Cargo build
#26
Newbie
Thread Starter
7018s for me 6013's will hold but im just making sure, if someone was to crash into me the frame wouldn't budge and also my plant / equipment is protected
Likes For Jordanjw:
#27
Newbie
Thread Starter
build list with some components;
frame bed 50x50x5mm box s235 steel
frame bike 38.1mm x 3mm tube - mild steel
headtube or headset as above but 2mm steel - cane creek 40 ec34 1 1/8th threadless headset - pipe will be 34.1mm but will drill out for 34mm
seat post 31.7mm x 3.2mm mild steel for 25mm seatpost may need spacers as pipe i.d is 25.3mm
bottom bracket 44.4mm x1.6mm tube - will be drilled down to 41mm also will be reinforced upto 5mm possibly 3 - shimano ultegra sm-bb72 press fit bb
front wheels bmw weinmann 48 spoke rim 35mm wide - will be spoking my own wheels yet to decide on spoke wont be using j spoke possibly straight
rear wheel - dillenger pas system 36 spoke - will be emailing dillenger about possibility for 48 h motor
this covers main points obviously components like brakes and tyres arent covered as i need to ensure im able to build the main bike itself along with crank and headset etc.
some minor changes also to the bed overall length is 1080 x 520 mm - actual loading dimensions are 980 x 520 mm
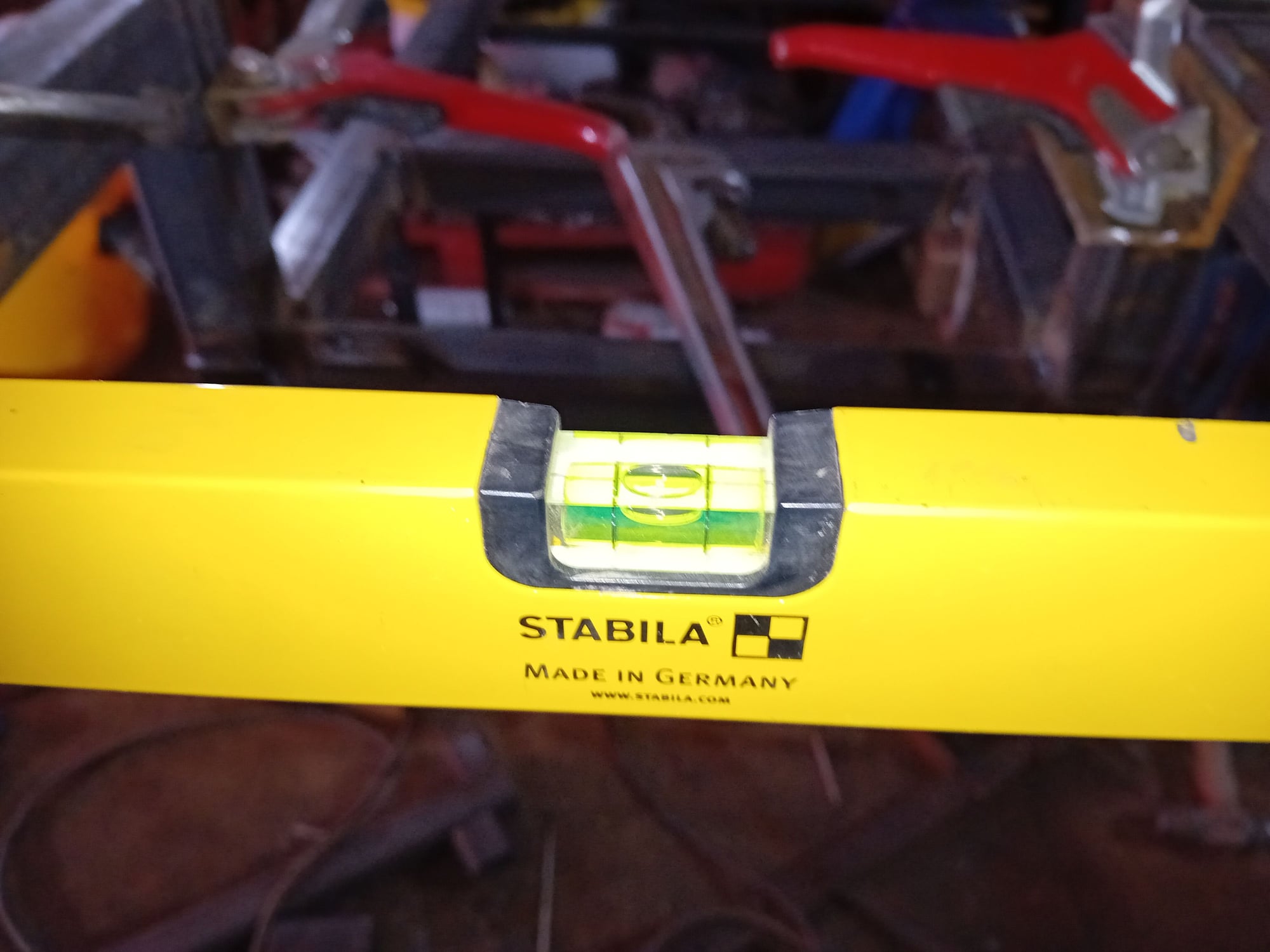
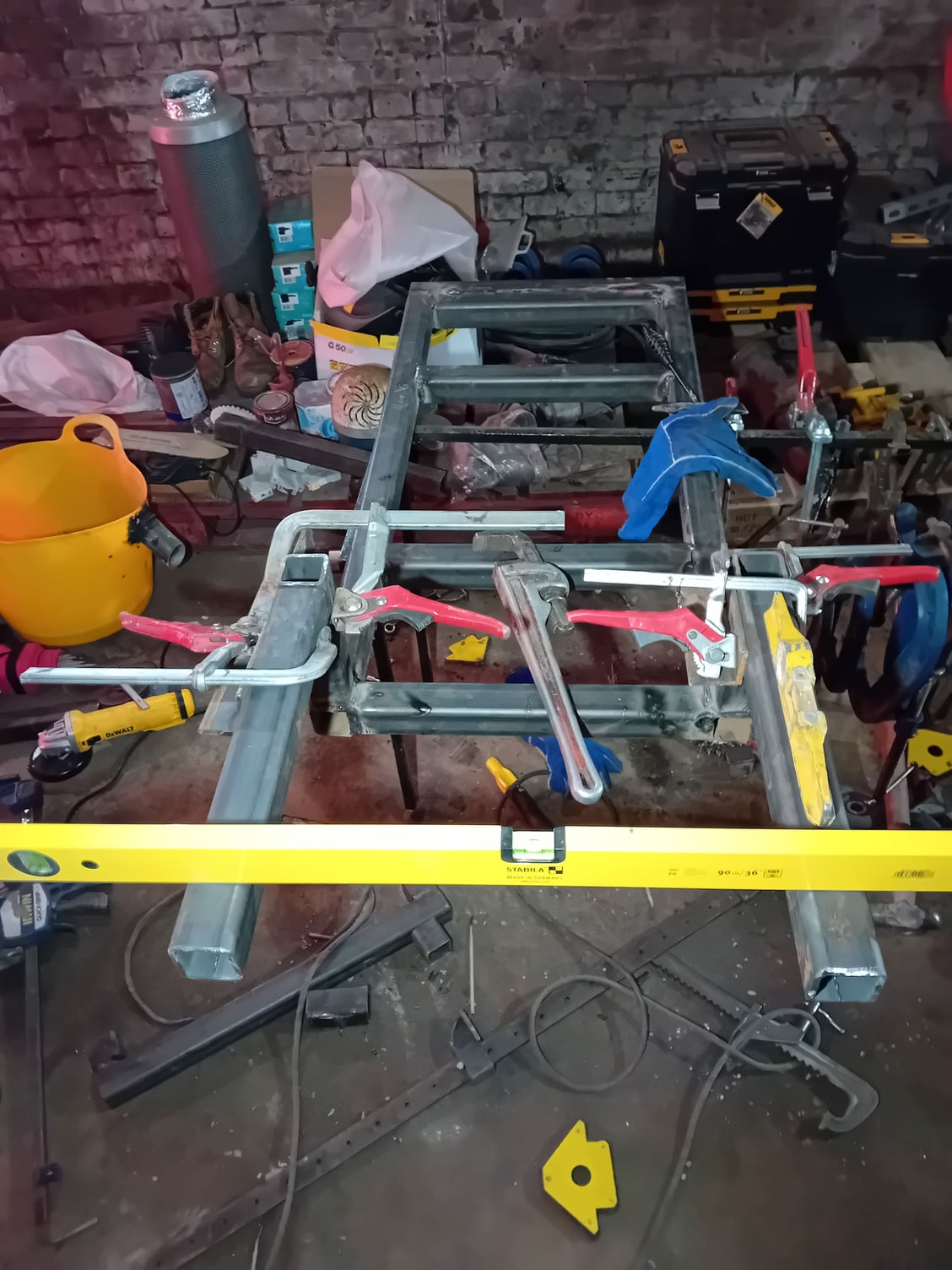
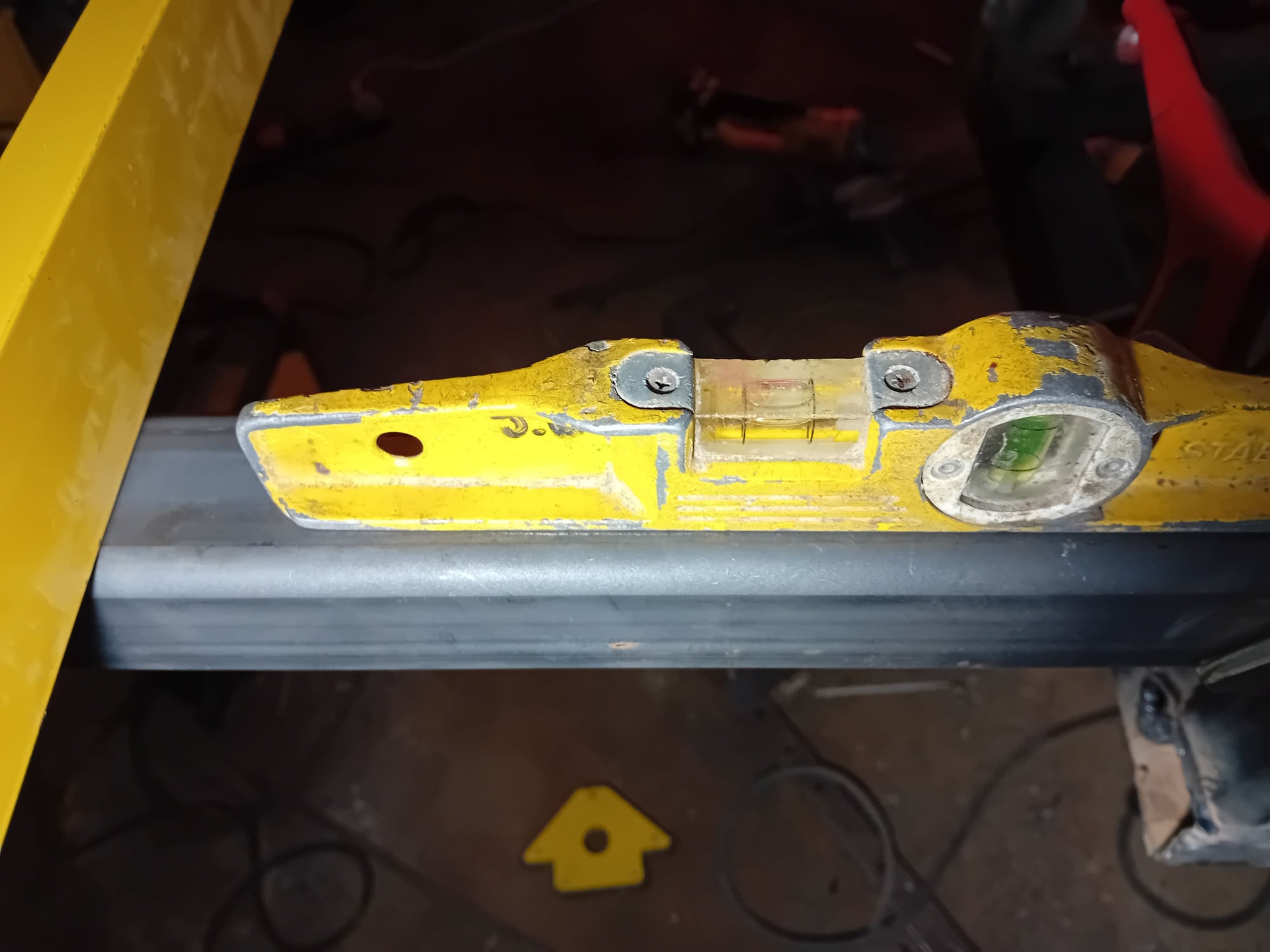
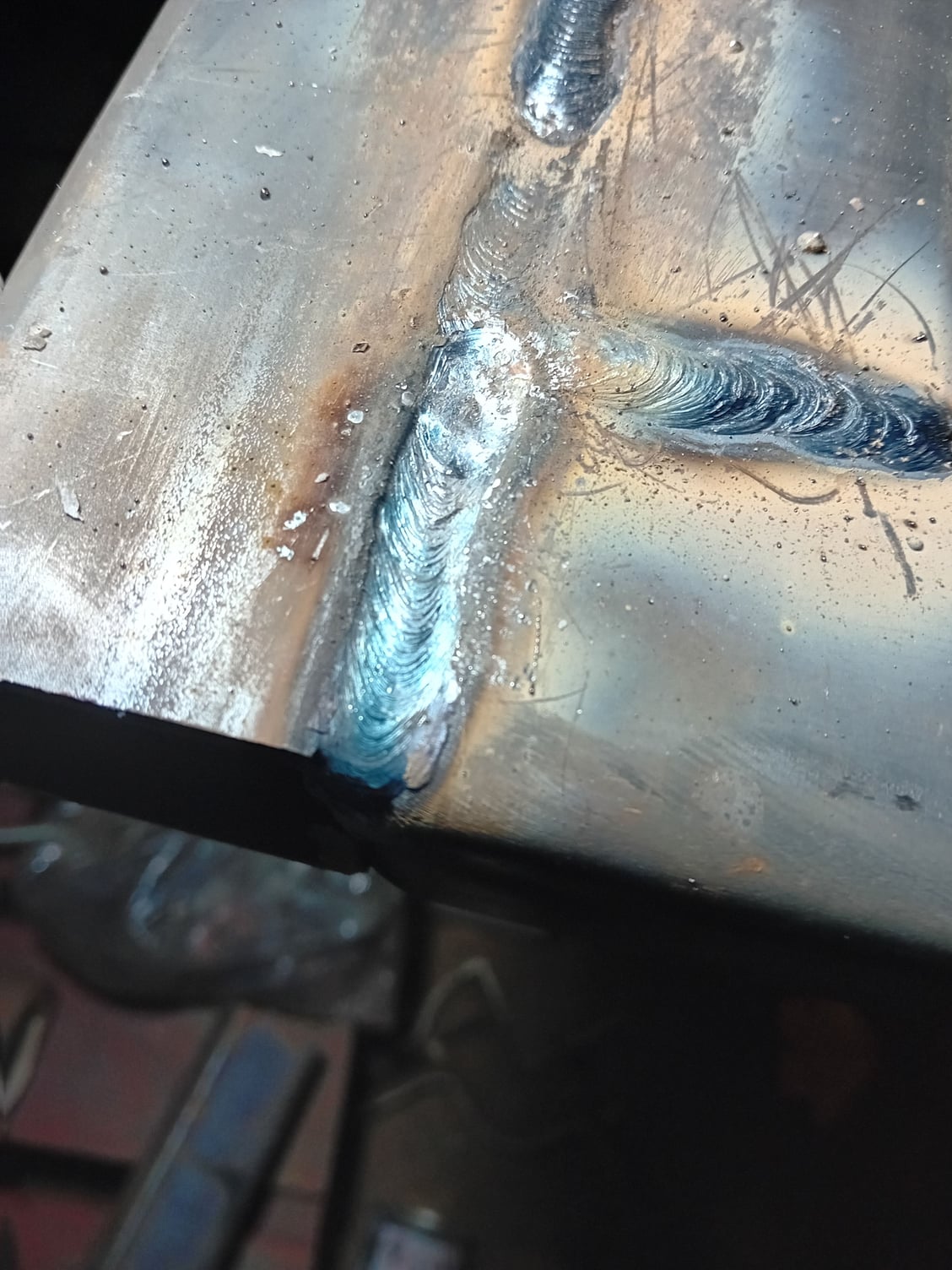
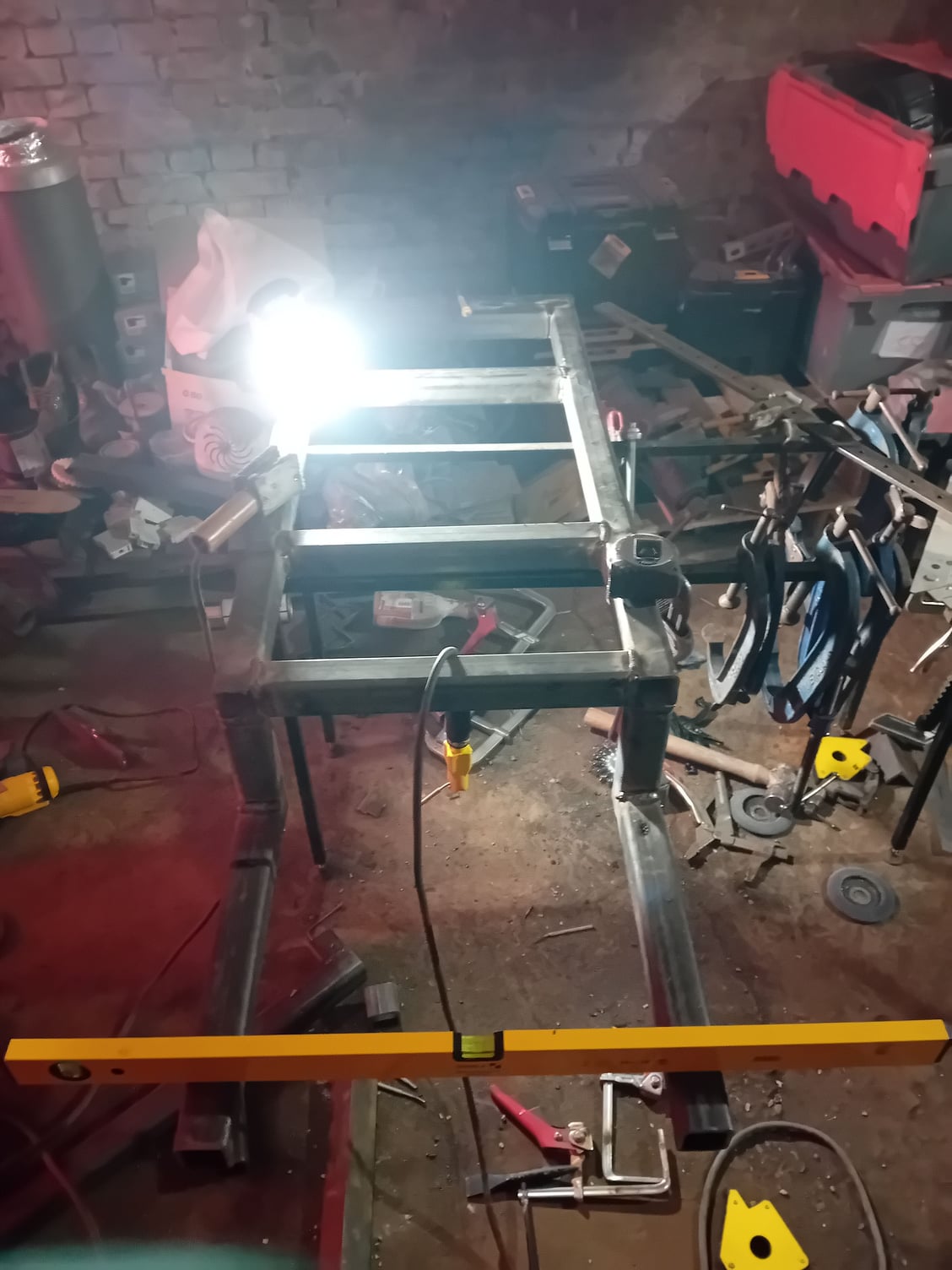
excuse the lighting and setup as im waiting for a electric meter install that is overdue, working from a generator & portable light which isn't great also haven't got a real workbench as was waiting for the electric before commencing with this
also the box was v prepped before welding - root or filler then capped will be ground flat with box frame - this is why you may see some undercut but this wont effect the quality of the final product also haven't took time to really clean slag from weld as welding is still taking place this will be done before painting
also the reason for it being so heavy duty is to hold the weight needed without deflection i said 400kg load but that is a bit of an exaggeration it will more than likely be 250kg to 300kg - also while i was working on a cargo bike before i had 4 crashes so i don't expect people to be considerate especially in London so if someone does end up crashing into me my bike will be fine and their car will bear most of the damage
frame bed 50x50x5mm box s235 steel
frame bike 38.1mm x 3mm tube - mild steel
headtube or headset as above but 2mm steel - cane creek 40 ec34 1 1/8th threadless headset - pipe will be 34.1mm but will drill out for 34mm
seat post 31.7mm x 3.2mm mild steel for 25mm seatpost may need spacers as pipe i.d is 25.3mm
bottom bracket 44.4mm x1.6mm tube - will be drilled down to 41mm also will be reinforced upto 5mm possibly 3 - shimano ultegra sm-bb72 press fit bb
front wheels bmw weinmann 48 spoke rim 35mm wide - will be spoking my own wheels yet to decide on spoke wont be using j spoke possibly straight
rear wheel - dillenger pas system 36 spoke - will be emailing dillenger about possibility for 48 h motor
this covers main points obviously components like brakes and tyres arent covered as i need to ensure im able to build the main bike itself along with crank and headset etc.
