tandem can use A front or rear hub motor. I am going to purchase from Grin because of quality and well thought design of there products. Check out All Axle Hub Motor and If you don't mind the noise a collaboration between Bafang Grin and an American company called the GMAC Motor. the All Axle Hub Motor is a front only motor and works with a regular quick release or 5 different thru axle types and specialty one sided setups on trikes. The GMAC is a powerful geared motor that also has powerful regen. It uses a solid round 10mm axle.
#3
Senior Member
Join Date: Feb 2005
Location: SW Florida
Posts: 1,673
Bikes: '06 Bianchi Pista; '57 Maclean; '10 Scott CR1 Pro; 2005 Trek 2000 Tandem; '09 Comotion Macchiato Tandem; 199? Novara Road; '17 Circe Helios e-tandem:1994 Trek 2300
Mentioned: 5 Post(s)
Tagged: 0 Thread(s)
Quoted: 147 Post(s)
Liked 93 Times
in
61 Posts
Search “We’ve “electrified” our Macchiato” on this forum.
#4
Full Member
I recently electrified our old Santana. I designed the system entirely opting for throttle control only and no central computer. Additionally, I went all in by building the wheel myself as well. I too went with Grin as they have great tools and support to help you design your system and they expect that most of their customers are capable of doing anything from an install through full design. I had never ridden ebike until this one so I was not sure if I was choosing the right mix of things, however, I do think I got it mostly right. I designed and 3D printed a mounting method for the throttle that works well for me with drop bars and I designed (and 3D printed) a basic display unit and throttle control circuit that displays voltage, Throttle voltage, and motor temperature. (Its not pretty, it's a pathfinder as I learn. I have longer term goal of designing in an Arduino controller with display).
Whether you "roll your own" as I did, or go with a pre-configured kit, there are a few things to keep in mind:
-Motor power is defined in watts and a higher the wattage rating does not necessarily mean a more "powerful" motor. You need to look at the torque or thrust force ratings of the motor for what you would think of as "power" and look at the motors power wattage rating as in how much thermal power can the motor dissipate before burning up. A 250W and a 1500W motor may likely give the same torque to accelerate you and pull up a hill, but the 250W motor will overheat and potentially burn up in a few minutes of heavy load where as the 1500W motor will survive longer. Even you are not going to roll your own, spend some time studying about this as well as how battery voltage, charge capacity and max current affect your overall system performance. It's not too difficult once you grasp the basics. Grin will help you with questions and their support is very good.
-Another thing to keep in mind: These solutions are HEAVY, it added over 20lbs to the bike which makes it hard to pedal without power and hard to transport due to the weight of the bike and there are not many options for quick release hub motors so the wheel may stay on (Ours stays on).
