Welding temperature versus frame stiffness at BB
#26
Newbie
Correct, welding almost always reduces the strength somewhere in the HAZ*. If it causes cracking, then the bike may feel less stiff, but the crack will become visible after a (usually short) time, and cracks too small to see are also probably (I'd guess "absolutely") too small to feel. The reduction in yield strength is irelevant to ride feel, since the frame doesn't yield in use. If it was yielding with each pedal stroke, it wouldn't make it a mile down the road before breaking in two. Even getting close to yielding will cause low-cycle fatigue, so maybe breaking in 10 miles (?) instead of one mile. Even department-store BSOs seldom do that.
* It's not easy to predict where the weak spot will be in the HAZ. The actual weld got well above the transformation temperature, and the cooling rate in air (aided by the "self-quench" from conduction to the cold part of the tube) is fast enough that the steel is Normalized, a heat-treat state that actually has pretty good properties in most bike steel. For some "air hardening" steels, the weld can end up stronger than the as-delivered value.
There may be exceptions but it seems to me that the weak spot is always somewhere back from the weld, where the transformation temperature wasn't reached, and the steel saw only tempering. The size of the tempered zone, and how tempered it is, can be affected by the skill of the welder, who can input the minimum heat consistent with proper penetration and keep the time-at-temperature to a minimum.
Heat sinks are sometimes used, which may help reduce the size and softening effect of the HAZ, but I haven't analyzed that myself. I'd be interested to hear what unterhausen and other pro FBs thinks about pros-cons of commonly-used heat sinks. I used them when making titanium frames, but that was more for argon purging, secondarily for maintaining roundness of the places they were inserted, like the headset and seatpost bores. You obviously can't have heat sinks inside the TT or DT or rear stays, but sinks in, say, the HT could still improve as-welded strength of the DT & TT in the HAZ if the sink pulls heat out of them by conduction.
EDIT: I realized I didn't comment on "im assuming frame builders would need to do some heat treatment to the metal post welding".
No, almost no welded steel frames get any post-weld heat-treat. My experience is all 30 years out of date so maybe there are steels now that need something, but I haven't heard of any. I made frames with Aermet 100 alloy in the '90s, and Carpenter specified some heat treat, I forget what, just stress-relieving probably or was it "aging"? But it was easy, one step, we baked them in a commercial pizza oven which did it just fine. The "quench and temper" typically done on say 4130 would be extremely expensive to do on a whole frame, and the frame would distort all over the place and be near impossible to straighten in the hardened state. I believe Keith Bontrager did it on some welded handlebar stems, but whole frames, no.
* It's not easy to predict where the weak spot will be in the HAZ. The actual weld got well above the transformation temperature, and the cooling rate in air (aided by the "self-quench" from conduction to the cold part of the tube) is fast enough that the steel is Normalized, a heat-treat state that actually has pretty good properties in most bike steel. For some "air hardening" steels, the weld can end up stronger than the as-delivered value.
There may be exceptions but it seems to me that the weak spot is always somewhere back from the weld, where the transformation temperature wasn't reached, and the steel saw only tempering. The size of the tempered zone, and how tempered it is, can be affected by the skill of the welder, who can input the minimum heat consistent with proper penetration and keep the time-at-temperature to a minimum.
Heat sinks are sometimes used, which may help reduce the size and softening effect of the HAZ, but I haven't analyzed that myself. I'd be interested to hear what unterhausen and other pro FBs thinks about pros-cons of commonly-used heat sinks. I used them when making titanium frames, but that was more for argon purging, secondarily for maintaining roundness of the places they were inserted, like the headset and seatpost bores. You obviously can't have heat sinks inside the TT or DT or rear stays, but sinks in, say, the HT could still improve as-welded strength of the DT & TT in the HAZ if the sink pulls heat out of them by conduction.
EDIT: I realized I didn't comment on "im assuming frame builders would need to do some heat treatment to the metal post welding".
No, almost no welded steel frames get any post-weld heat-treat. My experience is all 30 years out of date so maybe there are steels now that need something, but I haven't heard of any. I made frames with Aermet 100 alloy in the '90s, and Carpenter specified some heat treat, I forget what, just stress-relieving probably or was it "aging"? But it was easy, one step, we baked them in a commercial pizza oven which did it just fine. The "quench and temper" typically done on say 4130 would be extremely expensive to do on a whole frame, and the frame would distort all over the place and be near impossible to straighten in the hardened state. I believe Keith Bontrager did it on some welded handlebar stems, but whole frames, no.
thats actually a point i forgot about about air hardening type steels as im new to this bike building thing or frame.
but either way using a heat sink works in my experience and to be fair ive seen alot of welders not even know about the trick i usually use them for welding 2mm and under on mma, obviously you said you use to keep the tubes from warping during welding this could also be accounted for be using a piece of scrap that could fit the tubing? But round stock can be expensive i know
also on the stays im assuming this is the rear quater of the bike as in the post that connect to the seatpost for the rear wheel, cant you make some sort of half round sync by bending some copper ie youd have to weld half and then move the sync for the rest.
And arent some of the alloy or aluminium frames post treated
Last edited by Jordanjw; 05-06-24 at 04:34 PM.
#27
Randomhead
Join Date: Aug 2008
Location: Happy Valley, Pennsylvania
Posts: 24,459
Mentioned: 0 Post(s)
Tagged: 0 Thread(s)
Quoted: 4 Post(s)
Liked 3,758 Times
in
2,558 Posts
Aluminum frames undergo post-weld heat treating so they don't break. It has nothing to do with stiffness.
#28
Senior Member
Join Date: Dec 2019
Posts: 972
Mentioned: 3 Post(s)
Tagged: 0 Thread(s)
Quoted: 329 Post(s)
Liked 265 Times
in
214 Posts
Correct, welding almost always reduces the strength somewhere in the HAZ*. If it causes cracking, then the bike may feel less stiff, but the crack will become visible after a (usually short) time, and cracks too small to see are also probably (I'd guess "absolutely") too small to feel. The reduction in yield strength is irelevant to ride feel, since the frame doesn't yield in use. If it was yielding with each pedal stroke, it wouldn't make it a mile down the road before breaking in two. Even getting close to yielding will cause low-cycle fatigue, so maybe breaking in 10 miles (?) instead of one mile. Even department-store BSOs seldom do that.