some minor changes also to the bed overall length is 1080 x 520 mm - actual loading dimensions are 980 x 520 mm
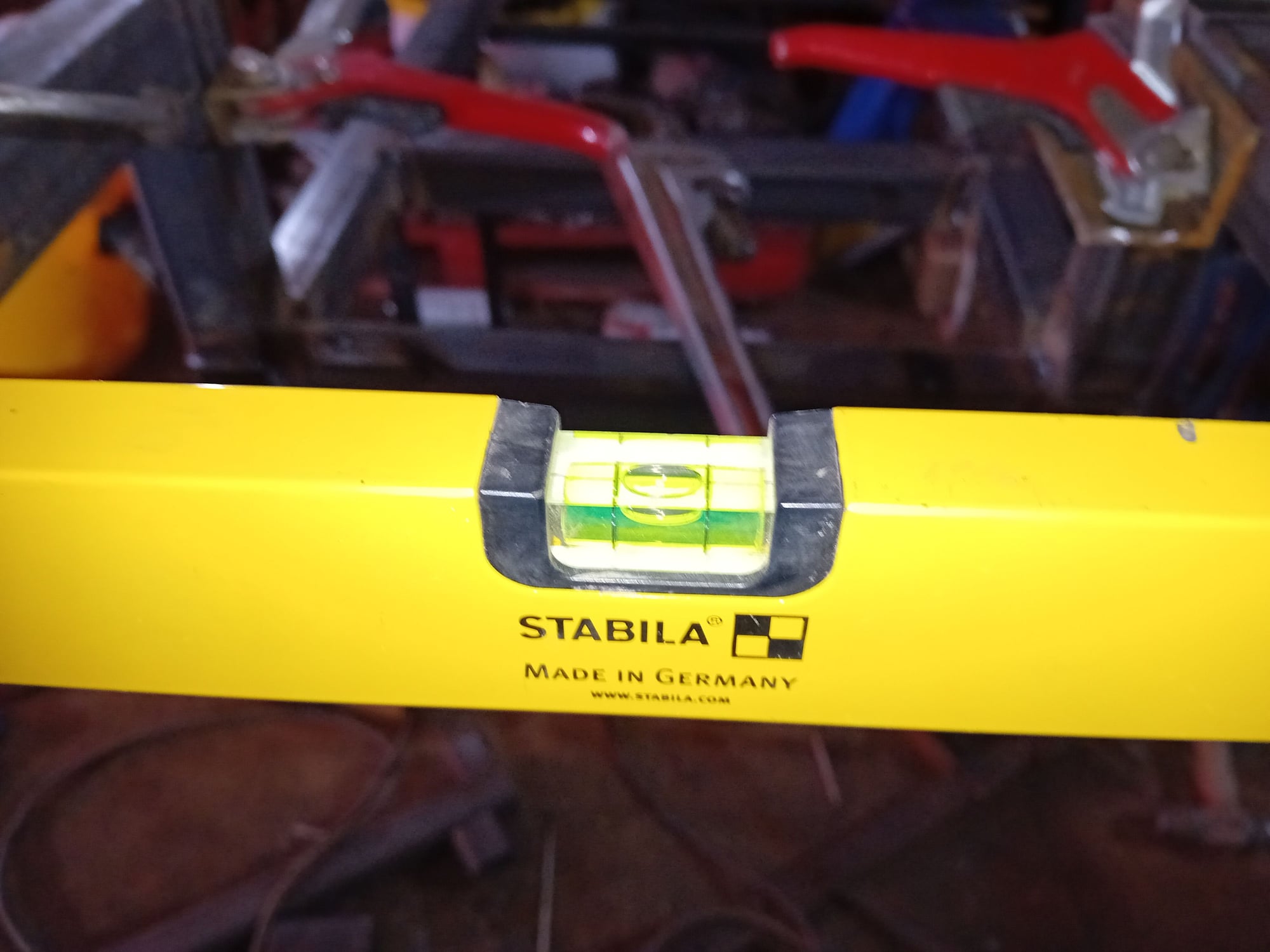
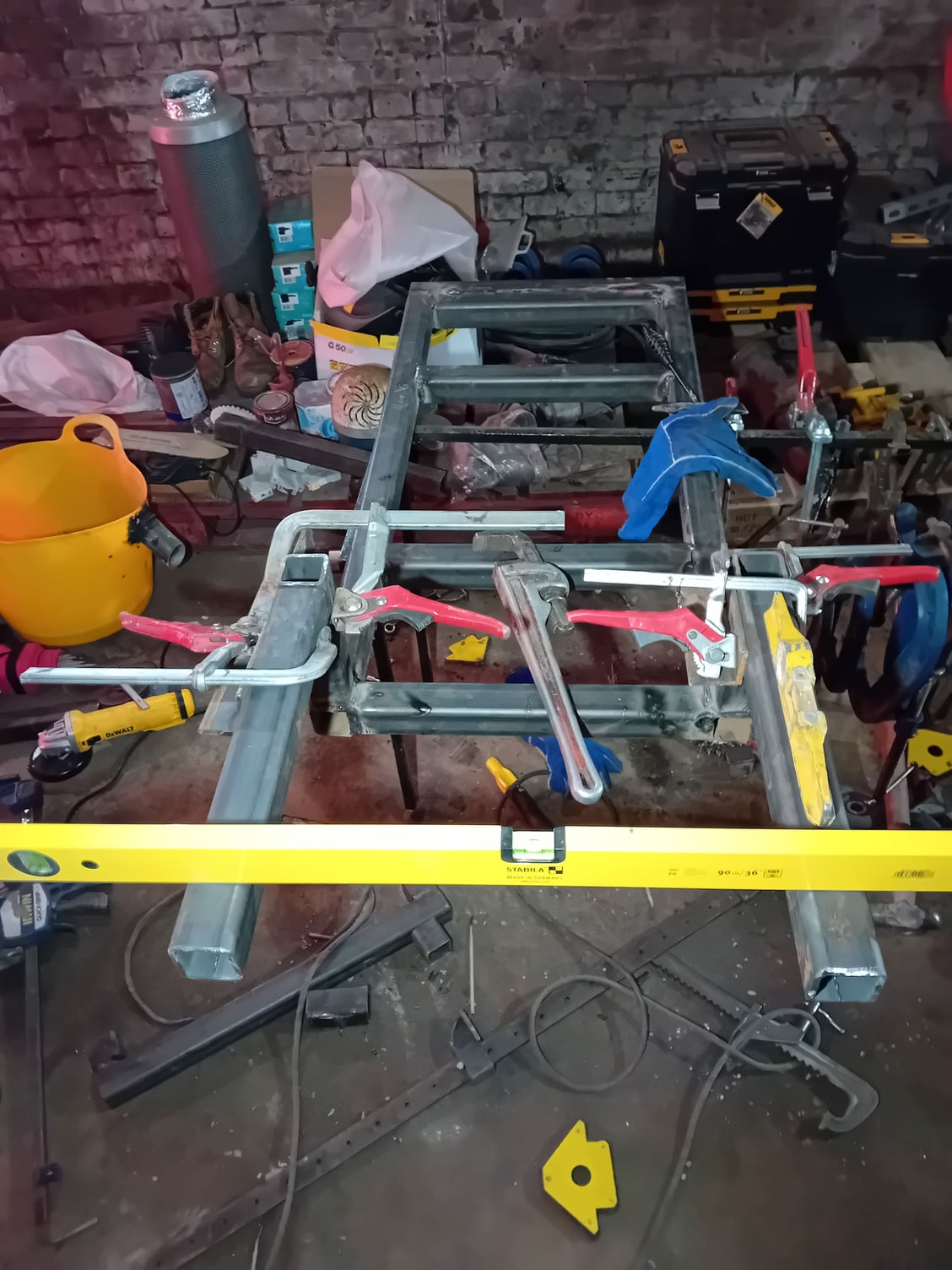
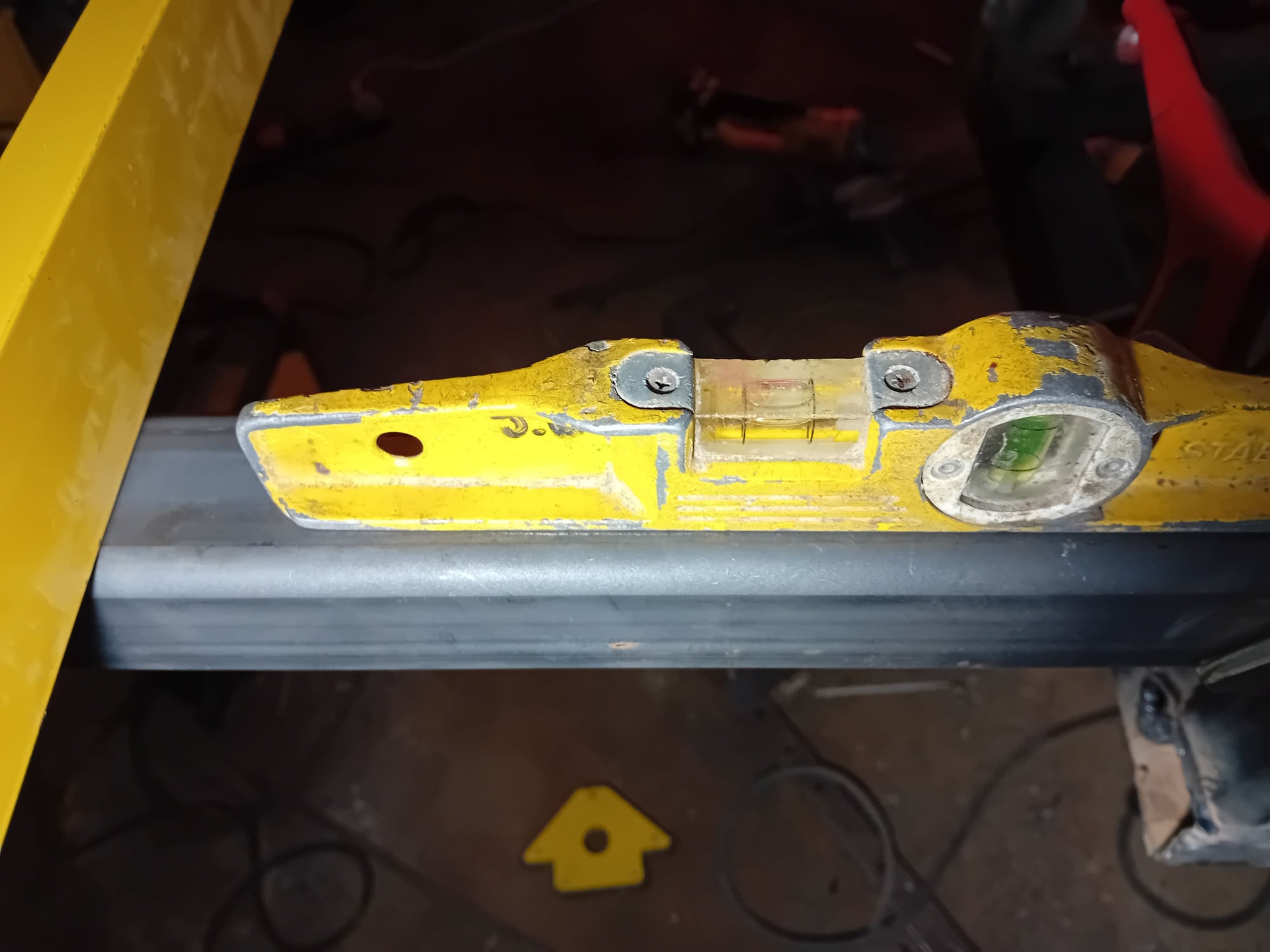
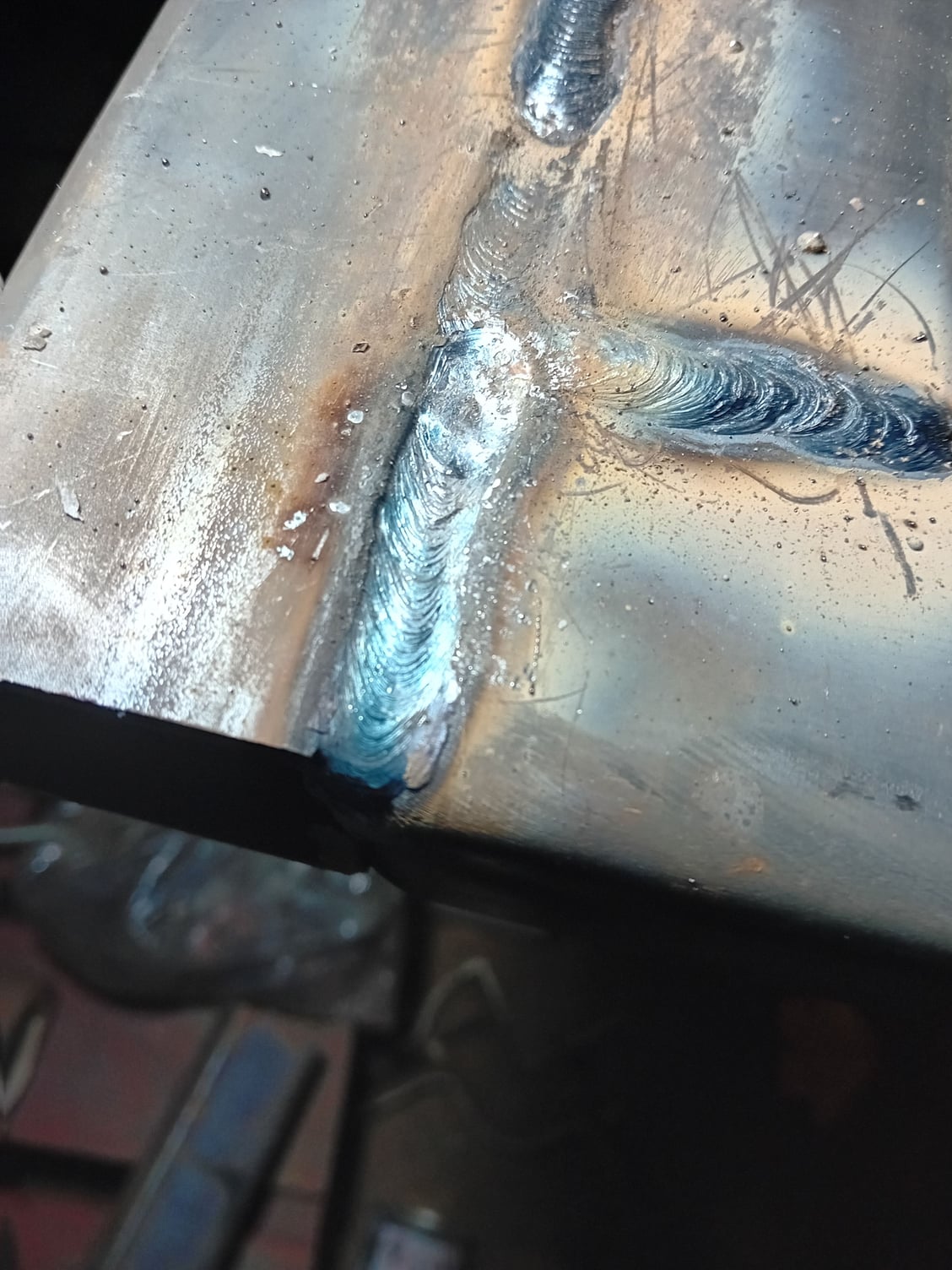
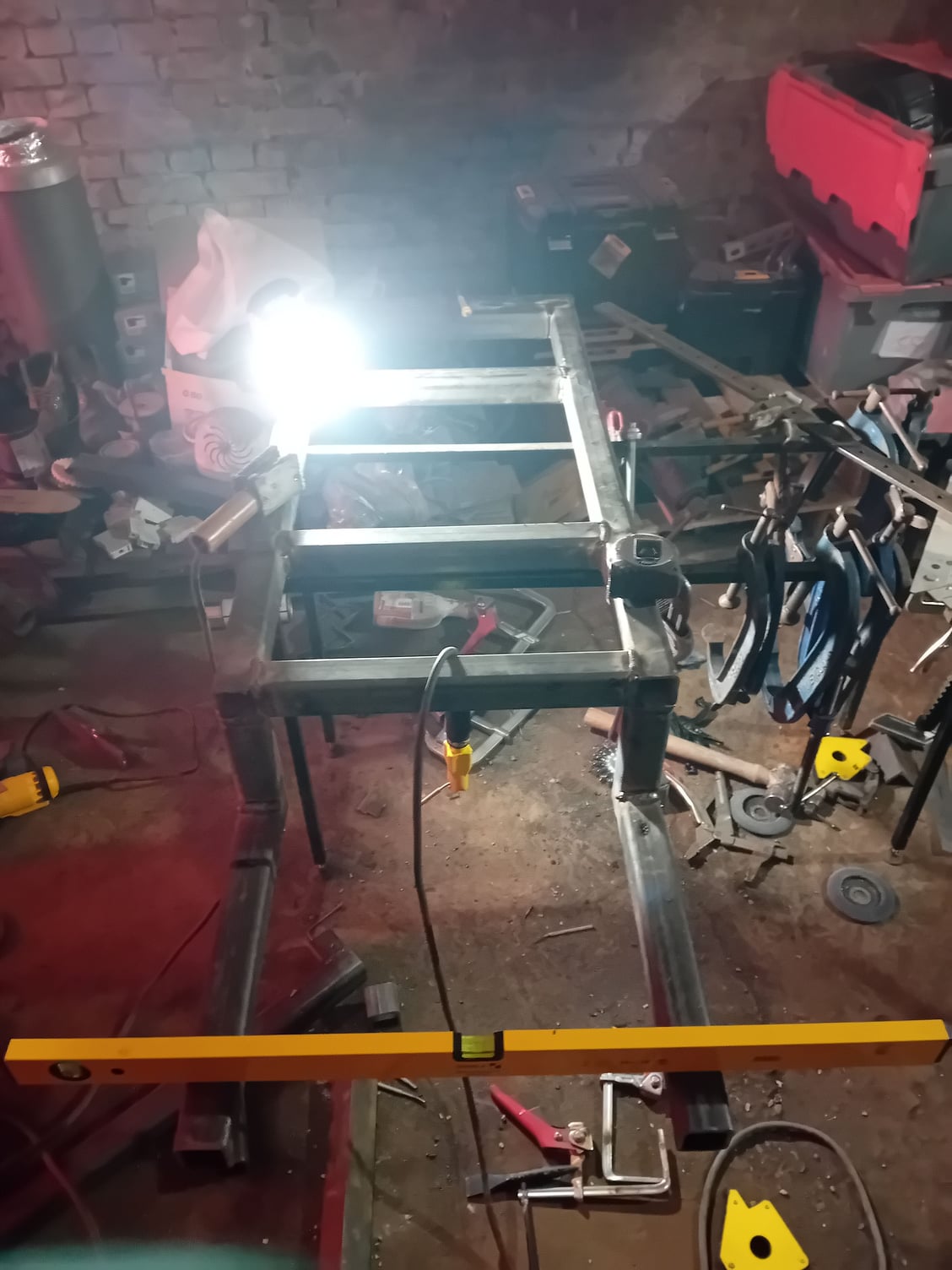
excuse the lighting and setup as im waiting for a electric meter install that is overdue, working from a generator & portable light which isn't great also haven't got a real workbench as was waiting for the electric before commencing with this
also the box was v prepped before welding - root or filler then capped will be ground flat with box frame - this is why you may see some undercut but this wont effect the quality of the final product also haven't took time to really clean slag from weld as welding is still taking place this will be done before painting
also the reason for it being so heavy duty is to hold the weight needed without deflection i said 400kg load but that is a bit of an exaggeration it will more than likely be 250kg to 300kg - also while i was working on a cargo bike before i had 4 crashes so i don't expect people to be considerate especially in London so if someone does end up crashing into me my bike will be fine and their car will bear most of the damage
Last edited by Jordanjw; 05-09-24 at 01:36 PM.