-If you go for a powerful system to pull you up the hills, you will have to pedal all that weight around when not climbing making it likely you will use motor assistance so you need more battery. (mo battery, mo weight)
-If you go for light weight to help with climbing, you will quickly run into the thermal issue above.
-Mid drives appear to be a good compromise, however, finding a setup that supports a tandem drive-train may limit your options, and the amount of torque and force on the drive train will lead you to heavier duty chains and hubs as well as potentially more drive train break downs.
-Pay attention to the need for a torque arm with hub motors. Until I get much for familiar with my set up, I am not going to risk it on a carbon fork.
-Finally, its a lot of fun.
I plan on writing are more detailed description of my system with some analysis of how I made the trade-offs, but that will be for another day.
A few pics of Sparky, the eTandem.
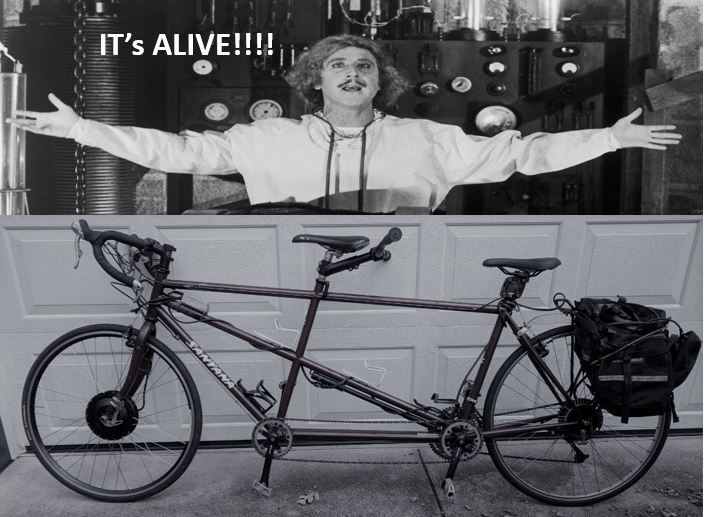
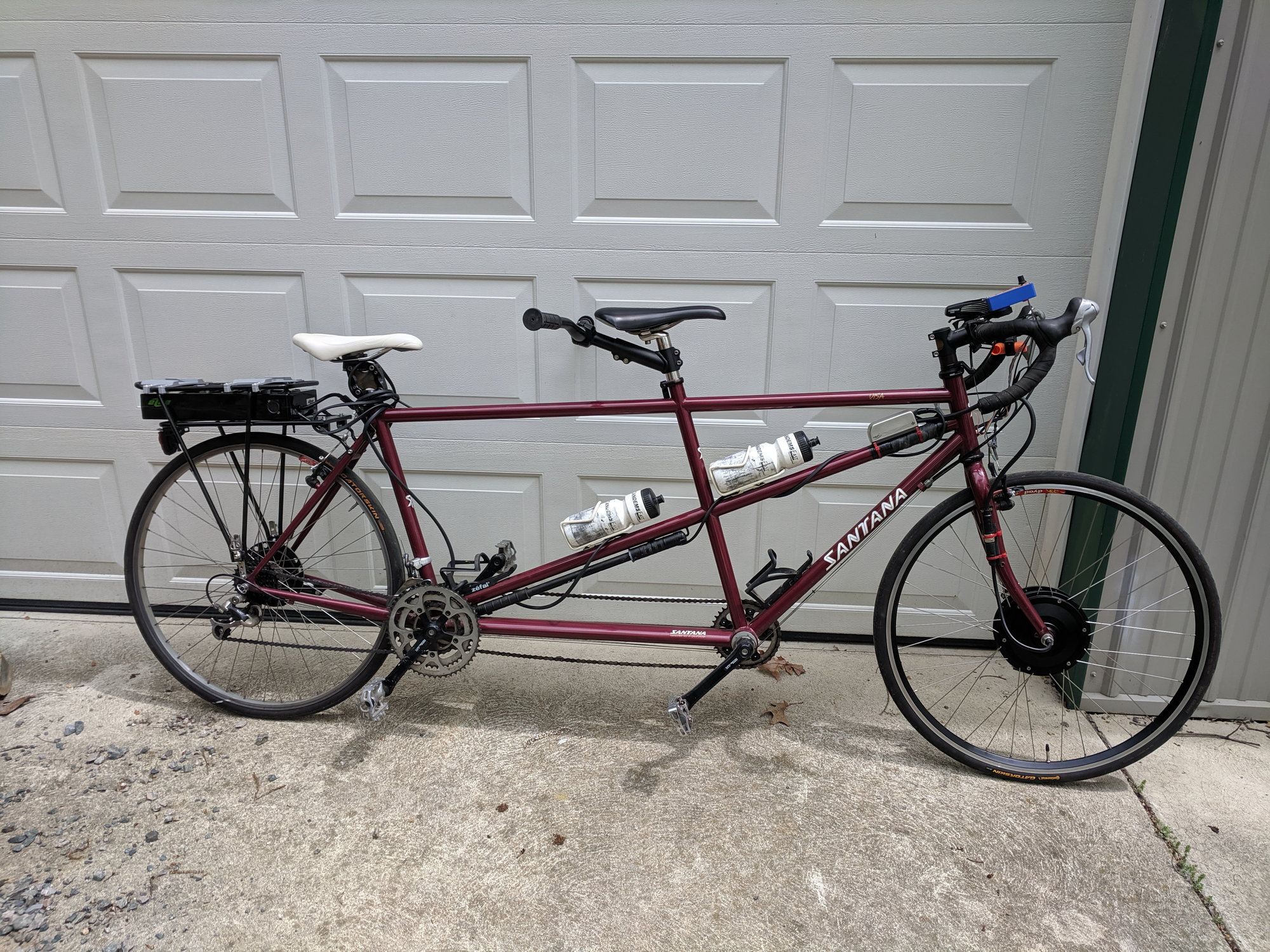
Whether you "roll your own" as I did, or go with a pre-configured kit, there are a few things to keep in mind:
-Motor power is defined in watts and a higher the wattage rating does not necessarily mean a more "powerful" motor. You need to look at the torque or thrust force ratings of the motor for what you would think of as "power" and look at the motors power wattage rating as in how much thermal power can the motor dissipate before burning up. A 250W and a 1500W motor may likely give the same torque to accelerate you and pull up a hill, but the 250W motor will overheat and potentially burn up in a few minutes of heavy load where as the 1500W motor will survive longer. Even you are not going to roll your own, spend some time studying about this as well as how battery voltage, charge capacity and max current affect your overall system performance. It's not too difficult once you grasp the basics. Grin will help you with questions and their support is very good.
-Another thing to keep in mind: These solutions are HEAVY, it added over 20lbs to the bike which makes it hard to pedal without power and hard to transport due to the weight of the bike and there are not many options for quick release hub motors so the wheel may stay on (Ours stays on).
-If you go for a powerful system to pull you up the hills, you will have to pedal all that weight around when not climbing making it likely you will use motor assistance so you need more battery. (mo battery, mo weight)
-If you go for light weight to help with climbing, you will quickly run into the thermal issue above.
-Mid drives appear to be a good compromise, however, finding a setup that supports a tandem drive-train may limit your options, and the amount of torque and force on the drive train will lead you to heavier duty chains and hubs as well as potentially more drive train break downs.
-Pay attention to the need for a torque arm with hub motors. Until I get much for familiar with my set up, I am not going to risk it on a carbon fork.
-Finally, its a lot of fun.
I plan on writing are more detailed description of my system with some analysis of how I made the trade-offs, but that will be for another day.
A few pics of Sparky, the eTandem.