* It's not easy to predict where the weak spot will be in the HAZ. The actual weld got well above the transformation temperature, and the cooling rate in air (aided by the "self-quench" from conduction to the cold part of the tube) is fast enough that the steel is Normalized, a heat-treat state that actually has pretty good properties in most bike steel. For some "air hardening" steels, the weld can end up stronger than the as-delivered value.
* It's not easy to predict where the weak spot will be in the HAZ. The actual weld got well above the transformation temperature, and the cooling rate in air (aided by the "self-quench" from conduction to the cold part of the tube) is fast enough that the steel is Normalized, a heat-treat state that actually has pretty good properties in most bike steel. For some "air hardening" steels, the weld can end up stronger than the as-delivered value.
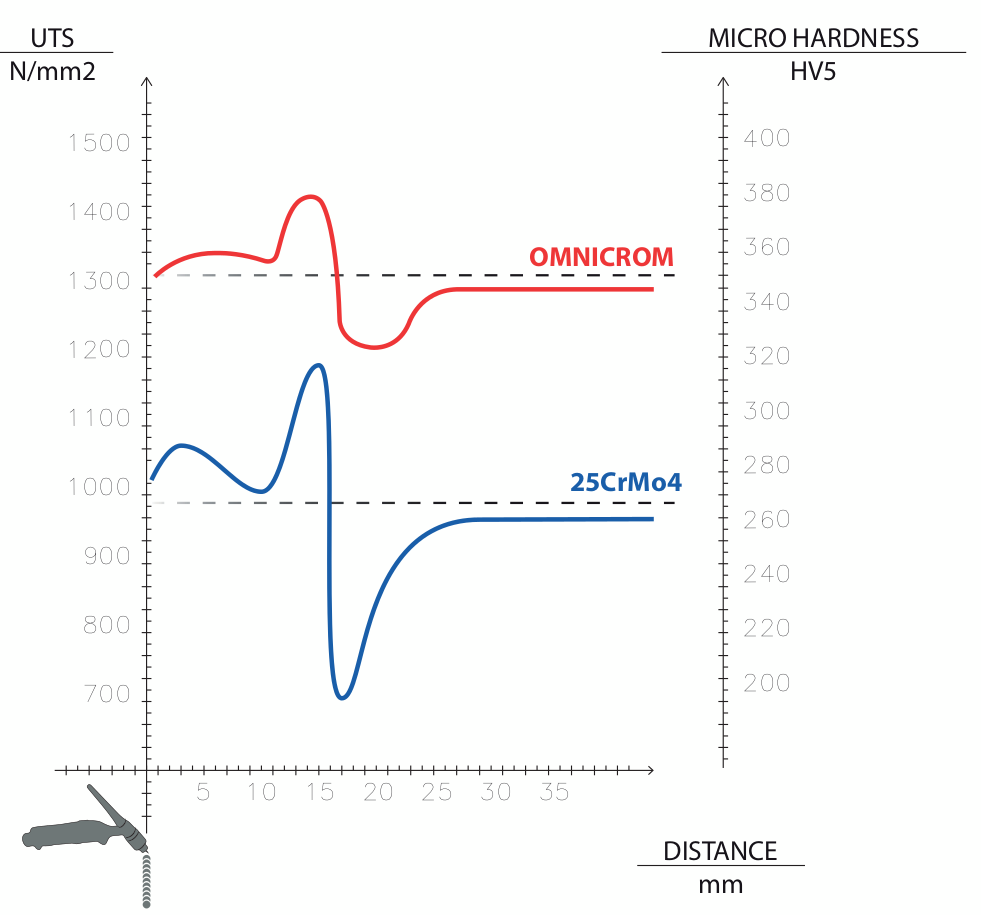
And then Reynolds have this one, which includes their "air-hardening" steels, 631 and 853:
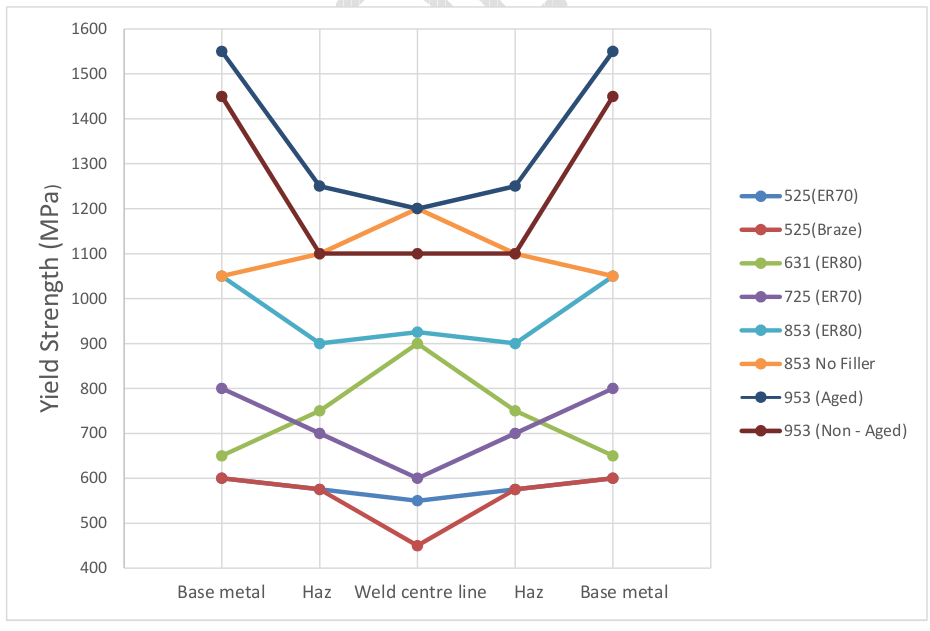
Showing how they get stronger and never weaker.
EDIT: I realized I didn't comment on "im assuming frame builders would need to do some heat treatment to the metal post welding".
No, almost no welded steel frames get any post-weld heat-treat. My experience is all 30 years out of date so maybe there are steels now that need something, but I haven't heard of any. I made frames with Aermet 100 alloy in the '90s, and Carpenter specified some heat treat, I forget what, just stress-relieving probably or was it "aging"? But it was easy, one step, we baked them in a commercial pizza oven which did it just fine. The "quench and temper" typically done on say 4130 would be extremely expensive to do on a whole frame, and the frame would distort all over the place and be near impossible to straighten in the hardened state. I believe Keith Bontrager did it on some welded handlebar stems, but whole frames, no.