Likes For Jordanjw:
#28
blahblahblah chrome moly
Join Date: Apr 2009
Location: Seattle
Posts: 2,039
Mentioned: 94 Post(s)
Tagged: 0 Thread(s)
Quoted: 1206 Post(s)
Liked 2,648 Times
in
1,104 Posts
Nobody threads their own bottom bracket, they come with threads. Some people use press-fit BB bearings anyway for various reasons, so do watcha like. Me, I dislike press-fits and would never use one, but that's a debate for another day. If you want to think about using a threaded BB, Paragon makes excellent ones. Get the 1-9/16" (40 mm) OD one, not the 1-1/2" (38 mm), which has thinner walls, not suitable for your joining method. Under $10, which I think is a steal, great quality for the money.
Note, chasing the threads after welding is usually needed due to weld distortion, so you would need to find a bike shop with the taps. They're too expensive to buy to build one frame. But press-fits should have their bore cleaned up after welding too, it might even be more important for a press-fit. Their tolerances need to be tight, and a bad fit can cause squeaking/creaking noises. A tight-fitting heat sink in the BB can help reduce weld distortion though.
Hey to any FBs reading this, if you make welded frames with PF, do they need to be machined after welding or do you keep distortion minimal enough somehow? I've stayed away from them, so zero personal experience. Oh except for eccentric BBs, like on tandems, which I've done a ton of. But those aren't really PF, despite being unthreaded, the insert needs to be able to turn, so they're not that tight of a fit. I use heat sinks on those and they come out very round, but I also have a milling machine that can bore them afterward if needed. I used to make titanium frames that way, BB inside diam was left a little small on purpose, then bored to fit after welding. Best-fitting eccentrics I ever saw. Would be a good way to make a perfect-fit PF, but I don't know if anyone does 'em that way.
#29
Newbie
Thread Starter
Well one way to avoid cracks is use stronger tubing, like 4130. In my experience, CrMo frames are a lot less likely to crack than carbon-steel as long as you don't go too thin. Maybe not if you're sticking to your plan to stick-weld though — I don't know nothin' 'bout that. My welder can do stick but I've never even tried it, not interested, 'cuz I'm a fussy/finicky type, I need my welds to look super sanitary.
Nobody threads their own bottom bracket, they come with threads. Some people use press-fit BB bearings anyway for various reasons, so do watcha like. Me, I dislike press-fits and would never use one, but that's a debate for another day. If you want to think about using a threaded BB, Paragon makes excellent ones. Get the 1-9/16" (40 mm) OD one, not the 1-1/2" (38 mm), which has thinner walls, not suitable for your joining method. Under $10, which I think is a steal, great quality for the money.
Note, chasing the threads after welding is usually needed due to weld distortion, so you would need to find a bike shop with the taps. They're too expensive to buy to build one frame. But press-fits should have their bore cleaned up after welding too, it might even be more important for a press-fit. Their tolerances need to be tight, and a bad fit can cause squeaking/creaking noises. A tight-fitting heat sink in the BB can help reduce weld distortion though.
Hey to any FBs reading this, if you make welded frames with PF, do they need to be machined after welding or do you keep distortion minimal enough somehow? I've stayed away from them, so zero personal experience. Oh except for eccentric BBs, like on tandems, which I've done a ton of. But those aren't really PF, despite being unthreaded, the insert needs to be able to turn, so they're not that tight of a fit. I use heat sinks on those and they come out very round, but I also have a milling machine that can bore them afterward if needed. I used to make titanium frames that way, BB inside diam was left a little small on purpose, then bored to fit after welding. Best-fitting eccentrics I ever saw. Would be a good way to make a perfect-fit PF, but I don't know if anyone does 'em that way.
Nobody threads their own bottom bracket, they come with threads. Some people use press-fit BB bearings anyway for various reasons, so do watcha like. Me, I dislike press-fits and would never use one, but that's a debate for another day. If you want to think about using a threaded BB, Paragon makes excellent ones. Get the 1-9/16" (40 mm) OD one, not the 1-1/2" (38 mm), which has thinner walls, not suitable for your joining method. Under $10, which I think is a steal, great quality for the money.
Note, chasing the threads after welding is usually needed due to weld distortion, so you would need to find a bike shop with the taps. They're too expensive to buy to build one frame. But press-fits should have their bore cleaned up after welding too, it might even be more important for a press-fit. Their tolerances need to be tight, and a bad fit can cause squeaking/creaking noises. A tight-fitting heat sink in the BB can help reduce weld distortion though.
Hey to any FBs reading this, if you make welded frames with PF, do they need to be machined after welding or do you keep distortion minimal enough somehow? I've stayed away from them, so zero personal experience. Oh except for eccentric BBs, like on tandems, which I've done a ton of. But those aren't really PF, despite being unthreaded, the insert needs to be able to turn, so they're not that tight of a fit. I use heat sinks on those and they come out very round, but I also have a milling machine that can bore them afterward if needed. I used to make titanium frames that way, BB inside diam was left a little small on purpose, then bored to fit after welding. Best-fitting eccentrics I ever saw. Would be a good way to make a perfect-fit PF, but I don't know if anyone does 'em that way.
My idea was to get some round stock for the id of the pipe for welding and then bore it down after welding
I also had an idea on a milling machine as im able to buy a pillar drill could probably do with one i could run the pillar drill but attach a movable bed onto the existing but obviously id have to account for dimensions etc
I mean press fit doesnt sound to great in my honest opinion but ill just try to make it as tight as possible and could possibly doing with greasing every so often, im just trying to get it done asap and as smooth as possible, thats also why i dont want to go for 4130 im unable to heat treat and probably wont ever be able to as i dont plan on getting an oven or keeping gas
Have you had experience with the belt drive system that is out now instead of a chain system? Ive heard their good but the price is ridiculous compared to a normal chain especially when the chain barely even snaps and even then thats due to poor maintenance
#30
Senior Member
Join Date: Dec 2019
Posts: 972
Mentioned: 3 Post(s)
Tagged: 0 Thread(s)
Quoted: 329 Post(s)
Liked 265 Times
in
214 Posts
BTW I highly recommend this YT channel. Next-level fabrication skills for someone with a pair of flip-flops and a stick welder. Shows what is possible!
https://www.youtube.com/@albertnario4877
#31
Senior Member
Join Date: Dec 2019
Posts: 972
Mentioned: 3 Post(s)
Tagged: 0 Thread(s)
Quoted: 329 Post(s)
Liked 265 Times
in
214 Posts
Well one way to avoid cracks is use stronger tubing, like 4130. In my experience, CrMo frames are a lot less likely to crack than carbon-steel as long as you don't go too thin. Maybe not if you're sticking to your plan to stick-weld though — I don't know nothin' 'bout that. My welder can do stick but I've never even tried it, not interested, 'cuz I'm a fussy/finicky type, I need my welds to look super sanitary.
Nobody threads their own bottom bracket, they come with threads. Some people use press-fit BB bearings anyway for various reasons, so do watcha like. Me, I dislike press-fits and would never use one, but that's a debate for another day. If you want to think about using a threaded BB, Paragon makes excellent ones. Get the 1-9/16" (40 mm) OD one, not the 1-1/2" (38 mm), which has thinner walls, not suitable for your joining method. Under $10, which I think is a steal, great quality for the money.