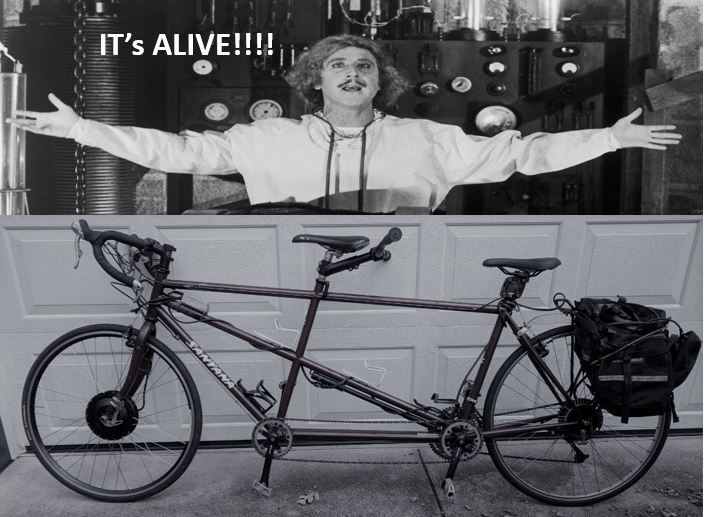
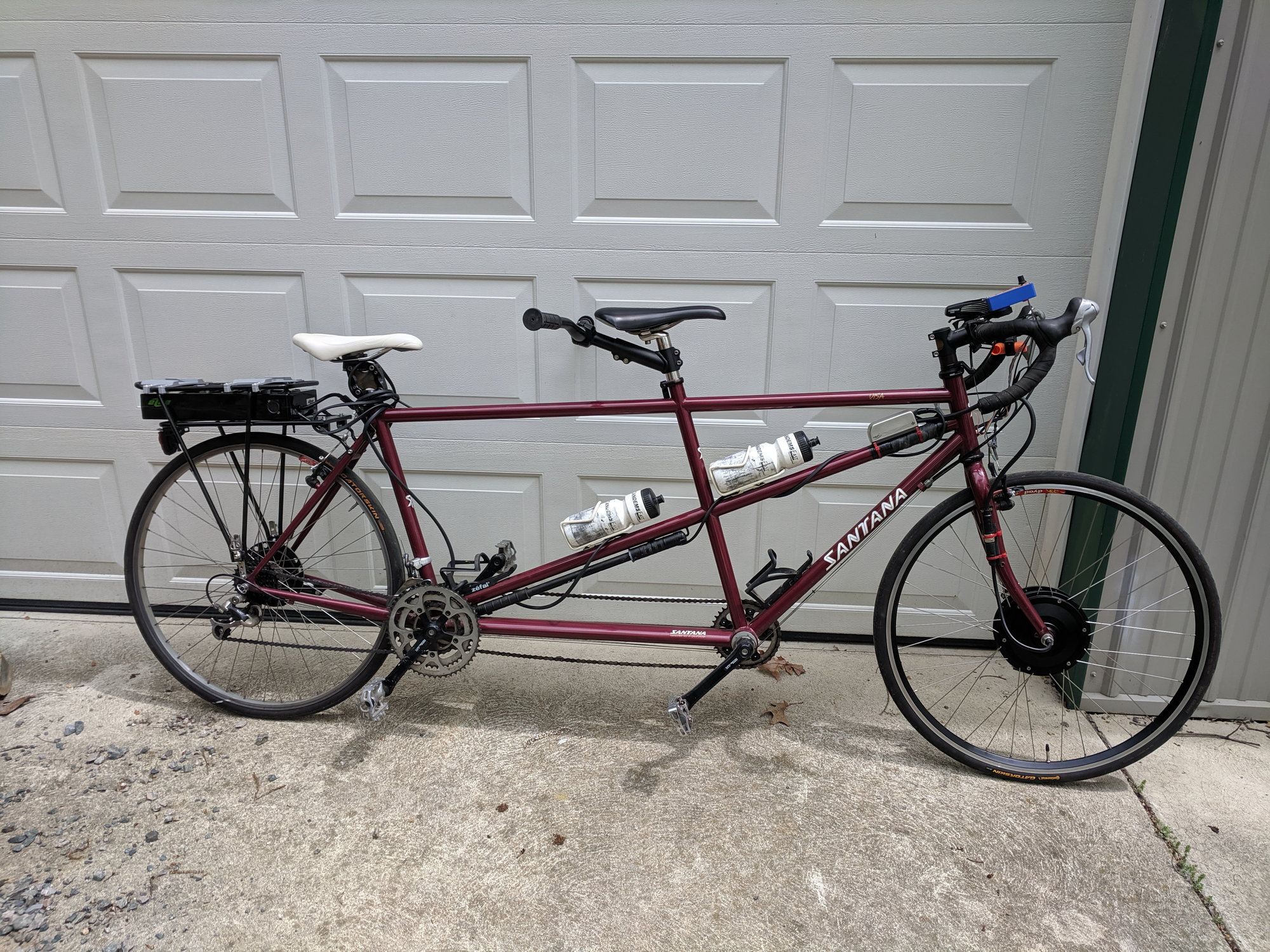
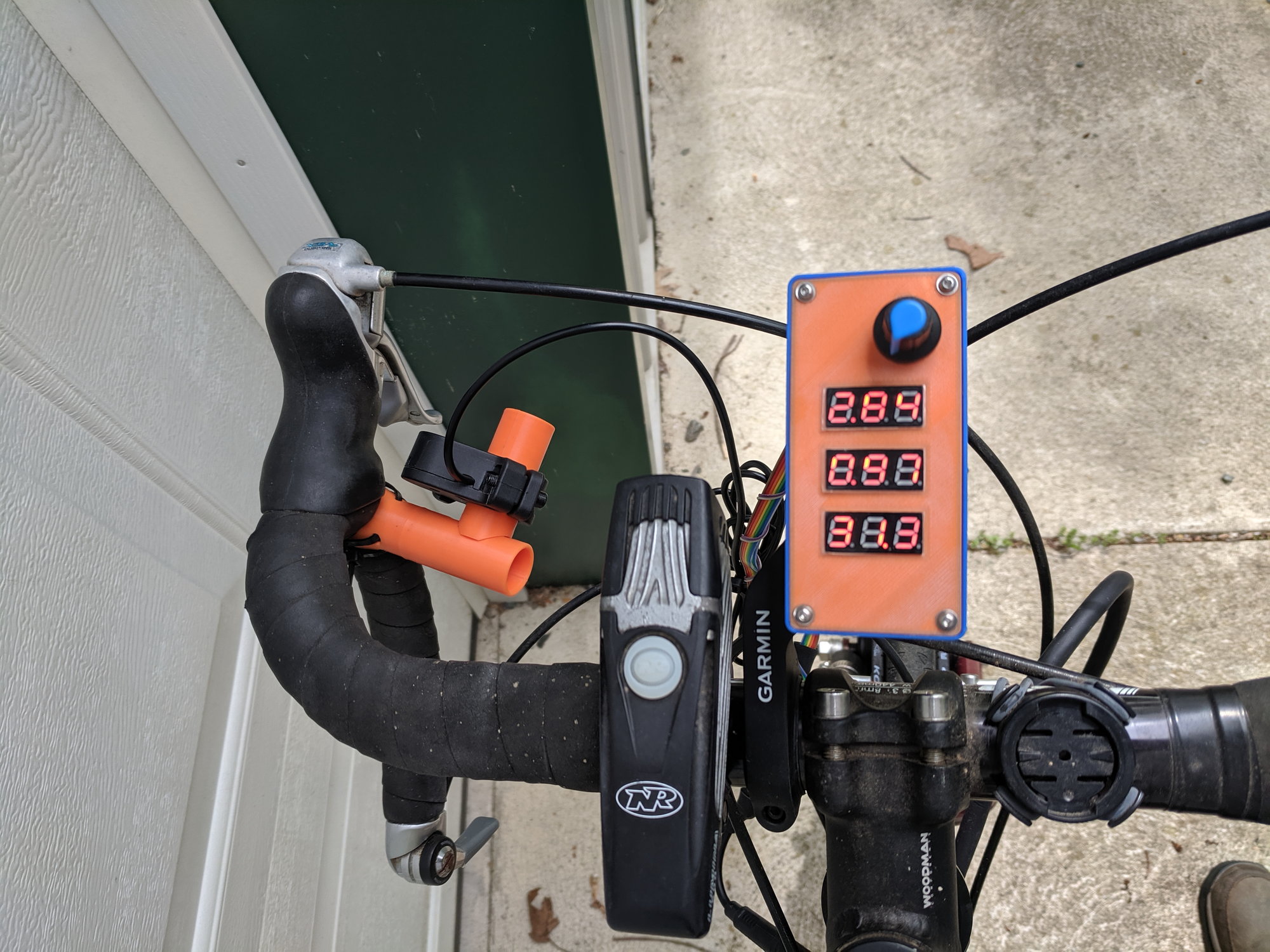
#5
Senior Member
Join Date: Feb 2007
Posts: 1,440
Mentioned: 5 Post(s)
Tagged: 0 Thread(s)
Quoted: 625 Post(s)
Likes: 0
Liked 397 Times
in
275 Posts
Looks like you have the EZEE geared hub motor on it. That would be a good choice for my 1990 Burley bongo. I am going to electrify my Co-Motion Pangea Rohloff, a 26" wheeled belt driven single with a 14 speed IGH. As I already posted I like the Grin All axle Hub Motor I of course intend to use Statorade and a HubSinkto help it stay cool.
#6
alpine cross trainer
Join Date: Mar 2010
Location: Central New York
Posts: 289
Bikes: Specialized Roubaix, Quintara Roo Sendoza, DaVici In-2-Ition Tandem,
Mentioned: 0 Post(s)
Tagged: 0 Thread(s)
Quoted: 21 Post(s)
Likes: 0
Liked 20 Times
in
8 Posts
I've posted this many times before. I've got a da Vinci Designs In-2-ition Road Tandem. Due to illness and old age, I added a electric motor to my tandem. It totally changed our riding enjoyment. Would recommend it to anyone that's struggling!
To keep it simple, I added a 26" wheel with a MAC geared front hub motor. It's 500 watts with a 48 volt battery. I specified a " high winding" motor. Advantages to the high winding motor is increased torque but at the expense of top speed. Great compromise for a tandem. It's throttle only setup, has three power setting along with cruise control. We live in very hilly countryside, so our riding is, motor assist over the hills and no motor assist for the flats. Works great for us.
Going with a front hub motor means we don't have to touch the the great daVinci drive train, leaving me with a very wide range of gears. When going up very steep hills, the very low gear on the tandem and the power of the Hub motor let's us comfortably peddle over every hill we've encountered. We never let the motor pull us over the hills. We peddle within our limits and try to keep the strain off the motor as much as possible. Have never had the motor get hot which bodes well for motor longevity.