No, almost no welded steel frames get any post-weld heat-treat. My experience is all 30 years out of date so maybe there are steels now that need something, but I haven't heard of any. I made frames with Aermet 100 alloy in the '90s, and Carpenter specified some heat treat, I forget what, just stress-relieving probably or was it "aging"? But it was easy, one step, we baked them in a commercial pizza oven which did it just fine. The "quench and temper" typically done on say 4130 would be extremely expensive to do on a whole frame, and the frame would distort all over the place and be near impossible to straighten in the hardened state. I believe Keith Bontrager did it on some welded handlebar stems, but whole frames, no.
#29
blahblahblah chrome moly
Join Date: Apr 2009
Location: Seattle
Posts: 2,038
Mentioned: 94 Post(s)
Tagged: 0 Thread(s)
Quoted: 1206 Post(s)
Liked 2,647 Times
in
1,103 Posts
For one thing it shows the "weld centre line" as the weakest spot, which is never the case in my experience. For one thing when frames buckle from overload, it's always a couple mm back from the toe of the weld, which I interpret as being the place that got only tempering. As shown in the Columbus curves. Which also agree with the testing done by Mario Emiliani for Bike Tech magazine. (Scan available here)
About "they get stronger and never weaker": 631 yes, somewhat believable since it's air-hardening and delivered non-heat-treated, so the weld is the heat-treat. (There should still be a tempered zone in the Haz though).
But 853 shows a dip in strength at the weld. Only "853 no filler" actually gets stronger, and how useful is that? Not many joints on a bike frame are made with no filler. And why would the presence/absence of filler make such a huge difference out in the HAZ (away from the weld site)? With no explanation of their testing / measurement methods, I'm inclined to assume they just pulled it out of their a$$.
I'm also rather dubious of the tiny loss of strength seen in 525. I'd like to see the actual numbers because this is not convincing at all! The Columbus curves are also a bit schematic (which is forgivable for a consumer ad) but at least they're believable. A schematic drawn by an engineer at least, not an intern in the marketing department who's never been in a metal shop (or a Strength of Materials class).
I still like Reynolds steel but I find their marketing materials to be an embarrassment, bordering on unethical. Luckily for them I judge steel on its merits, not on its advertizing.
Likes For bulgie:
#30
Newbie
Correct, welding almost always reduces the strength somewhere in the HAZ*. If it causes cracking, then the bike may feel less stiff, but the crack will become visible after a (usually short) time, and cracks too small to see are also probably (I'd guess "absolutely") too small to feel. The reduction in yield strength is irelevant to ride feel, since the frame doesn't yield in use. If it was yielding with each pedal stroke, it wouldn't make it a mile down the road before breaking in two. Even getting close to yielding will cause low-cycle fatigue, so maybe breaking in 10 miles (?) instead of one mile. Even department-store BSOs seldom do that.
in regards to what was said on over loading i was referring to weight on the actual bike rather than force from the crank i don't see how a crank with a bearing can put force onto the frame, obviously most of the weight is on the wheels but your still on the bike frame the op mentioned that the bike was loaded, ive read that alot of road or race bike do break close to their tolerance or advertised weight, when in practice this should be atleast 25% if not 50% above the recommended weight
also something to mention on hardened metals is they can be hardened by correct post and pre heating but if not done correctly this can lead to it being brittle and it causes cracks not only that chromium itself is a brittle metal, so in general an overloaded frame on a chromo frame is bound to show signs of cracks and fatigue
take this as an example if you fold a piece of hardox you can only fold it once, your unable to bend it back due to its hardness and brittleness if you do it cracks showing extreme fatigue this is the only similar example i can really think of its not really the same but in general you understand how the cracks can form easily on harder metals vs normal steel
id like to ask the people making these frames how brittle these are when they leave the factory as this is the only thing that causes cracks in frames
in regards to what was said on over loading i was referring to weight on the actual bike rather than force from the crank i don't see how a crank with a bearing can put force onto the frame, obviously most of the weight is on the wheels but your still on the bike frame the op mentioned that the bike was loaded, ive read that alot of road or race bike do break close to their tolerance or advertised weight, when in practice this should be atleast 25% if not 50% above the recommended weight
also something to mention on hardened metals is they can be hardened by correct post and pre heating but if not done correctly this can lead to it being brittle and it causes cracks not only that chromium itself is a brittle metal, so in general an overloaded frame on a chromo frame is bound to show signs of cracks and fatigue
take this as an example if you fold a piece of hardox you can only fold it once, your unable to bend it back due to its hardness and brittleness if you do it cracks showing extreme fatigue this is the only similar example i can really think of its not really the same but in general you understand how the cracks can form easily on harder metals vs normal steel
id like to ask the people making these frames how brittle these are when they leave the factory as this is the only thing that causes cracks in frames
Last edited by Jordanjw; 05-08-24 at 03:22 PM.
#31
Senior Member
Join Date: Dec 2019
Posts: 972
Mentioned: 3 Post(s)
Tagged: 0 Thread(s)
Quoted: 329 Post(s)
Liked 265 Times
in
214 Posts
I am dubious of the Reynolds chart — it seems "schematic" and not an actual plot of data. Likely concocted by the marketing graphics team, with no engineers in the room. (Reynolds has a long history of that.)
For one thing it shows the "weld centre line" as the weakest spot, which is never the case in my experience. For one thing when frames buckle from overload, it's always a couple mm back from the toe of the weld, which I interpret as being the place that got only tempering. As shown in the Columbus curves. Which also agree with the testing done by Mario Emiliani for Bike Tech magazine. (Scan available here)
About "they get stronger and never weaker": 631 yes, somewhat believable since it's air-hardening and delivered non-heat-treated, so the weld is the heat-treat. (There should still be a tempered zone in the Haz though).
But 853 shows a dip in strength at the weld. Only "853 no filler" actually gets stronger, and how useful is that? Not many joints on a bike frame are made with no filler. And why would the presence/absence of filler make such a huge difference out in the HAZ (away from the weld site)? With no explanation of their testing / measurement methods, I'm inclined to assume they just pulled it out of their a$$.
I'm also rather dubious of the tiny loss of strength seen in 525. I'd like to see the actual numbers because this is not convincing at all! The Columbus curves are also a bit schematic (which is forgivable for a consumer ad) but at least they're believable. A schematic drawn by an engineer at least, not an intern in the marketing department who's never been in a metal shop (or a Strength of Materials class).
I still like Reynolds steel but I find their marketing materials to be an embarrassment, bordering on unethical. Luckily for them I judge steel on its merits, not on its advertizing.