Note, chasing the threads after welding is usually needed due to weld distortion, so you would need to find a bike shop with the taps. They're too expensive to buy to build one frame. But press-fits should have their bore cleaned up after welding too, it might even be more important for a press-fit. Their tolerances need to be tight, and a bad fit can cause squeaking/creaking noises. A tight-fitting heat sink in the BB can help reduce weld distortion though.
Nobody threads their own bottom bracket, they come with threads. Some people use press-fit BB bearings anyway for various reasons, so do watcha like. Me, I dislike press-fits and would never use one, but that's a debate for another day. If you want to think about using a threaded BB, Paragon makes excellent ones. Get the 1-9/16" (40 mm) OD one, not the 1-1/2" (38 mm), which has thinner walls, not suitable for your joining method. Under $10, which I think is a steal, great quality for the money.
Note, chasing the threads after welding is usually needed due to weld distortion, so you would need to find a bike shop with the taps. They're too expensive to buy to build one frame. But press-fits should have their bore cleaned up after welding too, it might even be more important for a press-fit. Their tolerances need to be tight, and a bad fit can cause squeaking/creaking noises. A tight-fitting heat sink in the BB can help reduce weld distortion though.
Hey to any FBs reading this, if you make welded frames with PF, do they need to be machined after welding or do you keep distortion minimal enough somehow? I've stayed away from them, so zero personal experience. Oh except for eccentric BBs, like on tandems, which I've done a ton of. But those aren't really PF, despite being unthreaded, the insert needs to be able to turn, so they're not that tight of a fit. I use heat sinks on those and they come out very round, but I also have a milling machine that can bore them afterward if needed. I used to make titanium frames that way, BB inside diam was left a little small on purpose, then bored to fit after welding. Best-fitting eccentrics I ever saw. Would be a good way to make a perfect-fit PF, but I don't know if anyone does 'em that way.
Looking at the press-fit shells on Ceeway, I don't think you could ream these anyway because the bearing seat is only cut into the ends. Distortion is usually low because BB shells are so thick and so I reckon they're probably supplied at the exact size and you probably just press the bearings in. A true perfectionist would cut the bearing seats on a mill I suppose after making the frame.
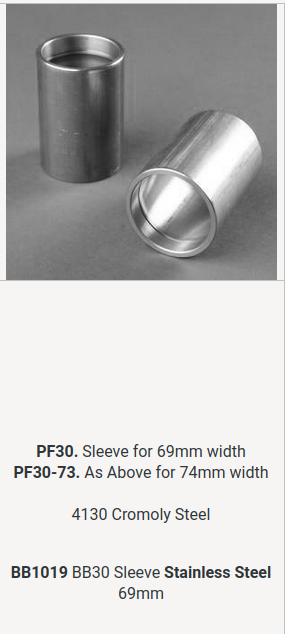
#32
Senior Member
Join Date: Dec 2019
Posts: 972
Mentioned: 3 Post(s)
Tagged: 0 Thread(s)
Quoted: 329 Post(s)
Liked 265 Times
in
214 Posts
I mean press fit doesnt sound to great in my honest opinion but ill just try to make it as tight as possible and could possibly doing with greasing every so often, im just trying to get it done asap and as smooth as possible, thats also why i dont want to go for 4130 im unable to heat treat and probably wont ever be able to as i dont plan on getting an oven or keeping gas
Have you had experience with the belt drive system that is out now instead of a chain system? Ive heard their good but the price is ridiculous compared to a normal chain especially when the chain barely even snaps and even then thats due to poor maintenance
#33
Senior Member
Join Date: Jul 2006
Location: San Jose (Willow Glen) Ca
Posts: 9,919
Bikes: Kirk Custom JK Special, '84 Team Miyata,(dura ace old school) 80?? SR Semi-Pro 600 Arabesque
Mentioned: 107 Post(s)
Tagged: 0 Thread(s)
Quoted: 2368 Post(s)
Liked 2,895 Times
in
1,579 Posts
not a builder yet, but not sure I understand the seat shown....is it supposed to be a semi recumbent design? Not clear to me how the seat as shown works with bottom bracket and crankset location?
__________________
Life is too short not to ride the best bike you have, as much as you can
(looking for Torpado Super light frame/fork or for Raleigh International frame fork 58cm)
Life is too short not to ride the best bike you have, as much as you can
(looking for Torpado Super light frame/fork or for Raleigh International frame fork 58cm)
Likes For squirtdad:
#34
Newbie
Thread Starter
there may be small issues with placement on the drawing, but obviously im going to build it to suit my height so i cant really do this until ive got most of it built
also @ guy if someones wearing flip flops welding it shows they havent learnt the theory side of it, i dont like the sound of skin cancer before im 50 although probably practical its still a big issue in this industry people dont take the cancer side serious, it literally says on the rod packet it causes cancer
also when i learnt to weld i wasnt even allowed to weld until i learnt the theory side, and also most pipefitters / welders wont let you tig weld until you can feed the wire through your fingers, if you mess up their welds then its on them not you as their the competent welder
on the electrodes 6013 is a basic rutile 7018 is a low hydrogen - both are low penetration a rod with high penetration is 6011 but its pointless buying these as a solid root pass with 7018 will be the same aslong as ive prepped correct - also 6011 normally used on pipe so your welding vertical so is harder to weld so on the flat 7018 is fine in this instance - not many people know but 7018 is used for structural vs 6013 is okay for minor repairs but under stress will show cracks
Last edited by Jordanjw; 05-11-24 at 04:28 AM.
#35
Senior Member
Join Date: Aug 2012
Location: Seattle
Posts: 515
Mentioned: 0 Post(s)
Tagged: 0 Thread(s)
Quoted: 106 Post(s)
Liked 145 Times
in
89 Posts
I would have thought 4130/Chromoly would be prefered since it would allow lighter overall structure but perhaps it would be much more expensive and you probably want the thicker walls for stiffness. Nearly all but the very lowest end steel bikes are made from chromoly and it doesn't require heat treatment post weld.
I'm desperately waiting for a full report on how this rides and handles. Please hurry!!
I'm desperately waiting for a full report on how this rides and handles. Please hurry!!
__________________
https://www.flickr.com/photos/54319503@N05/
https://www.draper-cycles.com
https://www.flickr.com/photos/54319503@N05/
https://www.draper-cycles.com
#36
Newbie
Thread Starter
update on this build;
have since welded on the brace for the bike frame, this is also for the crank, also have the backstop on for the bed to stop the load coming back onto me
waiting for monday for a delivery of pipe for continuation on front of bike, will make the front forks etc then work my way to the back

its pretty well balanced as it is i can imagine once everything is on the balance wont be heavier one end than the other
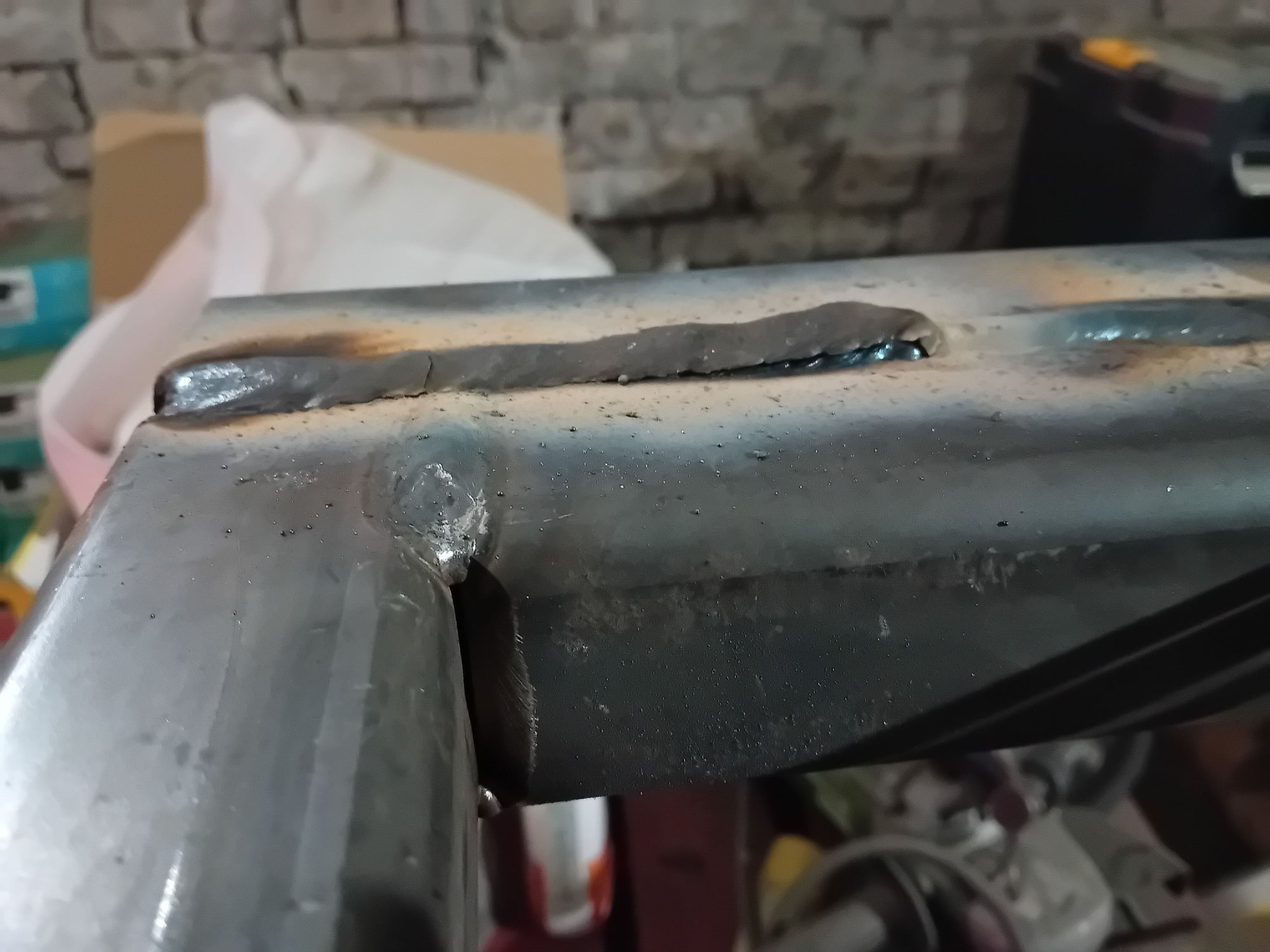
peeling slag is always a good thing
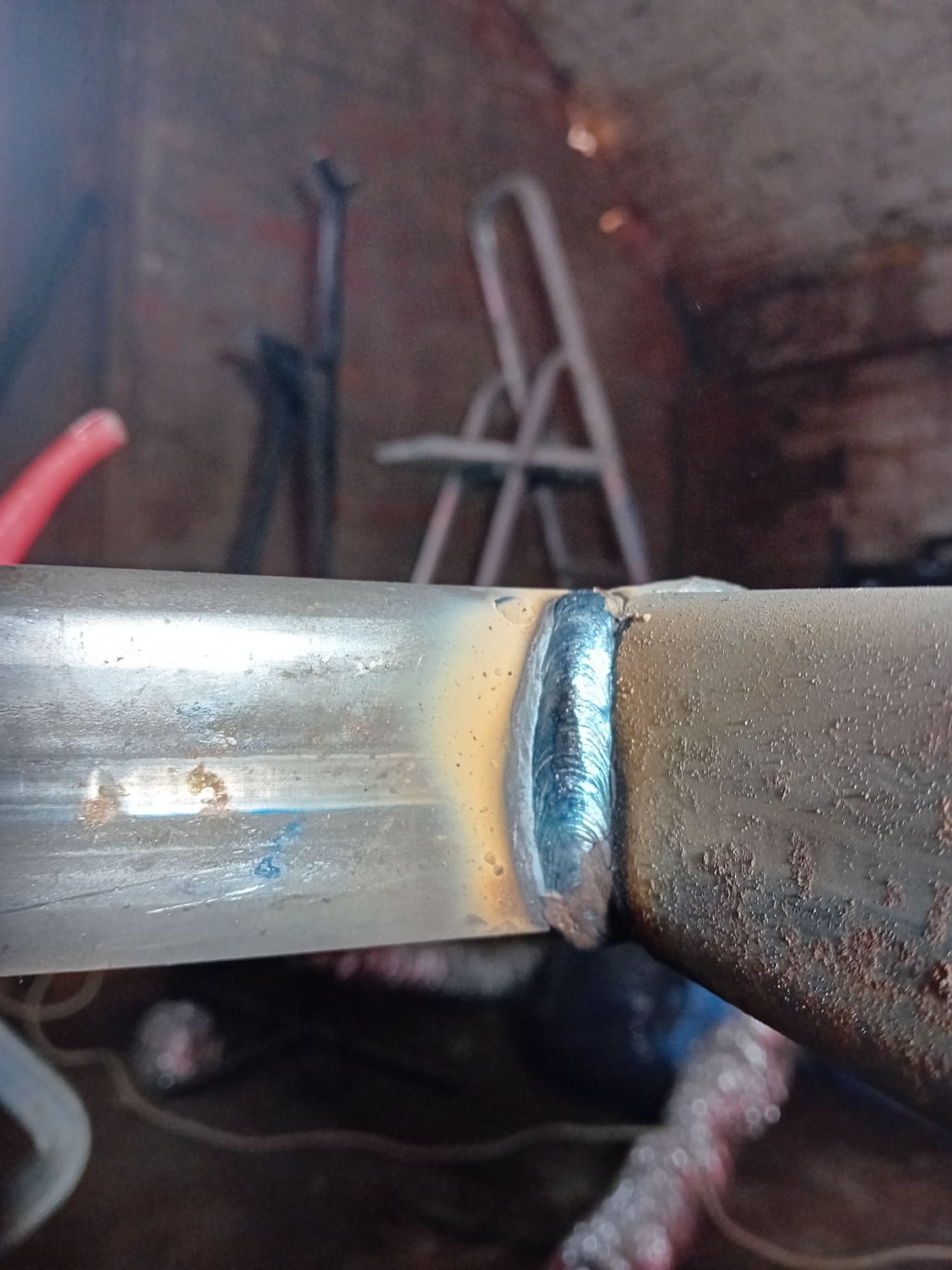
some welds like these were done in position as was to much effort to keep moving the bed around
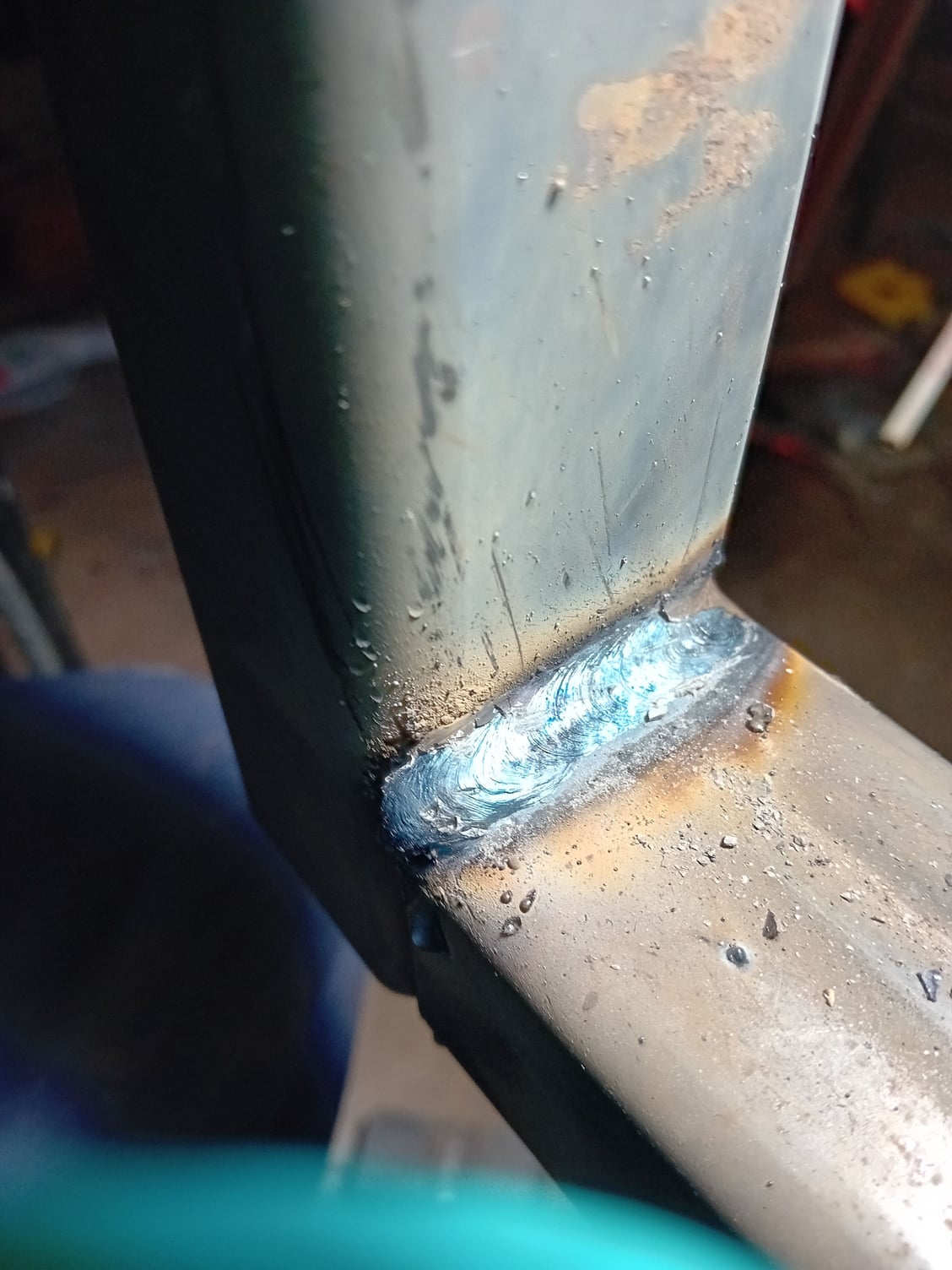
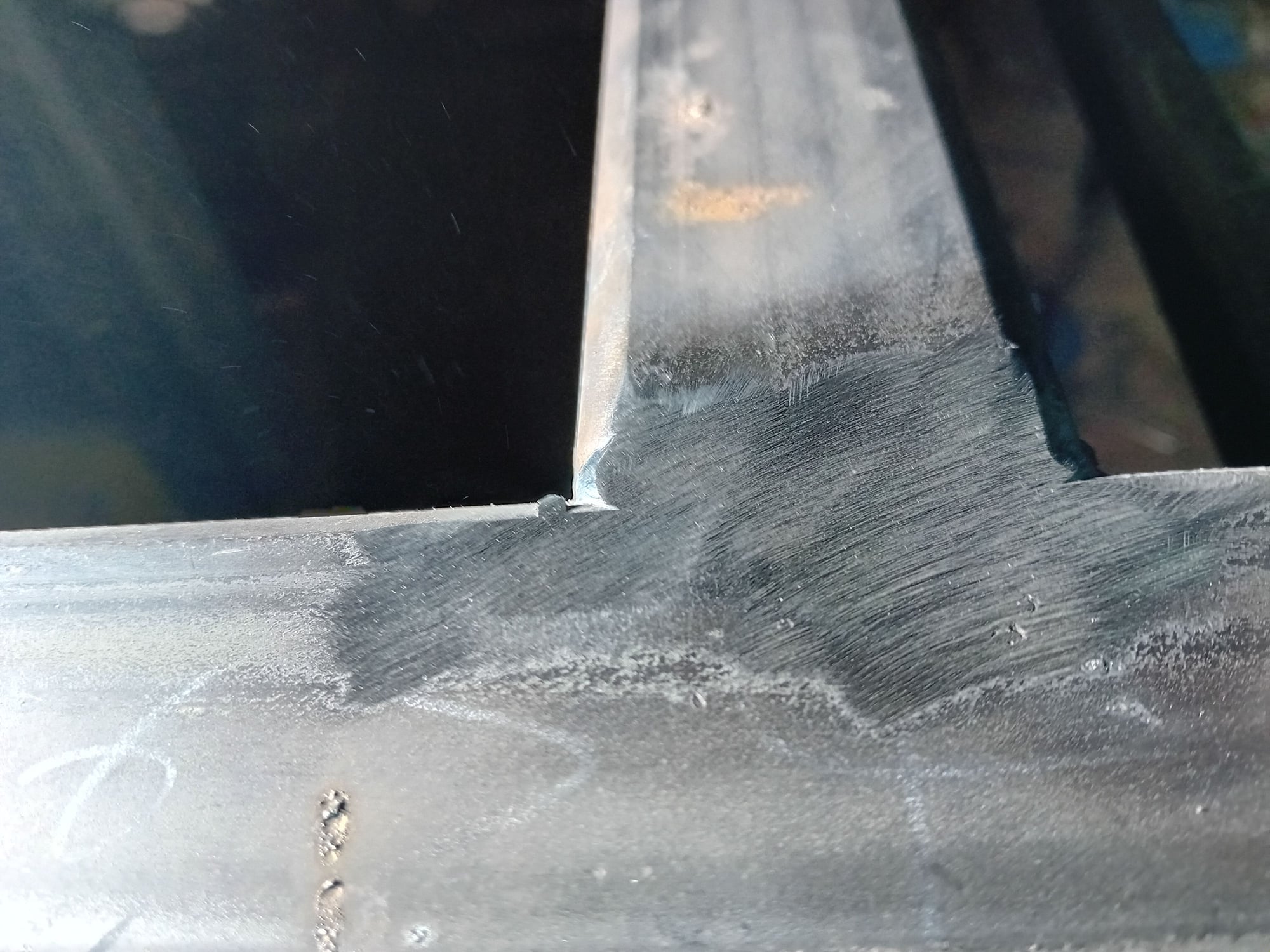
typical finish, has been stoned/40 grit will probably sand with 800 grit before painting possibly a lower grade if needed
have since welded on the brace for the bike frame, this is also for the crank, also have the backstop on for the bed to stop the load coming back onto me
waiting for monday for a delivery of pipe for continuation on front of bike, will make the front forks etc then work my way to the back

its pretty well balanced as it is i can imagine once everything is on the balance wont be heavier one end than the other
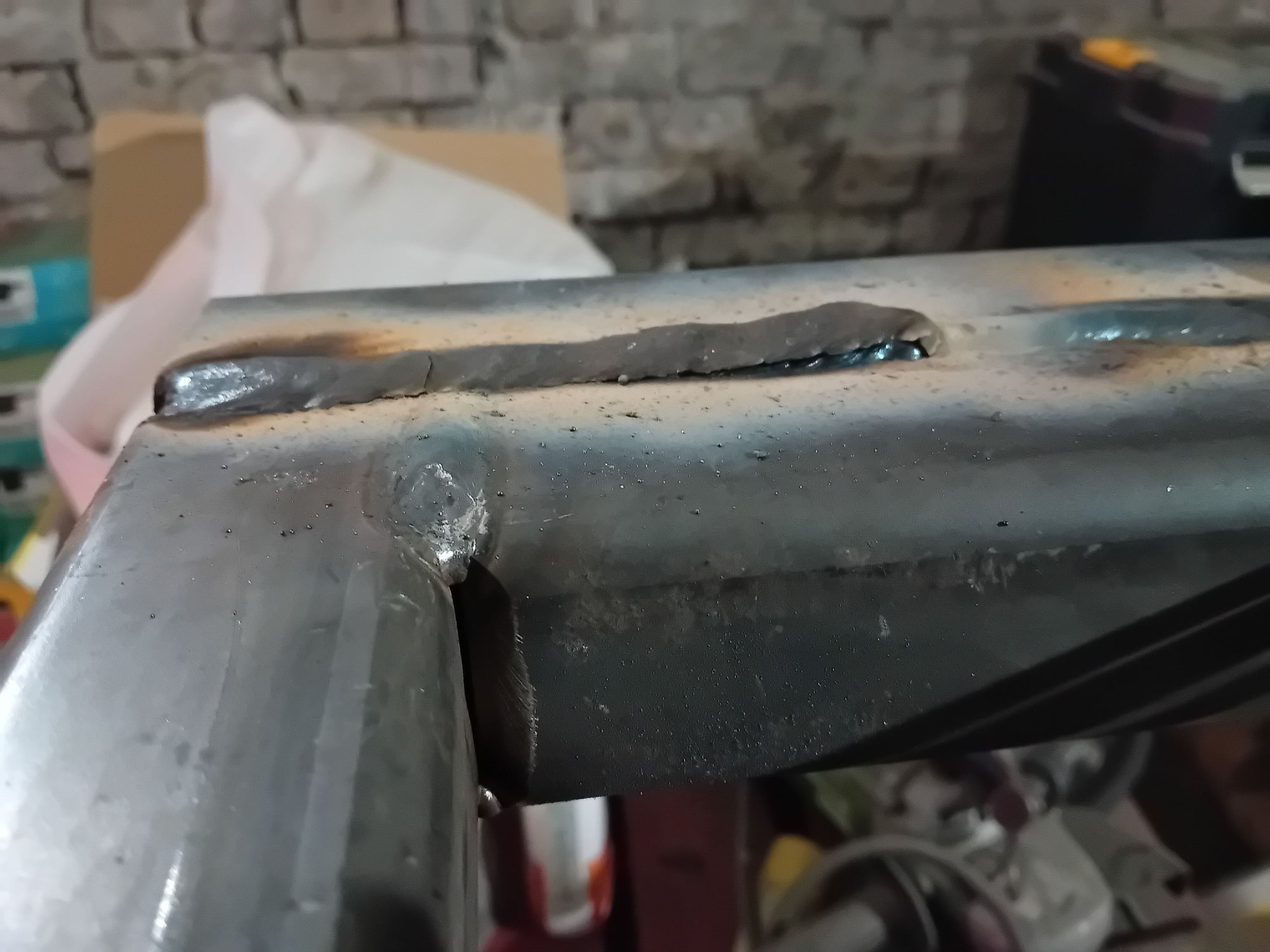
peeling slag is always a good thing
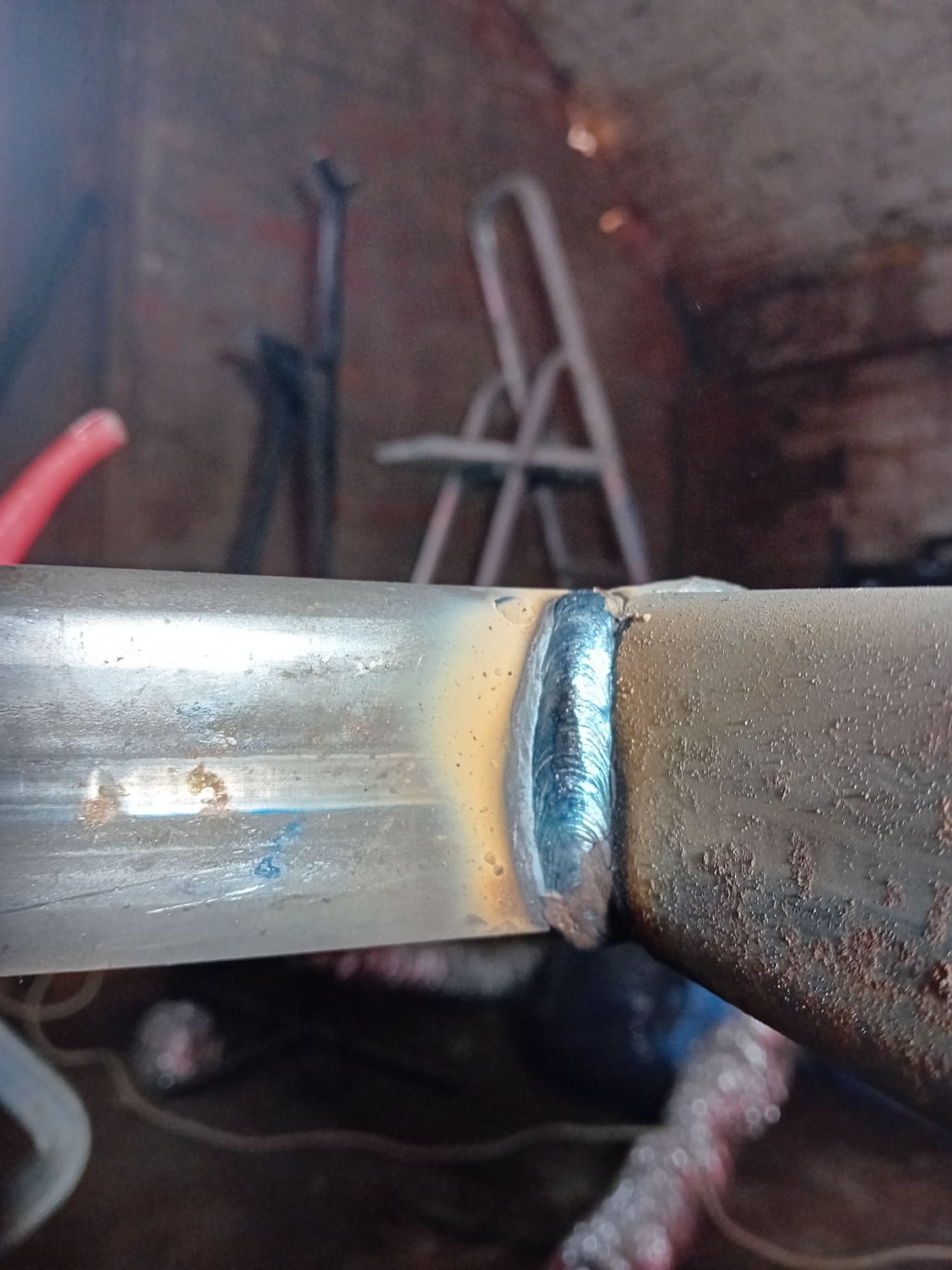
some welds like these were done in position as was to much effort to keep moving the bed around
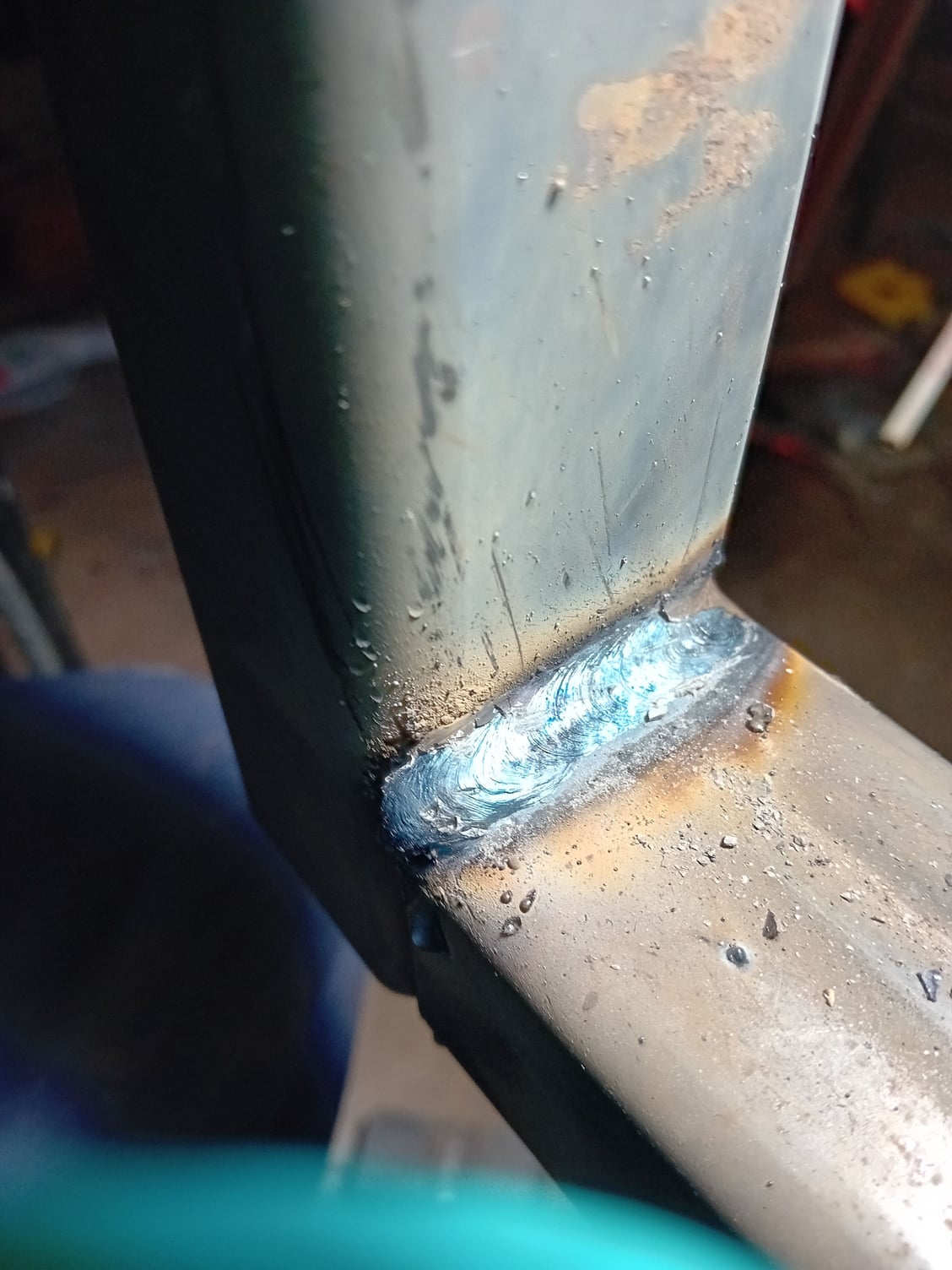
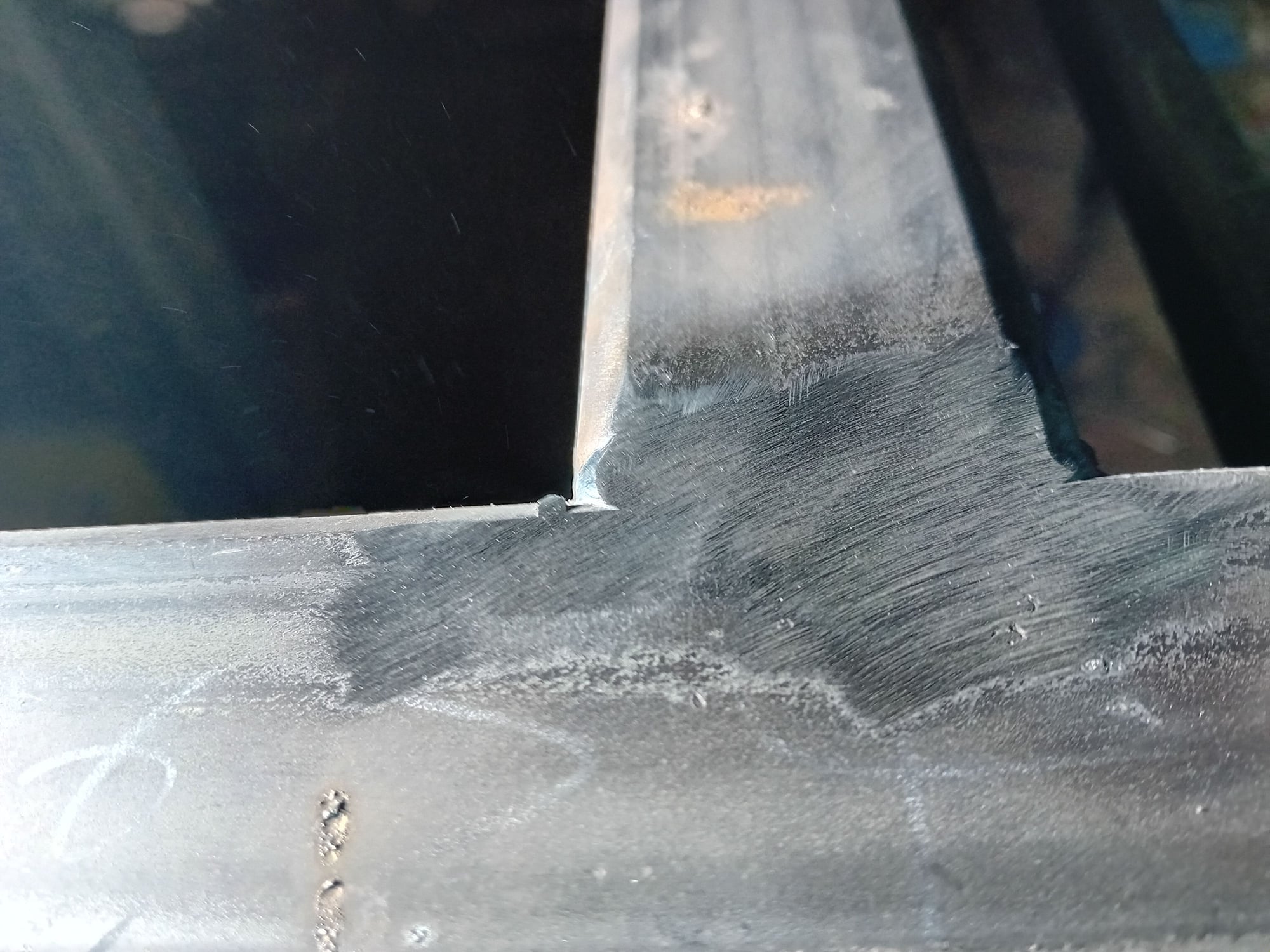
typical finish, has been stoned/40 grit will probably sand with 800 grit before painting possibly a lower grade if needed
Last edited by Jordanjw; 05-11-24 at 02:01 AM.