Sometimes KISS method is the best, and the tandem can easily revert back to a standard bike.
To keep it simple, I added a 26" wheel with a MAC geared front hub motor. It's 500 watts with a 48 volt battery. I specified a " high winding" motor. Advantages to the high winding motor is increased torque but at the expense of top speed. Great compromise for a tandem. It's throttle only setup, has three power setting along with cruise control. We live in very hilly countryside, so our riding is, motor assist over the hills and no motor assist for the flats. Works great for us.
Going with a front hub motor means we don't have to touch the the great daVinci drive train, leaving me with a very wide range of gears. When going up very steep hills, the very low gear on the tandem and the power of the Hub motor let's us comfortably peddle over every hill we've encountered. We never let the motor pull us over the hills. We peddle within our limits and try to keep the strain off the motor as much as possible. Have never had the motor get hot which bodes well for motor longevity.
Sometimes KISS method is the best, and the tandem can easily revert back to a standard bike.
#7
Senior Member
Join Date: Feb 2007
Posts: 1,440
Mentioned: 5 Post(s)
Tagged: 0 Thread(s)
Quoted: 625 Post(s)
Likes: 0
Liked 397 Times
in
275 Posts
Going with a front hub motor means we don't have to touch the the great daVinci drive train, leaving me with a very wide range of gears. When going up very steep hills, the very low gear on the tandem and the power of the Hub motor let's us comfortably peddle over every hill we've encountered. We never let the motor pull us over the hills. We peddle within our limits and try to keep the strain off the motor as much as possible. Have never had the motor get hot which bodes well for motor longevity.
#8
Senior Member
Join Date: Apr 2005
Location: Northern CA
Posts: 743
Bikes: Cannondale tandems: '92 Road, '97 Mtn. Mongoose 10.9 Ti, Kelly Deluxe, Tommaso Chorus, Cdale MT2000, Schwinn Deluxe Cruiser, Torker Unicycle, among others.
Mentioned: 5 Post(s)
Tagged: 0 Thread(s)
Quoted: 279 Post(s)
Liked 207 Times
in
129 Posts
A quick note of warning...
I am currently waiting on funds for making my bicycle an ebike. I am picky and don't want it to be noisy. Another criteria is not having to make major mods to the bicycle frame. There are mid drives in various power configurations. They are almost always noisy. There are direct drive hub motors that aren't noisy and Geared hub motors that are and not noisy. Dependability is a big factor for me so I have chosen a direct drive hub motor. Direct drive hub motors allow regen. It is not very much regen but enough to act as a drag brake on a grade. If you go this route you need to make sure the setup you purchase has this feature. Good fitment to the bicycle is important to me. I can only use a front hub motor. Your tandem can use A front or rear hub motor. I am going to purchase from Grin because of quality and well thought design of there products. Check out All Axle Hub Motor and If you don't mind the noise a collaboration between Bafang Grin and an American company called the GMAC Motor. the All Axle Hub Motor is a front only motor and works with a regular quick release or 5 different thru axle types and specialty one sided setups on trikes. The GMAC is a powerful geared motor that also has powerful regen. It uses a solid round 10mm axle.
Either way, caveat emptor to anyone purchasing & installing an electric wheel on a fork not designed for the torque loads they produce!
#9
Senior Member
Join Date: Feb 2007
Posts: 1,440
Mentioned: 5 Post(s)
Tagged: 0 Thread(s)
Quoted: 625 Post(s)
Likes: 0
Liked 397 Times
in
275 Posts
I just realized that I can offer a little advice on this subject. It just so happens I'm currently servicing an old Counterpoint semi-recumbent tandem for a friend. One of her relatives installed an electric front 20" wheel, which quickly bent, rotated and twised the fork blades and dropouts.
#10
Senior Member
Join Date: Jan 2020
Posts: 2,352
Mentioned: 2 Post(s)
Tagged: 0 Thread(s)
Quoted: 680 Post(s)
Liked 949 Times
in
556 Posts
not sure how a added on mid drive would work out. ours was built with a bosch mid drive and it has its quirks with the motor in front. wife can peddle while I don't so nothing lis locked together. it takes a lot of learning to work out how to do it well. but the motor has not caused too many issues with the drive train so far we got about 2000 miles out of the chain. maybe more but we had the chain jam together once and I think that screwed up the link on both chains. the motor cuts out at about 19 and thats where we cruise at. we can climb 16% grades for a couple of blocks.
#11
Senior Member
Join Date: Feb 2007
Posts: 1,440
Mentioned: 5 Post(s)
Tagged: 0 Thread(s)
Quoted: 625 Post(s)
Likes: 0
Liked 397 Times
in
275 Posts
The built on units have shift sensors so you don't jam up the drivetrain. If you were to add a mid drive to a bicycle you would need a system that allows you to add shift sensors to it. The most common problem with add on mid drive units is people wanting a motorcycle instead of an ebike. There are setups that run 2000 or more watts as an add on.
Likes For Rick:
#12
Senior Member
Join Date: Jan 2020
Posts: 2,352
Mentioned: 2 Post(s)
Tagged: 0 Thread(s)
Quoted: 680 Post(s)
Liked 949 Times
in
556 Posts
The built on units have shift sensors so you don't jam up the drivetrain. If you were to add a mid drive to a bicycle you would need a system that allows you to add shift sensors to it. The most common problem with add on mid drive units is people wanting a motorcycle instead of an ebike. There are setups that run 2000 or more watts as an add on.