For one thing it shows the "weld centre line" as the weakest spot, which is never the case in my experience. For one thing when frames buckle from overload, it's always a couple mm back from the toe of the weld, which I interpret as being the place that got only tempering. As shown in the Columbus curves. Which also agree with the testing done by Mario Emiliani for Bike Tech magazine. (Scan available here)
About "they get stronger and never weaker": 631 yes, somewhat believable since it's air-hardening and delivered non-heat-treated, so the weld is the heat-treat. (There should still be a tempered zone in the Haz though).
But 853 shows a dip in strength at the weld. Only "853 no filler" actually gets stronger, and how useful is that? Not many joints on a bike frame are made with no filler. And why would the presence/absence of filler make such a huge difference out in the HAZ (away from the weld site)? With no explanation of their testing / measurement methods, I'm inclined to assume they just pulled it out of their a$$.
I'm also rather dubious of the tiny loss of strength seen in 525. I'd like to see the actual numbers because this is not convincing at all! The Columbus curves are also a bit schematic (which is forgivable for a consumer ad) but at least they're believable. A schematic drawn by an engineer at least, not an intern in the marketing department who's never been in a metal shop (or a Strength of Materials class).
I still like Reynolds steel but I find their marketing materials to be an embarrassment, bordering on unethical. Luckily for them I judge steel on its merits, not on its advertizing.
That diagram is actually described as an "estimate subject to validation" (the document is dated 2017-- did they ever do the validation?)
525 just literally is standard 4130, so there is no reason why it should be any different from what is on Columbus's graph except marketing.
I use 631 for most of my builds because I'm TIG welding, and it doesn't cost much more here than 525 (or any other cromoly bicycle tubes), but yes I doubt there is a big difference. I do have some offcuts I could try to do some tests on, although I doubt I would be able to detect anything with my crude methods.
Likes For guy153:
#32
Newbie
I am dubious of the Reynolds chart — it seems "schematic" and not an actual plot of data. Likely concocted by the marketing graphics team, with no engineers in the room. (Reynolds has a long history of that.)
For one thing it shows the "weld centre line" as the weakest spot, which is never the case in my experience. For one thing when frames buckle from overload, it's always a couple mm back from the toe of the weld, which I interpret as being the place that got only tempering. As shown in the Columbus curves. Which also agree with the testing done by Mario Emiliani for Bike Tech magazine. (Scan available here)
About "they get stronger and never weaker": 631 yes, somewhat believable since it's air-hardening and delivered non-heat-treated, so the weld is the heat-treat. (There should still be a tempered zone in the Haz though).
But 853 shows a dip in strength at the weld. Only "853 no filler" actually gets stronger, and how useful is that? Not many joints on a bike frame are made with no filler. And why would the presence/absence of filler make such a huge difference out in the HAZ (away from the weld site)? With no explanation of their testing / measurement methods, I'm inclined to assume they just pulled it out of their a$$.
I'm also rather dubious of the tiny loss of strength seen in 525. I'd like to see the actual numbers because this is not convincing at all! The Columbus curves are also a bit schematic (which is forgivable for a consumer ad) but at least they're believable. A schematic drawn by an engineer at least, not an intern in the marketing department who's never been in a metal shop (or a Strength of Materials class).
I still like Reynolds steel but I find their marketing materials to be an embarrassment, bordering on unethical. Luckily for them I judge steel on its merits, not on its advertizing.
For one thing it shows the "weld centre line" as the weakest spot, which is never the case in my experience. For one thing when frames buckle from overload, it's always a couple mm back from the toe of the weld, which I interpret as being the place that got only tempering. As shown in the Columbus curves. Which also agree with the testing done by Mario Emiliani for Bike Tech magazine. (Scan available here)
About "they get stronger and never weaker": 631 yes, somewhat believable since it's air-hardening and delivered non-heat-treated, so the weld is the heat-treat. (There should still be a tempered zone in the Haz though).
But 853 shows a dip in strength at the weld. Only "853 no filler" actually gets stronger, and how useful is that? Not many joints on a bike frame are made with no filler. And why would the presence/absence of filler make such a huge difference out in the HAZ (away from the weld site)? With no explanation of their testing / measurement methods, I'm inclined to assume they just pulled it out of their a$$.
I'm also rather dubious of the tiny loss of strength seen in 525. I'd like to see the actual numbers because this is not convincing at all! The Columbus curves are also a bit schematic (which is forgivable for a consumer ad) but at least they're believable. A schematic drawn by an engineer at least, not an intern in the marketing department who's never been in a metal shop (or a Strength of Materials class).
I still like Reynolds steel but I find their marketing materials to be an embarrassment, bordering on unethical. Luckily for them I judge steel on its merits, not on its advertizing.
also hydrogen embrittlement happens in steel too regardless, the only way to counter this is to use low hydrogen consumables
#33
blahblahblah chrome moly
Join Date: Apr 2009
Location: Seattle
Posts: 2,038
Mentioned: 94 Post(s)
Tagged: 0 Thread(s)
Quoted: 1206 Post(s)
Liked 2,647 Times
in
1,103 Posts
but regardless the frame is still susceptible to nitrogen embrittlement, the only way to counter this is to paint but no one paints right after they weld do they? this occurs at room temperature, also if you was to tig weld youd need to purge the pipe so i assume some sort of port holes are drilled in for this, so therefore you cant help the nitrogen embrittlement because you dont paint the inside of the frame.
also hydrogen embrittlement happens in steel too regardless, the only way to counter this is to use low hydrogen consumables
also hydrogen embrittlement happens in steel too regardless, the only way to counter this is to use low hydrogen consumables
High-end steel frames (aircraft and auto/moto as well as bikes) have been made from CrMo for many decades and I've never heard of a single one cracking from nitrogen. Despite them being made as light as possible (consumers just want whatever's lightest), cracking without crashing first is remarkably rare. If you make it a bit heavier, it's easy to make a frame that will last multiple human lifetimes.
A few guys purge the inside of the frame with argon, but that's somewhat rare in steel. It's mostly a thing for titanium and stainless. Still recommended for the thinnest CrMo, but absolutely not necessary for the thick stuff you're talking about for this cargo bike.
Likes For bulgie:
#34
Newbie
Got any references for that? Cuz it goes against my experience.