Likes For Jordanjw:
#37
Newbie
Thread Starter
i mean after reasearch and other talks, ive concluded its not possible as my plan is to use for work loads and workbench while on jobs, could mean the bed gets things thrown on & off and also may use the bed for plasma cutting, also it just makes it easier from my point of view as im geared to deal with steel, i could weld chromoly, as i did a few weeks ago and also i think chromoly would be possibly cheaper but in the long run of buying welding rods it could possibly cost the same
and yes i need the stiffness on the bike as im known to just ride wherever i want type ie up kerbs etc so frame will take alot of abuse although i dont plan on riding it like that but who knows once im riding it, i expect it to be pretty stiff, also this is partly why its steel too so if i need to add and suspension or any extras down the line i can just do it without having to worry about structural problems or heat problems
i was planning on having the main parts done by next week the bed is basically done braces will the last thing as im planning to brace the bed to the bike which i cant do yet and also the front forks will be the same, so if anything i should have the main bike made up by the end of next week along with the front forks etc, so you can atleast see what it will look like although i dont think i will have the seat on by then as ill need to buy one or a piece of perforated sheet or aluminium
also on the weight issue of the bike ive looked at the biggest cargo bike available is 52kg - an arrow xl - the bed is around 15-25kg so aslong as i can stay around 40-60kg i think ill be fine
and yes i need the stiffness on the bike as im known to just ride wherever i want type ie up kerbs etc so frame will take alot of abuse although i dont plan on riding it like that but who knows once im riding it, i expect it to be pretty stiff, also this is partly why its steel too so if i need to add and suspension or any extras down the line i can just do it without having to worry about structural problems or heat problems
i was planning on having the main parts done by next week the bed is basically done braces will the last thing as im planning to brace the bed to the bike which i cant do yet and also the front forks will be the same, so if anything i should have the main bike made up by the end of next week along with the front forks etc, so you can atleast see what it will look like although i dont think i will have the seat on by then as ill need to buy one or a piece of perforated sheet or aluminium
also on the weight issue of the bike ive looked at the biggest cargo bike available is 52kg - an arrow xl - the bed is around 15-25kg so aslong as i can stay around 40-60kg i think ill be fine
#38
Newbie
Thread Starter
Andra 25 Disc - Ryde anyone had any experience with these? stating 180kg max load for a rim x2 is 360kg
i have recalculated my load and will be around 380kg
back wheel is 36 spoke assuming this can take 100kg ~ ?
the weight stated is including the bike weight as this is static and a constant
also some minor adjustments to the frame - steering rack or column is encased in a 50x50 piece of box so it doesnt get damaged incase i kick it when mounting the bike -
will be adding more pictures tomorrow have the rack in place will be welding together back stays tomorrow and hopefully a picture with a back wheel in place
i have recalculated my load and will be around 380kg
back wheel is 36 spoke assuming this can take 100kg ~ ?
the weight stated is including the bike weight as this is static and a constant
also some minor adjustments to the frame - steering rack or column is encased in a 50x50 piece of box so it doesnt get damaged incase i kick it when mounting the bike -
will be adding more pictures tomorrow have the rack in place will be welding together back stays tomorrow and hopefully a picture with a back wheel in place
#39
Randomhead
Join Date: Aug 2008
Location: Happy Valley, Pennsylvania
Posts: 24,461
Mentioned: 0 Post(s)
Tagged: 0 Thread(s)
Quoted: 4 Post(s)
Liked 3,762 Times
in
2,560 Posts
The internet tells me that a full keg of beer weighs 160 pounds, so there are about 700lbs on this bike. They just ran out of space, probably be 400kg if they hadn't. There are lots more on the trailer, which only has 3 normal looking bike wheels.
Picture from PedalMe, which is a bike cargo hauler in London. Pedalmeapp on twitter.
Picture from PedalMe, which is a bike cargo hauler in London. Pedalmeapp on twitter.
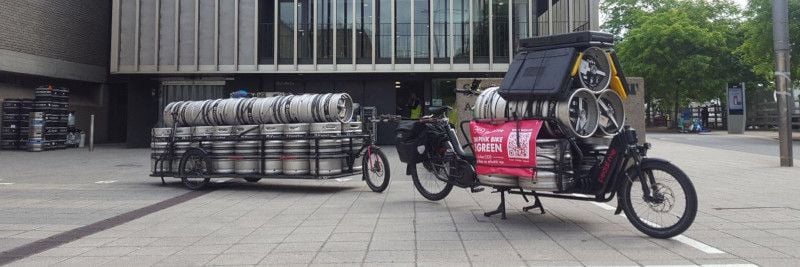
#40
Senior Member
Join Date: Feb 2012
Location: Rochester, NY
Posts: 18,139
Bikes: Stewart S&S coupled sport tourer, Stewart Sunday light, Stewart Commuting, Stewart Touring, Co Motion Tandem, Stewart 3-Spd, Stewart Track, Fuji Finest, Mongoose Tomac ATB, GT Bravado ATB, JCP Folder, Stewart 650B ATB
Mentioned: 0 Post(s)
Tagged: 0 Thread(s)
Quoted: 4231 Post(s)
Liked 3,940 Times
in
2,347 Posts
As far as the wheels go I think you've entered the weight capacity/loading range of motorcycle wheels and tires. The issue with talking about wheel "strength" is that it is so variable WRT the conditions and manor of the riding. Static loading is easy to mimic in the lab. Cyclic peak loading is also easy to attain in the lab. But real life use can often not follow completely the assumptions the testing (and thus claims of this or that number) made.
380kg is a bit over 800lbs. This is similar to me riding a nearly 700lb motorcycle, and look at those wheels... Another aspect that bike wheels don't really address well is the lateral forces. As bike lean when cornering the bike wheels see vastly more vertical loading and the wheel construction has ended up reflecting this. But most all trikes and many trailers don't lean when cornering. So their wheels will see far more side forces than two wheeled bikes will.
Looking at the rims linked to they do seem to be pretty heavy duty and made in the smaller sizes that will better hold up to the lateral forces a trike can see. I would strongly also consider thicker spokes and beefed up hubs. One design philosophy I try to follow is to net be using the complete capacity of a device or system in common/normal use the device will see. I describe this with an auto analogy: My car has a manual transmission and a tachometer with a red line for too high an engine RPM. Many might think they can rev the engine up to that redline for each and every shift and never encounter a problem. In real life sooner or later the increased stress and strain on the engine (and other related parts) will cause earlier wear and need for service. It's my opinion that running even beefy bicycle parts on a powered cycle that will weigh double+ what a bike usually does isn't a long term best choice. Andy
380kg is a bit over 800lbs. This is similar to me riding a nearly 700lb motorcycle, and look at those wheels... Another aspect that bike wheels don't really address well is the lateral forces. As bike lean when cornering the bike wheels see vastly more vertical loading and the wheel construction has ended up reflecting this. But most all trikes and many trailers don't lean when cornering. So their wheels will see far more side forces than two wheeled bikes will.
Looking at the rims linked to they do seem to be pretty heavy duty and made in the smaller sizes that will better hold up to the lateral forces a trike can see. I would strongly also consider thicker spokes and beefed up hubs. One design philosophy I try to follow is to net be using the complete capacity of a device or system in common/normal use the device will see. I describe this with an auto analogy: My car has a manual transmission and a tachometer with a red line for too high an engine RPM. Many might think they can rev the engine up to that redline for each and every shift and never encounter a problem. In real life sooner or later the increased stress and strain on the engine (and other related parts) will cause earlier wear and need for service. It's my opinion that running even beefy bicycle parts on a powered cycle that will weigh double+ what a bike usually does isn't a long term best choice. Andy
__________________
AndrewRStewart
AndrewRStewart
Likes For Andrew R Stewart:
#41
Randomhead
Join Date: Aug 2008
Location: Happy Valley, Pennsylvania
Posts: 24,461
Mentioned: 0 Post(s)
Tagged: 0 Thread(s)
Quoted: 4 Post(s)
Liked 3,762 Times
in
2,560 Posts
It would be interesting to know more about those PedalMe wheels. They do appear to have a lot of spokes and very large rotors. Tandem wheels, probably.
Maybe they just replace them often.
Maybe they just replace them often.
Likes For unterhausen:
#42
Senior Member
Join Date: Jul 2006
Location: San Jose (Willow Glen) Ca
Posts: 9,919
Bikes: Kirk Custom JK Special, '84 Team Miyata,(dura ace old school) 80?? SR Semi-Pro 600 Arabesque
Mentioned: 107 Post(s)
Tagged: 0 Thread(s)
Quoted: 2368 Post(s)
Liked 2,895 Times
in
1,579 Posts
Bit late for this idea, but you might be better served with trailer pulled by an appropriate bike based on the weights you are dealing with
Braking power will be need to match also
Braking power will be need to match also
__________________
Life is too short not to ride the best bike you have, as much as you can
(looking for Torpado Super light frame/fork or for Raleigh International frame fork 58cm)
Life is too short not to ride the best bike you have, as much as you can
(looking for Torpado Super light frame/fork or for Raleigh International frame fork 58cm)
Likes For squirtdad:
#43
Senior Member
Join Date: Aug 2012
Location: Seattle
Posts: 515
Mentioned: 0 Post(s)
Tagged: 0 Thread(s)
Quoted: 106 Post(s)
Liked 145 Times
in
89 Posts
This is what I meant by 'overbuilt out to the edges'. I know some of the pedi-cabs here in Seattle use what appear to be light weight motorcycle/moped rims on appropriate hubs (front or rear). They carry, 2-3 passengers, the rider and bike so that's probably getting up 300-350kg. Then you have heavier tires and tubes to think about. I have a friend who has a MTB tandem and he's doubled up 203mm rotors on the front to deal with the added heat generated with 2 riders on steep offroad downhills or gravel decents - he uses old 4 piston XT calipers. Alternatively, light motorcycle/moped brakes might work.
__________________
https://www.flickr.com/photos/54319503@N05/
https://www.draper-cycles.com
https://www.flickr.com/photos/54319503@N05/
https://www.draper-cycles.com
Likes For duanedr:
#44
Newbie
Thread Starter
As far as the wheels go I think you've entered the weight capacity/loading range of motorcycle wheels and tires. The issue with talking about wheel "strength" is that it is so variable WRT the conditions and manor of the riding. Static loading is easy to mimic in the lab. Cyclic peak loading is also easy to attain in the lab. But real life use can often not follow completely the assumptions the testing (and thus claims of this or that number) made.
380kg is a bit over 800lbs. This is similar to me riding a nearly 700lb motorcycle, and look at those wheels... Another aspect that bike wheels don't really address well is the lateral forces. As bike lean when cornering the bike wheels see vastly more vertical loading and the wheel construction has ended up reflecting this. But most all trikes and many trailers don't lean when cornering. So their wheels will see far more side forces than two wheeled bikes will.
Looking at the rims linked to they do seem to be pretty heavy duty and made in the smaller sizes that will better hold up to the lateral forces a trike can see. I would strongly also consider thicker spokes and beefed up hubs. One design philosophy I try to follow is to net be using the complete capacity of a device or system in common/normal use the device will see. I describe this with an auto analogy: My car has a manual transmission and a tachometer with a red line for too high an engine RPM. Many might think they can rev the engine up to that redline for each and every shift and never encounter a problem. In real life sooner or later the increased stress and strain on the engine (and other related parts) will cause earlier wear and need for service. It's my opinion that running even beefy bicycle parts on a powered cycle that will weigh double+ what a bike usually does isn't a long term best choice. Andy
380kg is a bit over 800lbs. This is similar to me riding a nearly 700lb motorcycle, and look at those wheels... Another aspect that bike wheels don't really address well is the lateral forces. As bike lean when cornering the bike wheels see vastly more vertical loading and the wheel construction has ended up reflecting this. But most all trikes and many trailers don't lean when cornering. So their wheels will see far more side forces than two wheeled bikes will.
Looking at the rims linked to they do seem to be pretty heavy duty and made in the smaller sizes that will better hold up to the lateral forces a trike can see. I would strongly also consider thicker spokes and beefed up hubs. One design philosophy I try to follow is to net be using the complete capacity of a device or system in common/normal use the device will see. I describe this with an auto analogy: My car has a manual transmission and a tachometer with a red line for too high an engine RPM. Many might think they can rev the engine up to that redline for each and every shift and never encounter a problem. In real life sooner or later the increased stress and strain on the engine (and other related parts) will cause earlier wear and need for service. It's my opinion that running even beefy bicycle parts on a powered cycle that will weigh double+ what a bike usually does isn't a long term best choice. Andy
#45
Newbie
Thread Starter
The internet tells me that a full keg of beer weighs 160 pounds, so there are about 700lbs on this bike. They just ran out of space, probably be 400kg if they hadn't. There are lots more on the trailer, which only has 3 normal looking bike wheels.
Picture from PedalMe, which is a bike cargo hauler in London. Pedalmeapp on twitter.
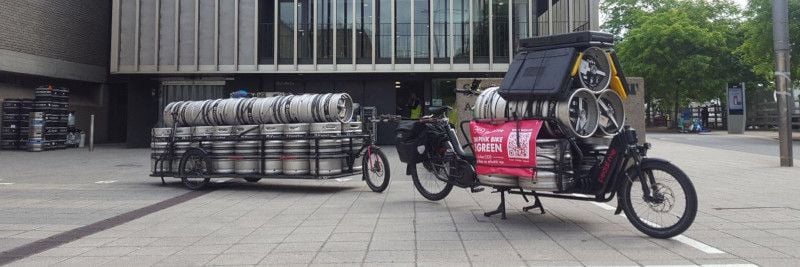
Picture from PedalMe, which is a bike cargo hauler in London. Pedalmeapp on twitter.