#13
Senior Member
Join Date: Jul 2005
Posts: 5,992
Mentioned: 26 Post(s)
Tagged: 0 Thread(s)
Quoted: 2495 Post(s)
Liked 738 Times
in
522 Posts
There is a lack of pertinent info in your advice. There are some reasons that this could happen. The main one that happens to come to mind. is due to poor fitment of the hub motor axle it was allowed to spin in the fork and twist the power cable and pull itself from the fork. poor fitment of hub motor axles is common. Most front hub motor axles are 12mm diameter with 10mm flats ground in them. There usually needs to be some filing of the openings in the stays so the axles will fit. The smaller hub motors use the stay opening with a type of tabbed washer as the torque arm. If the axle bolts work loose or the filing is not done properly or both. The force can cause the opening in the stays to spread and the axle to rotate. The power going through the motor can be excessive enough for this to be a problem. Even with a torque arm ...
#14
Senior Member
Join Date: Jul 2005
Posts: 5,992
Mentioned: 26 Post(s)
Tagged: 0 Thread(s)
Quoted: 2495 Post(s)
Liked 738 Times
in
522 Posts
The most common mid-drive and the most powerful one in wide use is the Bafang BBSHD it is a nominal 1500W unit. It could probably survive 2K Watts but you would still be FAR short of an e motorcycle. When you have 15K Watts onboard you are in e-motorcycle territory. Even the Cyclone mid-drive which is crude and rude and so uncivilized most people have never heard of it is only 3KW nominal. Way more powerful than many bicycle frames and drivetrains can handle but FAR short of 'motorcycle' capability. People wanting to cheap out on the donor bike that they use in e-bike builds is the most common with both hub and mid-drive add on kits.
#15
Senior Member
Join Date: Feb 2007
Posts: 1,440
Mentioned: 5 Post(s)
Tagged: 0 Thread(s)
Quoted: 625 Post(s)
Likes: 0
Liked 397 Times
in
275 Posts
There is only one reason this happened, and you only touch on it, almost in passing: the lack of torque arms (two) allowed the motor to destroy the fork. Beginning and end of story. The Grin All Axle Hub Motor is a pretty nice piece of kit, and you are pretty sold on it, but I haven't seen the post where you tell people how much it costs! You might be prepared to take on a motor, a wheel build, a suitable controller/display, and battery, for a total cost well exceeding $2K, but that would not be everyone. And it is terribly incongruous for someone as well informed on the subject as you clearly are, to use 'breaking' when you mean 'braking'.
#16
Senior Member
Join Date: Feb 2007
Posts: 1,440
Mentioned: 5 Post(s)
Tagged: 0 Thread(s)
Quoted: 625 Post(s)
Likes: 0
Liked 397 Times
in
275 Posts
The most common mid-drive and the most powerful one in wide use is the Bafang BBSHD it is a nominal 1500W unit. It could probably survive 2K Watts but you would still be FAR short of an e motorcycle
#17
Senior Member
Join Date: Feb 2005
Location: SW Florida
Posts: 1,673
Bikes: '06 Bianchi Pista; '57 Maclean; '10 Scott CR1 Pro; 2005 Trek 2000 Tandem; '09 Comotion Macchiato Tandem; 199? Novara Road; '17 Circe Helios e-tandem:1994 Trek 2300
Mentioned: 5 Post(s)
Tagged: 0 Thread(s)
Quoted: 147 Post(s)
Liked 93 Times
in
61 Posts
An update on our Cytronex C1 installation: after about 3500 miles and 146 discharge/charges:
the wheel hasn’t collapsed, the fork and dropouts haven’t bent and the C1 works like a charm. Installation takes about 30 minutes.
Handling is not affected and power comes in gradually, so there is no loss of control on starting. Power is 250W.
I cannot imagine having to deal with a 750W motor in the front wheel, aside from the weight of that plus a battery.
Of course it depends upon intended use, but for 30 mile rides, even at 17-18 mph, the C1 is ideal for our combined ages of 161!
The C1 adds about 8lb, so the tandem is easy to stick in the back of our car once the front wheel is removed, which is very easy.
After sales support and remote diagnostics from the UK are outstanding.
Just a note about Li-ion batteries: make sure you don’t frequently discharge completely as we have been doing, which has resulted in a decrease in capacity to about 80% of what it was when new.
the wheel hasn’t collapsed, the fork and dropouts haven’t bent and the C1 works like a charm. Installation takes about 30 minutes.
Handling is not affected and power comes in gradually, so there is no loss of control on starting. Power is 250W.
I cannot imagine having to deal with a 750W motor in the front wheel, aside from the weight of that plus a battery.
Of course it depends upon intended use, but for 30 mile rides, even at 17-18 mph, the C1 is ideal for our combined ages of 161!
The C1 adds about 8lb, so the tandem is easy to stick in the back of our car once the front wheel is removed, which is very easy.
After sales support and remote diagnostics from the UK are outstanding.
Just a note about Li-ion batteries: make sure you don’t frequently discharge completely as we have been doing, which has resulted in a decrease in capacity to about 80% of what it was when new.