High-end steel frames (aircraft and auto/moto as well as bikes) have been made from CrMo for many decades and I've never heard of a single one cracking from nitrogen. Despite them being made as light as possible (consumers just want whatever's lightest), cracking without crashing first is remarkably rare. If you make it a bit heavier, it's easy to make a frame that will last multiple human lifetimes.
A few guys purge the inside of the frame with argon, but that's somewhat rare in steel. It's mostly a thing for titanium and stainless. Still recommended for the thinnest CrMo, but absolutely not necessary for the thick stuff you're talking about for this cargo bike.
High-end steel frames (aircraft and auto/moto as well as bikes) have been made from CrMo for many decades and I've never heard of a single one cracking from nitrogen. Despite them being made as light as possible (consumers just want whatever's lightest), cracking without crashing first is remarkably rare. If you make it a bit heavier, it's easy to make a frame that will last multiple human lifetimes.
A few guys purge the inside of the frame with argon, but that's somewhat rare in steel. It's mostly a thing for titanium and stainless. Still recommended for the thinnest CrMo, but absolutely not necessary for the thick stuff you're talking about for this cargo bike.
Also my original point on it being overloaded was to do with weight issues on the frame itself the wheels would take the load but youd still have upward force from bumps etc aswell as some downward as the frames main load bearing point would be the bb, and i get the point on the cargo but its already been started so ill have to learn from it i guess
and do you know if main brands like trek etc have a specific break limit on their frames ie their limit on the bike is 120kg but in the warehouse the actual break point was at say 240kg as being a welder its normally atleast 75-100% above whats needed for load as normally people undercalculate and end up overloading things, as if they dont this could also be a factor in the sense the customer wants to load it all the way to the recommended max load
Last edited by Jordanjw; 05-09-24 at 05:09 PM.
#35
Senior Member
Join Date: Aug 2012
Location: Seattle
Posts: 514
Mentioned: 0 Post(s)
Tagged: 0 Thread(s)
Quoted: 106 Post(s)
Liked 145 Times
in
89 Posts
I have never heard paint protects against nitrogen embrittlement. That doesn't make any sense to me from a metalugical standpoint. I will caveat that with I am not an engineer or material scientist. I'm just saying that throughout the research I have done into welding, brazing and framebuilding along with practice, examples on the road and talking with dudes who have been doing this for 3-4 decades, I have never heard a single person suggest paint has any effect on preventing embrittlement. I have repeatedly heard that the argon purge is what protected against weld problems. Very interested to hear more or provide references. Thx
__________________
https://www.flickr.com/photos/54319503@N05/
https://www.draper-cycles.com
https://www.flickr.com/photos/54319503@N05/
https://www.draper-cycles.com
#36
Randomhead
Join Date: Aug 2008
Location: Happy Valley, Pennsylvania
Posts: 24,459
Mentioned: 0 Post(s)
Tagged: 0 Thread(s)
Quoted: 4 Post(s)
Liked 3,758 Times
in
2,558 Posts
Nitrogen embrittlement doesn't seem to be much of a problem with bike frames, for whatever reason. Just quickly googling it seems to suggest that's because it simply doesn't happen much.
#37
Newbie
This is particularly relevant as I recently acquired a TIG machine and will start welding soon.
I have never heard paint protects against nitrogen embrittlement. That doesn't make any sense to me from a metalugical standpoint. I will caveat that with I am not an engineer or material scientist. I'm just saying that throughout the research I have done into welding, brazing and framebuilding along with practice, examples on the road and talking with dudes who have been doing this for 3-4 decades, I have never heard a single person suggest paint has any effect on preventing embrittlement. I have repeatedly heard that the argon purge is what protected against weld problems. Very interested to hear more or provide references. Thx
I have never heard paint protects against nitrogen embrittlement. That doesn't make any sense to me from a metalugical standpoint. I will caveat that with I am not an engineer or material scientist. I'm just saying that throughout the research I have done into welding, brazing and framebuilding along with practice, examples on the road and talking with dudes who have been doing this for 3-4 decades, I have never heard a single person suggest paint has any effect on preventing embrittlement. I have repeatedly heard that the argon purge is what protected against weld problems. Very interested to hear more or provide references. Thx
I did have half of this written up last night heres a link on chromo and embrittlemenr https://masteel.co.uk/news/chromium-...20are%20formed.
https://f3timbertech.com/the-effects...%20of%20cracks.
Also says somewhere in there materials that are highly ductile are more likely to have nitrogen embrittlement
Thats coatings used om fasteners but as the top link proves it happens the coating can be used for the chromo too. I think its more a newer thing like epoxy coatings can be a good barrier but i doubt youd be able to find a bath big enough to zinc plate the bike even though you probably wouldnt want to
Also yes purging does protect during welding, it stops oxizidation from forming during welding
As i said before chromium in general is a brittle material granted harder than steel but not usable for structures due to if their struck its certain a failure will happen.
Also i know this is strange saying all this even though no one has had any real problems but is anyone actually able to test the nitrogen levels in their bike composition to confirm no embrittlement hasnt taken place
i did have another link ill have to find it
#38
Senior Member
Just a few thoughts, basic, do not address all things above.
A coil spring, in compression or tension (force direction in line with the coil axis), puts the spring wire in both bending and torsion stress. If a coil spring is being wound tighter or looser diameter, that puts the spring wire in mostly bending stress.
If a (compression) coil spring yields, i.e., stressed beyond its limit, as stated previously, the spring will take a set and have a shorter overall length, but the spring rate (stiffness) will remain the same. Yes, *IF AND ONLY IF*, there is the same length of spring being loaded in bending and torsion; If some of the coils "bottom", i.e., rest against each other, then a shorter overall length of wire is being stressed and the spring rate *increases*; This is how you create variable-rate coil springs.
If you stress any kind of spring beyond the actual material yield stress, the spring will yield immediately, not after repeated occurances, but the first time. It will yield plastically, unless you yield it above the ultimate tensile stress of the material, in which case it will break, known as ultimate failure.