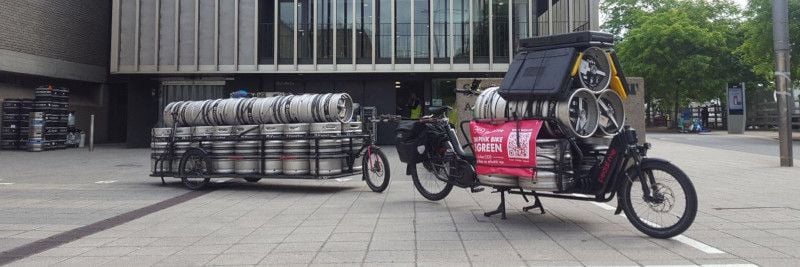

also reason i didnt go for a trailer is so i can see the load and from previous experience i know that a front loading is better suited for how i ride - i have had loads come loose in the past, caused by rain as ratchet straps stretch when wet and i cant imagine losing a piece of work or something similar to the road
#46
Newbie
Thread Starter
been a bit slow as i was unable to take the wheel and all the tube in one day - tomorrow will be better as now can concentrate on the front end once i have mounted the wheel and set the bed level
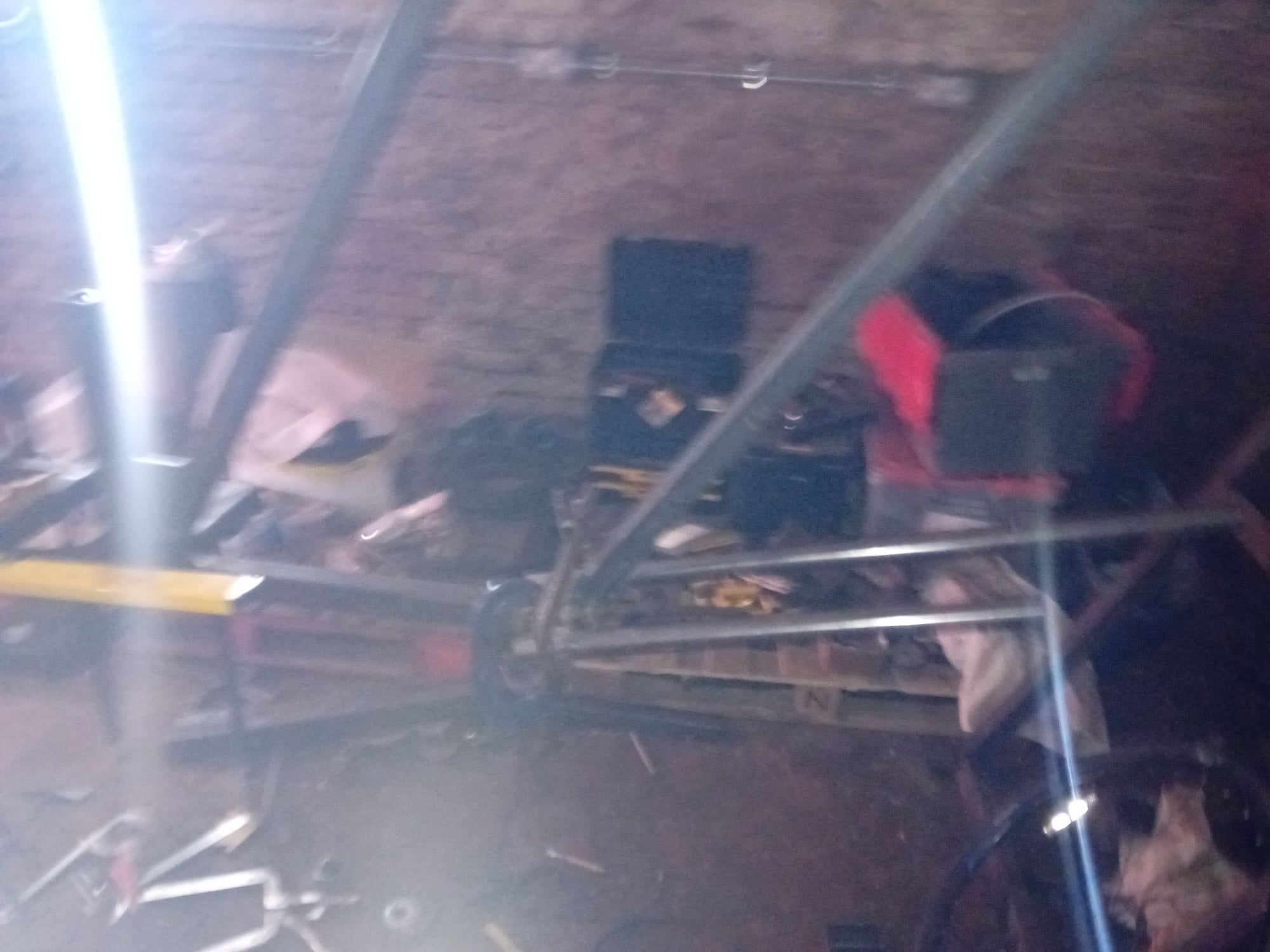
stays for rear wheel - was only able to do these two on one day - leved across them and have since cut to length and welded on drop outs
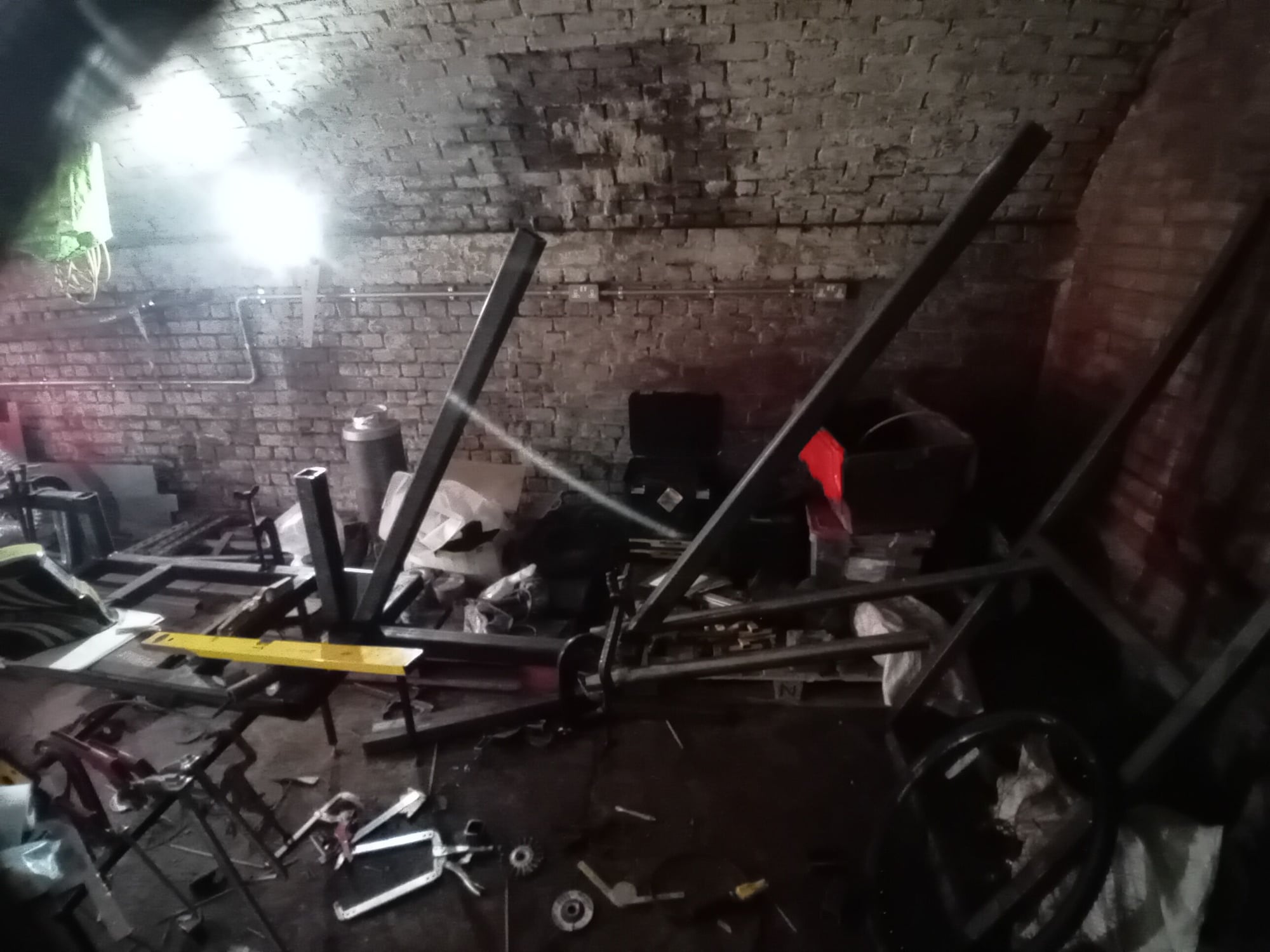
the steering & seat posts still need to be cut to length
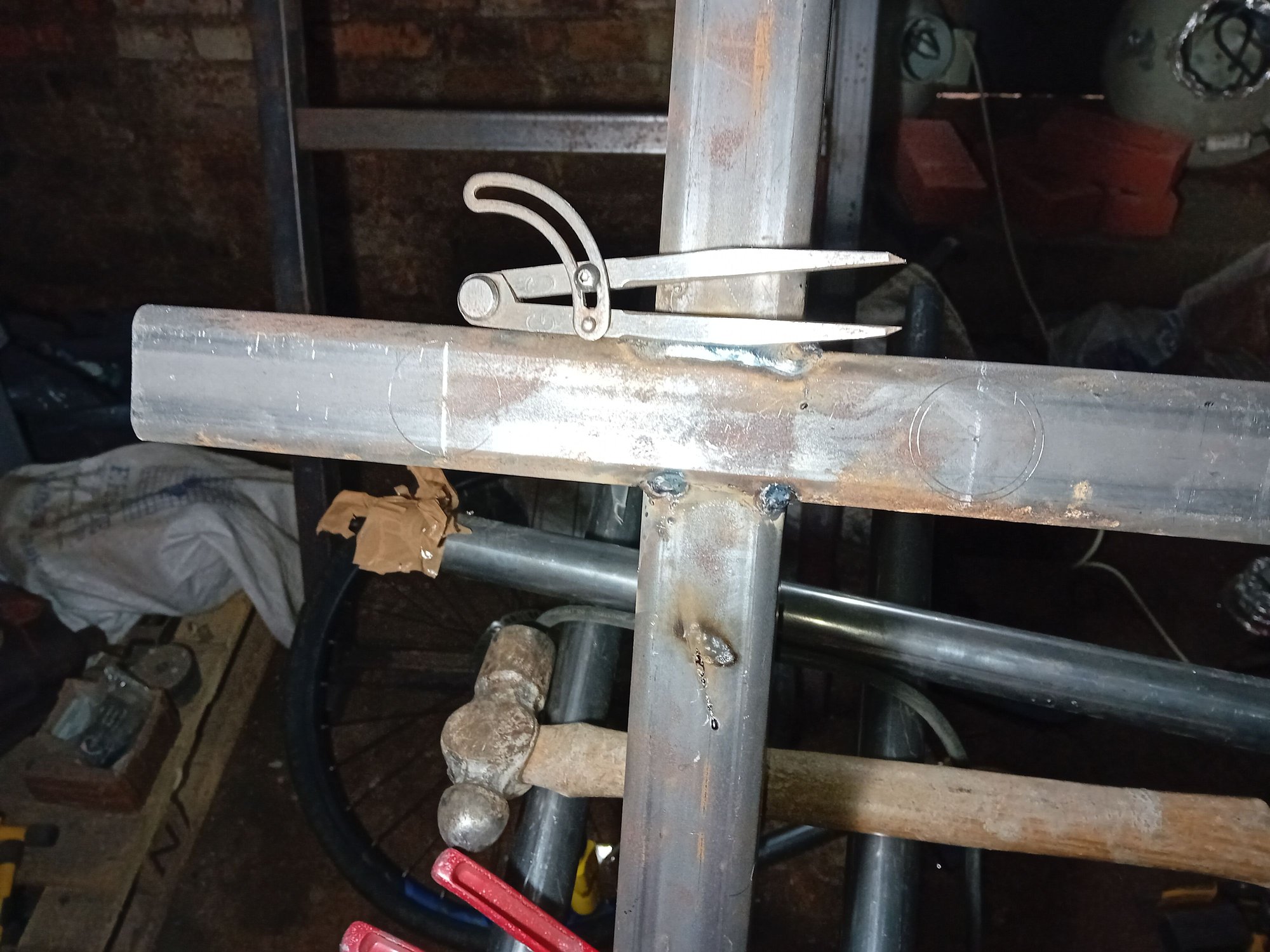
holes marked in box to take the stays
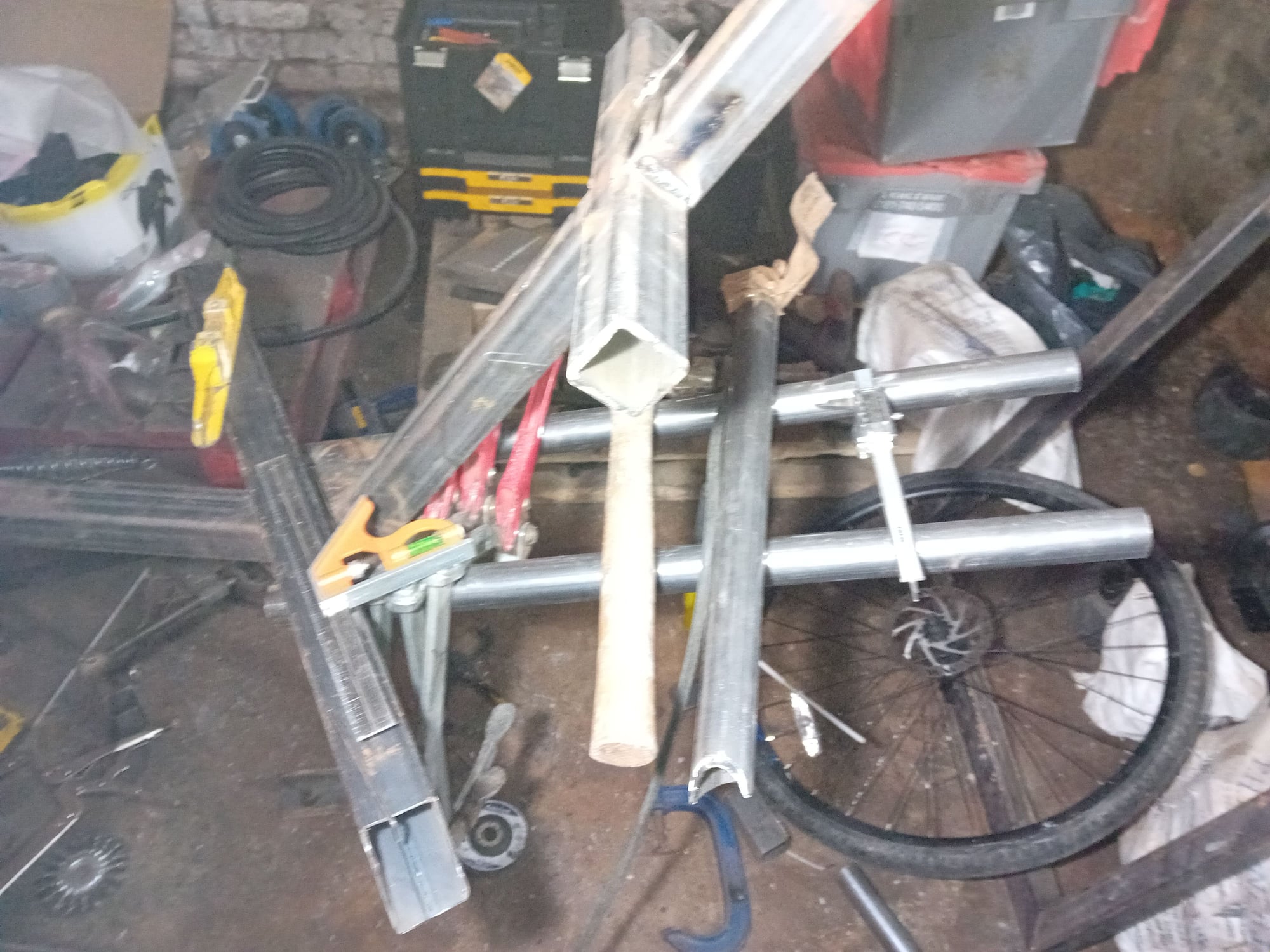
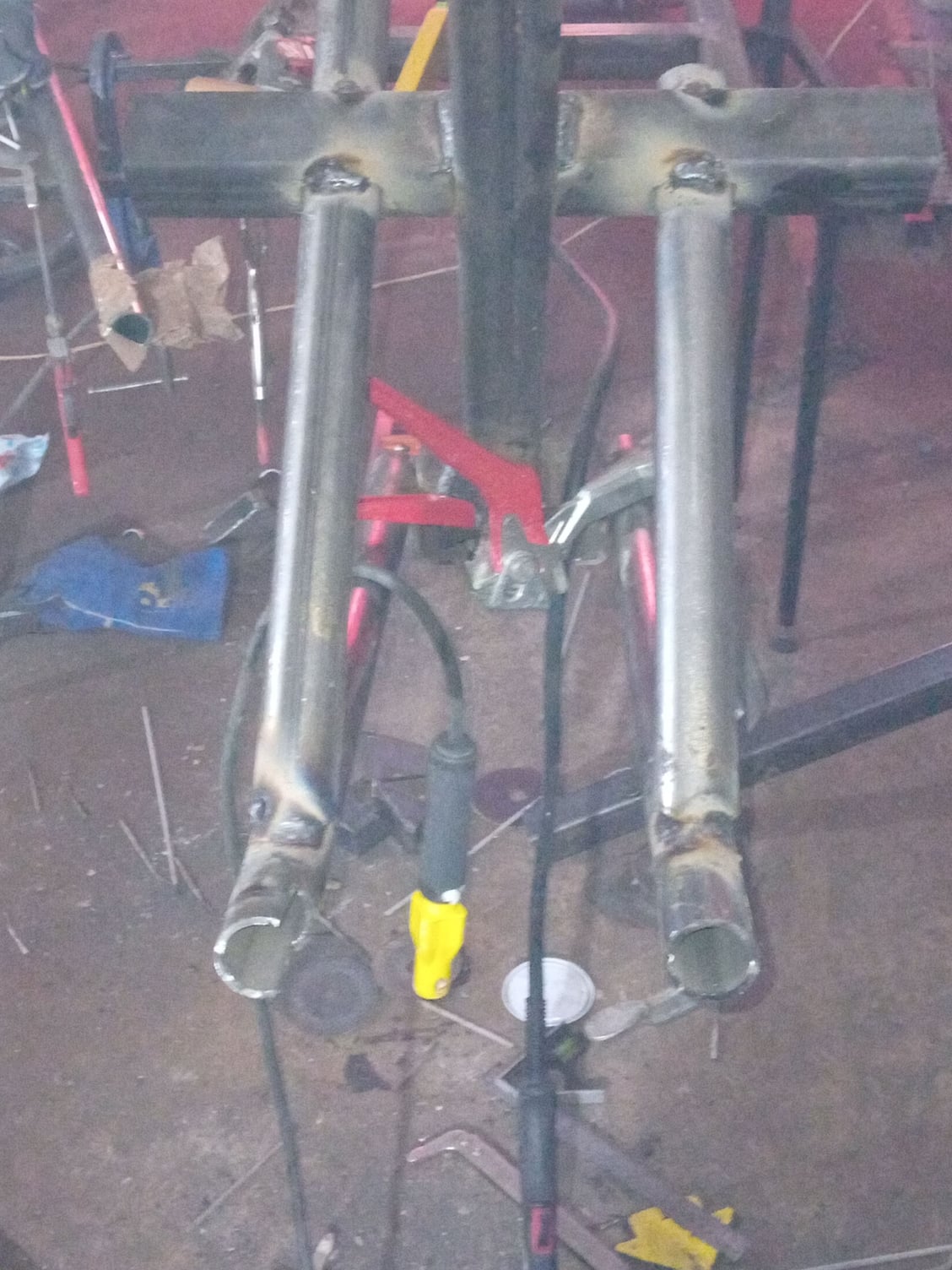
left stay is cut to take drop out - stays from top are sloted into box welded onto seat mount
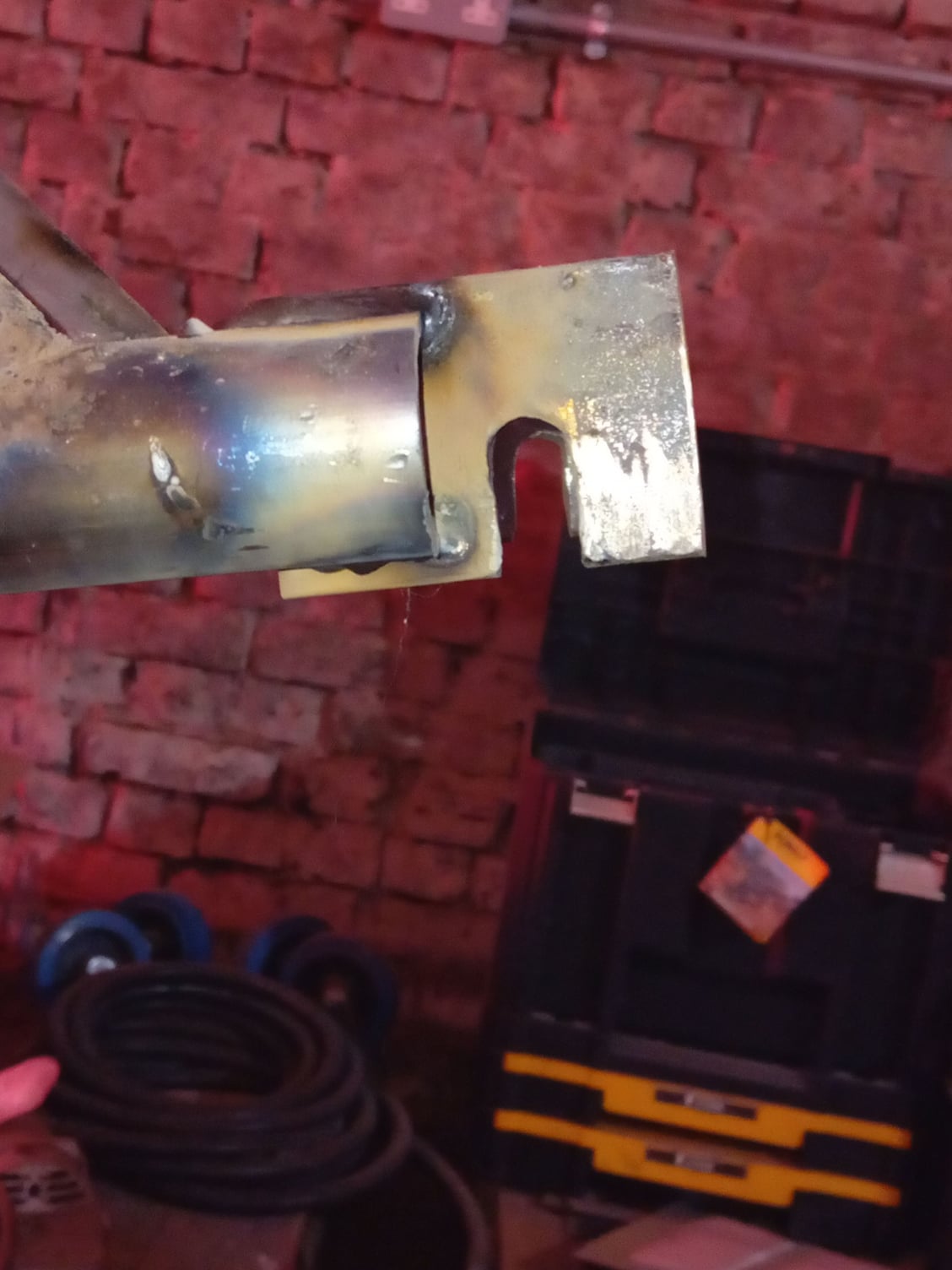
drop outs in place - made from 10mm steel cut using plasma cutter and cleaned with grinder - two identical pieces of steel then i had to tack into place and level the vertical of the dropouts & then once that was done i could place a 12mm rod in place to get correct spacing and level off the axle before i finished tacking in place before welding
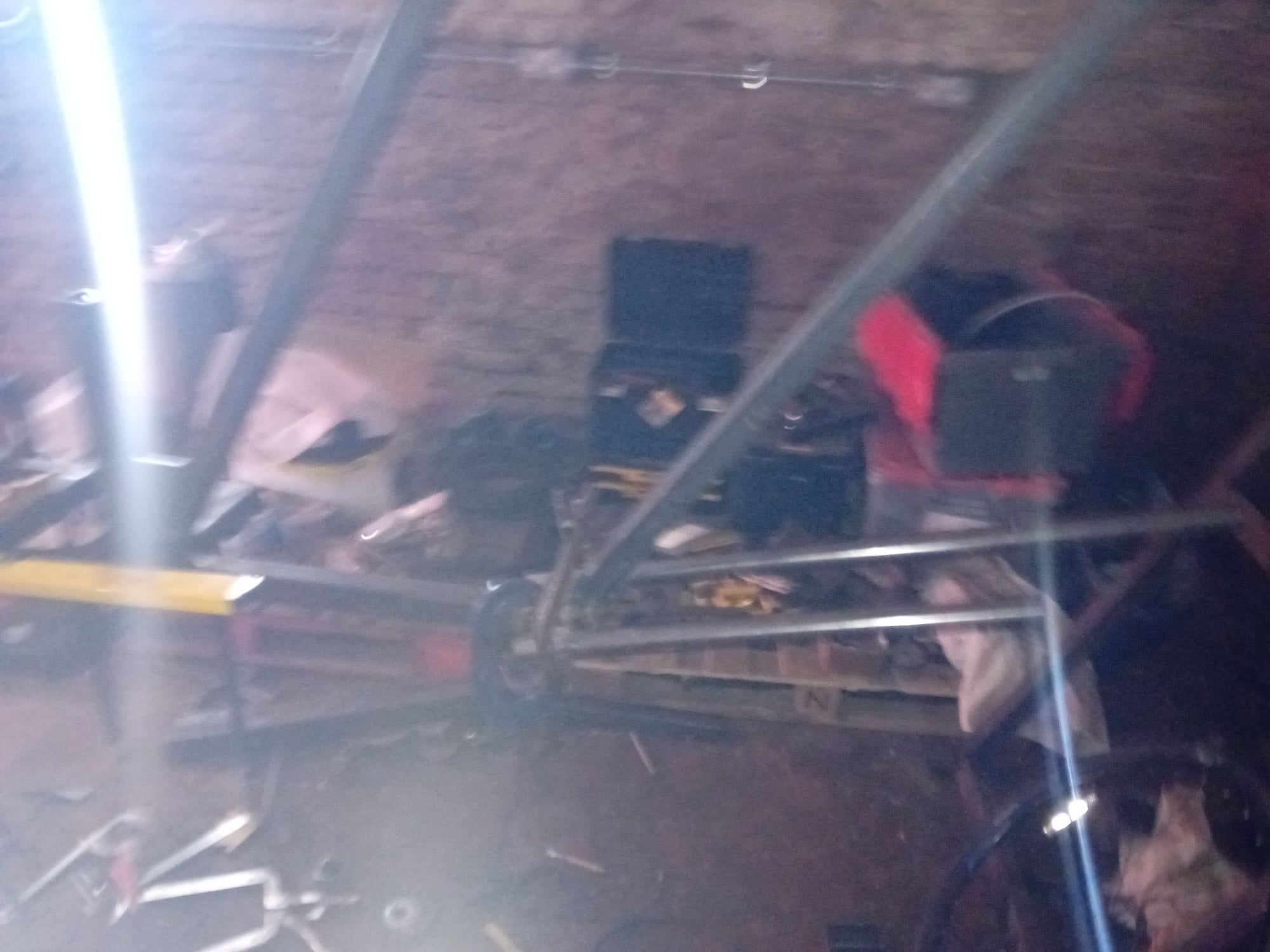
stays for rear wheel - was only able to do these two on one day - leved across them and have since cut to length and welded on drop outs
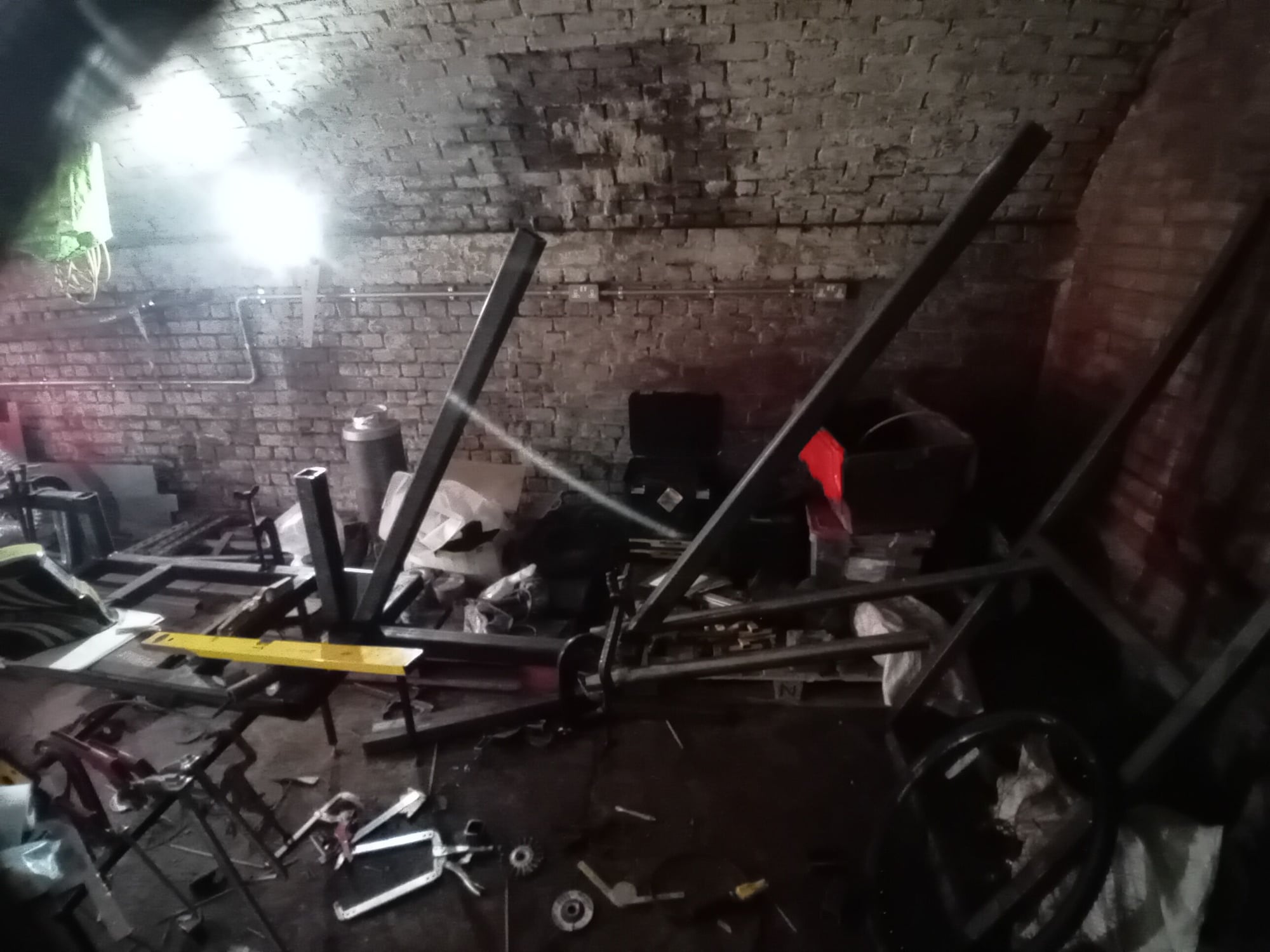
the steering & seat posts still need to be cut to length
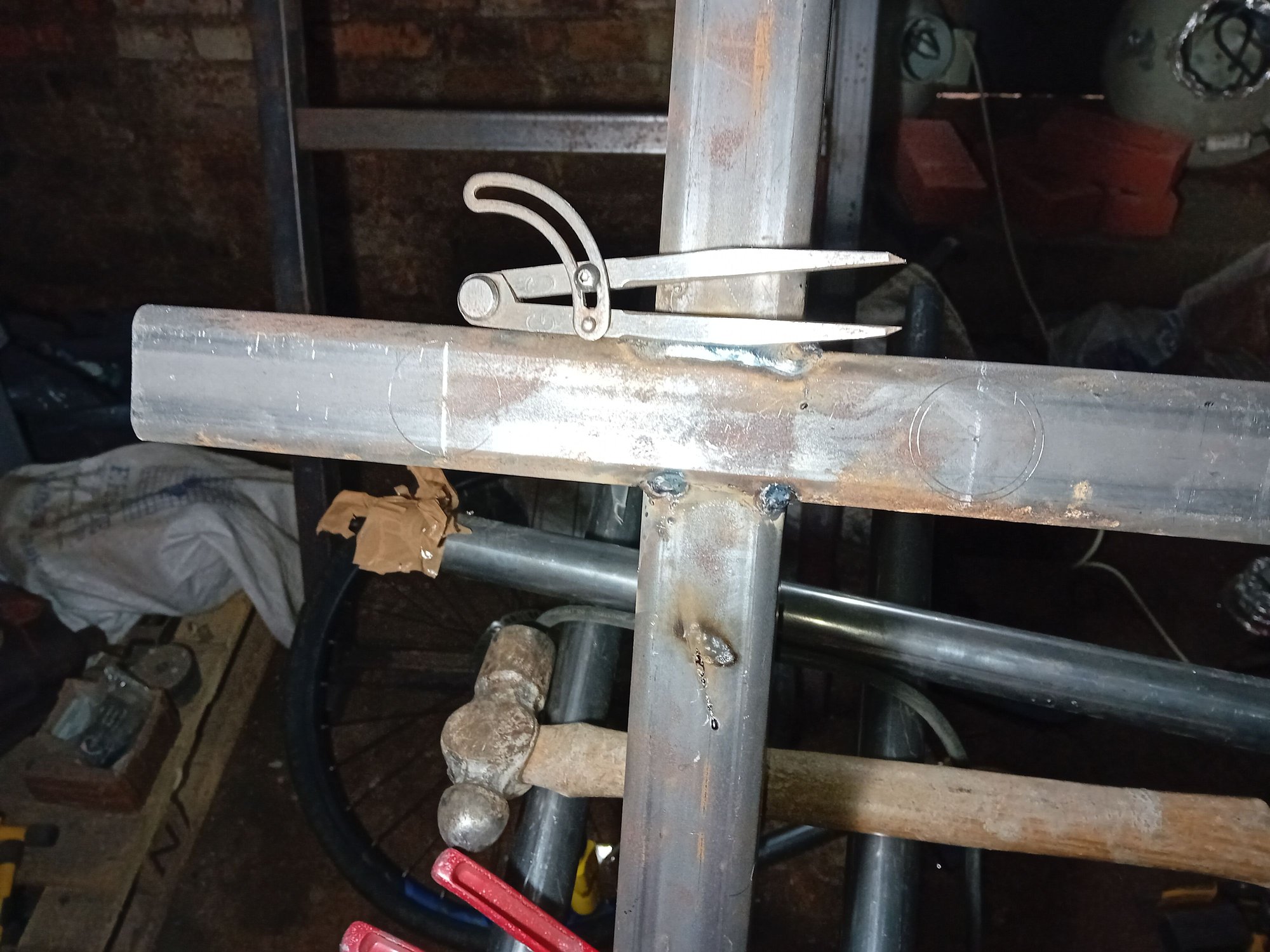
holes marked in box to take the stays
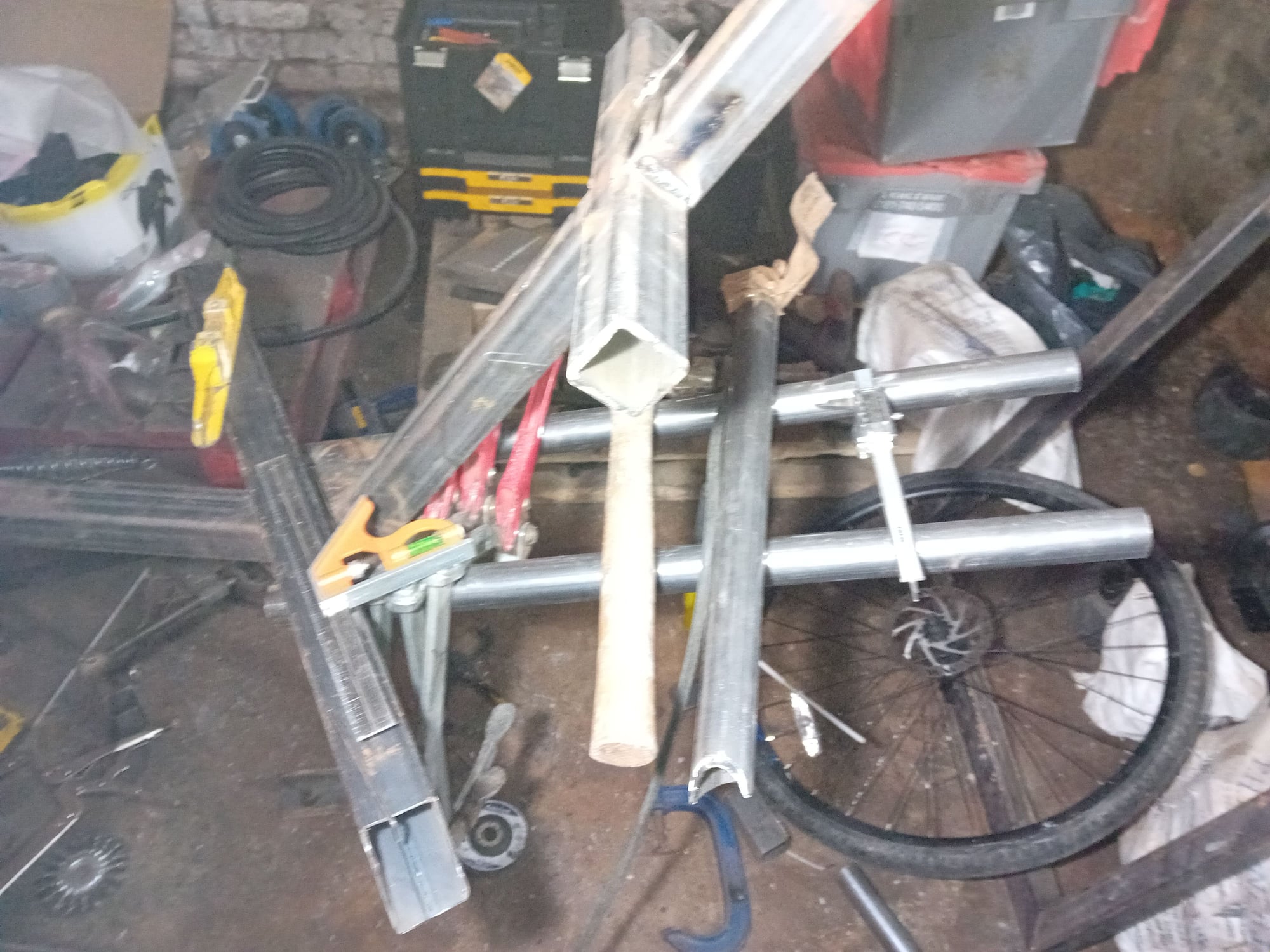
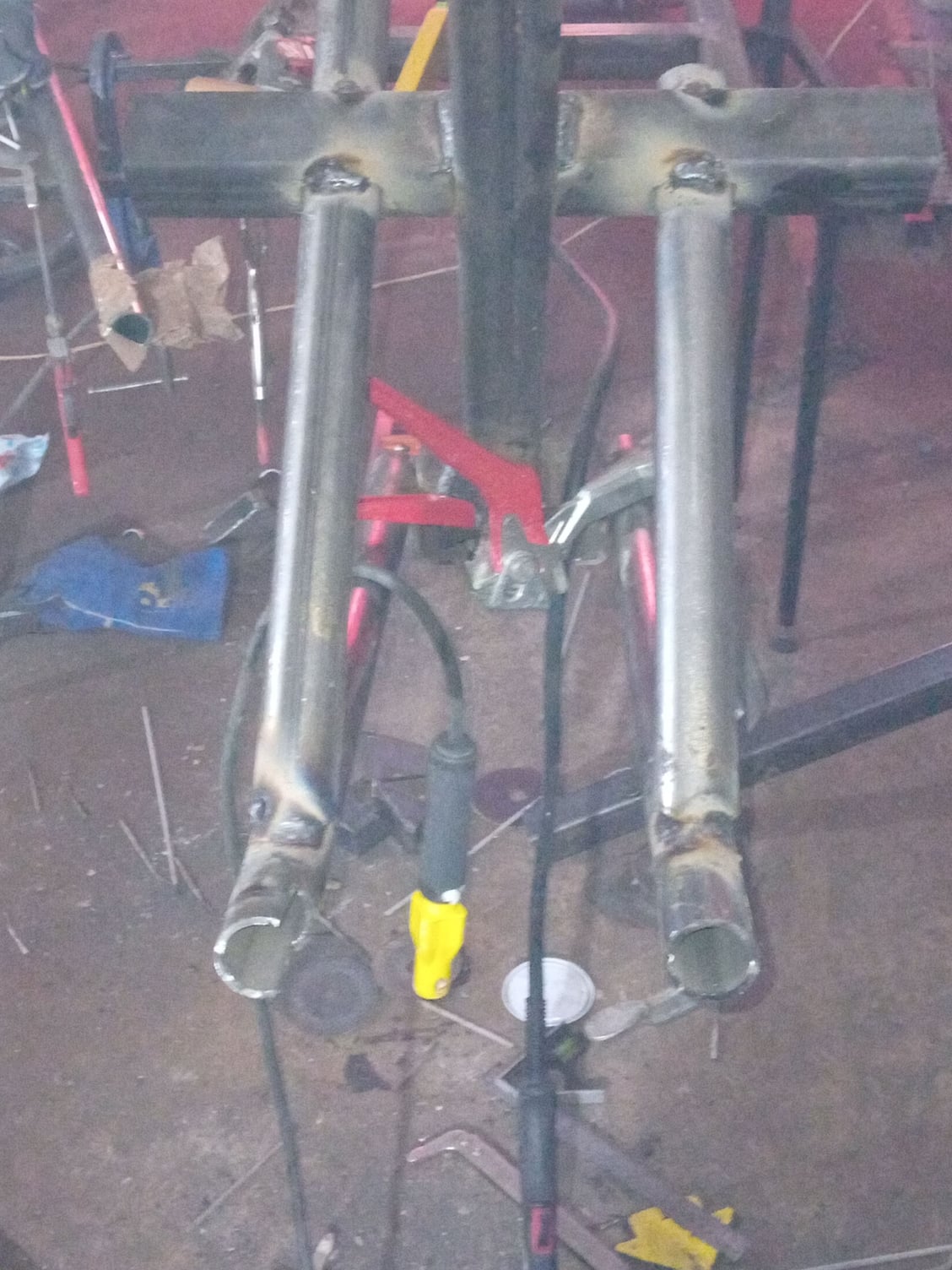
left stay is cut to take drop out - stays from top are sloted into box welded onto seat mount
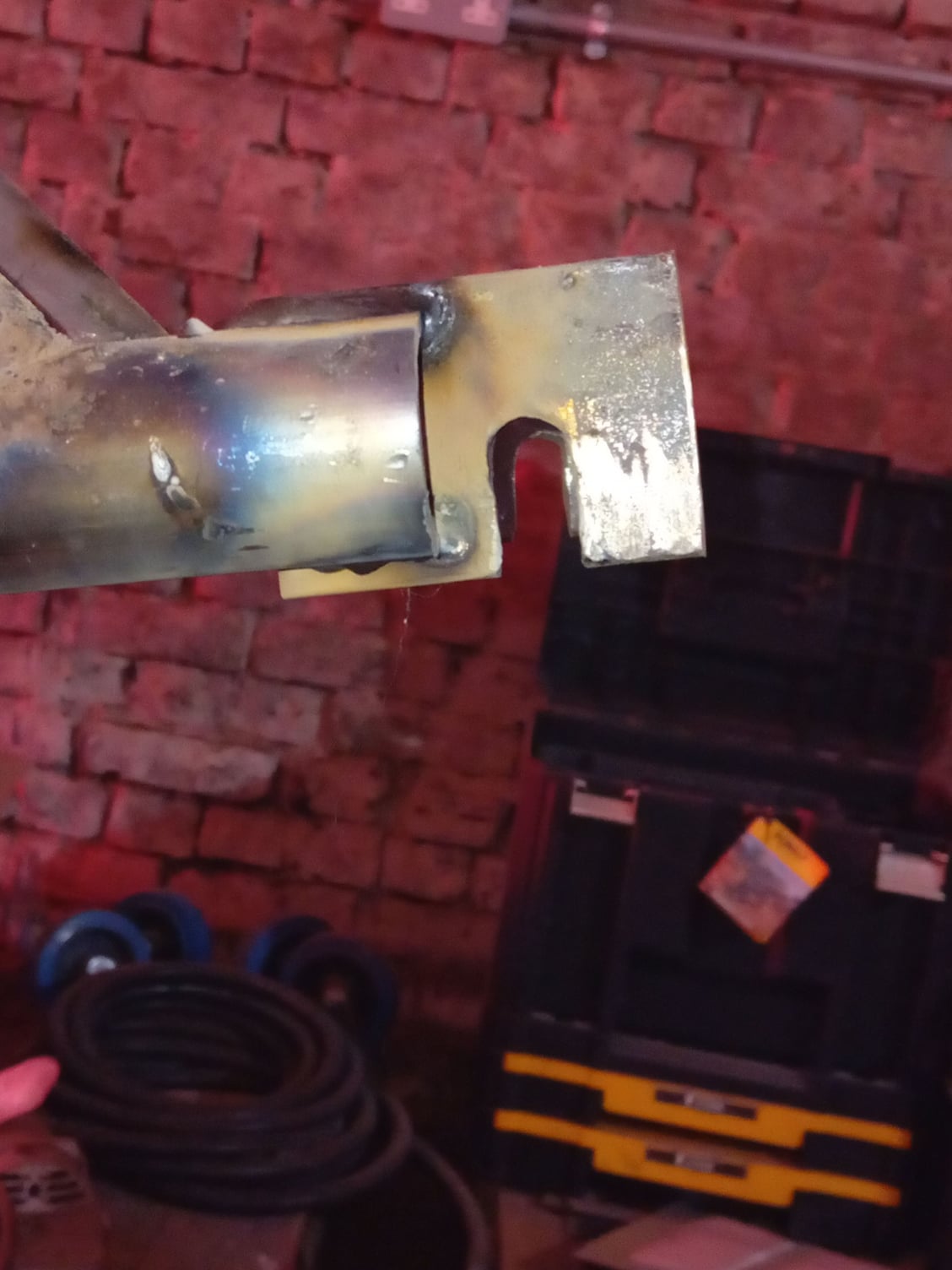