#18
alpine cross trainer
Join Date: Mar 2010
Location: Central New York
Posts: 289
Bikes: Specialized Roubaix, Quintara Roo Sendoza, DaVici In-2-Ition Tandem,
Mentioned: 0 Post(s)
Tagged: 0 Thread(s)
Quoted: 21 Post(s)
Likes: 0
Liked 20 Times
in
8 Posts
The most common mid-drive and the most powerful one in wide use is the Bafang BBSHD it is a nominal 1500W unit. It could probably survive 2K Watts but you would still be FAR short of an e motorcycle. When you have 15K Watts onboard you are in e-motorcycle territory. Even the Cyclone mid-drive which is crude and rude and so uncivilized most people have never heard of it is only 3KW nominal. Way more powerful than many bicycle frames and drivetrains can handle but FAR short of 'motorcycle' capability. People wanting to cheap out on the donor bike that they use in e-bike builds is the most common with both hub and mid-drive add on kits.
#19
Senior Member
Join Date: Jan 2020
Posts: 2,352
Mentioned: 2 Post(s)
Tagged: 0 Thread(s)
Quoted: 680 Post(s)
Liked 949 Times
in
556 Posts
I've got a Bafang BBSHD mid-drive on one my gravel bikes. It's 1000 Watts with a 52 volt battery. I think it's way more than any tandem would need. Their basic 750 Watt mid-drive would be more than enough for most tandem needs. Also, greater than 750 Watts is illegal in most jurisdictions for road use.
#20
Full Member
Quote:
I just realized that I can offer a little advice on this subject. It just so happens I'm currently servicing an old Counterpoint semi-recumbent tandem for a friend. One of her relatives installed an electric front 20" wheel, which quickly bent, rotated and twised the fork blades and dropouts.
There is a lack of pertinent info in your advice. There are some reasons that this could happen. The main one that happens to come to mind. is due to poor fitment of the hub motor axle it was allowed to spin in the fork and twist the power cable and pull itself from the fork. poor fitment of hub motor axles is common. Most front hub motor axles are 12mm diameter with 10mm flats ground in them. There usually needs to be some filing of the openings in the stays so the axles will fit. The smaller hub motors use the stay opening with a type of tabbed washer as the torque arm. If the axle bolts work loose or the filing is not done properly or both. The force can cause the opening in the stays to spread and the axle to rotate. The power going through the motor can be excessive enough for this to be a problem. Even with a torque arm that mounts off of the axle and straps to the fork. Careful attention needs to be made to assure everything fits, is properly tightened and there are no signs of the fork blades spreading or the flats rounding. The Grin All Axle Hub Motor Is made so there is no spreading force on the fork blades. There is a 20mm hole through the axle which you use the axle end caps that match your setup. 9mm quick release is what I will use. You can go to the info page I posted in a previous post in this thread. I believe that the torque created by the system I am building is less than the hard breaking of my disk brakes. The direct drive motor will be setup with regen also.
I just realized that I can offer a little advice on this subject. It just so happens I'm currently servicing an old Counterpoint semi-recumbent tandem for a friend. One of her relatives installed an electric front 20" wheel, which quickly bent, rotated and twised the fork blades and dropouts.
There is a lack of pertinent info in your advice. There are some reasons that this could happen. The main one that happens to come to mind. is due to poor fitment of the hub motor axle it was allowed to spin in the fork and twist the power cable and pull itself from the fork. poor fitment of hub motor axles is common. Most front hub motor axles are 12mm diameter with 10mm flats ground in them. There usually needs to be some filing of the openings in the stays so the axles will fit. The smaller hub motors use the stay opening with a type of tabbed washer as the torque arm. If the axle bolts work loose or the filing is not done properly or both. The force can cause the opening in the stays to spread and the axle to rotate. The power going through the motor can be excessive enough for this to be a problem. Even with a torque arm that mounts off of the axle and straps to the fork. Careful attention needs to be made to assure everything fits, is properly tightened and there are no signs of the fork blades spreading or the flats rounding. The Grin All Axle Hub Motor Is made so there is no spreading force on the fork blades. There is a 20mm hole through the axle which you use the axle end caps that match your setup. 9mm quick release is what I will use. You can go to the info page I posted in a previous post in this thread. I believe that the torque created by the system I am building is less than the hard breaking of my disk brakes. The direct drive motor will be setup with regen also.