If you stress a spring below the yield stress, even at 99% of the yield stress, it will not yield plastically. However, if you stress it at that high a level, enough times in cyclic stress (not static), it will eventually break via *fatigue*, without ever exceeding the ultimate tensile strength of the material. Steels have a "fatigue limit", a stress where, if you never exceed that stress, the steel will not fail in fatigue, ever. This fatigue limit stress is far below the yield strength, I'm gonna pull a number out of thin air and say 50% yield, but I've forgotten where that actually is, and it varies by steel composition and processing. Most steel things where weight matters, like cars and bicycles, will be stressed over the fatigue limit, because if below the fatigue limit, the part would be too heavy, and the part does not need to last forever, just the life of the vehicle. Safety critical parts will have additional safety margin to prevent "catastrophic" (sudden and without warning) failure, or a "graceful degradation mode" with plenty of warning. Coil springs on old cars would often fail in fatigue after a time, usually at the end, a piece would snap off, that corner of the car would sag, but keep on working, but by shortening the spring, the stresses are raised, so a year later another piece would snap off, the car would sag lower, but not fail in an unsafe way, and continue to happen until the car eventually is riding on the bump stops. Leaf springs too, but on any of the leaves *except* the top leaf that holds the axle in place, that one cannot fail or the car or truck loses control.
Aluminum does not have a fatigue limit; If you stress it enough times in cyclic loading, it will fail. At a low enough stress, that make take ten million years, but it will happen eventually. This is why aluminum parts need to be designed more stiff than steel to hold up in fatigue. This works well for a bike that you want stiff in torsion, like a road race bike for fast sprints, or a loaded touring bike, or a suspension mountain bike. But under other conditions, in general, rigid frame aluminum bikes ride stiffer than other materials.
Titanium has fantastic fatigue strength, and is half the weight of steel. It makes excellent bike frames that ride well. You can make auto springs from titanium, they are just expensive, so the purview of race cars. You can make titanium foil camera shutters that wind around a spool and unwind straight, repeatedly; A Nikon F(1) had a ball bearing and titanium foil focal plane shutter that was good for a minimum of 100,000 cycles.
The elastic ("Young's") modulus or a material (defined as "stress over strain"), i.e., how much it stretches or flexes elastically below the yield stress, in general, does not change within a "family" of materials; Low strength steel has the same stiffness as high strength steel, however the latter can be stressed higher before yielding or breaking. Steel has about 3X the elastic modulus of aluminum. There can be relatively small changes to this due to alloying elements. This has been doctrine for forever. *However*, there have been some very recent developments in "nano-structured High Modulus Steel" that breaks this rule, and is 25% higher elastic modulus than steels that have been produced in the past, and is also excellent strength and ductility (spread between yield and ultimate strengths). This is especially good news for part designs limited by compressive buckling, as that is NOT a factor of the part strength, but the part stiffness, the latter being a function of a) the geometric stiffness, i.e., the geometric section modulus, b) the unconstrained column length, c) the end fixing conditions, and d) the material elastic modulus.
(to be continued if I think of more relevant things)
A coil spring, in compression or tension (force direction in line with the coil axis), puts the spring wire in both bending and torsion stress. If a coil spring is being wound tighter or looser diameter, that puts the spring wire in mostly bending stress.
If a (compression) coil spring yields, i.e., stressed beyond its limit, as stated previously, the spring will take a set and have a shorter overall length, but the spring rate (stiffness) will remain the same. Yes, *IF AND ONLY IF*, there is the same length of spring being loaded in bending and torsion; If some of the coils "bottom", i.e., rest against each other, then a shorter overall length of wire is being stressed and the spring rate *increases*; This is how you create variable-rate coil springs.
If you stress any kind of spring beyond the actual material yield stress, the spring will yield immediately, not after repeated occurances, but the first time. It will yield plastically, unless you yield it above the ultimate tensile stress of the material, in which case it will break, known as ultimate failure.
If you stress a spring below the yield stress, even at 99% of the yield stress, it will not yield plastically. However, if you stress it at that high a level, enough times in cyclic stress (not static), it will eventually break via *fatigue*, without ever exceeding the ultimate tensile strength of the material. Steels have a "fatigue limit", a stress where, if you never exceed that stress, the steel will not fail in fatigue, ever. This fatigue limit stress is far below the yield strength, I'm gonna pull a number out of thin air and say 50% yield, but I've forgotten where that actually is, and it varies by steel composition and processing. Most steel things where weight matters, like cars and bicycles, will be stressed over the fatigue limit, because if below the fatigue limit, the part would be too heavy, and the part does not need to last forever, just the life of the vehicle. Safety critical parts will have additional safety margin to prevent "catastrophic" (sudden and without warning) failure, or a "graceful degradation mode" with plenty of warning. Coil springs on old cars would often fail in fatigue after a time, usually at the end, a piece would snap off, that corner of the car would sag, but keep on working, but by shortening the spring, the stresses are raised, so a year later another piece would snap off, the car would sag lower, but not fail in an unsafe way, and continue to happen until the car eventually is riding on the bump stops. Leaf springs too, but on any of the leaves *except* the top leaf that holds the axle in place, that one cannot fail or the car or truck loses control.
Aluminum does not have a fatigue limit; If you stress it enough times in cyclic loading, it will fail. At a low enough stress, that make take ten million years, but it will happen eventually. This is why aluminum parts need to be designed more stiff than steel to hold up in fatigue. This works well for a bike that you want stiff in torsion, like a road race bike for fast sprints, or a loaded touring bike, or a suspension mountain bike. But under other conditions, in general, rigid frame aluminum bikes ride stiffer than other materials.
Titanium has fantastic fatigue strength, and is half the weight of steel. It makes excellent bike frames that ride well. You can make auto springs from titanium, they are just expensive, so the purview of race cars. You can make titanium foil camera shutters that wind around a spool and unwind straight, repeatedly; A Nikon F(1) had a ball bearing and titanium foil focal plane shutter that was good for a minimum of 100,000 cycles.
The elastic ("Young's") modulus or a material (defined as "stress over strain"), i.e., how much it stretches or flexes elastically below the yield stress, in general, does not change within a "family" of materials; Low strength steel has the same stiffness as high strength steel, however the latter can be stressed higher before yielding or breaking. Steel has about 3X the elastic modulus of aluminum. There can be relatively small changes to this due to alloying elements. This has been doctrine for forever. *However*, there have been some very recent developments in "nano-structured High Modulus Steel" that breaks this rule, and is 25% higher elastic modulus than steels that have been produced in the past, and is also excellent strength and ductility (spread between yield and ultimate strengths). This is especially good news for part designs limited by compressive buckling, as that is NOT a factor of the part strength, but the part stiffness, the latter being a function of a) the geometric stiffness, i.e., the geometric section modulus, b) the unconstrained column length, c) the end fixing conditions, and d) the material elastic modulus.
(to be continued if I think of more relevant things)
#39
Senior Member
I did have half of this written up last night heres a link on chromo and embrittlemenr https://masteel.co.uk/news/chromium-...20are%20formed.
https://f3timbertech.com/the-effects...%20of%20cracks.