drop outs in place - made from 10mm steel cut using plasma cutter and cleaned with grinder - two identical pieces of steel then i had to tack into place and level the vertical of the dropouts & then once that was done i could place a 12mm rod in place to get correct spacing and level off the axle before i finished tacking in place before welding
Likes For Jordanjw:
#47
Newbie
Thread Starter
My front wheel on my regular bike buckled, am i able to true another wheel by eyeballing it or would it need to be mounted for more precision
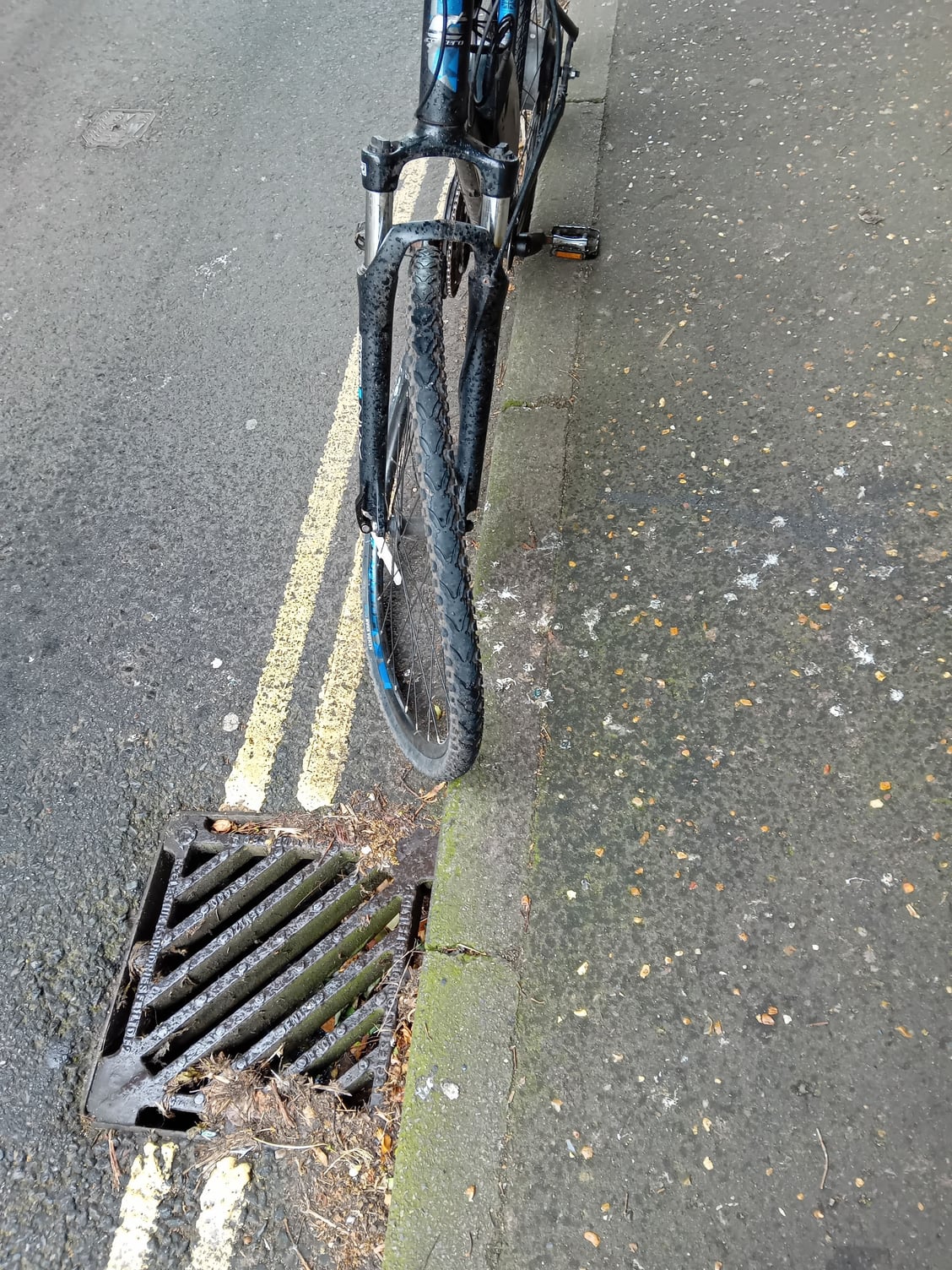
this was my fault as the wheel was over tensioned, wasnt aware of this until after i tightened the spokes i did untighten most of them but i was using a regular adjustable spanned which is way to big for the job
I assumed tightening all the spokes to tension would true the wheel but after reading this is wrong
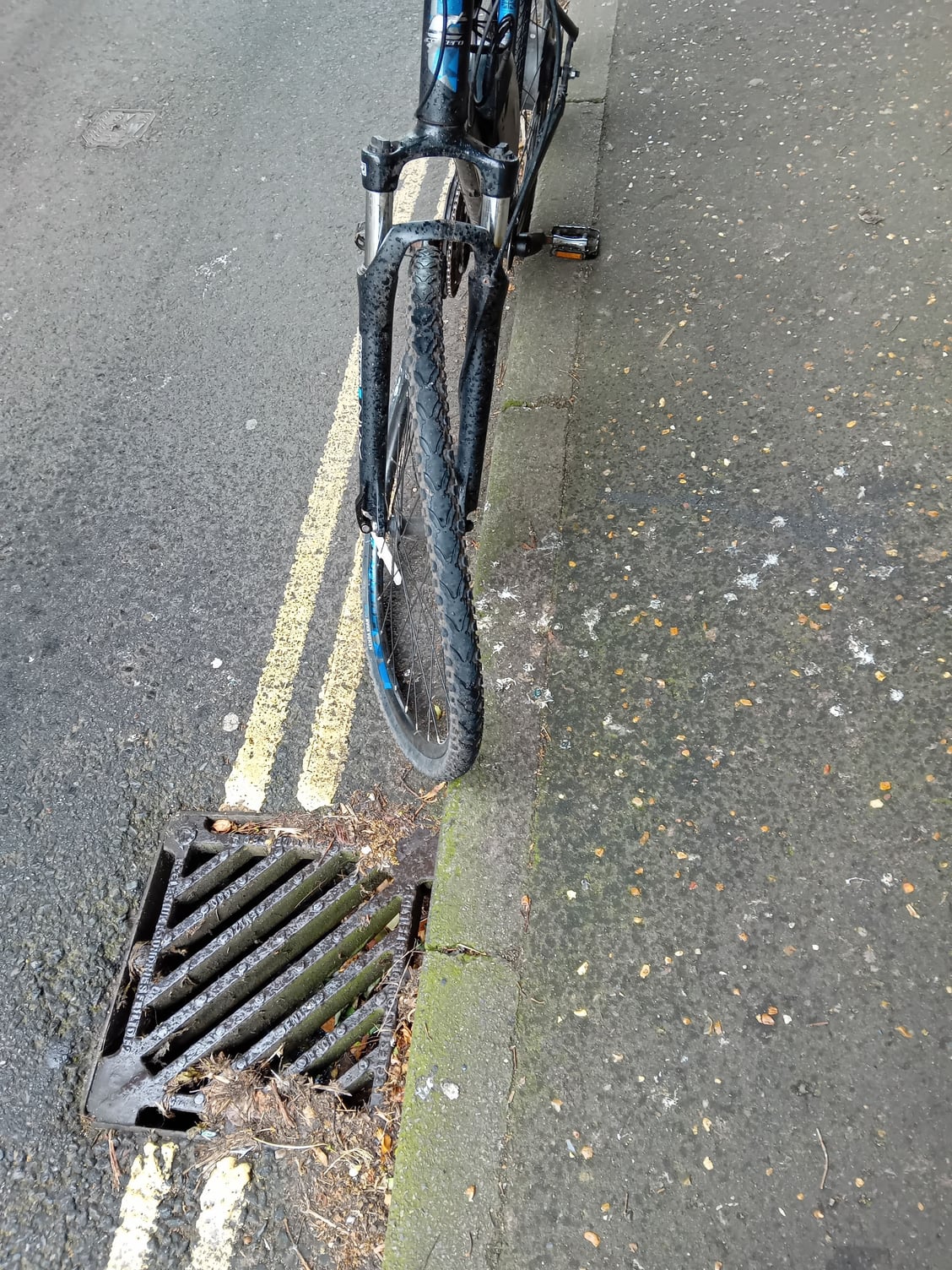
this was my fault as the wheel was over tensioned, wasnt aware of this until after i tightened the spokes i did untighten most of them but i was using a regular adjustable spanned which is way to big for the job
I assumed tightening all the spokes to tension would true the wheel but after reading this is wrong
#48
Senior Member
Join Date: Dec 2019
Posts: 972
Mentioned: 3 Post(s)
Tagged: 0 Thread(s)
Quoted: 329 Post(s)
Liked 265 Times
in
214 Posts
You can true a wheel with something like a fork to hold it in. But don't just eyeball that huge gap on that enormous fork-- hold a piece of card against it right up close to the rim and you can see where it's moving in and out.
Yes too much tension and you can get the "pringle" shape which you seem to have achieved rather well! And no you can't true a wheel just by tightening all the spokes. Back them all off and then true it in the normal way, and finish up with a reasonable amount of tension. Just get the spokes to feel about the same (when you pluck them like a guitar) as a similar wheel on a known good bike.
Yes too much tension and you can get the "pringle" shape which you seem to have achieved rather well! And no you can't true a wheel just by tightening all the spokes. Back them all off and then true it in the normal way, and finish up with a reasonable amount of tension. Just get the spokes to feel about the same (when you pluck them like a guitar) as a similar wheel on a known good bike.
#49
Newbie
Thread Starter
You can true a wheel with something like a fork to hold it in. But don't just eyeball that huge gap on that enormous fork-- hold a piece of card against it right up close to the rim and you can see where it's moving in and out.
Yes too much tension and you can get the "pringle" shape which you seem to have achieved rather well! And no you can't true a wheel just by tightening all the spokes. Back them all off and then true it in the normal way, and finish up with a reasonable amount of tension. Just get the spokes to feel about the same (when you pluck them like a guitar) as a similar wheel on a known good bike.
Yes too much tension and you can get the "pringle" shape which you seem to have achieved rather well! And no you can't true a wheel just by tightening all the spokes. Back them all off and then true it in the normal way, and finish up with a reasonable amount of tension. Just get the spokes to feel about the same (when you pluck them like a guitar) as a similar wheel on a known good bike.
ever had this problem with the nipples seems everything bad happens to me
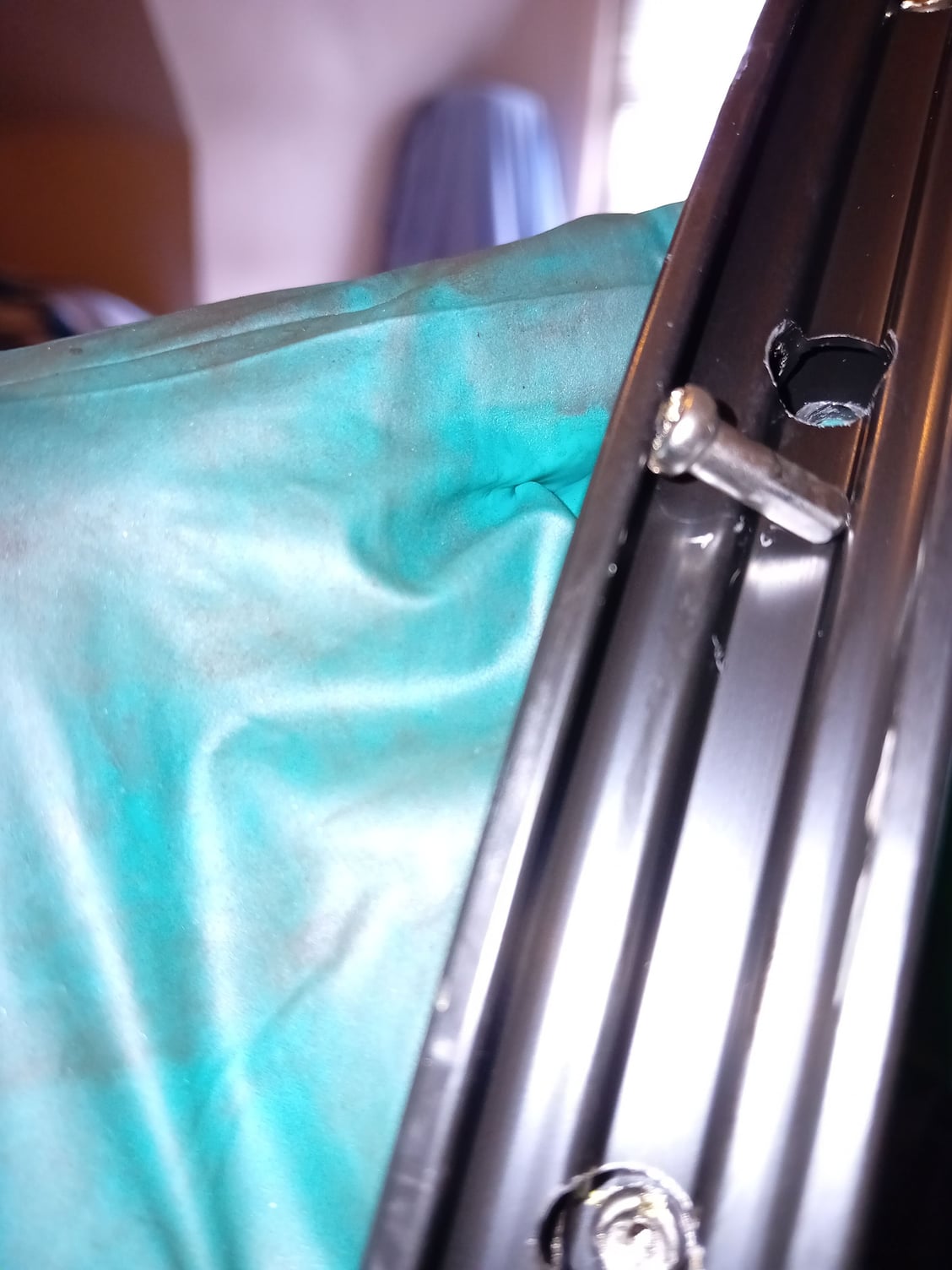
I was trying to put it in blindly and it ended up in that position for some reason, all sorted now though
As i was taking off the old hub to reuse, around 6 or 8 were loose and the same were overtaught, the rest seemed to be around the right tension
Ill use this wheel as a learning curve for the next wheels as ive never spoked a wheel before but it doesnt seem to hard was a bit awkward keeping the angle for the 3 cross but i got there
Likes For Jordanjw:
#50
Senior Member
Join Date: Dec 2019
Posts: 972
Mentioned: 3 Post(s)
Tagged: 0 Thread(s)
Quoted: 329 Post(s)
Liked 265 Times
in
214 Posts
Never had the nipple wedged like that, but sometimes they do fall in and get stuck between the two "skins". You have to shake the rim around until they fall out of the spoke hole eventually.
Spoking a wheel isn't too hard if you have another one to copy, but it's much easier if you follow one of the guides. The Sheldon Brown one is very good.
Spoking a wheel isn't too hard if you have another one to copy, but it's much easier if you follow one of the guides. The Sheldon Brown one is very good.