Also, you state:
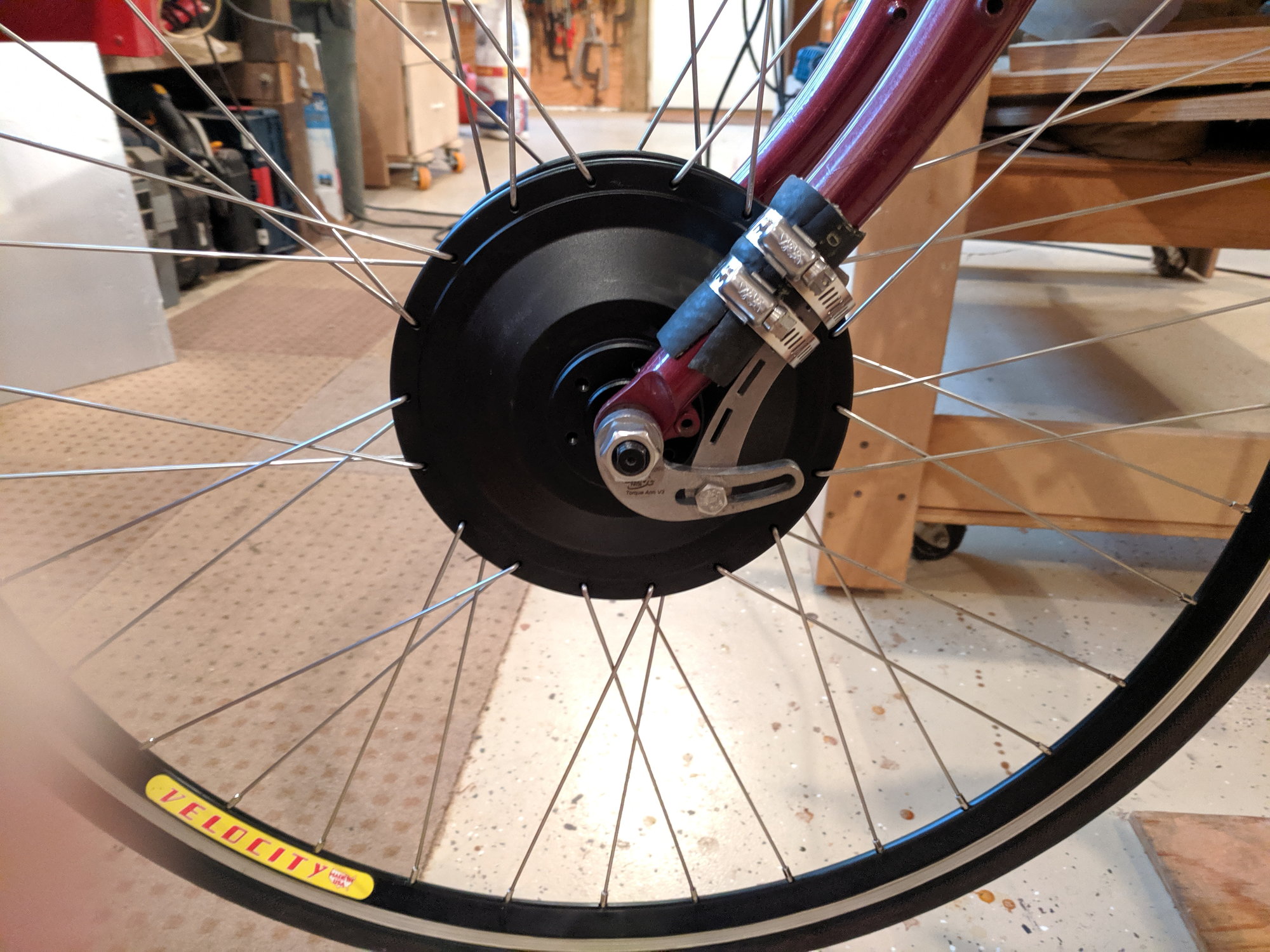
#21
Full Member
Looks like you have the EZEE geared hub motor on it. That would be a good choice for my 1990 Burley bongo. I am going to electrify my Co-Motion Pangea Rohloff, a 26" wheeled belt driven single with a 14 speed IGH. As I already posted I like the Grin All axle Hub Motor I of course intend to use Statorade and a HubSinkto help it stay cool.
The point of my rambling is that with a tandem, climbing will be slower which is resulting in higher battery and motor currents. I my case, the battery plant appears to be the limiting factor (both in terms of max supported current and thermal mitigation) - The hub motor has only been warm to the touch and we have not even gotten close to the 150C max rating. You may not need the Statoraide or cooling fins. (Maybe system performance is different for a single).
My next step is to use the Phaserunner application running on an old net book to log all the system parameters during a few rides and analyze the characteristics of when we are stressing the batteries. Depending on what I find I may modify the battery case such that I can increase cooling of the battery array, or I will design and build my own battery subsystem with a higher power BMS and cooling. One thing that is very interesting with the electric motors, is that it is more efficient and dissipates less heat the faster you ride.
Last edited by Alcanbrad; 05-09-21 at 06:00 PM.
#22
Senior Member
Join Date: Feb 2007
Posts: 1,440
Mentioned: 5 Post(s)
Tagged: 0 Thread(s)
Quoted: 625 Post(s)
Likes: 0
Liked 397 Times
in
275 Posts
The torque resulting from the disc brakes are between the tire/rim and the hub flange. The torque resulting from the motor is between the tire/rim and axle. You won't be able twist the axle and spread the drop outs via the disc unless the brake calipers were attached directly to the axle.
#23
Senior Member
Join Date: Feb 2007
Posts: 1,440
Mentioned: 5 Post(s)
Tagged: 0 Thread(s)
Quoted: 625 Post(s)
Likes: 0
Liked 397 Times
in
275 Posts
You may not need the Statoraide or cooling fins. (Maybe system performance is different for a single).
#24
Full Member
#25
Full Member
Grin produces the All Axle Hub Motor themselves. It weighs around 4 kilos instead of the 6 or more kilos of their competitors. Due to less thermal mass Grin recommends you use Staterade. The ferrel flud they developed called statorade allows heat to escape more efficiently through the outer casing of the motor. Your geared motor creates better torque than a direct drive like the All Axle Hub Motor. I have disk brakes and A fork designed for the Son SL dyno hub. I am not going to modify my SS dropouts with a file. Because I can setup regen to help with braking I am going to use a battery pack rated for 14s.