Also says somewhere in there materials that are highly ductile are more likely to have nitrogen embrittlement
Thats coatings used om fasteners but as the top link proves it happens the coating can be used for the chromo too. I think its more a newer thing like epoxy coatings can be a good barrier but i doubt youd be able to find a bath big enough to zinc plate the bike even though you probably wouldnt want to
Also yes purging does protect during welding, it stops oxizidation from forming during welding
As i said before chromium in general is a brittle material granted harder than steel but not usable for structures due to if their struck its certain a failure will happen.
Also i know this is strange saying all this even though no one has had any real problems but is anyone actually able to test the nitrogen levels in their bike composition to confirm no embrittlement hasnt taken place
i did have another link ill have to find it
https://f3timbertech.com/the-effects...%20of%20cracks.
Also says somewhere in there materials that are highly ductile are more likely to have nitrogen embrittlement
Thats coatings used om fasteners but as the top link proves it happens the coating can be used for the chromo too. I think its more a newer thing like epoxy coatings can be a good barrier but i doubt youd be able to find a bath big enough to zinc plate the bike even though you probably wouldnt want to
Also yes purging does protect during welding, it stops oxizidation from forming during welding
As i said before chromium in general is a brittle material granted harder than steel but not usable for structures due to if their struck its certain a failure will happen.
Also i know this is strange saying all this even though no one has had any real problems but is anyone actually able to test the nitrogen levels in their bike composition to confirm no embrittlement hasnt taken place
i did have another link ill have to find it
Chrome has a very strong affinity to bonding with carbon to form chromium carbides, which, unfortunately, often grow to a large grain size and thus act as a failure site. On high carbon (martensitic) stainless steels used commonly in kitchen knives (X50Cr15MoV), under close inspection it is common to find tiny coarse "pits" in the sides, breakout of chromium carbides from the finish grinding, and tiny semi-circular breakouts along the sharpened edge (poor "edge stability"), from breakout of same under any lateral edge stress.
Better quality knives control the chrome content to just barely "saturate" the iron for corrosion resistance, but not a bit more, to prevent chromium carbide formation. This forces the excess carbon not in solution with the iron, to, with sufficient vanadium, form vanadium carbides, which are of a very fine grain structure and size, and very hard, in fact harder than typical aluminum oxide sharpening stones, thus requiring carborundum (silicon carbide) stones or diamond plates. However, if you create this perfect alloy mix, melt and pour it into an ingot mold, it doesn't work; The cooling boundary as it progresses inward in all directions, "pulls" chrome out from just ahead of the solidifying boundary and you get the undesirable chrome carbides. So for this to work, you need Powder Metallurgy process; You spray this molten metal out into gas jets, not unlike a paint spray gun, and very tiny droplets of this steel instantly solidify in perfect homogeneity, and drop into a bin. Then you put the powder in a machine, and press it hard in all directions, then heat it to the forging temperature, Hot Isostatic Pressing (HIP) and the particles all bond. Then you roll the steel and cut into parts. Fantastic hardness (edge retention), toughness (edge stability), and corrosion resistance. But *expensive*, not due to any alloying elements, but the PM process. Like 10X the material cost.
"Conventional" ingot steels are usually a tradeoff between hard but brittle, or tough but soft. But there are a couple outliers. One is 14C28N, developed by Sandvik; 0.62% carbon, 14% chromium, and 0.11% nitrogen; No molybdenum, no vanadium. Excellent hardness, and surprise, 6X the toughness of X50Cr15MoV, and 8.8/10 rating in corrosion resistance, almost as good as a saltwater dive knife. And 1/10 the material cost of PM steels. Is it as tough as good bike frame tubing? I don't know, but I question the pure acceptance of nitrogen as embrittling, in all steels, at all quantities. GM is gas nitriding all their truck brake discs for both corrosion resistance and abrasion durability.
Materials that are highly ductile are more likely to have nitrogen embrittlement.
From your link:
Unlike some other metals, chromium does not experience hydrogen embrittlement, but it does suffer from nitrogen embrittlement. Nitrogen embrittlement is a reaction with nitrogen in the air and brittle nitrides are formed.
https://link.springer.com/article/10.1007/BF02645939
Last edited by Duragrouch; 05-19-24 at 05:01 AM.
#40
Randomhead
Join Date: Aug 2008
Location: Happy Valley, Pennsylvania
Posts: 24,459
Mentioned: 0 Post(s)
Tagged: 0 Thread(s)
Quoted: 4 Post(s)
Liked 3,758 Times
in
2,558 Posts
There are a lot of wrong assertions in this thread, and I'm not sure at all why we're talking about springs. I think of all the things that have caused people to be confused about ductile metals, paper clips are the worst. And springs are just fancy paper clips. Bicycle frames are so much simpler than a spring.
Likes For unterhausen:
#41
Newbie
There are a lot of wrong assertions in this thread, and I'm not sure at all why we're talking about springs. I think of all the things that have caused people to be confused about ductile metals, paper clips are the worst. And springs are just fancy paper clips. Bicycle frames are so much simpler than a spring.
That was supposed to be quoted from the website i linked regarding chromium & embrittlement
Im also going to add off another thread ive been reading sometimes manafacturers cut costs and buy cheap components etc, also i doubt there would actually testing regarding this for bike frames as its classed as a consumable product, most people buy a bike for the summer use a handfull of times and leave it, so i doubt any testing will have actually taken place as the cost/ reward isnt worth it
it was also mentioned on that post that if the bike fails most people wont know about warranty so they wont try to claim and it had figures on the post here;
https://www.bikeforums.net/general-cycling-discussion/1174431-cracks-rim.html
The reply was by wilfred laurier
Thats what also leads me to believe no testing is done on this even on cracked frames
Last edited by Jordanjw; 05-19-24 at 08:42 AM.
#42
Randomhead
Join Date: Aug 2008
Location: Happy Valley, Pennsylvania
Posts: 24,459
Mentioned: 0 Post(s)
Tagged: 0 Thread(s)
Quoted: 4 Post(s)
Liked 3,758 Times
in
2,558 Posts
Usually, bike failures are caused by some pretty prosaic things. Badly drawn tubes, poorly extruded rims, badly performed welds, that sort of thing. In 130 years of building bike frames, the welding processes have been pretty well worked out. Even crummy bikes have thin tubes, bad welding shows up sooner or later. Properly welded bike frames never break at a weld. I have rideable bikes that are almost 50 years old that are still going strong. There just aren't any problems with the welding processes used to make bike frames. And they don't get softer over time.
Last edited by unterhausen; 05-19-24 at 01:00 PM.
Likes For unterhausen:
#43
Senior Member
Join Date: Apr 2011
Posts: 7,301
Mentioned: 43 Post(s)
Tagged: 0 Thread(s)
Quoted: 4552 Post(s)
Liked 1,695 Times
in
1,113 Posts
Steel frames can and do wear out from fatigue. And not at the join. Often several inches back on the right chainstay.
But until they fail, they don't feel different or flex differently.
But until they fail, they don't feel different or flex differently.
#44
Randomhead
Join Date: Aug 2008
Location: Happy Valley, Pennsylvania
Posts: 24,459
Mentioned: 0 Post(s)
Tagged: 0 Thread(s)
Quoted: 4 Post(s)
Liked 3,758 Times
in
2,558 Posts
We have different definitions of "wear out." A frame with any size fatigue crack is a failure. I edited my post to make it a bit more clear what I mean.
Likes For unterhausen:
#45
Senior Member
There are a lot of wrong assertions in this thread, and I'm not sure at all why we're talking about springs. I think of all the things that have caused people to be confused about ductile metals, paper clips are the worst. And springs are just fancy paper clips. Bicycle frames are so much simpler than a spring.
Regarding other posts, bike frames are tested more now than they used to be, it's cheaper than a recall or liability suit. Both ultimate loading, and high-cycle fatigue loading using servo-hydraulic equipment. I think some of the brand-x bikes that are a dead copy of an established bike in design, material, and weld specs, will try to get away with no testing. However there was one thread asking about a low-priced folding bike, and the design flaws were obvious to me, I recommended against, and within a week the OP had posted of reviews where purchasers had frames break completely in half where I said they would, after little use. Astonishing that bike made it to production.
My early '00s folding bike had a fatigue crack in the frame. Later bikes of the same model showed countermeasures for that. Now, there are videos online for that same company, showing servo-hydraulic fatigue test rigs in operation.
Custom frame makers don't do this, but design and make frames based on established practices and experiences. I think in designing sailboats before computer analysis, this was known as "scantlings".
Last edited by Duragrouch; 05-19-24 at 06:02 PM.
Likes For Duragrouch:
#46
Randomhead
Join Date: Aug 2008
Location: Happy Valley, Pennsylvania
Posts: 24,459
Mentioned: 0 Post(s)
Tagged: 0 Thread(s)
Quoted: 4 Post(s)
Liked 3,758 Times
in
2,558 Posts
Regarding other posts, bike frames are tested more now than they used to be, it's cheaper than a recall or liability suit. Both ultimate loading, and high-cycle fatigue loading using servo-hydraulic equipment. I think some of the brand-x bikes that are a dead copy of an established bike in design, material, and weld specs, will try to get away with no testing. However there was one thread asking about a low-priced folding bike, and the design flaws were obvious to me, I recommended against, and within a week the OP had posted of reviews where purchasers had frames break completely in half where I said they would, after little use. Astonishing that bike made it to production.
#47
Senior Member
Join Date: Apr 2011
Posts: 7,301
Mentioned: 43 Post(s)
Tagged: 0 Thread(s)
Quoted: 4552 Post(s)
Liked 1,695 Times
in
1,113 Posts
Well, at least there doesn't seem to be anyone that believes that welding can make steel less rigid.
#48
Newbie
but the fact nitrogen embrittlement only happens after welding has taken place not during welding.
which means no one has taken the point if everyone pointing to purging during welding?
the air from the environment is seeping into your bike frame whether you like it or not.
this includes steel and chro/mo types and not aluminium
ill add this a test someone did on embrittlement on 4130 steel Embrittlement of 4130 steel by low-pressure gaseous hydrogen | Semantic Scholar
just to clarify, after reading embrittlement is still not fully understood by experts therefore information is a bit scarce on certain metals or subjects
which means no one has taken the point if everyone pointing to purging during welding?
the air from the environment is seeping into your bike frame whether you like it or not.
this includes steel and chro/mo types and not aluminium
ill add this a test someone did on embrittlement on 4130 steel Embrittlement of 4130 steel by low-pressure gaseous hydrogen | Semantic Scholar
just to clarify, after reading embrittlement is still not fully understood by experts therefore information is a bit scarce on certain metals or subjects
Last edited by Jordanjw; 05-19-24 at 11:23 PM.
#49
Senior Member
This thread isn't really about bike failures, and people keep trying to make it about failures. Go read the first post again. If we open it up to failures, then there is a wide world of problems to discuss. It seems to me that it got into failures as an obfuscation technique because people still wanted to poke at the idea that bikes get softer due to poor welding technique. Of course, this thread would have died a long time ago if people hadn't tried to change the subject multiple times. Tbh, I don't think any of it is particularly important for framebuilders and it should be obvious I'm annoyed that non-framebuilders are keeping it going.
I can clearly remember, in my early teens, long before I even thought it a possibility that I could become an engineer (I pretty much failed high school, and then I worked blue collar, that sucked), my dad was telling me about Young's modulus of elasticity (in general, not how to do calculations), and values for different materials, and implications. Ten years later in college ME331 mechanics of materials, it really started to make sense. Now, I have FEA on the brain, I can see stiffness in my head. No use. Retired. I try to pass on the knowledge when I can.
#50
Randomhead
Join Date: Aug 2008
Location: Happy Valley, Pennsylvania
Posts: 24,459
Mentioned: 0 Post(s)
Tagged: 0 Thread(s)
Quoted: 4 Post(s)
Liked 3,758 Times
in
2,558 Posts
Hydrogen embrittlement is definitely something that welders worry about and take steps to avoid. I haven't seen evidence that there is a widespread issue with it in framebuilding. Tig welded 4130 has been used in bicycle framebuilding since the mid '80s. I'm pretty sure everyone has a pretty good handle on the processes by now, and the information about how to weld it correctly is widely available. The welding industry is pretty good at publishing good information and sponsoring research.
From what I have seen looking at bike failures, there are far easier ways to get a bike to fail than the joining process. Lots of bikes are designed by non-engineers who have very little clue about fatigue failures, and even engineers can fail to properly take fatigue failure into account. We really couldn't cover all the different ways that bikes can fail in one thread. It would be an amorphous mess of very little utility.
Likes For unterhausen: